Walking the talk
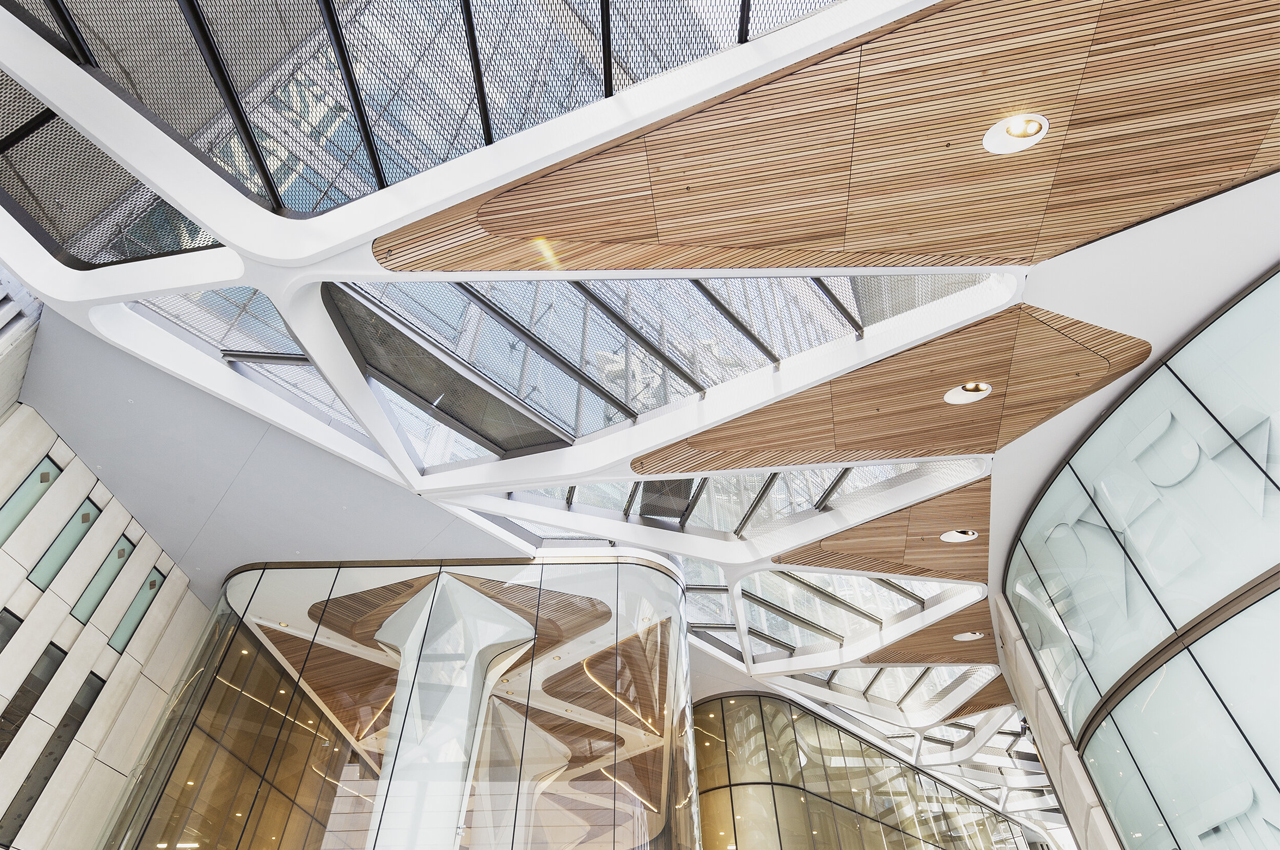
The new-look 388 George Street office tower in Sydney’s CBD represents one of the largest commercial office building refurbishments the city has ever seen. As Sean McGowan reports, the multidisciplinary approach taken by consulting engineer Arup has delivered world-class amenity, connectivity and comfort to tenants. Importantly, the clever refurb integrates the site with a newly pedestrianised George Street.
388 George Street overlooks one of Sydney’s busiest intersections on what has come to be known as the George Street Boulevard.
The city’s downtown retail destination, George Street is undergoing a multi-billion dollar, car-free revitalisation following the completion of light rail into the street connecting the CBD to Sydney’s eastern suburbs.
The city aspires to create a pedestrian boulevard to rival others around the world.
When completed, it will feature new green spaces, street furniture, wider footpaths and outdoor dining precincts.
Part of the street’s new look is the $200 million redevelopment of the 30-storey office tower at 388 George Street, which has transformed the busy CBD corner.
Designed by Australian architect John Andrews, and constructed in 1976, the building became internationally recognised due to its innovative and distinctive 45-degree angle on the street corner.
Now jointly owned by Brookfield and Investa Gateway Offices (IGO), the recent refurbishment has transformed the building both inside and out.
As well as achieving an increased net lettable area (NLA) of new Property Council of Australia (PCA) A-Grade office space across 27 levels, the refurbishment has seen the addition of a five-level pavilion designed by architect fjmtstudio.
Integrating the site with the newly pedestrianised George Street, the pavilion introduces 2,680m² of new retail space, and provides the existing building with a new lobby, end-of-trip facilities and through-site link connecting it to King Street.
The design – featuring a curved sandstone and glass façade – complements the rich history of the site, and is inspired by the topography of the surrounding CBD landscape.
“This new façade reinforces a juxtaposition between the new pavilion and the existing modernist tower whilst strengthening the streetscape of George Street,” says Richard Francis-Jones, design director at fjmtstudio. “Our design will not only restore the street wall but also create a through-link on the site that will be a natural extension of the existing link between Pitt and King streets.”
Multi-disciplinary benefits
Arup building services associate Tim Boorman says it’s common for the firm to be involved in multi-disciplinary projects.
“It is how we prefer to work on large-scale projects,” he says, “and where we can add the most benefit.
“We are able to workshop internally, look at the problem holistically and integrate among the relevant disciplines to find the optimum solution for the project. We can then present a complete solution or suite of solutions to the client.”
A multidisciplinary approach
Arup was first engaged by the co-owners of 388 George Street to complete a feasibility study that would instruct the refurbishment of the original 1970s building into a modern commercial tower.
“We worked with our ESD and building management control system (BMCS) teams to identify as part of a feasibility study areas of improvement for energy and the indoor environment,” says Arup building services associate Tim Boorman.
As part of the feasibility study, Arup reviewed stretch targets for Green Star and WELL rating programs, as well as reviewing the building’s compliance and PCA grade status.
