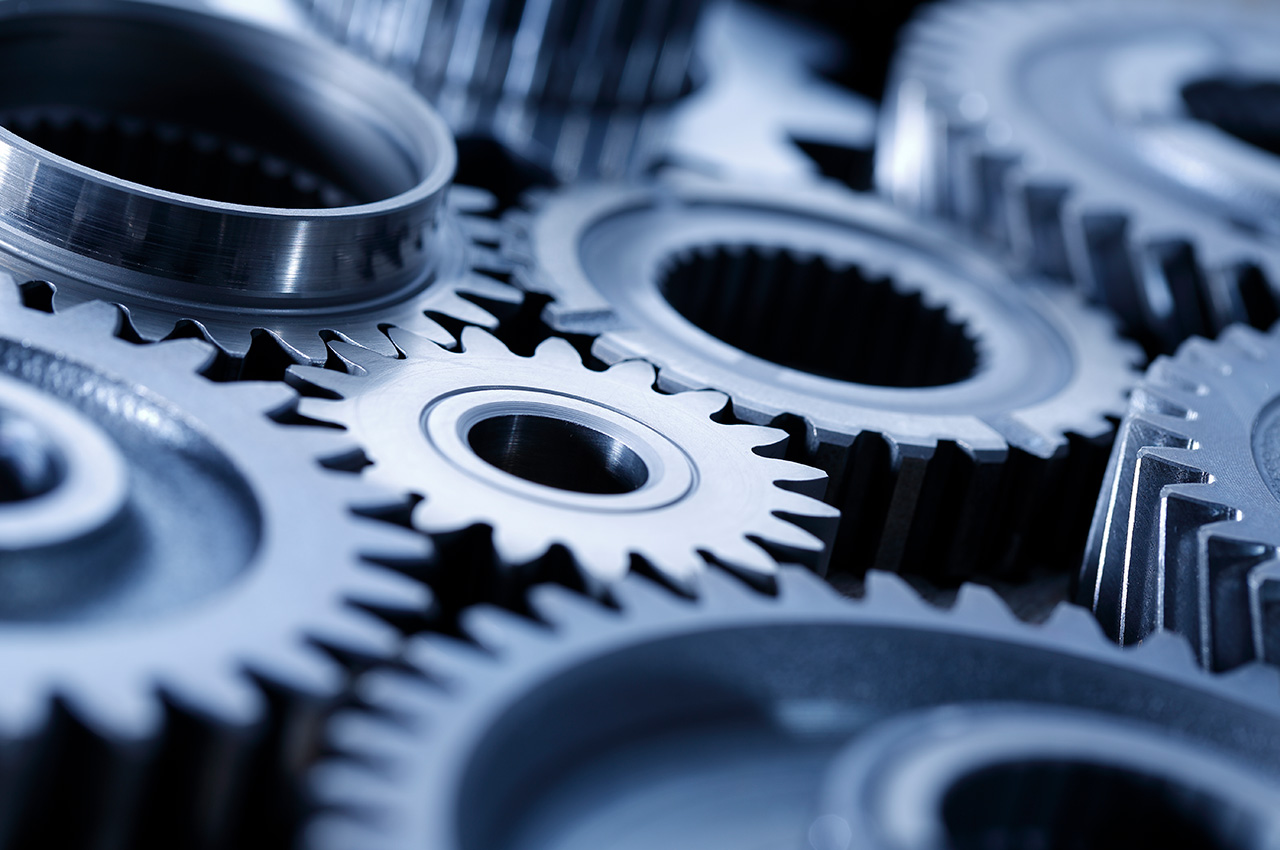
When Ecolibrium last took a deep dive into the state of Australia’s HVAC&R manufacturing base, we discovered that contrary to negative commentary at the time, there was a strong beating heart. As Sean McGowan reports, the challenges may differ today but the same optimism and ingenuity remains.
