Together in electric schemes
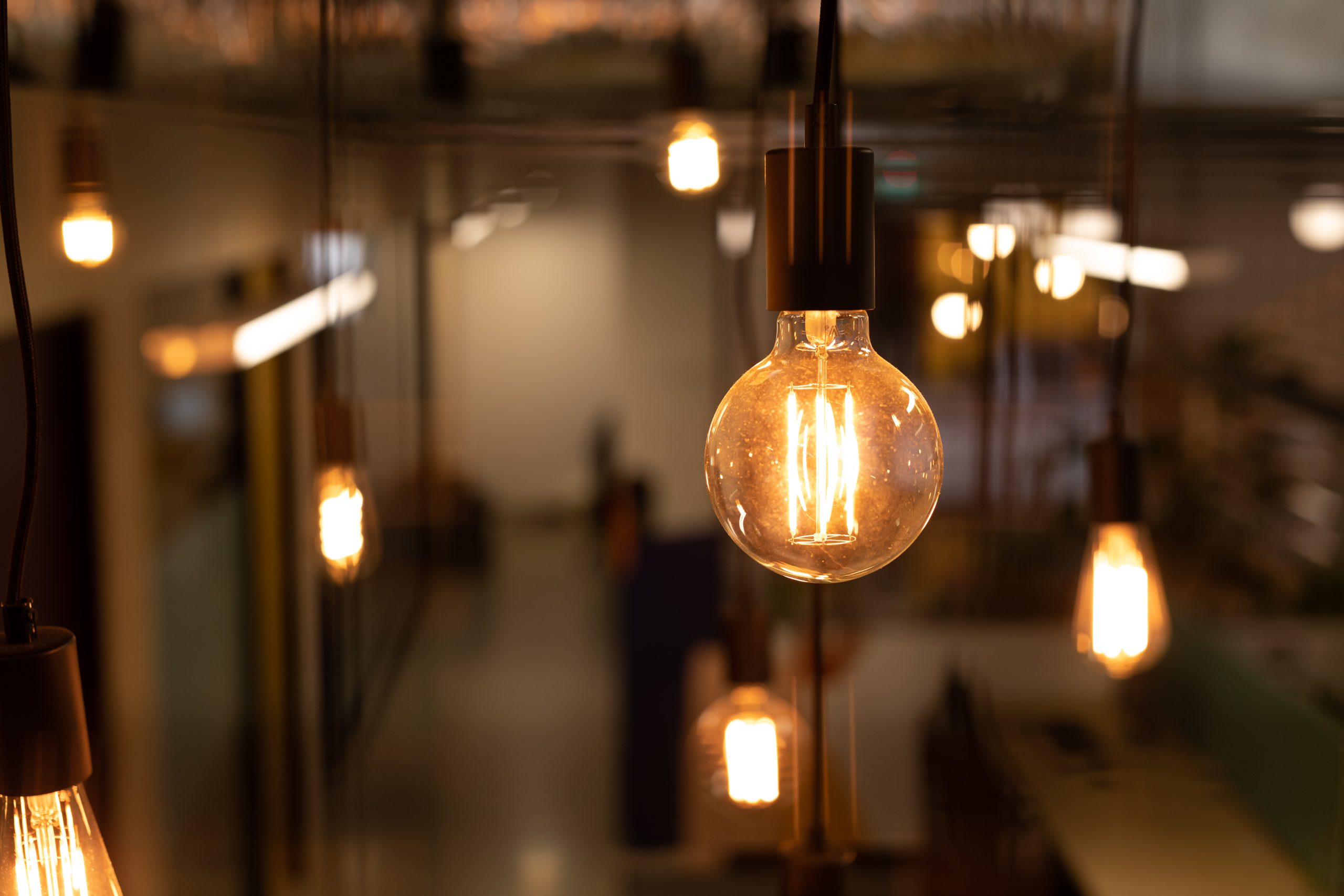
The Australian building industry is on the path to electrification, signalling an end to a reliance on natural gas for hot water, heating and cooking. Sean McGowan explores how this path is being forged with Bruce Precious M.AIRAH, principal consultant at Six Capitals Consulting; Yale Carden, M.AIRAH, founder and managing director at GeoExchange Australia; VA Sciences’ James Moyes and Simon Witts, M.AIRAH; and RMIT industry fellow Alan Pears.
