Very chill
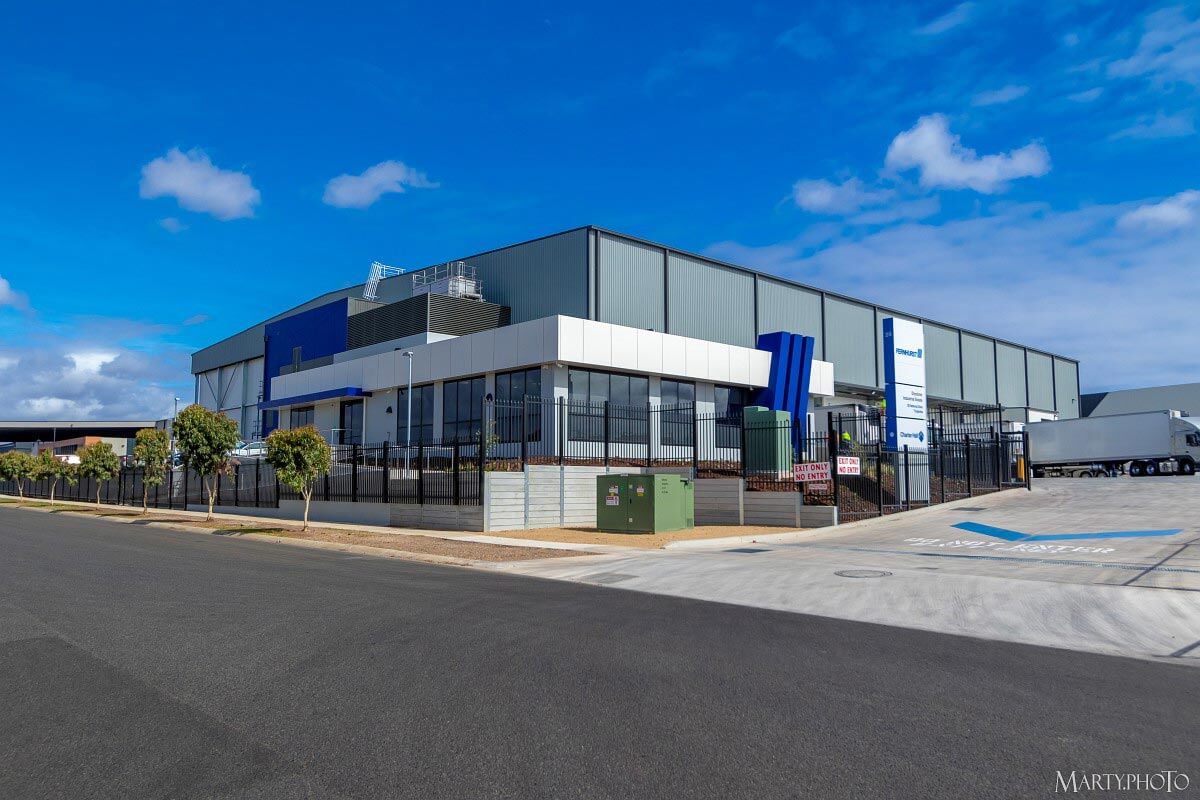
A centralised dual-stage, low-charge NH3 refrigeration plant with batch blast freezing at a new refrigerated warehouse in Melbourne is believed to represent a world-first. As Sean McGowan reports, the project is a finalist in the Excellence in Refrigeration category at the 2021 AIRAH Awards.
A leader in cold storage and refrigerated transport, Fernhurst operates a state-of-the-art 60,000m³ cold store and refrigerated logistics warehouse at Truganina in Melbourne’s outer-west.
As well as allowing the company to consolidate three existing facilities into one, the new facility presented an opportunity for Fernhurst to move away from traditional air-cooled HFC and CFC systems, and consider a future-proof, energy-efficient alternative.
In doing so, it has adopted a centralised dual-stage, low-charge NH3 (ammonia) refrigeration system, incorporating insulated coolers, “cold lake” air distribution, dry- expansion refrigerant feed and automatic ambient air defrost.
“There is an increasing body of evidence that the liquid-overfeed plant concept patented by York Corporation in 1925 is significantly less energy-efficient than system concepts where the suction line network conveys dry NH3 vapour only,” says Stefan Jensen, F.AIRAH, managing director of Scantec Refrigeration Technologies.