Let’s face it. The pandemic, coupled with the crisis in Eastern Europe and continuing international trade relations, have turned everything on its head.
It has forced a spotlight on economic problems that were previously papered over in a carefree, pre-pandemic world. Training and skilled labour shortages, wages, an overreliance on cheaper imports, and the cost of doing business in Australia all existed long before COVID-19.
Then there is the topic – the big topic – of the disruption to global supply chains.
Where once it was easy to ship in anything and everything from Asian manufacturers at a fraction of the price of a locally made item (if indeed there was one), the pandemic’s impact on the supply of electronics, components, equipment and even timber, will continue to be felt for years to come.
According to professional services firm KPMG, the pandemic has made obvious the flaws in global trade and shown that most organisation’s supply chains are not nearly as resilient as they were thought to be.
Consequently KPMG sees a structural shift toward economic nationalism – and what is described in its Supply Chain’s New World Order paper as a “make where you sell and buy where you make” approach emerging.
How far this extends in an Australian context is debatable (the manufacturing powerhouse we are not). But the idea that supply shortages should stoke our inner nationalism is hardly surprising.
“There is a lot of support to source and buy local, and there is momentum around building Australia’s sovereign capability,” says Seeley International group managing director Jon Seeley, Affil.AIRAH.
“Customers are more actively seeking out locally manufactured products, particularly as international supply chains become riskier or more unreliable with the impact of COVID and other trade issues.”
It’s a similar view shared by another local manufacturer, Fantech.
“Local manufacturing provides flexibility, reduced lead times, improved service and responsiveness, and is a critical ingredient to our ongoing success,” says Fantech managing director, Anthony Lamaro.
“We also have greater control over product quality, and minimise ourselves and our customers to world events that are impacting current supply chains.”
Is a paradigm shift occurring? Is KPMG right in saying that the supply chain’s new world order might be one where efficiency is de-emphasised and the lowest cost is no longer the dominant definition of value?
“The current challenges caused by this global pandemic provide an opportunity to reset the baseline for Australian manufacturing through clear policies that support and incentivise R&D and the application of new manufacturing automation and technologies,” says Henry Brunekreef, national supply chain practice lead at KPMG.
As Seeley International put it, the country has been presented with a once-in-a-lifetime opportunity to reset Australian manufacturing.
In talking to a number of leading local HVAC&R product manufacturers, those wheels are already in motion.
Fans of their work
Company: Fantech
Managing director: Anthony Lamaro
Headquarters: Dandenong South, Victoria
Manufacturing Locations: Victoria, Queensland and New South Wales
Employees: 230 local staff
Export: Yes
Fantech was founded in 1973 and has since been at the forefront of fan engineering and acoustic control products. It manufacturers one of the largest ranges of air movement products sold across Australia, including fan products that are installed in HVAC systems for commercial, industrial and domestic applications.
Where does Fantech manufacture from?
Anthony Lamaro: We currently manufacture across four locations within Australia – Queensland, NSW and our two manufacturing facilities in Victoria.
Our recently purpose-built 20,000m² facility in Dandenong South has been designed specifically for competitive manufacturing and state-of-the-art logistics. This facility incorporates lean manufacturing assembly cells that provide both efficient and responsive manufacturing results. The Dandenong South facility also includes the latest technologies in smart logistics and warehousing, which automatically generate replenishments and stock movements.
Burra Steel, our second Victorian manufacturing facility, manufactures all of Fantech’s steel and metal components used across our range of products. The Korumburra facility is the second largest manufacturing employer in the area, and home to unique world-class fan case manufacturing equipment.
Why does Fantech choose to manufacture in Australia?
Over Fantech’s 50-year history, we have always remained focused on local Australian manufacturing. The diversity and range of our products as well as physical size really lends itself to local manufacturing.