Ecolibrium: Does the talk of degasification and subsequent electrification of commercial building stock match the appetite of building owners and managers in the market?
Carden: The “talk” will always come first – marketing leads and then (hopefully) operations eventually catch up. We are somewhere along this path and, promisingly, the curve appears to be getting steeper.
A key here is whether this electrification curve is seen as a trend or a transition. Most that we speak with are open to at least obtaining a better understanding of electrification and will explore options. However, due to the nature of what we do, I tend to think that we engage with the more progressive owners and managers.
“A key here is whether this electrification curve is seen as a trend or a transition.”
Moyes and Witts: At an individual manager level – mostly, at the corporate level – not often, but sometimes.
If we take the concept that a major driver for companies is to monitor their bottom lines, switching solely to electricity will cost more in the short term, which logically doesn’t fit with their financial reality and responsibility to investors.
Up until 2019, existing commercial buildings were fairly well tenanted. Once the pandemic hit, everyone went to work from home and realised it’s actually quite easy – and even nice. As restrictions began to ease, this left a lot of the surviving companies looking at their leases and wondering if they were still getting a deal and began to shop around. From this aspect, a lot of buildings owners needed to have a point of difference to get their buildings full of tenants again. Electrification is a huge talking point at the moment, and so was one option to attract tenants with environmental policies. This led to appetite to offer degasified buildings.
Besides this, unfortunately until legislation matures it is unlikely that there will be a big push to remove natural gas supplies from buildings – especially when the grid is struggling already and upgrades require further investment from developers.
Pears: Many investors such as super funds are looking for long-term, reliable returns and have substantial capital to invest, along with sophisticated financial analysis. In a context of climate change and volatile, increasingly costly gas, as well as pressure from fiduciary regulators such as APRA, and investor pressures, long-term climate impacts are taking higher priority. The National Electricity Market is expected to be 80 per cent renewable by 2030.
“The National Electricity Market is expected to be 80 per cent renewable by 2030.”
Building regulators are already moving in ACT, NSW and Victoria. The GBCA is pushing all-electric solutions in the commercial sector.
Precious: Electrification of homes and commercial buildings is well under way, with homeowners and commercial property owners taking steps to eliminate fossil fuel gas from buildings. Electric technology for space heating, hot water heating and cooking is available off the shelf right now, and many people and organisations are swinging their minds to constructing fully electric new buildings and converting existing buildings.
Mirvac, GPT and Lendlease are among the growing band of property companies that are phasing out fossil gas from new and existing buildings. Meanwhile, Green Star is encouraging market leaders to avoid gas in new buildings with technical guidance in the form of their electrification guides.
Cbus Property’s 435 Bourke St development, a $1 billion, 60,000m² office building and GPT’s 51 Flinders Lane, a 29,000m² office building, are both in Melbourne, and both planned to be all electric.
NABERS is planning to release a new Renewable Energy Indicator that will communicate sources of energy and highlight the contribution of fossil fuels. This feature will also allow tenants and investors to create new market demand, with requirements for buildings that have a high NABERS energy rating and a high renewable energy percentage. Electric buildings will be able to achieve 100 per cent renewable energy, while those with gas will only ever achieve a lower percentage.
Electrification isn’t something new or uncommon – more than half our homes and many of the commercial buildings across the nation aren’t connected to the gas grid.
“NABERS is planning to release a new Renewable Energy Indicator that will communicate sources of energy and highlight the contribution of fossil fuels.”