This work led to a major refurbishment of the building. This put sustainability, occupant wellbeing and resource efficiency front and centre of its design.
The refurbishment project targeted a 5 star NABERS Energy and IEQ ratings, 4 star NABERS Water rating, 5 star Green Star Design & As-Built v1.1 ratings and a WELL Gold Shell & Core rating.
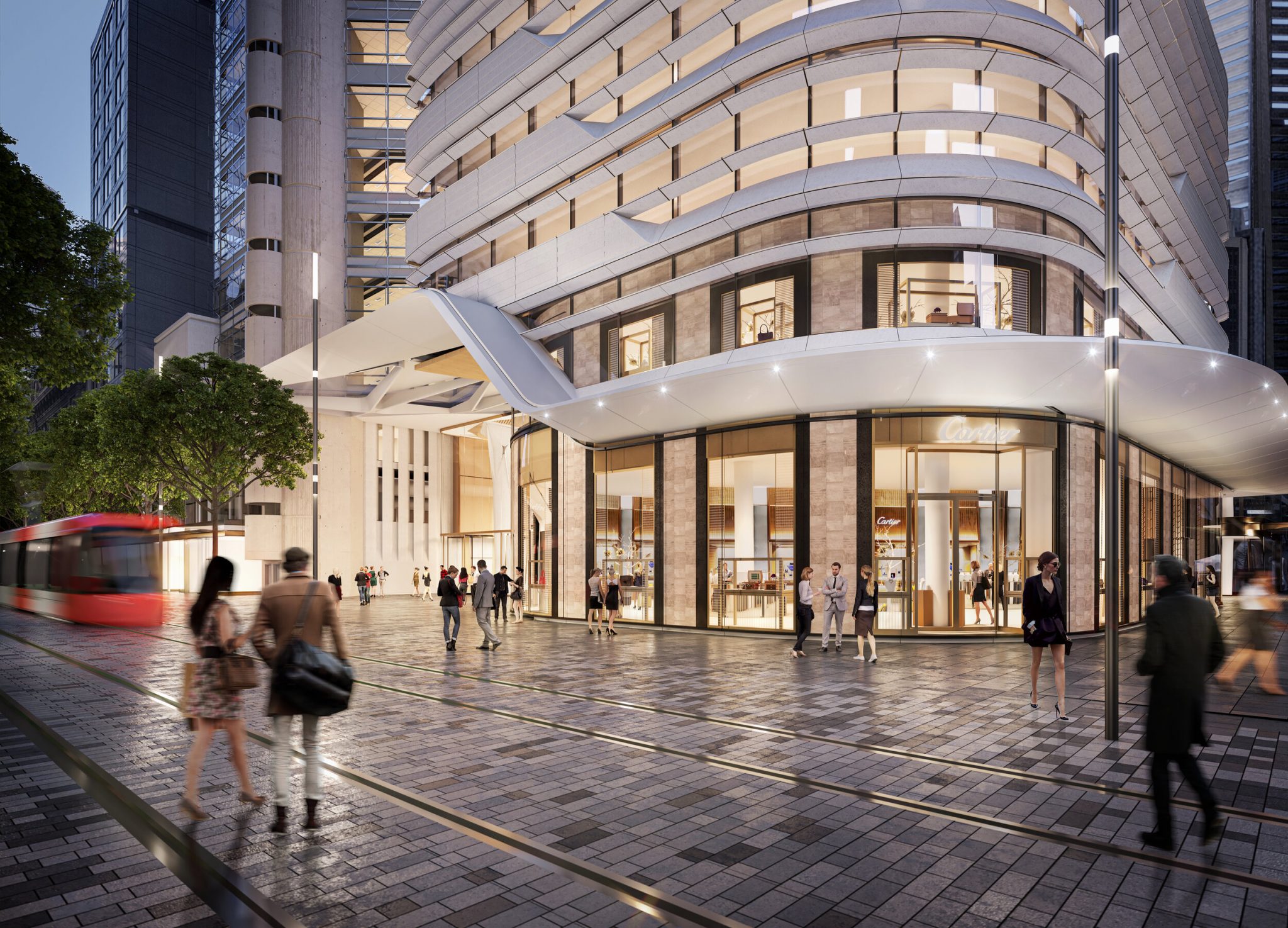
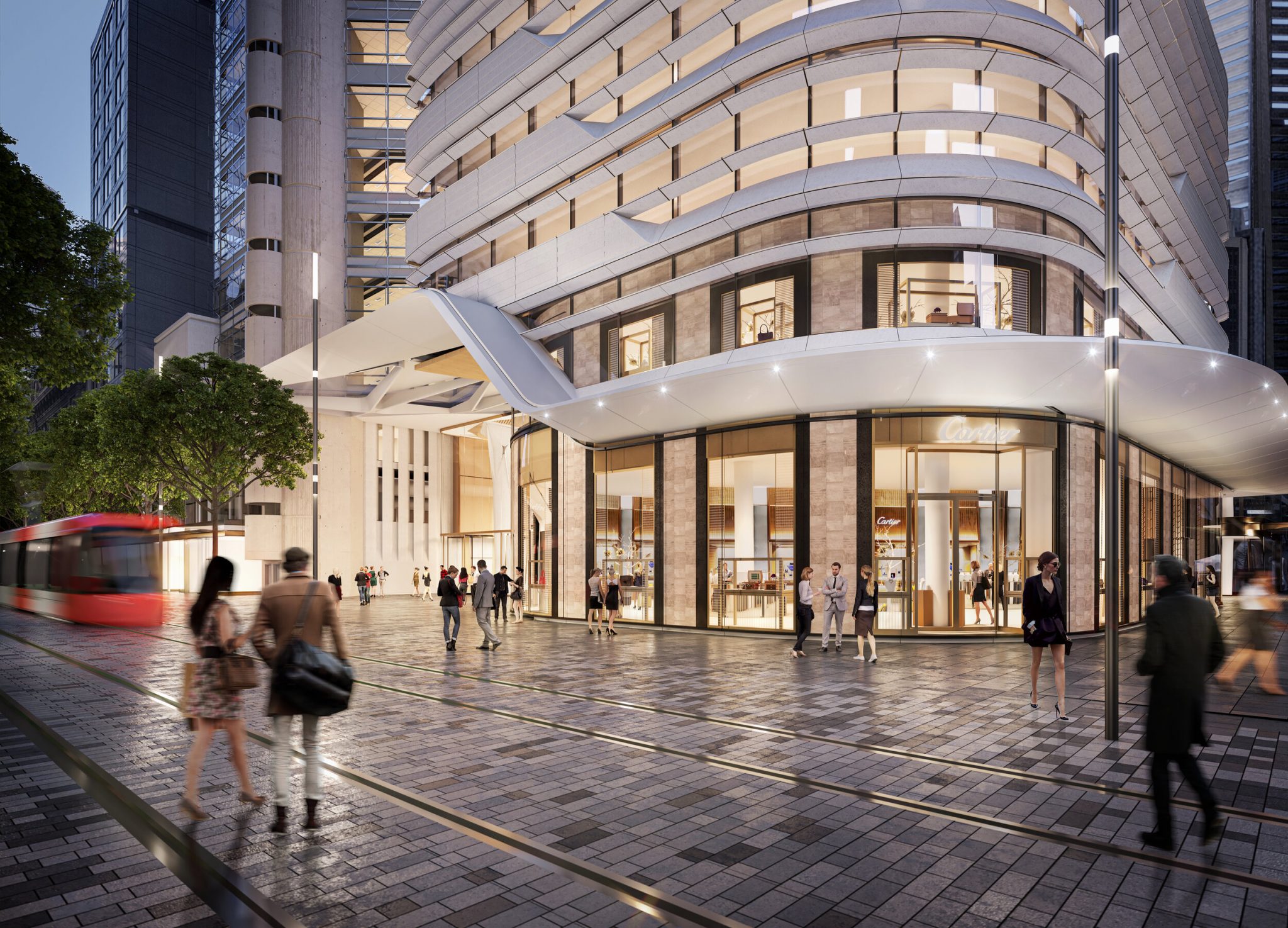
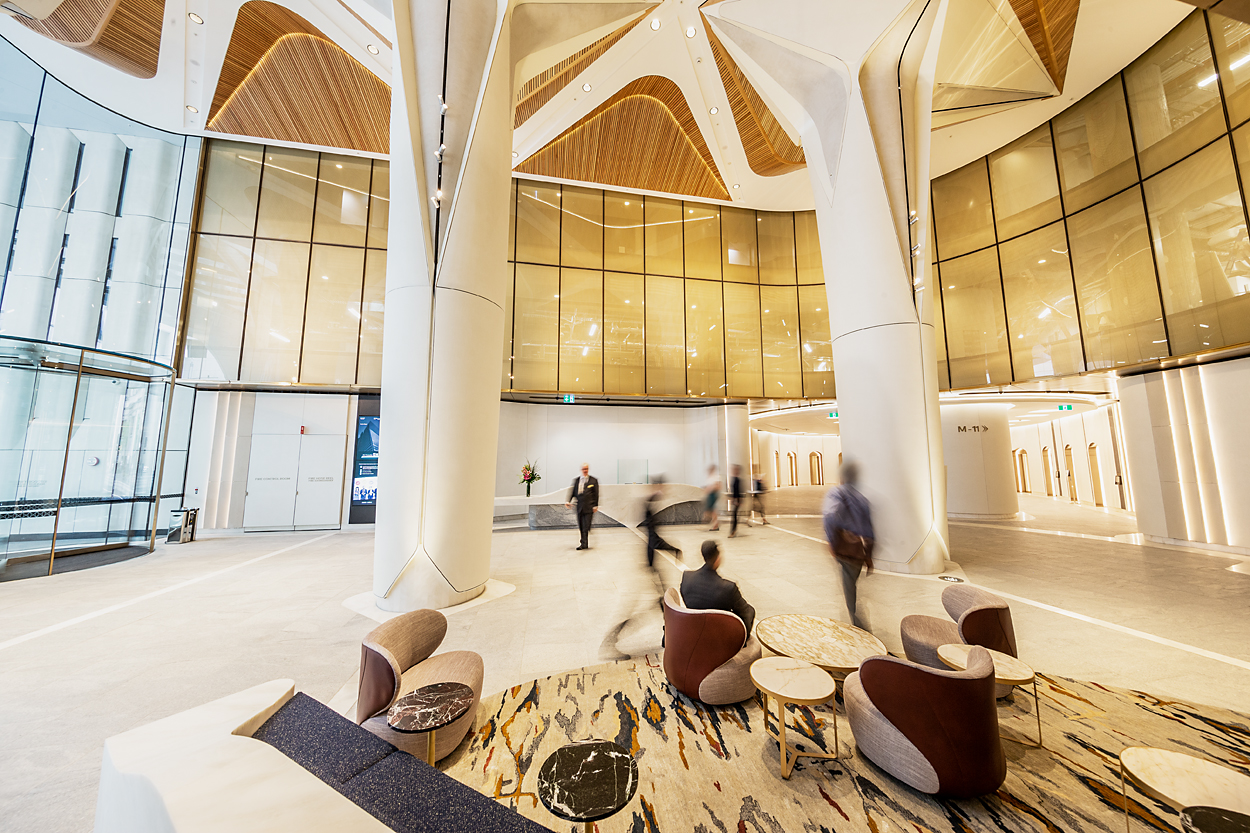
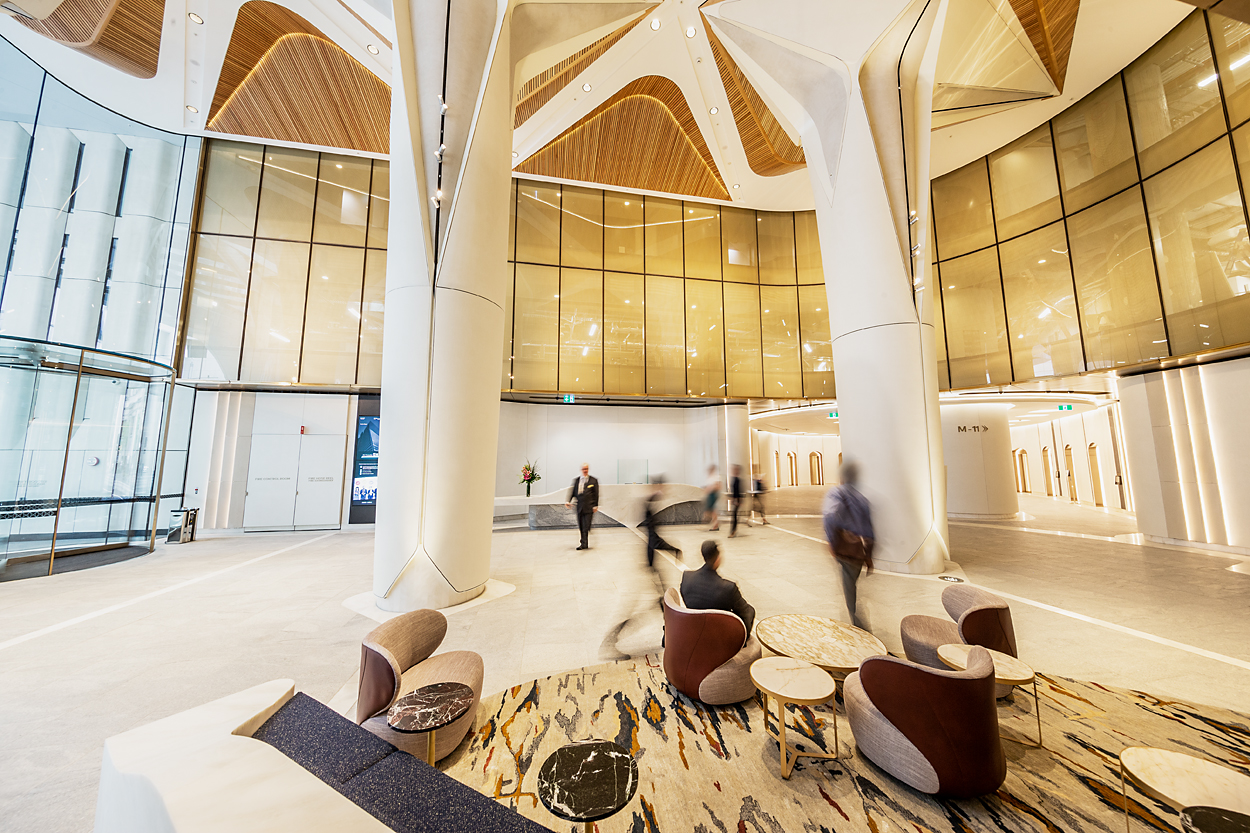
Minimising change
Following major refurbishments in 1998 as well as 2009, the existing commercial office tower needed modernisation to improve its operational performance.
But with the 388 George Street building listed on the Australian Institute of Architects’ Register of Significant Architecture – as well as on the National Trust of Australia’s register – any change to the external appearance of the building needed to be minimised.
Additionally, a key client focus for engineering services was to retain existing infrastructure where possible and minimise waste and any capital expenditure outlay.
For Arup, this meant making the existing configuration fit for a modern office building by working within the constraints of plantroom locations, inaccessible concrete risers and electrical infrastructure.
“The majority of the mechanical services equipment was at end-of-life, and required upgrading following the building’s refurbishment in 1998,” says Boorman.
This included chillers and air-handling units (AHUs) that required replacement to achieve increased capacity.
“We were able to offset the additional load with the increase in efficiency from the new chillers to negate the need to replace the cooling towers on the roof.”
Detailed dilapidation and intrusive surveys were also completed to determine the condition of pipework and internal workings of the mechanical services systems.
