Premium content
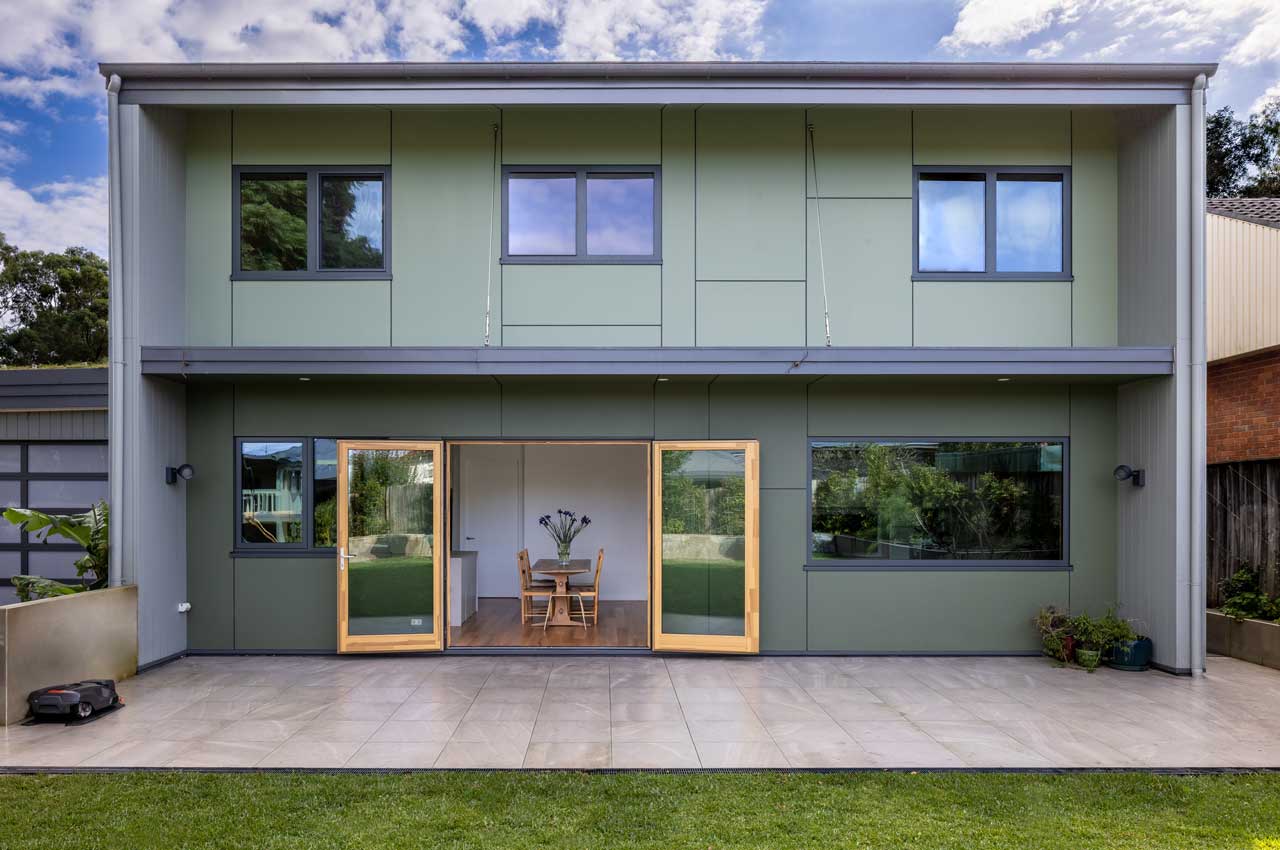
In a quiet street in Sydney’s northern suburbs resides New South Wales’ first Passivhaus Premium certified building. The residential home is the result of more than five years of painstaking research and planning by a family determined to future-proof their investment against climate change.
Located on a large suburban block in northern Sydney’s Asquith, a net-zero energy Passivhaus now sits proudly among neighbouring 1950s era weatherboard homes much like the one it replaced.
Typical of Sydney housing stock, these homes built of timber frame on brick piers offer little to no wall or floor insulation. Combined with single-glazed aluminium frame windows, and no external shading, such homes can become unbearable for their occupants when the weather reaches its extremes.
“I knew I wanted a certified Passivhaus, but the question was could I afford it? And could I find someone to design and build it?”
Nunn, head of platform operations and ESG investing at AMP Capital and former Chair of the Australian Passive House Association (APHA), purchased the Asquith property with his wife Maylynn in 2016.
They had been searching for a suburban home to raise their children. Yet after finding house prices on Sydney’s North Shore too high, looked further afield before discovering a suitable property in Asquith.
“In 2016, there were still properties for sale on big suburban blocks close to the train station for under $1 million,” Nunn says. “I knew that if I spent our entire borrowing capacity buying a house closer to the city, then I would never realise my dream of building a sustainable house.”
After moving into the 1950s weatherboard in April 2016, the family saved for the deposit on a construction loan while going through an extensive planning and design process to build their “dream” home.
“I knew I wanted a certified Passivhaus,” Nunn says. “But the question was could I afford it?
“And could I find someone to design and build it?”
After engaging the only certified Passivhaus architect in Sydney at the time, Nunn commenced the design process. But it wasn’t long before he became unhappy with the design direction and the initial cost estimates to build it.
After thoroughly investigating other options, including an attempt to convince a volume builder to adapt an off-the-shelf design to Passivhaus, Nunn went back to the drawing board.
By this time, more certified Passivhaus designers and builders had emerged in Sydney, including fellow APHA board member Andy Marlow of Envirotecture.