Ecolibrium: What are the key drivers of electrification? Aside from the rising cost of gas, what are the other influences?
Precious: The key driver to electrification is the response to climate change. It has taken time, but the realisation that emissions must be cut urgently not only to protect the environment but also to protect business reputation and the bottom line is fuelling a groundswell of change.
Renewable electricity, wind and solar PV are now the cheapest forms of new electricity generation, and with electricity perfectly suited to efficiently providing comfort around 22˚C, hot water to 50˚C and cooking a delicious steak, it has become the energy source of choice. Australian homeowners have been world leaders at installing solar panels and this clean, renewable energy can be used throughout the home and even to charge the family electric car.
Australian property businesses know that moving to net zero is a key talking point with investors and increasingly with tenants. Climate Active carbon neutral certifications are one of the fastest growing of the NABERS suite of certifications with over 60 buildings now certified and while Climate Active allows organisations to use carbon offsets; moving to 100 per cent renewable electricity avoids the costs of fossil gas and associated carbon offsets.
The International Energy Agency is very direct: “In buildings, bans on new fossil fuel boilers need to start being introduced globally in 2025, driving up sales of electric heat pumps.”
With these compelling reasons to move away from gas there is an urgent need for community leadership from government to guide this transition of the built environment. With fewer new buildings connecting to gas and a growing cohort of homeowners and businesses disconnecting from the urban gas grid, we could see an ugly spiral as the cost of aging gas grid upkeep is carried by fewer and fewer consumers.
Governments are starting to act. The ACT government is offering homeowners interest-free loans towards sustainable upgrades like hot water heat pumps or induction cooktops. The Victorian government has expanded the Victorian Energy Upgrades scheme with new incentives for switching to efficient electric appliances and phasing out incentives for fossil gas residential appliances by the end of 2023, as part of the Gas Substitution Roadmap.
The Committee for Sydney has recently called for a target of “no new gas connections from 2025 and no new gas appliances by 2030”, reflecting the growing urgency that many community members see is required to ensure an orderly transition of buildings away from the gas grid.
In summary, if you were to invest in a new gas appliance for a building today, or for a building in the planning stage today, there may not be grid-delivered gas available to power it before it reaches end of life.
Moyes and Witts: Climate change is the obvious answer here. Saul Griffith’s The Big Switch sets out a very clear and compelling path to achieving an electric future for Australia if we are to avoid irrevocable damage to Mother Nature. However, this is not without its issues.
Unfortunately, corporate Australia, which does include government sectors, has for a long time not been at the forefront of leading change. If it affects the bottom line, a lot of corporations won’t willingly embrace the idea, and so it must be legislation that drives things forward. Alternatively, if marketing appeal for sustainable design becomes a requirement, the bottom-line-driven corporations will have to respond.
It’s not all doom and gloom though. If you look at the last election, there was a much larger focus on environmental issues than we have seen in previous years. So, more and more, the world is becoming conscious of the environment, with its limited resources, and demanding more from those in power.
Pears: Hence the significance of the GBCA and NABERS. The recently announced NSW Sustainable Buildings SEPP states for commercial buildings they must “Demonstrate that the building can operate without fossil fuels by 2035 (for state significant and large commercial builds).
“The key driver to electrification is the response to climate change. It has taken time, but the realisation that emissions must be cut urgently not only to protect the environment but also to protect business reputation and the bottom line is fuelling a groundswell of change.”
In short, some states and territories are way ahead of the national government.
Carden: Our experience is that the rising cost of gas has been the main driver so far. In some instances, a tripling of cost has occurred in the past few months. State and territory gas phase-out policies (e.g., ACT and Victoria) provide useful support but sometimes the longer time horizons are beyond planning considerations and fall into the category of being a future problem for someone else.
The issues of high emissions from methane leakage and human health implications from particulates are gradually gaining traction and will no doubt contribute more to the transition as awareness increases. Greater awareness and possibly stronger policy responses are required. Some incredibly progressive gas phase-out policies are being implemented around the world at the moment, many in the next few years.