Arup’s feasibility study did, however, identify several opportunities for the reuse of existing services in the refurbishment project, including the mechanical services system.
The existing mechanical services system was found to be in a condition such that it could be retained, with the existing variable air volume (VAV) system able to be converted to a low-temperature VAV system to increase capacity without increasing airflow.
In this way, the capacity of the system was able to be increased without the need to replace the existing supply air risers – sized for 1-in-10m² building occupancy – located within inaccessible concrete shafts.
Existing ductwork was also found to be reusable, and was subsequently cleaned.
“Due to low supply air temperatures and VAV systems used, high-induction swirl diffusers were utilised in the commercial office spaces for increased occupant comfort,” says Boorman.
New control strategies were implemented for increased energy efficiency and thermal performance. To this end, Boorman says Arup’s ESD team completed detailed thermal modelling.
The chilled water system load was increased to account for the additional load of an increase in occupant density (1-in-8m²) and floor area.
High-efficiency chillers were used to avoid the need to increase the size of the condenser water system.
To avoid the need for a crane, the existing AHU fans (some more than 3m high) were replaced with a series of smaller EC (electronically commutated) plug fans that were able to be moved into the plantrooms via the building’s goods lift.
“This saved the client significant cost,” says Arup’s project lead, Eric Serret, “And reduced the construction program.”
The building’s existing cooling towers were able to be retained, with aging parts replaced or refurbished to ensure longevity of the heat-rejection system.
Lessons from the consultant
Arup project lead Eric Serret offers several lessons about the upgrade works at 388 George Street, Sydney.