“So I engaged Envirotecture to develop a concept design based on what was, by now, my very extensive and detailed written brief – and my three-dimensional SketchUp model,” says Nunn.
“I don’t think they’d ever had a client come to them with such well-formed views about the details of the house they wanted – let along a 3D model!”
Envirotecture developed three variations of Nunn’s initial concept drawings before one was selected and taken to the detailed design stage in preparation of construction.
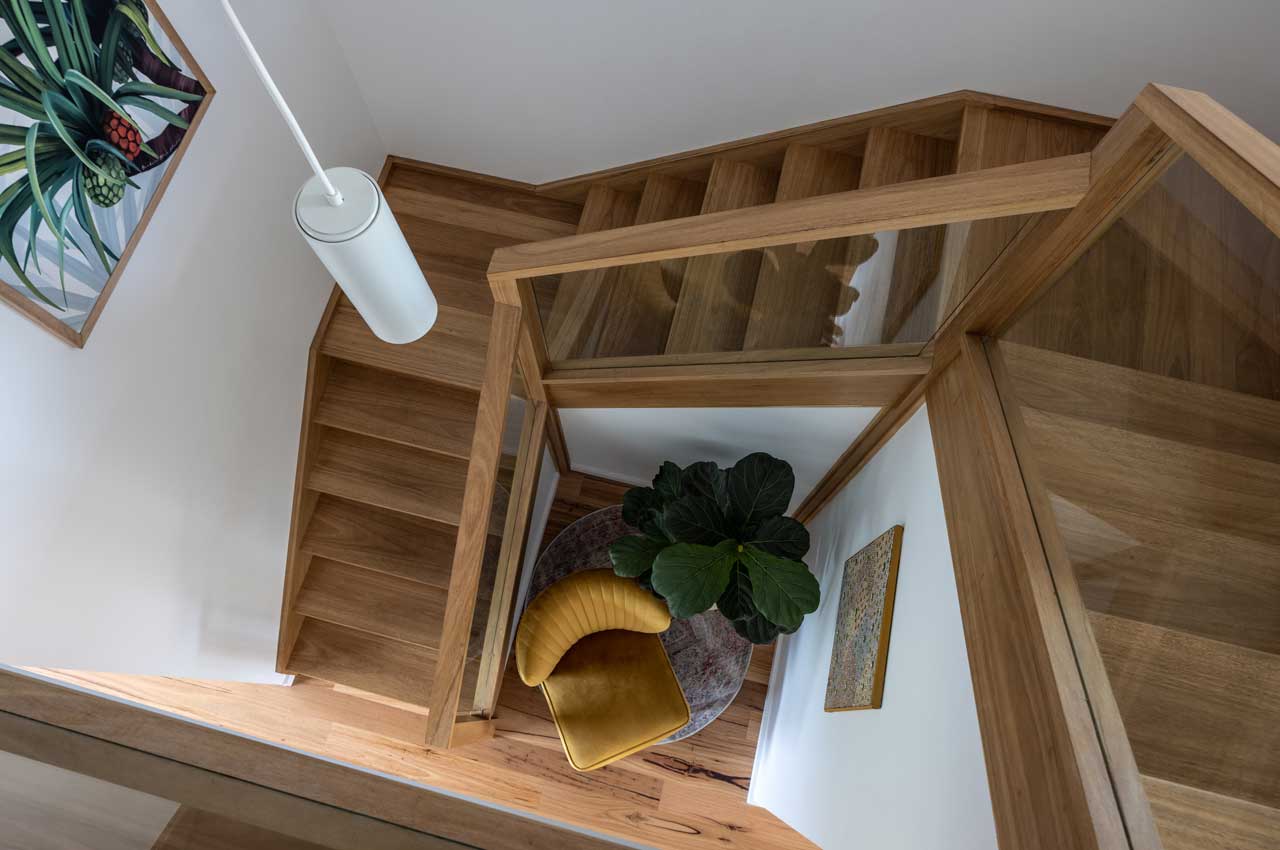
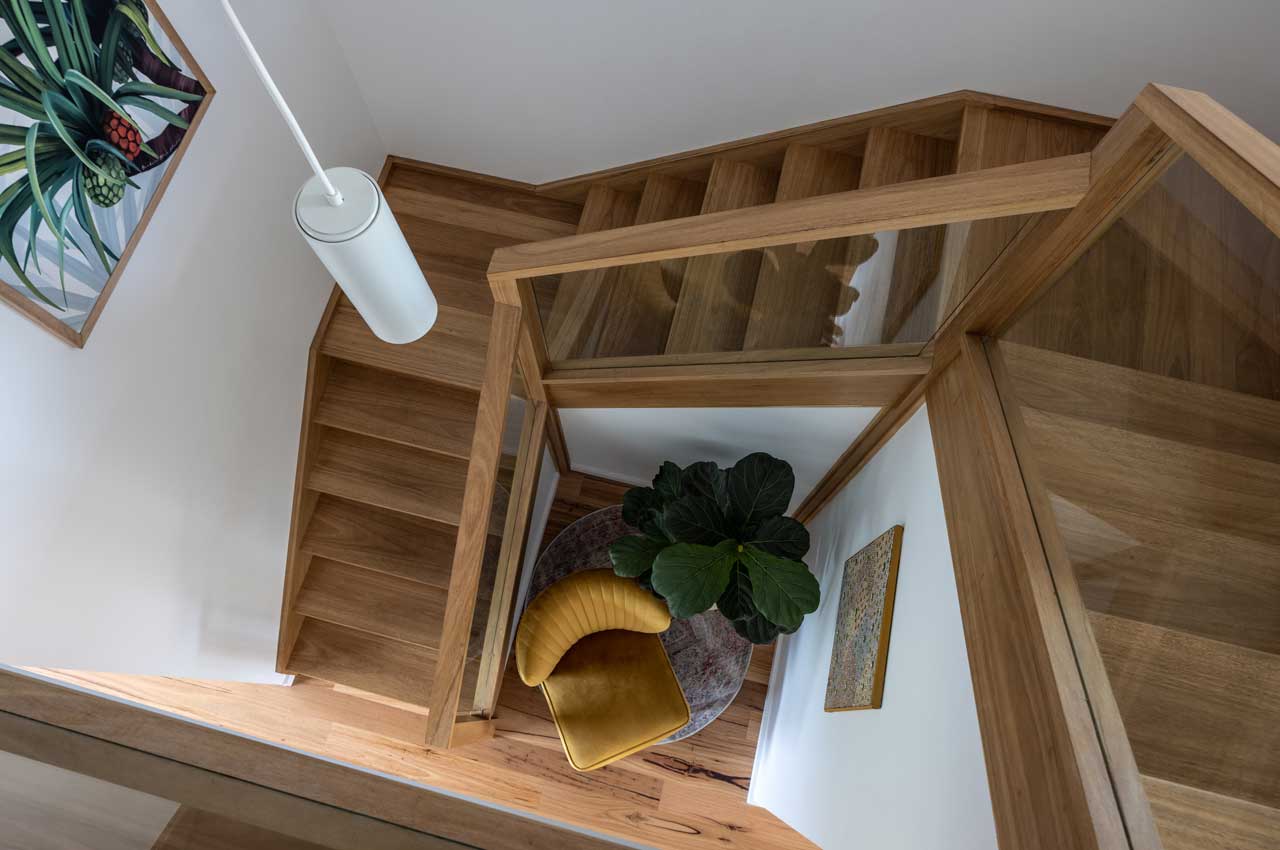
The build
With few certified Passivhaus builders in Sydney, Nunn recognised there would be risks in the construction of a Passivhaus design.
“Going into the process of building a Passivhaus, one of the key risks was achieving the airtightness criteria, which requires great attention to detail by the builder to ensure the airtight membrane is not punctured by plumbing and electrical trades in particular.”
An opportunity arose to visit a manufacturer of Passivhaus certified modular prefabricated wall and roof panels*. Through his role with APHA, Nunn recognised that using this technology could remove some of the risk in achieving airtight criteria.
“Using the … system also gave me access to a very experienced team who had built many certified Passivhaus buildings before,” says Nunn.
“They were also able to work with Andy to resolve details during the design phase, and to brief and support our builder – Superior Constructions – during construction. This gave me a lot of confidence that I was going to meet the Passivhaus standard.” (See breakout: “Airtight Prefabrication”).
Demolition of the existing house commenced in September 2020, with construction of the slab and pre-fabricated walls and roof panels occurring soon after.
According to Nunn, the build proceeded very rapidly under the supervision of Superior Constructions, with the whole frame erected within just three days.
“It was weatherproof too, which was lucky because it poured soon after,” Nunn says. “That’s another benefit of the prefabricated system – you don’t have your frame sitting out in the weather getting wet, where moisture can get trapped in the structure and cause problems down the track on conventional builds.”
“From demolition to occupancy, construction of the four-bedroom, double-storey Passivhaus took just eight months – even with the disruptions caused by the COVID-19 pandemic.”
Air supply
Like other Passivhaus projects, the Asquith home relies on a mechanical ventilation heat recovery (MVHR) unit to provide a continuous supply of filtered fresh air to every occupied room in the house.