Pears: It’s worth noting that the mandatory Commercial Building Disclosure scheme will put pressure on high-emission buildings
“Renewable electricity, wind and solar PV are now the cheapest forms of new electricity generation.”
Ecolibrium: From a life-cycle and capex perspective, does the degasification/electrification of mechanical plant make more sense when existing plant has reached end of life rather than as a proactive retrofit? Is the business case clear-cut?
Carden: “It depends” is my stock standard response on this one (and many others!). An admittedly frustrating response that is particularly the case for retrofits. A perfect one-stop solution that fits all scenarios doesn’t exist, and a change in such thinking will be a big part of whether the electrification transition succeeds.
Non-engineering factors or distribution systems as they relate to the physical build itself may be just as influential in a retrofit as the selection of mechanical plant.
Further, how the client defines their business case and the financial tools available to them can be equally as important as the engineering solution. For degasification/electrification (in fact the complete energy transition) to succeed we need new progressive financial engineering tools and a rethink of the traditional business case as much as we need energy or heat pump engineering.
Pears: We also need building rating tools to be more focused on lowering peak energy demand, especially in winter, when output from variable renewables can be lower. Evening and overnight energy use will also become more of an issue, as electricity demand tends to peak in evenings and variable RE is lower at night. A problem with NABERS and NCC is that they focus on annual energy/GHGs. For commercial buildings this can lead to lower building envelope thermal performance in moderate climates due to the often beneficial heat leakage reducing cooling energy requirements of buildings with high internal heat generation and low ratio of external envelope to floor area while increasing winter heating and peak cooling energy demand.
Lower-cost options for retrofitting (eg see this low cost glazing retrofit – 10–25% of cost of replacing windows and effectively low-e triple glazing https://betterbuildingssolutioncenter.energy.gov/sites/default/files/2022Summit-Pushing_the_Envelope-slides.pdf
Precious: The business case for each electrification decision will be unique with different end use requirements, space, and installation conditions for every project. There will be cases right now where there is a benefit to switching a gas system across to electric – in this case there’s no reason to delay gaining the benefit. Especially if you have onsite solar, switching across to electric systems is likely to provide immediate savings so you’re better off the sooner you switch.
In other cases, yes, switching at end of life keeps costs to a minimum. What’s important in this discussion is planning. Don’t wait until the gas appliance fails to try and work out your best electric equivalent, plan ahead, redesign the system now to be best prepared and don’t get cornered into a like-for-like replacement you’ll regret.
Overlaying these considerations is the imperative to continue driving energy efficiency improvements. Upgrading insulation and eliminating draughts from buildings means the heating system needs to do less work. Gas for space heating has been used as something of a blunt instrument so reducing the heating demand means less capex spent on replacement equipment and lower running costs for all its life. Same for hot water systems, reducing loads and diversifying hot water supply can lead to overall system savings.
Pears: And there is rapid innovation in EU and the US driven by the gas crisis. Large heat pumps are being designed for district and precinct heating, reverse-cycle HPs will be able to replace existing chillers and gas boilers. Some more modular equipment may be progressively added to reduce gas use and enhance resilience by reducing reliance on central plant.
Moyes & Witts: If it is legislated, then the cost-benefit argument evaporates, and the case is clear cut. If there is no legislation, then evaporation is instead the fate of our seas with the subsequent storms and floods only then hitting the bottom line of corporate Australia.
Of course, timing is everything. There is no point ripping out brand new, efficient machines and replacing them just because they use gas. When they are due for renewal, it is then when we consider the options – don’t just replace like-for-like. Hopefully in that time the Australian power grid will have caught up and isn’t burning brown coal to produce power.