Take time to look at a problem holistically. There were many occasions where we challenged the normal approach to increase reuse and reduce construction cost and program.
Although it is easier to replace existing services rather than retaining the existing in regards to reliability and engineering assessments/capacities, this is not a sustainable approach, and one we do not strive for.
To maintain, we had to assess existing cooling and heating capacities against new demands and existing riser capabilities for services that were being retained. We developed a scope for a detailed intrusive dilapidation report to be completed that helped identify where existing pipework and ductwork was in good condition and could be retained.
Scanning of existing buildings is essential. We completed 3D scans of the existing plantrooms where we remodelled the existing services in the 3D Revit model. This enabled coordination of new and modified services easier, and we were able to remove any clashes before the construction team got to site.
Coordination with existing structures is important. Extensive structural strengthening was required for any new penetrations in the structure, so early identification of penetrations and coordination was critical.
Serving the pavilion
The addition of the pavilion on the building’s podium saw services including chilled and heating hot water provided from the main building’s existing infrastructure and connected via a common basement.
Local fan coil units (FCUs) were provided to the commercial floors of the pavilion to maximise the roof space available to facilitate the rooftop bar.
According to Boorman, an alternative fire engineering solution was developed in collaboration with Arup’s fire engineering team. This removed the requirement for stair pressurisation from the five-level building.
“This building was classified as an alternative solution as a separate building and would be less than 25m in height,” he explains, “removing the requirement for stair pressurisation to free up roof space for a rooftop bar.”