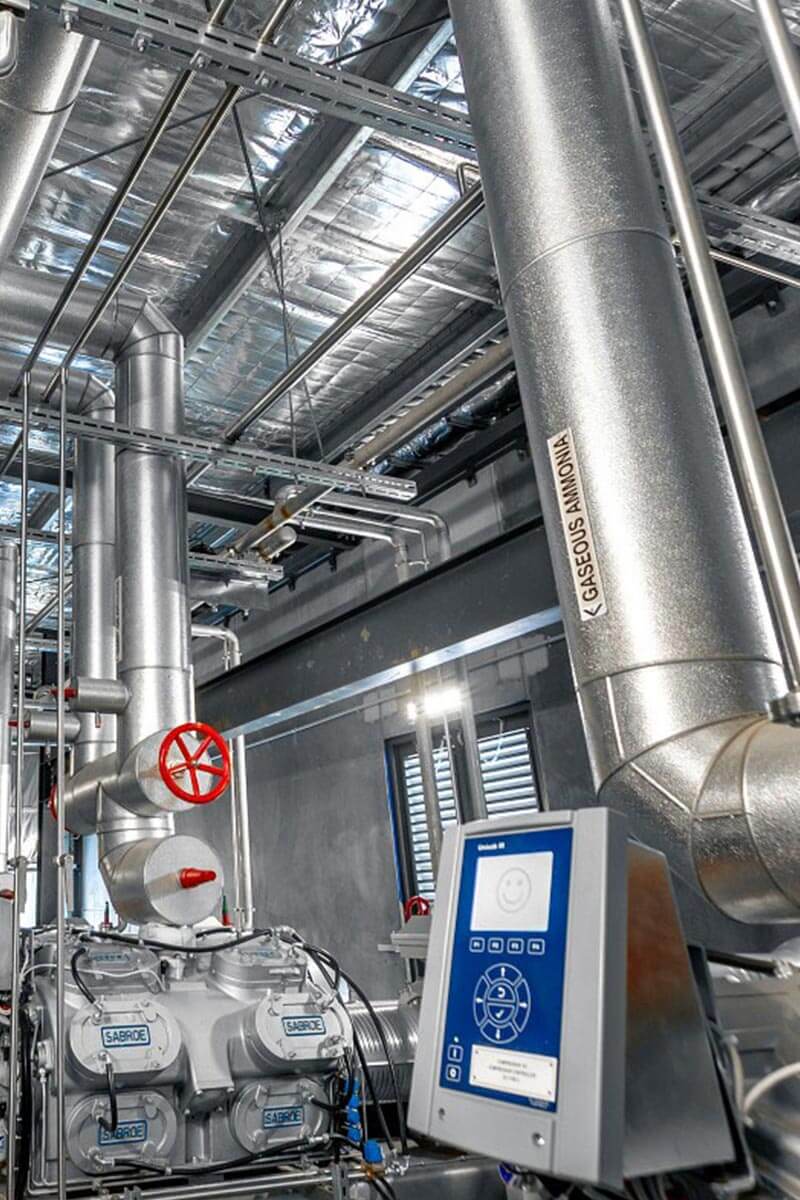
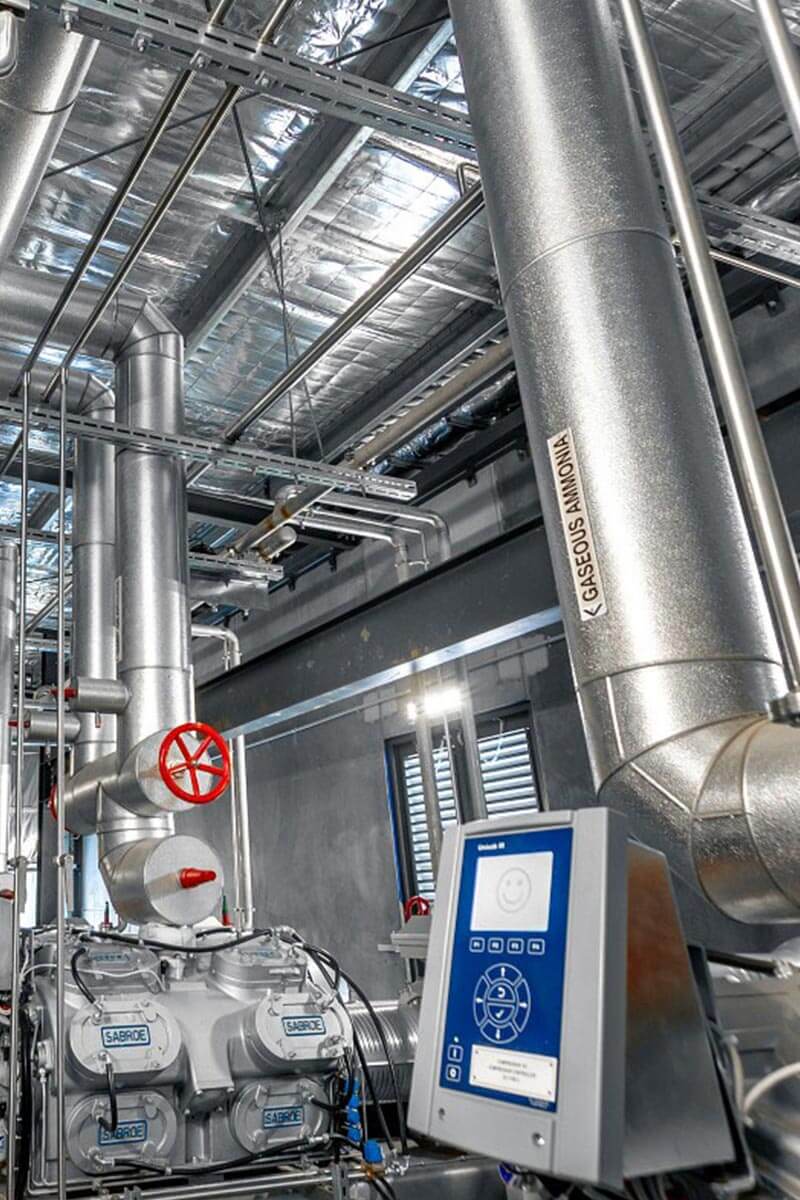
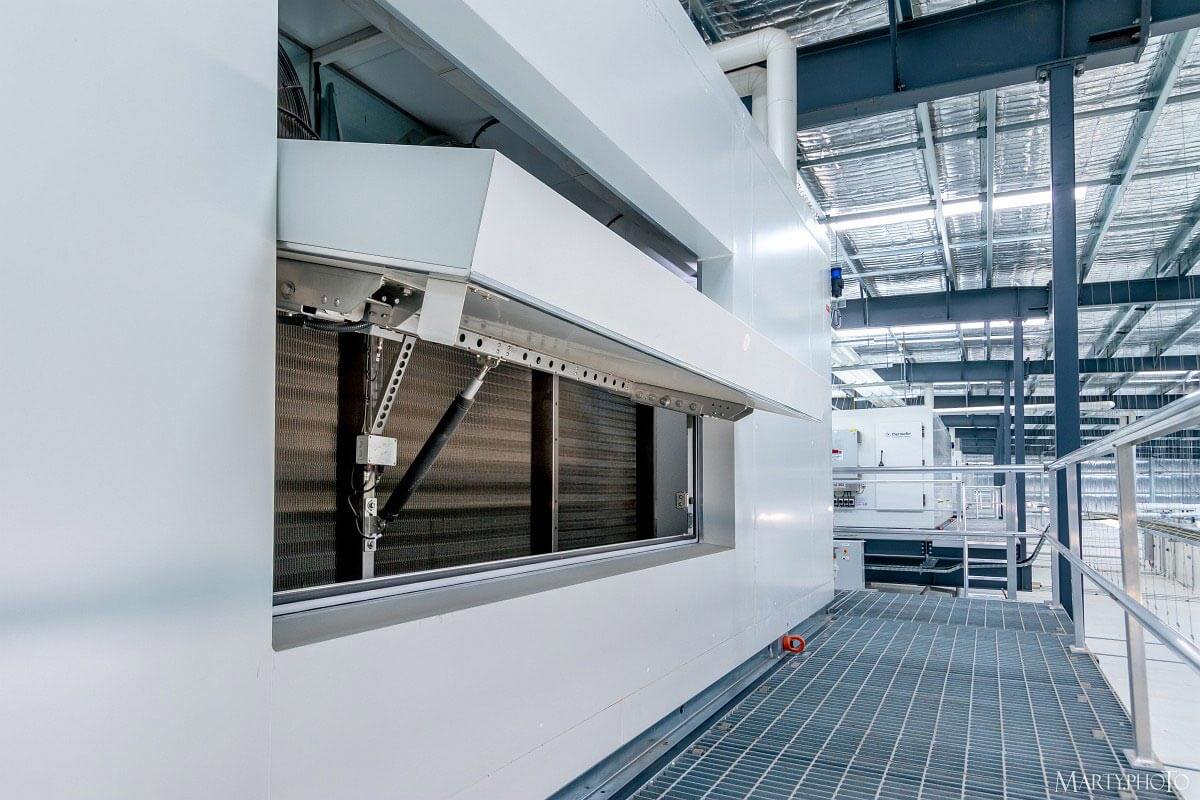
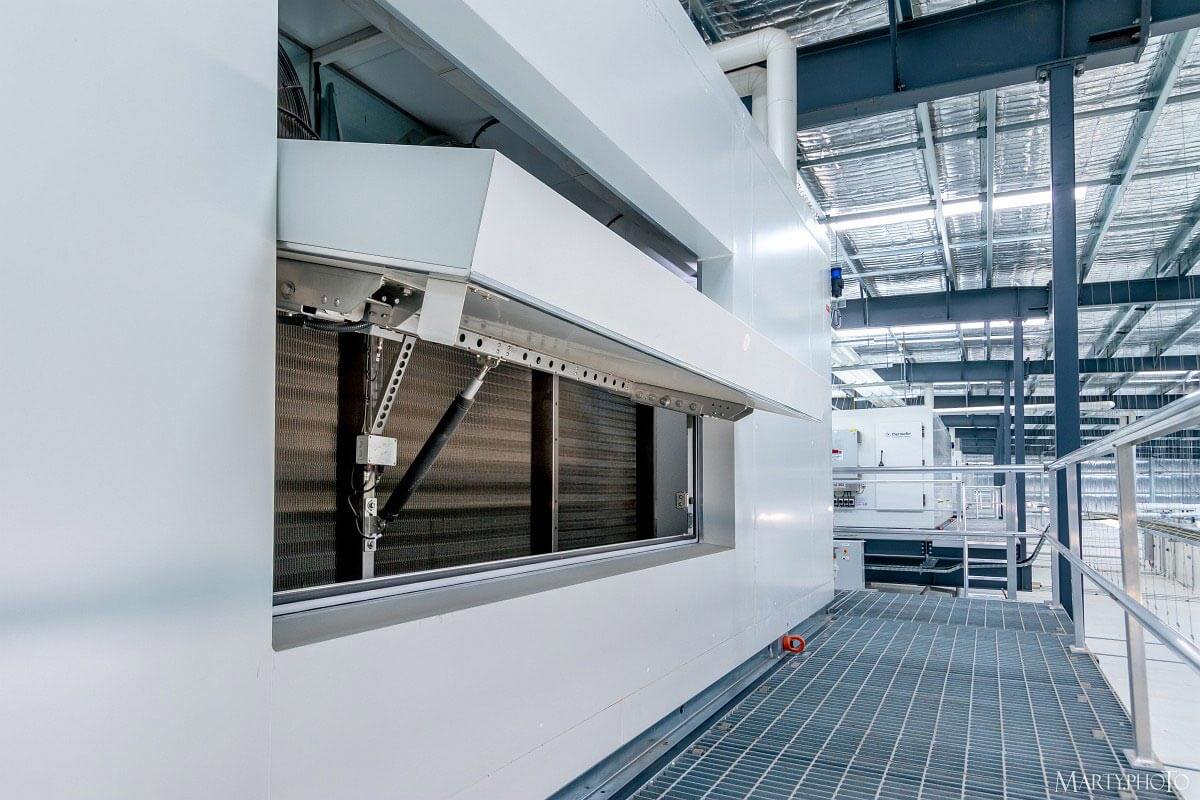
Defrost and emergency ammonia venting are carried out by means of automatic motorised shutters.
Proven performers
In designing the centralised dual-stage, low-charge NH3 refrigeration system at Truganina, Scantec Refrigeration Technologies elected to locate all air coolers (evaporators) outside the refrigerated space.
As well as simplifying access and maintenance, this design is able to utilise the ceiling space often available above ante rooms, which have lower ceiling heights than freezer rooms.
The location of the air coolers outside the refrigerated space also reduces noise levels, improves operator safety, simplifies the refrigerant pipework design and installation, eliminates any protrusions or obstructions within the refrigerated warehouse, and improves refrigerant leak management.
The “cold lake” air distribution concept employed by Scantec Refrigeration Technologies relies on the differences in density between relatively cool and relatively warmer air.