The unit also extracts air from the kitchen, toilets and circulations spaces.
Sized with the assistance of some Passivhaus planning package software, the design calculations were reviewed by the mechanical services provider, who then supplied and commissioned the MVHR unit.
According to Nunn, the heat exchanger is highly efficient such that there is very little energy cost associated with the continuous supply of filtered fresh air into the home.
The design also features an F7 filter on the supply-air side, and a G4 filter on the return-air side.
“This provides a great level of filtration of fine particulates, so the fresh air supply is always clean,” says Nunn.
In addition, Nunn has had a HEPA filter cassette installed. In normal operation, this filter is bypassed, but in the event of bushfire or other severe pollution event this section of ductwork can be opened and the HEPA filter inserted to provide a very high level of fine particulate filtration.
“This does, of course, increase the fan power,” Nunn says. “But it is well within the capacity of the MVHR unit.”
Given the impact of the 2019/2020 bushfires on Sydney’s air quality – and the home’s proximity to the Ku-ring-gai Chase National Park – Nunn was determined to protect his family and home from similar events in the future.
“This should be something everyone considers in new buildings – the option to provide a higher level of filtration during extreme events,” he says, “which could include bushfires and thunderstorm asthma events.”
Nunn says living with the MVHR unit is simple.
“I love the fresh air it is continuously providing, and that it is constantly filtering out pollutants,” he says. “It is easy to change the filters – about once every three to six months depending on air quality. And it is amazingly quiet. You can’t even hear it running when you are standing right next to it.”
Airtight prefabrication
Prefabrication of Passivhaus certified walls and roof components helps ensure the standard’s airtightness requirements are met – while also reducing the construction program by six to eight weeks.
Each prefabricated wall panel used at the Asquith Passivhaus is made from laminated veneer lumber (LVL), which remains straight and square, unlike normal framing timber, which can be warped.
Insulation – in this case a recycled glass product – is fitted between the LVL frame and studs, before the airtight membrane is fixed to the frame. Once on site, the join between the panels are taped together using specialist airtight tape.