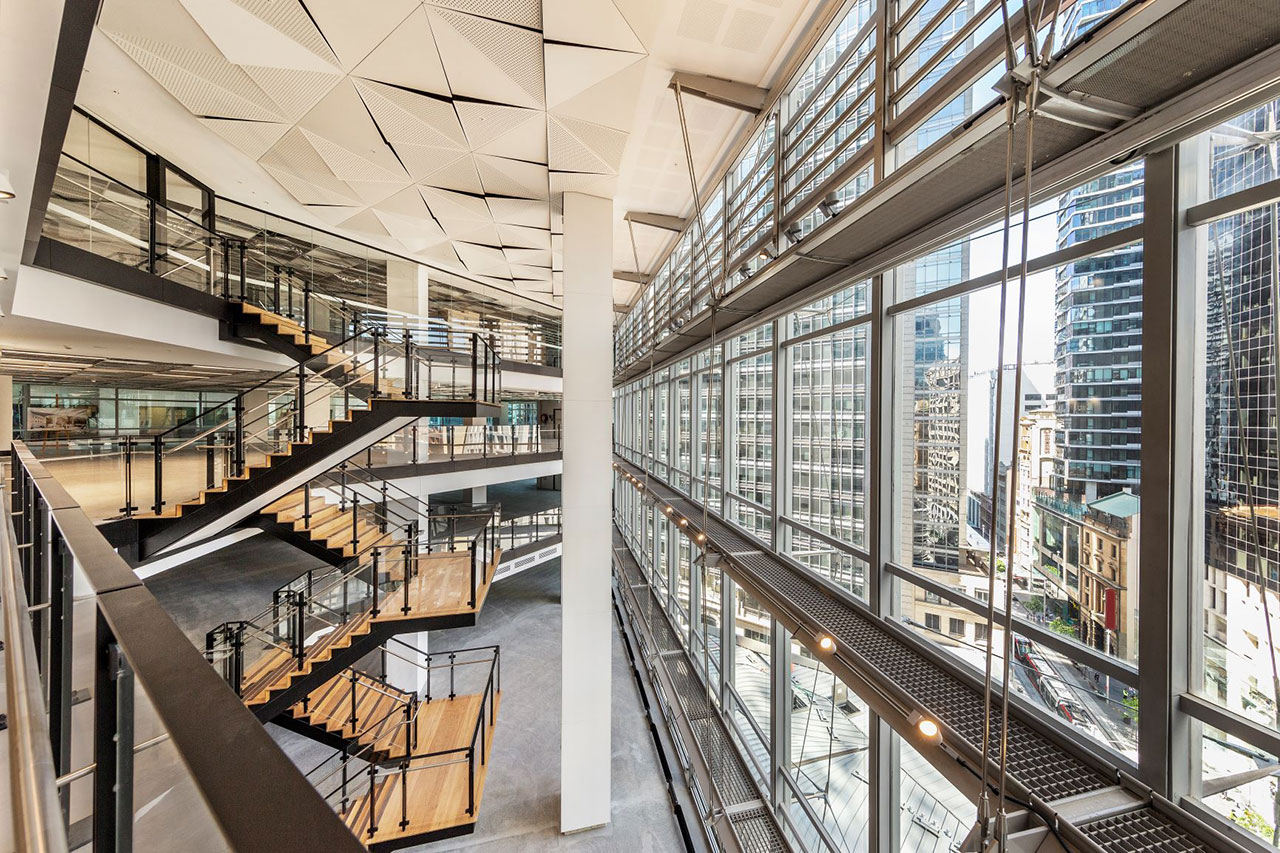
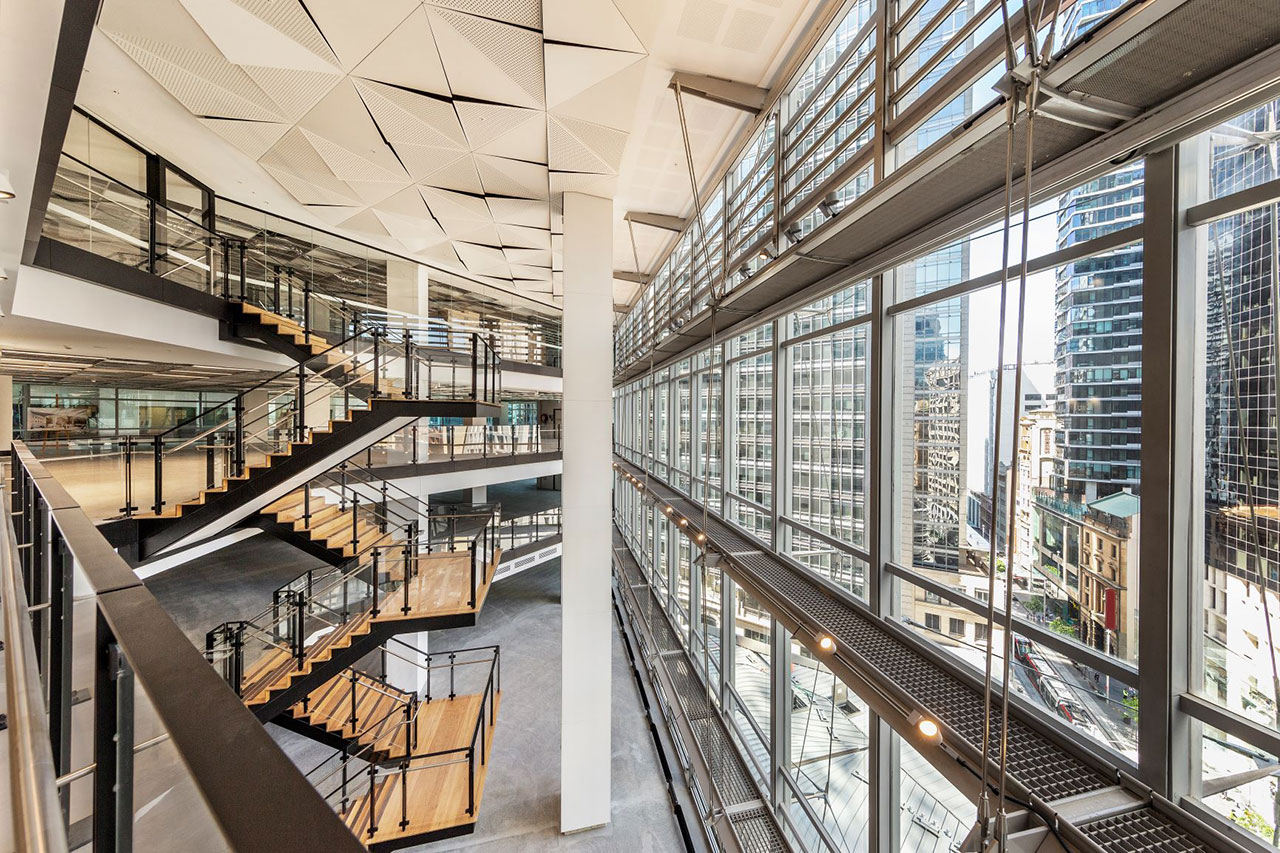
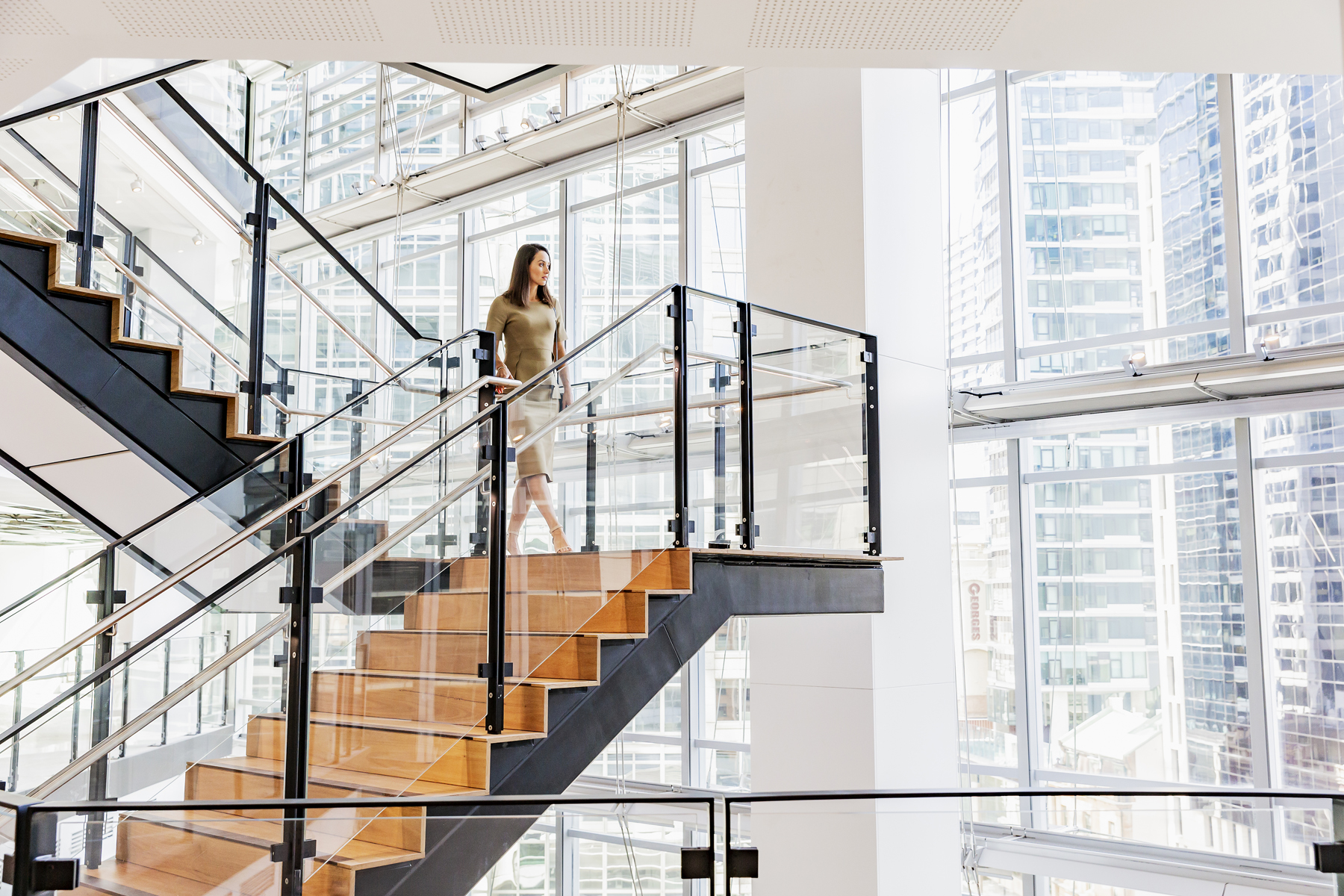
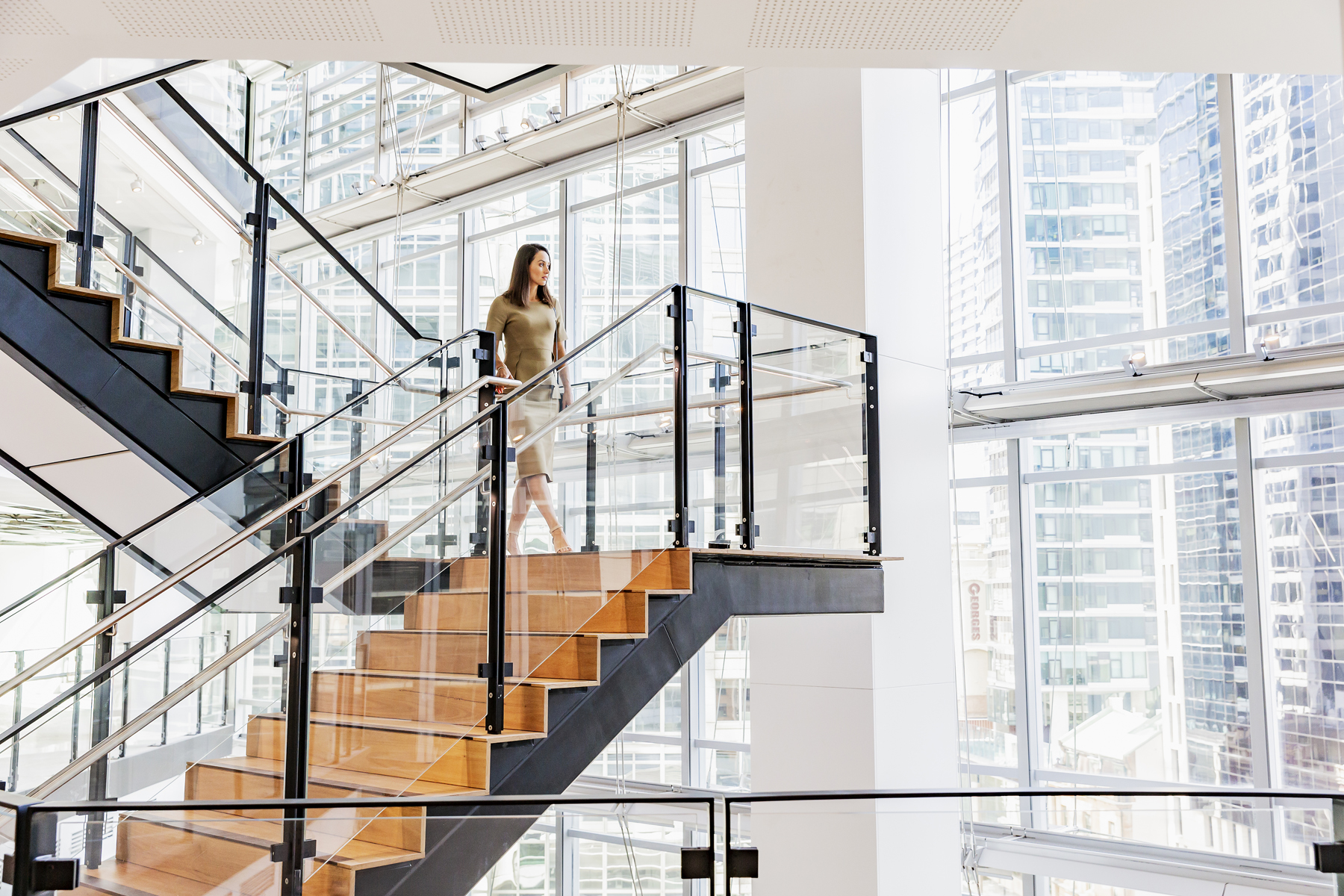
Basement fix
According to Serret, the existing electrical substation was retained, with the electrical infrastructure carefully managed.