Pears: As noted above, regulation is just one aspect of what is happening voluntary programs and rapid innovation too. As noted there is scope to use modular equipment to partially replace gas equipment, and hybrid heat pumps that use gas (or stored heat) pre-heating to cope with winter peaks exist. And building upgrades and more focus on winter peak load reduction ect all play parts. Also, improving efficiency of electric appliances, lighting, equipment frees up electricity supply capacity while battery storage can maintain resilience, reduce need to upgrade local electricity network capacity and generate revenue through demand response.
“For a building in the planning stage today, there may not be grid–delivered gas available to power it before it reaches end of life.”
Ecolibrium: Domestic hot water (DHW) plant is the obvious target for electrification given the availability of heat pump alternatives, but what are the challenges associated with this? Not all buildings offer the same opportunities, do they?
Moyes & Witts: Every site is going to be different, particularly when climate zones are different. Generally however, power supply and space are the two largest challenges. There is significantly more power required for a heat pump system that more than likely was not allowed for during the original design. In the southern states, like Victoria, where heating demand occurs in winter when there is not a lot of cooling demand, then there may be very little impact to the incoming supply capacity. This is less likely to be the case as you encroach further north.
Now, it may be the case that there is spare capacity overall, but where is this coming from? The main switchboard is likely not near the DHW plant, so there is a long and reasonably large cable run required that may even necessitate a shutdown to areas of the building given the size of supply emanating from the main switchboard.
Spatial provision is the next big issue. Is there space for the increased plant size? Is this space in a suitable location for a heat pump to reject/absorb heat? If an electrical supply upgrade is required, is there space for this? If not, where do you sacrifice the space from? It certainly wouldn’t be net lettable area, so you can bet that maintenance just got a whole lot harder!
Pears: Space and supply capacity are certainly issues – but an integrated approach can help, as noted above. An HPHWS – heat pump hot water system – with battery and/or thermal storage (and using waste heat if available) can reduce peak loads.
Carden: Again “it depends” on which solution may be most suited to any given building, and some may not at all. Opportunity may be about willingness to consider alternatives as much as the alternative itself. And incremental transition for different parts of a building by targeting wasteful or high peak demand parts.
It is important to note that heat pumps of today (and tomorrow) are not necessarily the clumsy, noisy, inefficient boxes of the past decade or two. Technologies evolve and we need to evolve with them.
The main limitation with replacing a gas boiler with a heat pump is space. Heat pumps have a larger footprint per kW and require thermal storage. Further, air source heat pumps require an outdoor location or ventilated space (much like gas boilers), whereas ground/water source heat pumps do not.
The best solutions will occur when we integrate at the building scale and not just limit consideration of solutions to the “boiler versus heat pump” binary comparison. This includes non-heat pump options such as solar DHW and an electric element can be a useful solution if powered by renewable energy.
Pears: Not always – in southern areas winter solar thermal HW performance may not be great, which can lead to high reliance on electric boosting at times when loads from other areas are high.
Precious: DHW is an exciting option for electrification because of the availability of heat pumps that satisfy hot water requirements.
Even better, coupling a heat pump with a hot water tank to create super-efficient energy storage, making use of cheap solar energy during the day and storing the hot water for use throughout the day and night, allows for energy to be used when it’s plentiful and contributes to a flatter grid demand profile.
“More and more, the world is becoming conscious of the environment, with its limited resources, and demanding more from those in power.”
Ecolibrium: Is electric technology ready to replace gas-fired heating hot water (HHW) plant, and what are the options?
Carden: In most instances, yes. (Although keeping the “it depends” response as an option!)
Heat pumps are readily reversible, and combining heating and cooling into an integrated system provides system efficiencies through thermal sharing whether simultaneously or at varying times through thermal storage Once we head down the electric technology/heat pump path, our main considerations are selecting the source of thermal energy as well as how that thermal energy is delivered to the application/building (air, water or refrigerant).