To minimise penetrations through the airtight membrane, wooden battens are fixed to the frame to create a services cavity where electrical cables and plumbing pipework can be run. Once installed, plasterboard is fixed to the services cavity battens.
Externally, Nunn chose to clad the home in watertight, termite resistant panels made from recycled Australian native hardwood timber offcuts.
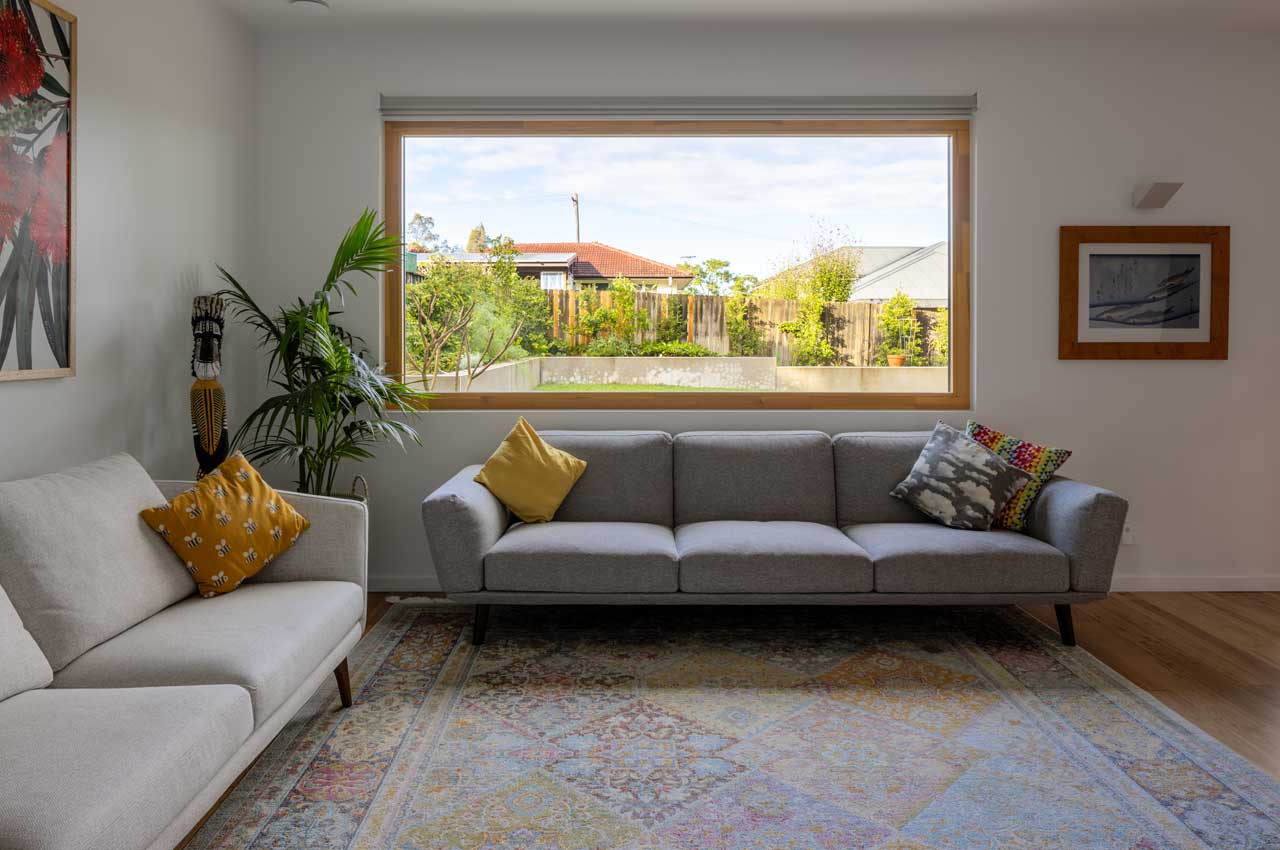
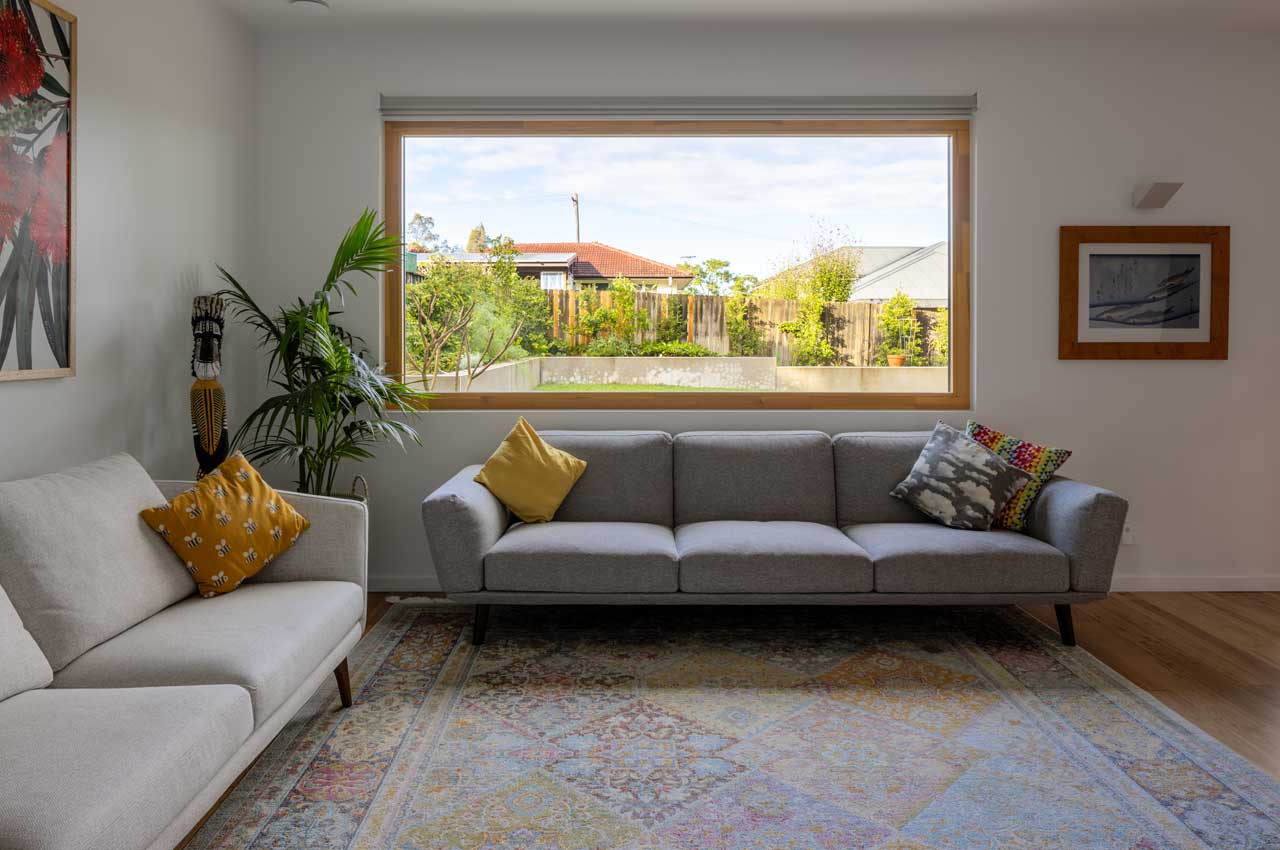
Achieving net-zero
Part of achieving Passivhaus Premium certification is the requirement for the building to be net-zero energy.
Critical to achieving this is the solar PV array that covers the entire north-facing slope of the home’s gable roof – reflecting the design of the Passivhaus terrace houses in Vauban, Germany.
Nunn oversized the solar array for the home. Consequently, it generates excess electricity that is sold to the grid.
The aim was to set the house up to over-produce so that it could be net-zero energy over the course of the year, as well as participate in the emerging demand response or “frequency control ancillary services” (FCAS) markets via a virtual power plant (VPP).
At the time of publication, Nunn was in the process of installing more detailed energy meters, as well as temperature, humidity and indoor air quality (IAQ) sensors.
He hopes to partner with an academic institution to evaluate the temperature, humidity and energy data from the previous house (from which he has a few years of data) against the occupied data from the Passivhaus.
Sitting down with Chris Nunn
Eco: How did you first learn about Passivhaus?
Nunn: I knew about Passivhaus from my time working as a sustainability consultant in London between 2005 and 2011, which was about the time it was gaining traction in the UK.
While studying at the London School of Economics I’d had the opportunity to visit some model sustainable housing developments, and the Solar Settlement at Vauban in Freiburg Germany really inspired me and still does.
I have been working in sustainability for over 20 years, and I am not aware of a more sustainable development anywhere in the world.
When I first saw the terrace rows of Vauban’s zero emission district – and heard that each resident was making €6,000 per year selling solar electricity into the grid from the building integrated solar panels that form the bulk of the roof. I thought – this is the kind of house I want to live in.
Eco: There are some similarities between the design of the terrace houses at Vauban and your house, are there not?