“In any refrigerated warehouse, it is the circulating airstream that cools the space,” says Jensen.
“The airstream does this by warming up slightly as it circulates throughout the facility. As the air warms, the density reduces and the air seeks to rise towards the ceiling of the facility without requiring any mechanical assistance to do so.”
From there, the air is returned to the air cooler (evaporator), is refrigerated again and returned to the room.
According to Jensen, this is in contrast to the conventional air distribution method, which injects relatively cold air at high level into the refrigerated space. This forces the airstream to more or less do the opposite of what it naturally seeks to do when used as the cooling agent in the refrigerated warehouse.
The air temperature and air velocity distribution throughout the facility was determined using computational fluid dynamics (CFD) modelling based on actual building dimensions, evaporator locations and racking layout.
At Fernhurst’s new Truganina facility, defrost is carried out by means of automatic motorised shutters.
During defrost, the cooling coil is isolated from the refrigerated warehouse on the air side, while ambient air is circulated through the cooling coil causing it to defrost.
Scantec says this design minimises heat ingress into the freezer during defrost.
“The use of dry expansion refrigerant feed and the employment of evaporator materials with high thermal conductivities creates a faster defrost cycle,” says Jensen.
The reason, he says, is that the air coolers contain significantly less refrigerant than conventional liquid overfeed evaporators at the commencement of defrost, and hence warm up faster.
The defrost arrangement doubles as an automatic venting feature in the event of an ammonia leak from the evaporator. Should a leak occur, the air cooler is forced into defrost mode to prevent leaked refrigerant from entering the refrigerated space.
A new benchmark
“Based on documentary evidence from a range of other centralised, low-charge NH3 refrigerating plants servicing mixed refrigerated warehouses, the SEC as a function of refrigerated volume was determined by means of polynomial regression analysis,” says Scantec’s Stefan Jensen, F.AIRAH
“This analysis was used for the prediction of an annual ammonia refrigerating plant energy consumption of 900–1050MWh/year for storage only.”