Local manufacturing provides flexibility, reduced lead times, improved service and responsiveness, and is a critical ingredient to our ongoing success. We also have greater control over product quality and minimise ourselves and our customers to world events that are impacting current supply chains. Our local manufacturing activities also support many other local manufactures within our supply chain.
What are the challenges facing Australian manufacturing at present?
There are many challenges facing Australian manufacturing including skills shortages, inflation, global supply chain issues, the unpredictability of international freight, and cost increases of components and raw material. There always remains a challenge of blending the need for local and overseas input and content to meet customer and market demands. Australian manufacturers cannot survive on purely overseas or local supply chains, and the blending of this supply chain with strategic partners remains critical for success.
How do local manufacturers stay competitive?
We remain flexible, adaptable and focus on service delivery. I believe local manufacturing also needs to be brave and focus on capital investment to support efficiency and productivity while ensuring products are of the highest quality.
Fantech has continued to invest in technology like WMS (warehouse management systems) to help improve productivity and responsiveness. Our dedication to lean manufacturing techniques ensures that we minimise waste in our production processes, and continual staff engagement and training ensures that we are investing in our staff to be the best they can be. Working with other local manufacturers, and sharing experiences and problems, also helps to ensure that we are aware of industry trends and opportunities to improve.
What does the future hold for Australian HVAC&R product manufacturing?
There is a new sense of positivity around Australian manufacturing, as recent history has highlighted that it is critical for all businesses. It will become a more important part in all supply chains in the future as organisations look to make lead times more reliable and product availability more predictable.
I get the sense that businesses are now looking more for Australian-made products as they look at ways to maintain quality and secure supply.
Seal of approval
Company: Seeley International
Group Managing Director: Jon Seeley, Affil.AIRAH
Headquarters: Lonsdale, South Australia
Manufacturing Locations: South Australia, New South Wales, Colorado USA
Employees: Over 450 local and international staff
Export: Yes
Celebrating 50 years of “World Leading climate control solutions”, Seeley International is Australia’s largest evaporative air conditioning and ducted gas heating manufacturer, developing ingenious, energy efficient cooling and heating products.
Where does Seeley manufacture from?
Jon Seeley: Seeley International’s head office and main manufacturing operation is in Lonsdale, South Australia, with other manufacturing operations in Albury, New South Wales and in Denver, Colorado (USA).
Why does Seeley choose to manufacture in Australia?
There is a lot of support to source and buy local, and there is momentum around building Australia’s sovereign capability. Customers are more actively seeking out locally manufactured products, particularly as international supply chains become riskier or more unreliable with the impact of COVID and other trade issues.
We might have higher production costs in Australia, but we live in a great country. To compensate, we must innovate like there is no tomorrow, use world-class technology and have the highest levels of automation in our production processes.
What are the challenges facing Australian manufacturing at present?
Continuing rising cost of raw materials in volatile and unstable global markets have widespread implications for Australian-based manufacturing. From rising energy costs to unexpected fluctuations in raw material and freight costs, it is difficult for manufacturers to maintain profitability. With supplies of many raw materials becoming increasing harder to secure, and continuing commodity price volatility, it is difficult for manufacturers to decide whether to either absorb some of the additional costs, or pass price increases on to customers.
How do local manufacturers stay competitive?
Seeley stays competitive by ensuring a strong R&D investment, focused on energy efficiency, peak demand reduction, health and biological control and extreme climate performance capability.
Particularly in the commercial world, we are seeing the convergence of sustainability and health, with the growing challenge for buildings being the efficient delivery of fresh, outside air.
What does the future hold for Australian HVAC&R product manufacturing?
Seeley International believe that COVID-19 has presented Australia with a “once-in-a-lifetime opportunity” to refocus on the benefits of manufacturing at home. It is time to refocus on local manufacturing to capitalise on growing demand for Australian made products.