Nunn: You can see the similarity between the design of the Vauban houses and our house. For instance, the asymmetrical gable roof with a longer pitch facing the sun completely covered in solar panels.
Shading on the solar exposed parts of the façade, certified to the Passivhaus Standard, and a simple rectangular footprint with only four corners to minimise risks around airtightness detailing and thermal bridging. In my view, this is the most rational and sustainable form that a house can take.
Eco: I understand that you explored building something other than a Passivhaus, and even considered whether working with a volume builder could work?
Nunn: I visited the major display home villages in Sydney – and I would encourage anyone contemplating building a house to visit these display home villages as you learn a lot about what you like and what you don’t like.
I also took a tape measure and measured room sizes, so I could have a clear view on the dimensions of various rooms that I felt would suit our family’s needs. This helped inform by reviews of plans and the way I ultimately briefed our architect and builder. It put me in a much more informed position.
After getting to the point of having a costed set of plans from a volume builder and understanding how far they were willing to go in terms of improving insulation, installing double glazing with thermally-improved frames (not thermally broken, mind you), and realising they were not prepared to install an airtight membrane, I decided that I would not be satisfied unless I built a certified Passivhaus. So I literally went back to the drawing board.
Eco: And how did you come to select your architect?
Nunn: I chose Envirotecture because they are a leading sustainable design firm and one of the few architectural practices with experience designing and building Passivhaus buildings in Sydney.
At the time we were going through the design process of my house, Envirotecture had recently completed the Thornleigh Passivhaus not too far away from where my house is located. Choosing a designer with Passivhaus experience gave me a lot of confidence that I wasn’t going to be paying for their learning curve or risk making costly mistakes along the way. And that’s how it turned out.
Eco: How challenging was finding a project team, and is that still a barrier to the broader adoption of Passivhaus in Australia?
Nunn: The APHA website has a directory of Passivhaus-certified tradespeople and builders. There are currently 484 APHA members across Australia, so there are now plenty of architects and builders available who can design and build a Passivhaus – it’s no longer a significant barrier.