Space was provisioned for the future introduction of micro-turbines to increase electrical capacity.
“This gave the co-owners flexibility on leasing, depending on the mix of retail and commercial tenants,” Serret says.
The existing basement carpark ventilation system was found to not be compliant with current standards, and many areas of the carpark had low head height due to ductwork reticulation.
By working with Arup’s fire services team, this head height was able to increased, and achieve compliance. The solution involved removing the ductwork and introducing jet fans to facilitate air movement in the space.
“Computational fluid dynamics (CFD) modelling studies were completed to demonstrate the alternative compliance to standard design,” says Serret.
Converting the atriums
One of the more challenging aspects of 388 George Street’s refurbishment was the conversion of the building’s atriums from natural ventilation to mechanically air conditioned spaces.
The existing building configuration featured five atria across the building, located on the south-west façade, with each atria connecting four office floors. The naturally ventilated winter garden was rarely used with glazing used to separate the air conditioning office space and naturally ventilated atria.
“The new design was to make these spaces air conditioned, and open to the office areas,” says Boorman.
The atria were provided with sidewall jet diffusers from new FCUs to ensure good air distribution in the large open space. High-temperature exhaust was provided to remove excess heat at the top of the atria, and radiant heating convectors were provided at low level adjacent to the façade to offset cold down drafts and ensure comfort in winter.
Due to the building’s existing structural constraints, the radiant heaters at the base of the atria were located above the exposed slab. A risk assessment was carried out in accordance with Annex F of BS EN ISO 1372.1:200 to illustrate that there was no safety issue or potential of burns from touching the exposed radiators.
The mechanical smoke management system was also modified to enable three floors to be interconnected via stairs. Existing infrastructure was retained, with new stair pressurisation fans installed in discrete locations to deal with the increased in airflow required.
According to Boorman, the introduction of mechanical air conditioning to the atria required that the existing façade be upgraded to meet current National Construction Code (NCC) Part J requirements.
“We collaborated with our ESD and electrical engineers,” he says, “to provide an alternative solution that would retain the existing façade.”
This was realised under the Section J renewable energy offset provisions that allowed the installation of solar photovoltaic panels to account for additional energy used by the façade, and close the compliance gap.
Internally, mechanical services systems were designed to optimise thermal performance, comfort and achieve Green Star points.
Extensive modelling was also completed to ensure the space could be used for general office purposes.
“Our approach contributed to a circa-$3 million saving, plus program and construction benefits and resulted in no crane being required for the project,” says Boorman.
Across the building, a new lighting design has provided improved lighting conditions within the new lobby, pavilion building, arcade and refurbished atria.
An electric lighting design within the lobby was developed that took into account daylighting to determine the play of lighting and overall level of brightness required. The interior façade within the lobby comprises of curved visual glass with integrated gold mesh lit from numerous locations.