Temper of the times
Company: Temperzone
Group Brand Manager: Damien Walsh
Headquarters: Blacktown, New South Wales
Manufacturing Locations: New South Wales
Employees: More than 230 local staff
Export: Yes
For more than 65 years, Temperzone has designed, manufactured and supplied Australian- made commercial and industrial air conditioners. Today, Temperzone Australia manufacturers a range of commercial air-cooled package units, split ducted systems, water- cooled package units, chilled water fan coil units and air handling units.
From where does Temperzone manufacture?
Damien Walsh: The Temperzone factory is based in Blacktown, Sydney where it first began. Temperzone has moved several times over the years and our manufacturing has grown to meet local demands.
The factory in Blacktown employs 150 local factory team members providing employment for the greater western Sydney area.
Why does Temperzone choose to manufacture in Australia?
The main advantage of designing and manufacturing locally is the ability to produce equipment that matches the unique needs of Australian customers in a short period of time.
What are the challenges facing Australian manufacturing at present?
Apart from higher wages, insurance costs, land taxes – factories need big blocks of land – and payroll taxes, we also have a raft of regulatory, safety and social responsibility obligations that do not apply to many of our competitors who source product from South-East Asia.
We are certainly supportive of the additional requirements, as they provide for a safer and more inclusive workplace, but they do add costs to our finished products that is not burdened by imported product.
Sourcing of materials and high technology components can also be challenging, as there is little manufacturing of components in Australia. Furthermore, local manufacturers are often faced with import duties on components they purchase when the whole finished product they are competing with can be imported duty-free if the country of origin has a Free Trade Agreement with Australia.
Another disadvantage is that Australian manufacturers do not have the economies of scale to apply the vertical-integration structures of the large overseas manufacturers who design and produce their own compressors, motors, integrated inverter control PCBs, etc. An Australian manufacturer is typically reliant on selecting and purchasing discrete components from a vendor’s catalogue at a higher price.
How do local manufacturers stay competitive?
To be competitive local manufacturers need to have a point of difference or produce niche products, and of course, be as efficient and cost-effective as can be in their local operations.
What does the future hold for Australian HVAC&R product manufacturing?
To be sustainable Australian manufacturers need to target their offering to be different to overseas mass-produced commodity products.
Both sides of government are spruiking support and growth for Australian manufacturing, but we suspect this will be for a select type of manufacturing such as healthcare, food, defence and environment. They are also proposing policies to stimulate wage growth, which will be a bit counteractive to investing in local manufacturing.
The sweet smell of success
Company: Air Odour Solutions
Managing Director: Benjamin Clark
Headquarters: Smithfield, New South Wales
Manufacturing Locations: New South Wales
Employees: 15
Export: Yes
Founded in 2012, Air Odour Solutions manufactures kitchen exhaust filtration systems including proprietary kitchen exhaust hoods, misters, carbon filtration, ozone generators, duct-mounted UV ozone, negative-pressure units, pollution-control units and UVC filter boxes.