The barriers now are market awareness and cost. There is work to do to bring the kinds of economies of scale and efficiencies that volume builders deliver, to Passivhaus buildings in Australia (but) this will come with experience.
International studies have shown that every time you build a Passivhaus, you get better at it, you solve problems on each project and that benefits the next project. You develop repeatable details that you know will work.
Published studies on the cost of Passivhaus indicate the additional cost averages between 5 and 9 per cent. Evidence from international case studies shows that the experience of the project team in delivering Passivhaus buildings is a critical success factor for limiting additional costs associated with achieving certification.
Passivhaus can be achieved cost-effectively with the right team, working collaboratively to achieve Passivhaus from the outset.
Eco: You mentioned market awareness. Is Passivhaus well understood in Australia yet?
Nunn: There is a lack of understanding about what Passivhaus is, and its appropriateness for Australian climate zones. There is still limited understanding among customers that the way we currently build buildings will not necessarily deliver comfortable temperatures, low energy costs or healthy indoor environments.
Passivhaus guarantees these things – it means the temperatures will always be stable, there will be continuous supply of filtered fresh air, and energy costs for heating and cooling will be very low. Or in my case, with the addition of solar panels and the achievement of Passivhaus Premium certification, I no longer have energy costs.
In fact, each energy bill I’ve had since occupying my house has been a credit from the energy company because we are exporting significantly more solar electricity into the grid than we are using. Like Vauban, our house makes us money – it doesn’t cost us money.
Eco: Speaking of money, I believe you were the first to use Passivhaus to get a Bank Australia Clean Energy Home loan, which is backed by the Clean Energy Finance Corporation (CEFC)?
Nunn: I was. There was a fair bit of education and extra engagement with the loan assessor to find a way to make it all work with the different staging involved in modular construction, and this is something the banks need to get better at.
We did the heavy lifting to find a solution that worked for the Bank, but it should be the other way round.
It’s great that Bank Australia is offering a discounted mortgage interest rate on construction loads for green buildings. They are a real leader in this space. But like everything, when you are the first, there are challenges that you have to work harder to overcome.
Eco: You recently completed your term as Chair of the Australian Passive House Association (APHA). How long was your involvement?
Nunn: I became involved in the Australian Passive House Association (APHA) in October 2016. I had bought the block at Asquith earlier that same year, so happily the planning phase coincided with my time on the board of APHA. So I was able to inform my own planning process with the knowledge I was gaining by being involved in the APHA board and broader Passivhaus community.
I stepped down as APHA chair in November 2021 after serving the maximum five-year term allowable under APHA’s constitution.
Ed’s note: At the time of publication, Kate Nason serves as APHA chair.
Not alone
In the five years since Nunn and his family commenced their Passivhaus journey, a lot has changed.
While the Asquith home is the first Passivhaus Premium certified building in New South Wales (and one of just 17 projects worldwide), there are many more Passivhaus projects to be found across Sydney and the country.
“It’s great to see more Passivhaus buildings being built,” says Nunn.
“I particularly like seeing the larger scale buildings like The Fern apartment block in Sydney, and the Gillies Hall and Woodside buildings at Monash University in Melbourne. These large buildings are helping to raise awareness among architects and engineers.”
Nunn believes Australians are also starting to realise the superior comfort and air quality experience that Passivhaus offers compared to that of the past.
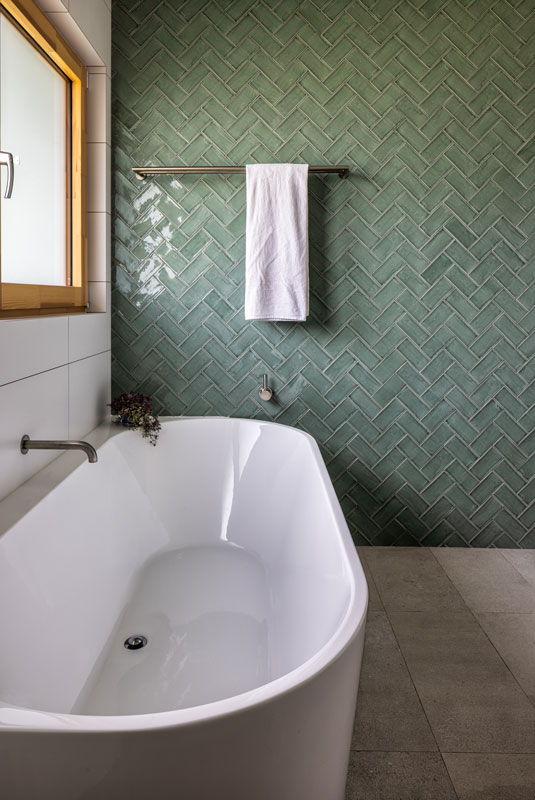
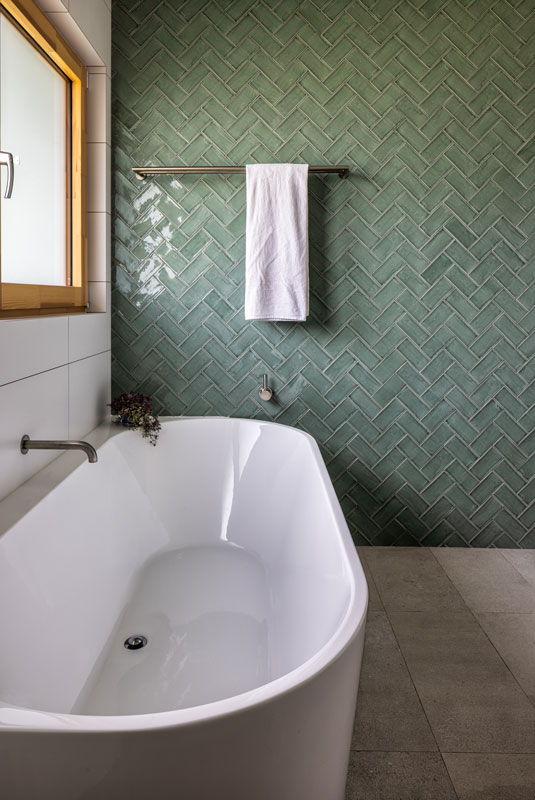
“Every person I’ve met who has lived in a cold climate like Germany or Canada comes to Sydney and says it’s the coldest they’ve ever been because of the poor quality of residential buildings,” Nunn says. “Anyone who’s visited Europe or North America understands this. They are simply building to a much higher standard – one that consistently delivers thermal comfort.”