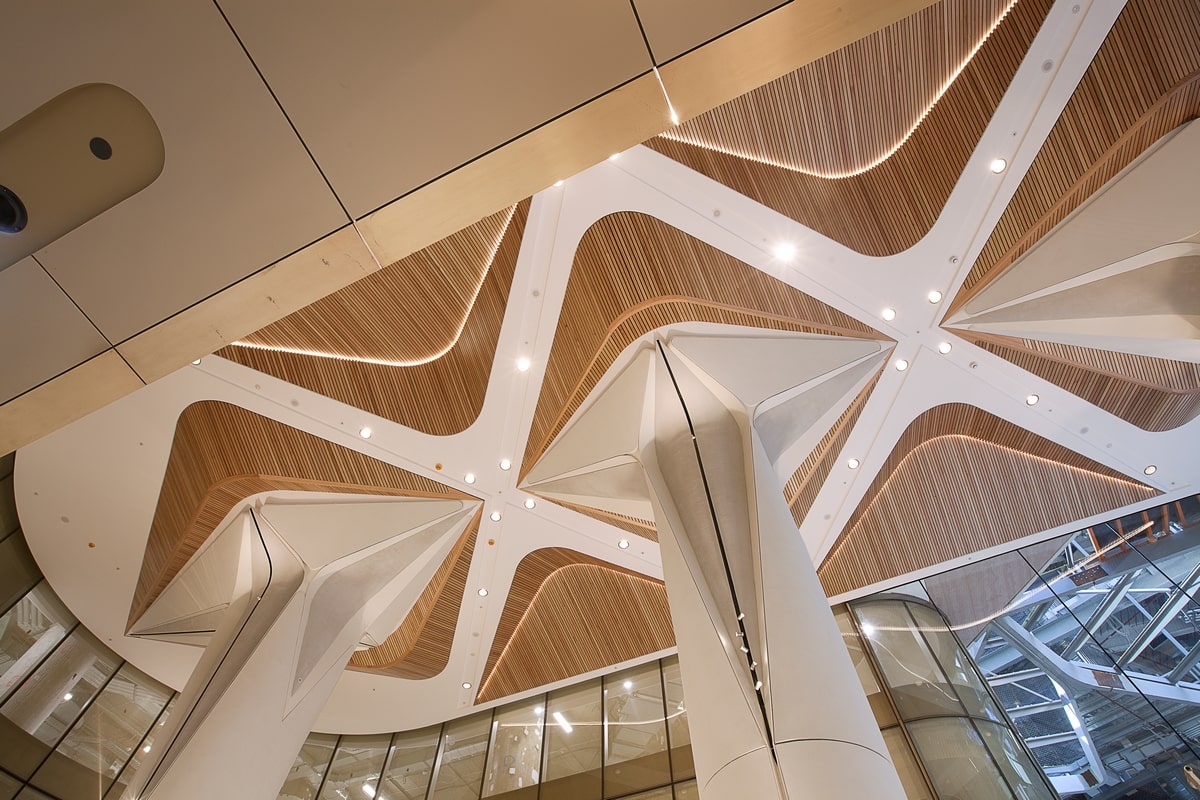
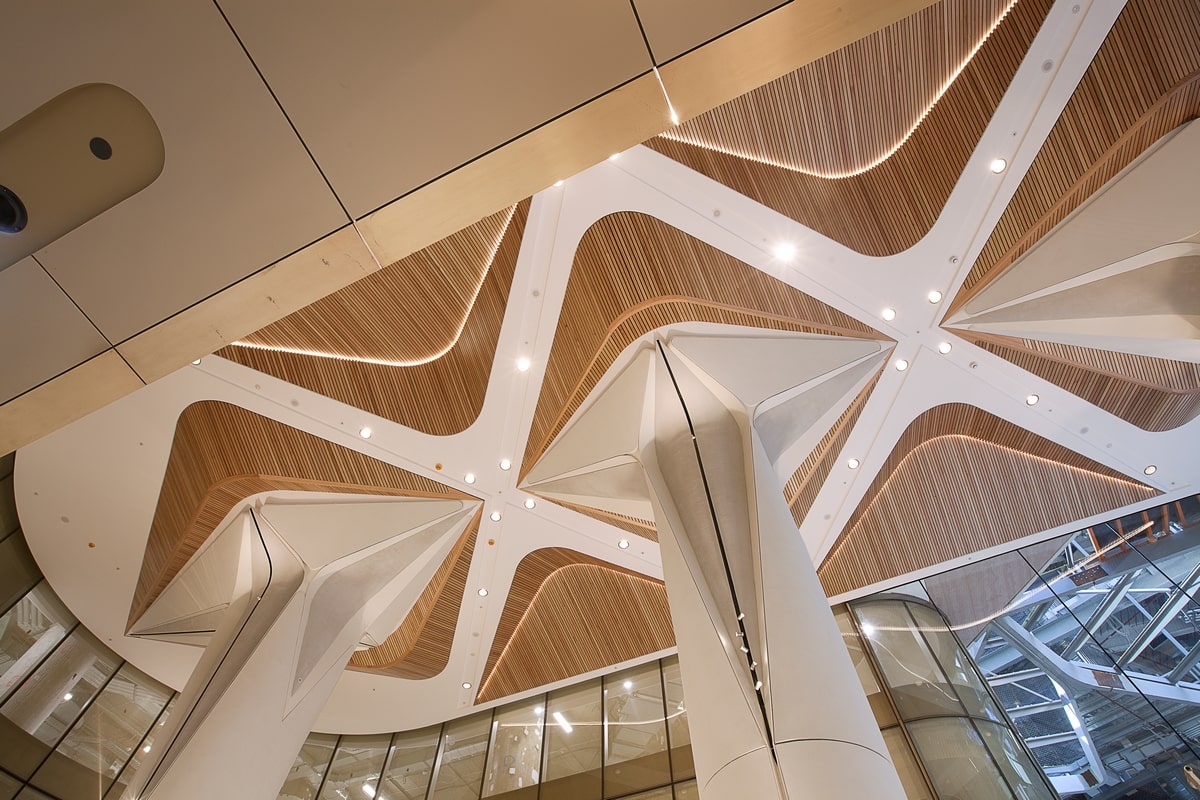
A triumph of reuse
As well as delivering more than 38,000m² of A-Grade commercial office space across the 46-year-old building, the refurbishment of 388 George Street is a triumph in mechanical services reuse.
“Given there were many items to be retained, consultation with all parties was critical to ensure any existing systems, equipment or external appearance were not being affected,” says Serret.
“It was very difficult to create any new penetrations in the existing structure, making coordination and reticulation of services that much harder.”
The building now features a new integrated communications network (ICN) allowing all building systems to communicate via a single, building-wide network.
This provides a framework for monitoring all sub-systems and control of the building including BMCS, security, vertical transport, smart lockers, lighting control systems, fire systems, solar PV generation and smart metering.
Following practical completion in November 2020, Arup has remained involved in the tuning phase. This work has been interrupted by COVID-19 restrictions that have delayed occupancy of some tenants.
Despite this, all sustainability targets are on track to be achieved.
“We are awaiting a minimum occupancy of 70 per cent to complete the ongoing phase of quarterly review of the metering data against the NABERS Energy modelling predicted performance,” says Boorman.
This includes the implementation of an integration platform to analyse the BMCS trend logs, tuning the controls algorithms, and measure energy, water and gas data.
Project at a glance
The personal
The Personnel
Architect: HDR/fjmtstudio
Builder: Multiplex
Client: Brookfield Properties and Investa Gateway Offices (IGO)
Consulting Engineer (multidisciplinary): Arup
Mechanical services contractor: Fredon
The equipment
BMS: Schneider
Chillers: York
Controls: Schneider
Fans: Fantech
Fans (AHUs): Ziehl-Abegg
FCUs: Temperzone
Grilles: QAE
Heat exchangers: AHTT
Mechanical electrical boards: Kerfoot
Pumps: Masterflow
Radiators: Isan
Sensors: Schneider
Solar PV: Astroenergy
VSDs: Danfoss
(Source: Arup)

This article appears in Ecolibrium’s May 2022 edition
View the archive of previous editions
Latest edition
See everything from the latest edition of Ecolibrium, AIRAH’s official journal.