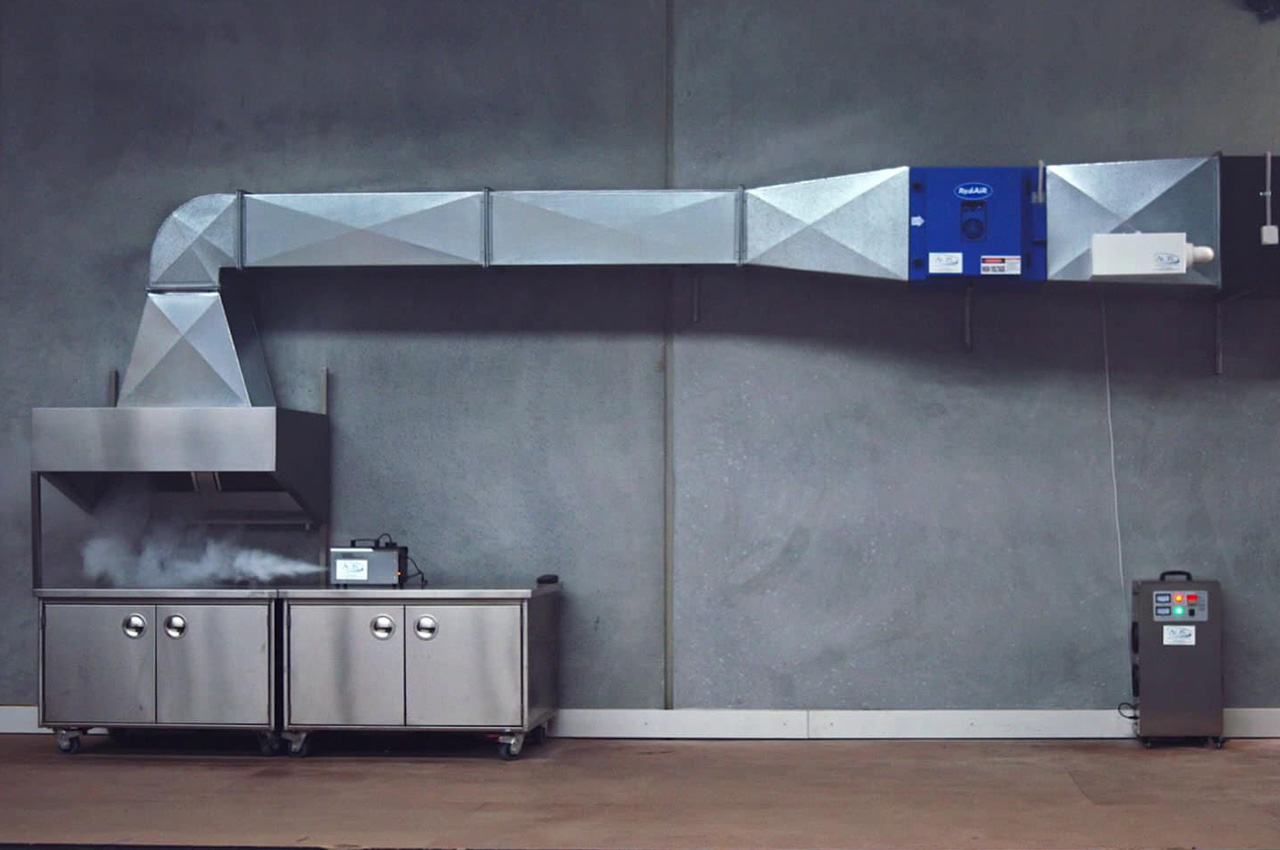
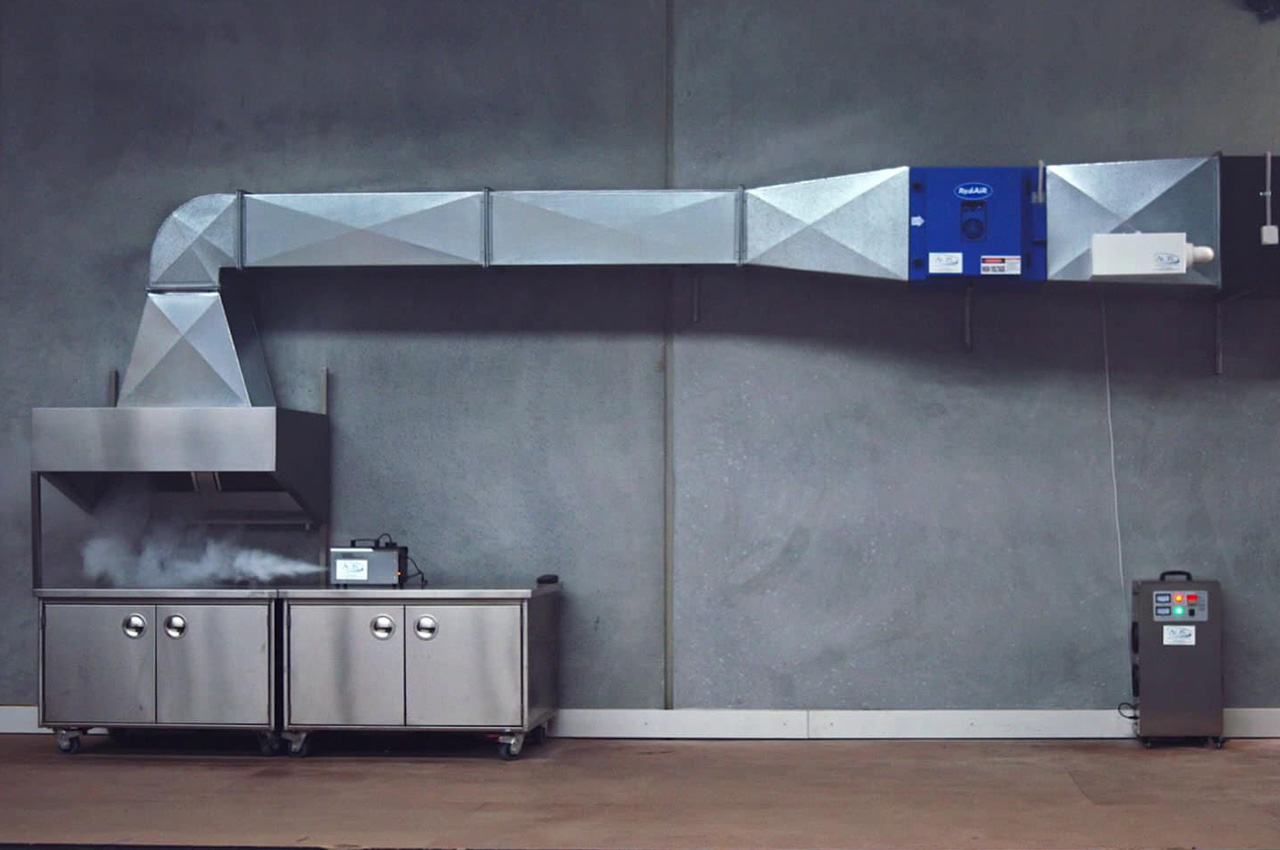
AOS integrates innovation into its strategy.
From where does Air Odour Solutions manufacture?
Benjamin Clark: Air Odour Solutions (AOS) is based in Smithfield, in the western suburbs of Sydney.
Why does Air Odour Solutions choose to manufacture in Australia?
AOS chooses to manufacture in Australia because we have quality control through all the stages of design, engineering and manufacture to the end product. AOS has control of what we manufacture and engineer, which is undertaken in our factory. And with any changes to our product order we can adapt quickly. This leads to a competitive advantage in the marketplace.
The biggest advantage is a reduction in delivery times to the customer. Manufacturing in Australia allows us not to be reliant on overseas supply chains.
What are the challenges facing Australian manufacturing at present?
Rising costs and lead times of raw materials have risen significantly. AOS has seen an up to 30 per cent increase in the cost of stainless steel. It is now evident that rising costs and lead times are cascading through the supply chain and ending up as a price increase to the end consumer because of the volatile nature of the economy.
Also, the need to provide more innovative, carbon-neutral and sustainable energy-efficient products.
I believe Australian businesses need to invest in new technologies to create a competitive advantage in the marketplace by boosting productivity through automation and innovation. This enables new products to be created.
Our long-term vision and strategy, for many years, is to invest profits back into the business. Significant investments have been made to the certification, manufacturing, engineering and research and development of the AOS products.
How do local manufacturers stay competitive?
There’s a need to focus on breakthrough innovation that reshapes business models. This will create new products and services that can be sold locally and internationally. Businesses that invest in innovation over longer periods will out-perform the competition.