He says that Australia’s temperate climate is both a blessing and a curse, and has resulted in acceptance of a low building standard that fails to deliver either comfortable or healthy buildings.
“Buildings built to the current and historical Australian building standards will overheat in summer and be cold in winter,” he says, “and they will be expensive to heat and cool.
“But there is a better way, and that is Passivhaus.”
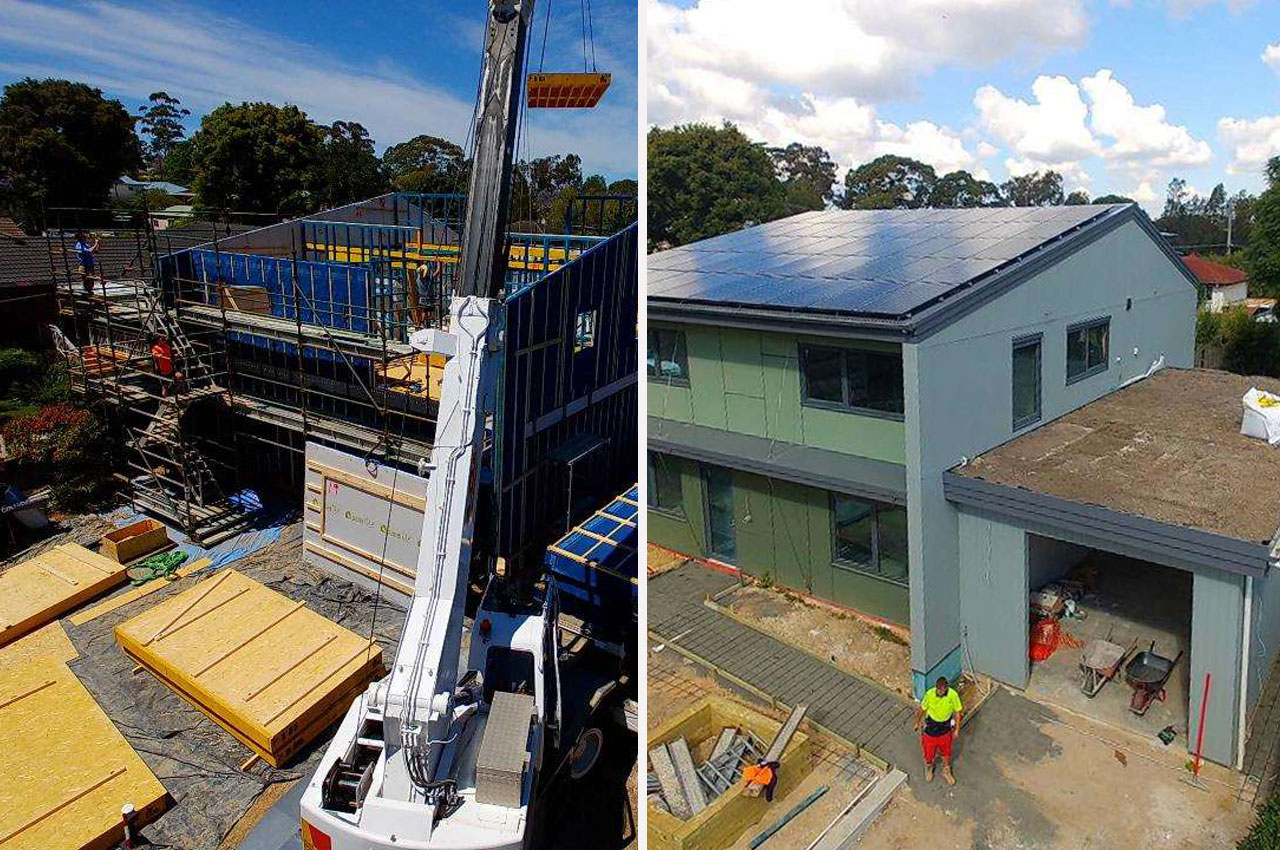
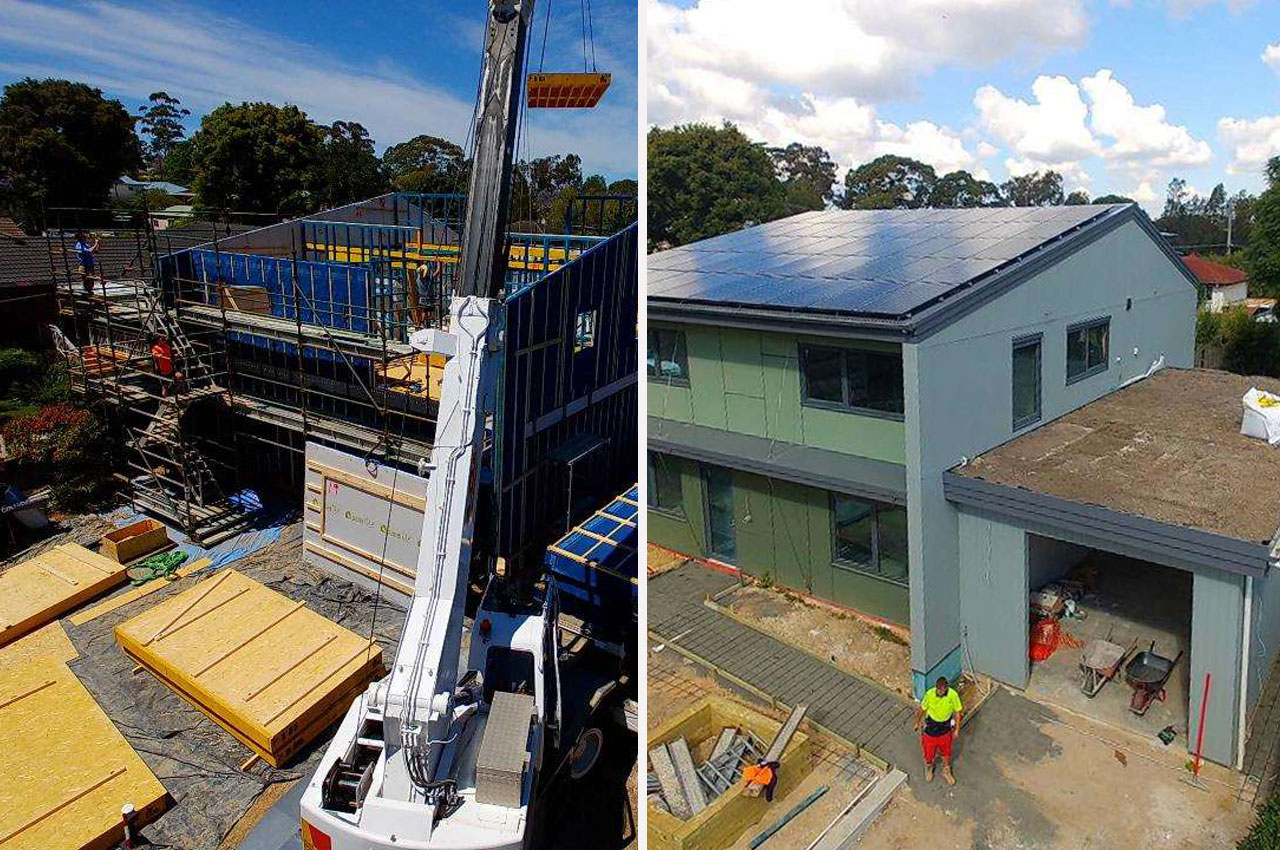
Lessons from the project
As owner and developer of his Asquith Passivhaus home, Chris Nunn offers several lessons to those considering a Passivhaus journey.
1. Order early. The lead time on windows from Europe was too long for our construction timeline so I actually bought the windows before the finance – and our DA – was approved, so that they would arrive on time.
2. Passivhaus works in Australian climates. It’s healthy and comfortable. And it’s future-proofed us against the predicted impacts of climate change.
3. If you are considering a new build, you really should seriously consider Passivhaus Certification – you won’t regret it. In fact, if you do, you’ll never want to live in anything that’s not Passivhaus certified. That’s certainly how I feel.
4. If you’re a designer or builder, take the course and learn about Passivhaus. Once you do, you will only want to do Passivhaus projects.
Why it’s a sustainable house
- PassivHaus certification
- Solar 20kWp
- Zero net energy and emissions