The source of thermal energy for heat pumps, providing properly designed of course, tends to be renewable. Although ambient air is the most common, options include the ground, water bodies (ground and surface), building foundations (energy piles), infrastructure such as sewer and irrigation water and even other buildings. A system doesn’t even have to limit itself to just one of these. There can be efficiency, redundancy, resilience and cost- saving measures in integrating two or more sources of renewable thermal energy. Exhaust air from the building can be useful.
Pears: There are several efficient models on the market, and I expect more reversible and heat/cool products to emerge – they are already widespread in residential and smaller commercial settings.
Precious: The technology is ready. Heat pumps are used to provide effective, clean space heating around the world as well as in lots of our buildings and homes, but in some applications, especially retrofits, it is right to be cautious. Sometimes heat pumps won’t be a simple one-for-one replacement – some of our practices, our behaviours, in designing and applying heat pumps will need to change.
Larger commercial buildings, especially those designed with heating hot water plant, will provide some challenges. A 400kW heat pump probably doesn’t just slide into the same spot the 400kW boiler is in – it’s going to take some design innovation from our engineers. Understanding and minimising the real heating demand is critical. Anecdotally, gas systems are often overdesigned, rarely run to capacity, and gas metering with accurate time of use data is unavailable, making replacement equipment selection difficult.
There’s a good case for installing well-calibrated meters on critical heating equipment now so you know what service is provided and what drives it. Not only can this information lead to plugging any thermal leaks you have in the building you’ll have information to right-size a heat pump alternative.
Where heating coils have traditionally been designed with 80˚C entering HW temperature, this will challenge the heat pump design, but even then, hybrid systems of cascading heat pumps or heat pumps with supplementary resistance heating might prove a suitable alternative. There are a lot of options to be explored that will only be enhanced as research into ever better heat system technologies continues around the world.
Contrasting these difficult retrofit cases will be those cases where a ready source of waste heat makes heat pump installation easy and super-efficient. Scavenging process heat or geothermal energy leads to high efficiency and long-term savings. Efficiency improves significantly if the temperature lift can be reduced.
Pears: Combining a building upgrade with conversion to a HP can reduce loads so lower temps can be used, and variable temperature and flow when thermal loads are lower can allow a HP to vary output and minimise temperature lift in real time if the HP is designed to operate efficiently over a suitable range of output. For example, residential inverter-controlled HPs can operate at higher efficiency at part-load.
Moyes and Witts: The technology we’re talking about is not new – it has been used successfully for many years. The only thing that is changing is the efficiency, and this is only improving. In fact, as efficiency improves, we start to solve some of the spatial implications touched on in previous questions.
Technology isn’t the problem – attitude is.
Pears: But attitudes are shifting rapidly, as is the technology, and the smart installation and management is following suit.
“For degasification/electrification … to succeed we need new progressive financial engineering tools and a rethink of the traditional business case.”
Ecolibrium: What are the wider implications of electrification in the commercial building space, such as electricity supply to site and the like?
Carden: Degasification or electrification is about supply and demand so both sides need to be working together.
Thermal demand can play a large role in the success of the broader energy transition to 100 per cent renewables so we need to avoid the heat pumps will ruin the grid commentary. Heat pumps powered by renewable electrical energy that source from renewable thermal energy, have grid communicating control systems and supplemented by thermal storage, are at the centrepiece of this and some of the most exciting future areas of our industry.
In existing areas or existing buildings, assuming that peak cooling has determined grid supply and the grid has been well managed, the relatively smaller peak heating loads are not such an issue on electrical infrastructure. A new build or significant building expansion will depend on what is already present and the state of the grid itself.
For example, we have some current projects where the inclusion of higher efficiency (peak and annual) ground-source heat pumps rather than air-source heat pumps has avoided the need for costly grid connection upgrades. That is without any onsite solar PV. These avoided grid upgrade costs are effectively paying for the installation of the ground heat exchanger (thermal storage).
Moyes and Witts: There are absolutely downstream considerations beyond the plant itself that relies on gas but put simply, the load isn’t changing – there is a demand that is currently being met by gas.