Manufacturing companies should integrate innovation into their strategy and into the operating business model, and a culture making innovation a prime consideration moving forward.
What does the future hold for Australian HVAC&R product manufacturing?
Australia has enormous potential in the manufacturing sector. The Australian government could implement more tax incentives and grants for Australian manufacturers for R&D investment work to enhance productivity and innovation growth as a key driver for economic growth and prosperity.
Australians are some of the great thinkers and problem-solvers in the world.
Regulation nation
Company: Regulator Australia
Chief Executive Officer: Neil Kenny, AM.AIRAH
Headquarters: Melrose Park, New South Wales
Manufacturing Locations: New South Wales
Regulator Australia commenced business as an importer of Swedish-made controls in 1974. Recognising these controls weren’t entirely suitable for the Australia climate and more suitable for heating, the company began designing and manufacturing its own range of control systems from its Marrickville facility three years later.
From where does Regulator Australia manufacture?
Neil Kenny: Regulator Australia operates from its manufacturing facility in Melrose Park, in Sydney’s inner western suburbs.
Why does Regulator Australia choose to manufacture in Australia?
Local Australian manufacturing removes the problems involved with manufacturing overseas [in terms of] stock supply issues and quality control. Australian-made products have always had a high attention to detail for quality and customer satisfaction. Manufacturing locally also gives us the ability to make changes and updates faster to suit local requirements to better support our customer network.
What are the challenges facing Australian manufacturing at present?
The biggest issue facing electronic manufacturing around the world, and of course here in Australia, is the sourcing of components. So forward planning and advanced pre-ordering of critical components is essential.
Additionally, we now have to keep our thoughts open to different components and options moving forward so we do not lock ourselves into a situation where a product is made redundant due to part supply issues.
What does the future hold for Australian HVAC&R product manufacturing?
With the evolution of electronic components over the past few decades, the size of controllers has shrunk, while the capacity and complexity of control solutions has increased immensely. Regulator continue to strive to invent, manufacture in Australia and deliver solutions to our customers that make sense.
The big issues
What are the big issues facing Australian HVAC&R manufacturers? Ecolibrium asked that very question, and here’s what our manufacturers said:
High employment costs
Including wages, workers compensation, payroll tax and restrictive work practices.
Supply chain volatility
According to Fantech, the challenges of supply chain volatility, supply issues and freight costs affecting locally and overseas content is impacting prices. This is then impacting builders and sub-contractors facing fixed-price contracts, as well as local suppliers and manufacturers.
Shipping costs
AOS says soaring shipping costs have hit importers and exporters hard, with cargo container hire sometimes tripling in price. The cost of a shipping container pre-pandemic was $5,000, and can now be as high as $20,000.
Skilled labour shortages
Skills shortages are hampering growth and investment, and putting strain on many existing businesses.
Environmental Policy impacts
According to Temperzone, the Kigali Amendment to the Montreal Protocol effectively disadvantages Australian manufacturers by imposing a restriction on bulk importation of HFC refrigerant (needed for local manufacture) from 2019, whereas products manufactured in Article 5 countries (including China, Malaysia, Thailand, Korea and others) do not have any HFC restrictions imposed until 2029, or in the case of India, 2032.
Differing state-based regulations
Temperzone says state-based regulations or efficiency incentive programs add further complication and restrictions to product offerings.
Higher energy costs
According to AOS, Australia’s high energy costs and declining energy security are damaging the ability of local manufacturers to compete globally. This can impact both current and future manufacturing investments.
Already, significant investments in energy-intensive manufacturing, by Australian and international companies have gone offshore because of uncertainty about energy security or high prices, while local investments or expansion plans have been put on ice or rejected.
Pandemic management
Management of the COVID-19 pandemic continues to put pressure on the available workforce.

This article appears in Ecolibrium’s May 2022 edition
View the archive of previous editions
Latest edition
See everything from the latest edition of Ecolibrium, AIRAH’s official journal.