- Organic waste and compost; integrated bin joinery
- 400m to train, walk/ride to school and daycare
- EV charging
- Electric cargo bike
- Timber frame – FSC certified LVL
- Prefab cladding: recycled native wood fibre boards
- Food growing: bees, planter beds
- Rainwater tanks, greywater reuse, sustainable drainage
- Green roof
- Open days; promoting culture of sustainable living
- Local job creation and skills development
- Accessibility: Livable Housing Australia Silver
- Healthy and comfortable: constant temperature; indoor air quality; HEPA filter for bushfire smoke
- Active play areas for kids, interaction with nature.
Project at a glance
The personal
Architect: Envirotecture
Builder: Superior Constructions
Building services: Fantech
Client: Chris and Maylynn Nunn
Design review: Envirotecture
Energy rater: Envirotecture
Green Star consultant: Hip V. Hype
Mechanical contractor: Alpine Air
Passivhaus certifier: Grün Consulting
Passivhaus consultant: Envirotecture
The equipment
Air Vents: Fantech
Airtight membrane: ProClima Intello
Cladding: Weathertex
Fans: Aeratron and BigAss Haiku
Heat pump hot water: Sanden
MVHR unit: Fantech
Prefabricated walls: CarbonLite
Solar PV: Sydney Solar Electricity
Split system air conditioning: Mitsubishi Electric
Windows: LogikHaus
(Source: Chris Nunn + Envirotecture)
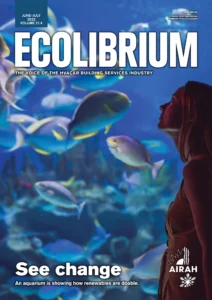
This article appears in Ecolibrium’s June-July 2022 edition
View the archive of previous editions
Latest edition
See everything from the latest edition of Ecolibrium, AIRAH’s official journal.