As well as informing the Fernhurst project, this analysis forms the basis for a proposed best-practice energy performance benchmark for refrigerated warehouses in Australia, as detailed at the AIRAH Refrigeration 2021 Conference.
Low charge
Any ammonia exposure risk in the freezer(s) is further mitigated by the inherently lower operating refrigerant inventory in the air coolers of the centralised, dual-stage, low-charge NH3 refrigeration system.
Jensen says the operating refrigerant inventory in the air coolers is typically 30–50 times lower than in conventional liquid overfeed ammonia plant. The overall plant inventory is typically four to five times lower.
At Fernhurst’s Truganina facility, the total refrigerant inventory is only 472kg. Importantly, this figure is below the threshold that would classify the site as a Dangerous Goods Storage facility.
“If the facility had been serviced by a conventional liquid overfeed refrigeration plant, the ammonia inventory would have been 2,000 to 2,500kg,” says Jensen.
The operating refrigerant inventory in all air coolers combined is just 25kg – up to 40 times lower than conventional liquid overfeed systems. Likewise, the combined NH3 operating inventory in the three freezer evaporators was reduced to less than 5kg using refrigerant-wetness-controlled DX feed.
Says Jensen: “The significantly lower refrigerant inventories in the air coolers – and in the plant as a whole – contribute to an installation that is safer than conventional plant with liquid overfeed.”
Energy
Fernhurst took an active interest in determining the centralised dual-stage, low-charge NH3 refrigeration plant concept – going so far as to inspect a comparable facility in Brisbane that was serviced by the same type of refrigeration plant.
This due diligence ensured Fernhurst was confident such a system would be fit-for-purpose at its new Truganina facility.
Well known for its design and construction of NH3 refrigeration systems serving various sectors across the country, Scantec Refrigeration Technologies has collected sufficient data to accurately compare the energy efficiency this type of plant offers against other concepts.
Plant benefits
Other features of the centralised dual-stage, low-charge NH3 refrigeration plant include:
Avoidance of most liquefied refrigerant management problems associated with extensive periods of low loads and/or automatic re-start after power failures.
Use of all stainless steel pipelines
Stainless steel condenser
Elimination of ammonia pumps
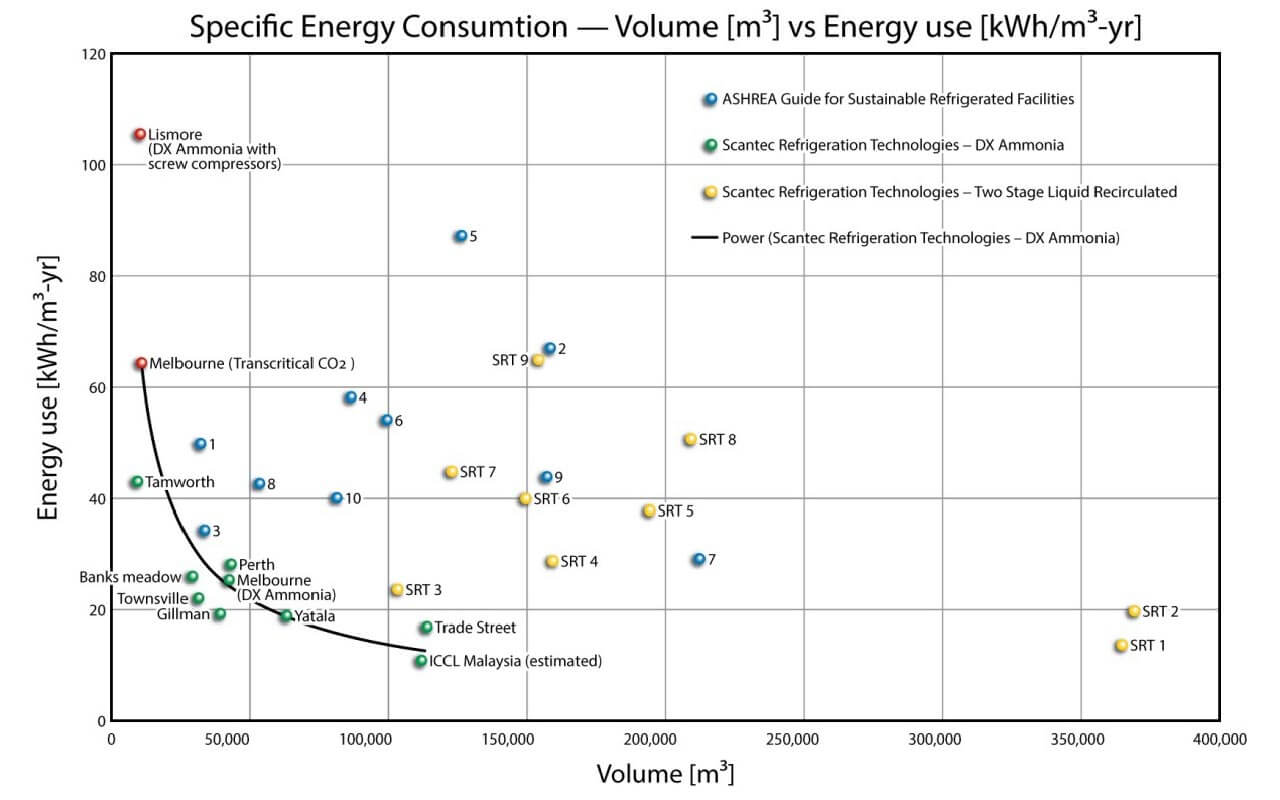
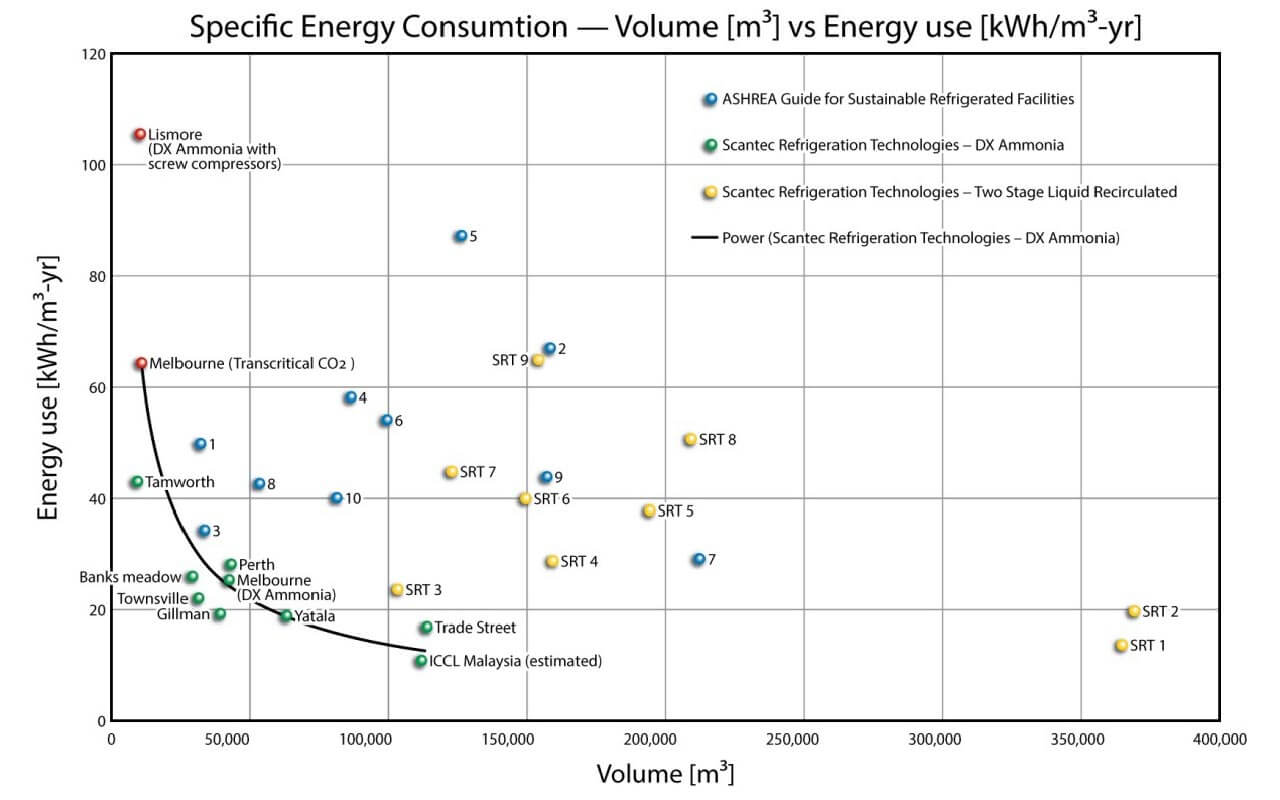
This is evidenced by the green dots in the graph below that represent a number of centralised dual-stage, low-charge NH3 plants. In some cases, energy consumption is several times lower than the conventional systems also featured in the graph.
According to Jensen, it is also evident that there is a greater level of predictability associated with the specific energy consumption (SEC) of centralised dual-stage, low-charge NH3 refrigerating plant.
“The SEC values on the vertical axis are recorded in kWh/m³/year, where the volume in m³ refers to the refrigerated volume,” explains Jensen.
The energy consumption associated with product freezing at Fernhurst’s Truganina facility was estimated to be 110kWh/tonne.
“Based on the design blast freezing capacity of 300 tonnes per week, the annual predicted energy consumption for storage and product freezing combined was in the range of 2550–2700MWh/year.”
Following temperature pull-down of the facility, and occupancy in early November 2020, the energy consumption for the entire site was monitored during Melbourne’s summer.
During the period from January 31 to February 28, 2021, site energy consumption was recorded at 182.7MWh. This included HFC-based office air conditioning, general light and power, forklift charging and other consumers – as well as the NH3 refrigeration plant.
The energy consumption of the NH3 plant is also monitored separately via a power meter forming part of the facility’s SCADA system. For the same period, the recorded energy consumption of the NH3 plant in isolation was 151.0MWh.
“Extrapolating these values to a year yields a range of 1968–2382MWh,” says Jensen.
With Fernhurst nominating the blast freezer quantities during the period as “being close to the design quantity of 300 tonnes per week”, actual energy consumption is therefore in line with the predictions made by Scantec Refrigeration Technologies.
The rack blast freezer fans were later identified as significant energy consumers via separate metering. In response, they were retrofitted with variable frequency drives and a more advanced control system that modulates fan speed in response to product temperature.
These modifications were completed in mid-2021. While the anticipated simple payback for this investment is one year, the impact on energy consumption associated with the freezing operation is yet to be verified.
“Evidence is building in several countries that the energy performance penalty associated with the presence of relatively high-density liquefied refrigerant in the suction line networks of large, expansive liquid overfeed ammonia plant is higher than hitherto assumed,” says Jensen.
Jensen says the experience at the Fernhurst plant supports this body of evidence, and demonstrates the potential benefit that plant owners may realise through exercising a degree of technical input during the initial phases of the development.
“Ultimately, these types of systems will be game-changers once the practical experiences associated with their design and operation are disseminated and published.”
Comparing ammonia
The chart below provides a comparison between a typical centralised low-charge NH3 refrigeration plant and a range of other refrigeration plant concepts.
The small green star represents a Brisbane-based refrigerated storage facility serviced by a low-charge NH3 plant commissioned in 2020. The remaining dots represent facilities owned and operated by one US-based entity specialising in refrigerated storage.
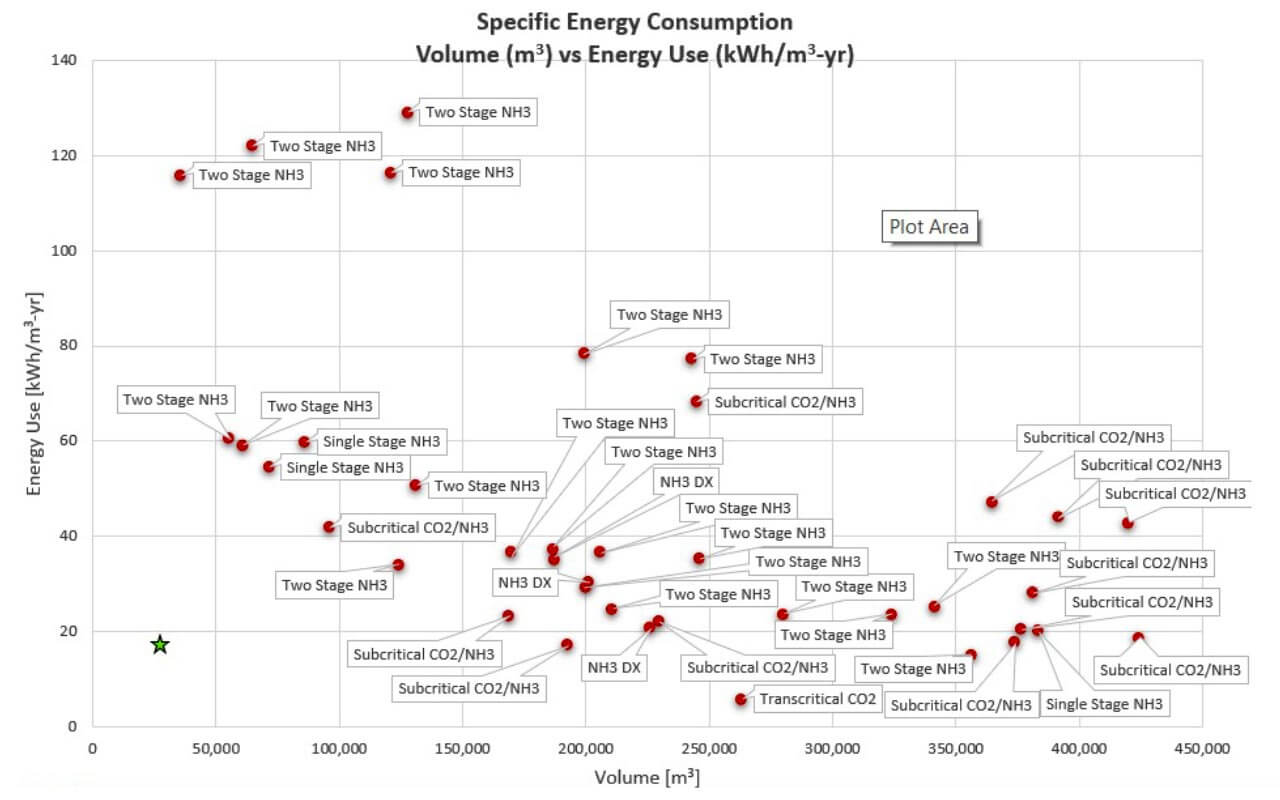
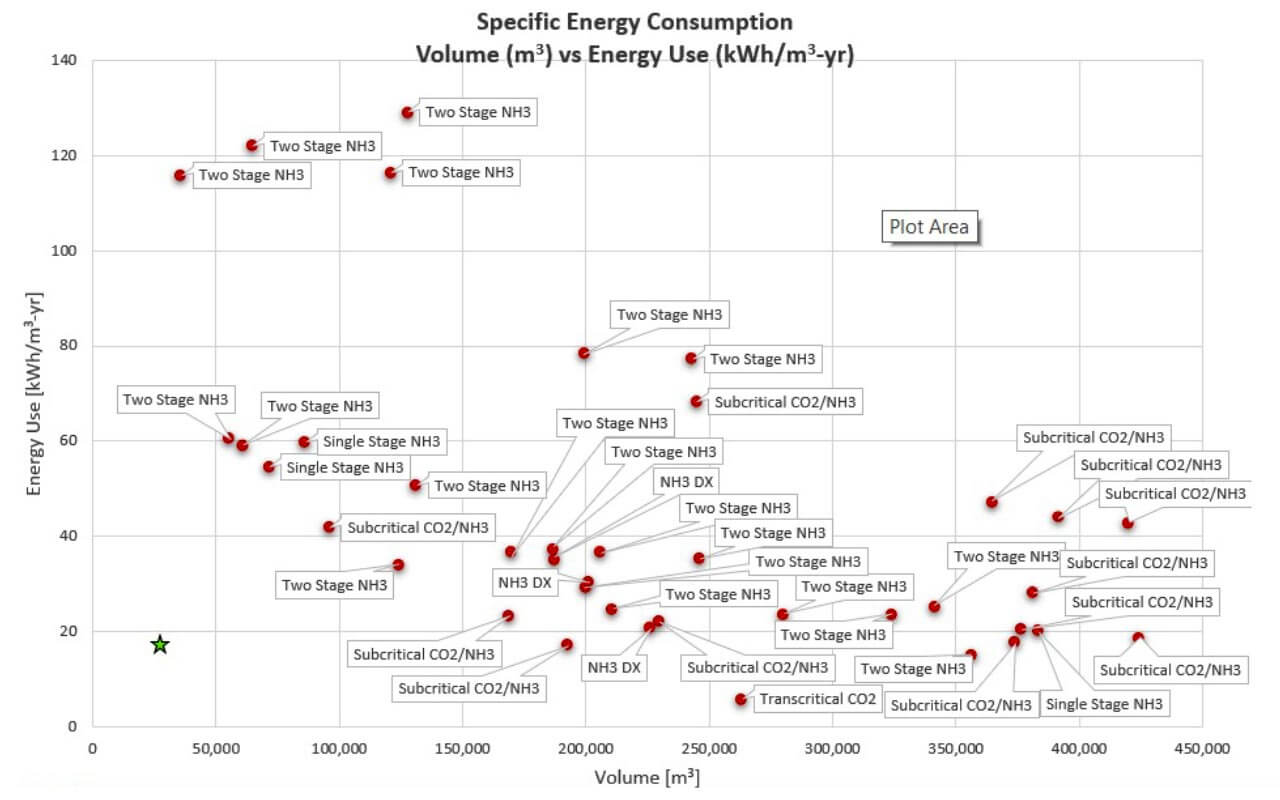
Project at a glance
The personal
Client: Fernhurst
Controls: Allen Bradley
Developer: Charter Hall
Head contractor: CIP Constructions
Refrigeration design engineer and contractor: Scantec Refrigeration Technologies
Refrigeration maintenance contractor: Lucas Refrigeration
The equipment
Air coolers: Thermofin
Compressors: SABROE/Johnson Controls
Condensers: Patkol Heataway
Controls: Allen Bradley
Evaporators: Thermofin
Pipework: Scantec Refrigeration Technologies
Sensors: HB Products, Danfoss and ECE Fast
Valves: Danfoss
VSDs: Danfoss
(Source: Scantec Refrigeration Technologies)
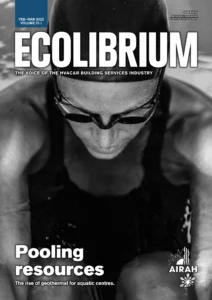
This article appears in Ecolibrium’s February-March 2022 edition
View the archive of previous editions