Typically, this is heating and domestic hot water, but can be other areas such as sterilisation in processing and healthcare facilities, and commercial kitchens. Removing this fuel source means it needs to be replaced, and that requires an equivalent amount of energy in some form or another. In this case, electricity. Thankfully we’re not just relying on running a lot of electrons through metal anymore to produce a lot of heat, so the system demand isn’t a direct conversion of kW (heat) to kW (electricity). A shockingly low amount of existing commercial buildings have any form of onsite generation (think less than 1 per cent!). That means most commercial buildings rely on the grid for all their energy.
From our calculations on Grade 1 hospitals, removing gas entirely resulted in around a 30 per cent increase to the estimated maximum demand. However, if we consider the usage characteristics, the peak demand change for commercial buildings is a lot less. Commercial buildings (mostly) have a peak electrical demand in summer when cooling is prevalent. The gas that is being removed would largely be heating in winter (obviously, this is less relevant in northern states) and so the electrical demand in winter would rise, but be unlikely to exceed the summer peak. This is because internal gains during winter help reduce the heating demand, whereas in summer they increase the cooling demand.
As for domestic hot water, the load is quite low within commercial buildings – especially those without end-of-trip facilities. For the buildings that do have these facilities, the demand is early in the morning, and so could be scheduled to pre-heat the storage units prior to the chillers ramping up. Café tenancies with small gas supplies would lead to a slight increase in electrical demand, but minimal in the context of a large office building.
So, what does this mean? Well, if the design and implementation is properly engineered, the increase to peak load is actually minimal if any. So incoming supply/substation upgrades (the largest cost from an electrical perspective) can be avoided in most cases.
Turning the lens inside the building, and the picture is a little different. It would be a stroke of luck if no upgrades were required to any of the main switchboard, submains or switchgear. Obviously, this does carry a cost and potential to cause interruption to supply. This isn’t the end of the world for a commercial building though. With enough forward planning, a weekend changeover is bread and butter for a decent electrical contractor and the power companies.
Pears: Arguing that there is a demand that is currently being met by gas is a flawed position. End-use efficiency measures of many kinds and demand management/storage can transform the underlying thermal demand and the efficiency of the HP.
On the point that removing gas as a fuel source means it needs to be replaced, and that this requires an equivalent amount of energy in some form or another, I disagree. Many central systems are very inefficient, and stand-by losses can be high for intermittently used equipment.
Precious: At the grid scale the Australian Energy Market Operator (AEMO) is charged with planning how the system will respond to the new, decentralised, renewable electricity generation systems as well as catering for new demands such as electric vehicles and the electrification of buildings. Their most recent Integrated System Plan includes a scenario called “step change”, which, according to the consultation they have with energy experts, is the most likely of scenarios.
Step change will see 82 per cent of electricity in 2030 supplied by renewables, a target recently adopted by the federal government. It’s an extraordinary transformation, from the 32 per cent now to 82 per cent in just eight years. Some have described this as the fastest decarbonisation of any large-scale grid in the world. This projection also resolves any concern that switching from gas to electricity is going to increase emissions. Right now, there are periods (hours, days) where the grid is heavily reliant on fossil fuel generation, but in the very immediate future this won’t be the case.
The step-change scenario analysed by AEMO also factors in a lot of electrification, expecting gas use in homes to be cut by 85 per cent by 2040. These plans will guide investment in the electricity network.
No doubt there’s work ahead on all fronts to avoid overloading generation, transmission and distribution capacities, and one of the best ways to do that is still through energy efficiency. Improving the passive thermal performance of all buildings avoids unnecessary investment in oversized systems and avoids paying oversized energy bills.
The electricity infrastructure will require careful management to accommodate the electrification of buildings and transport. But just as importantly the gas grid is going to require very careful management, and probably some government guidance, as customers leave it.
Managing the rolling back of the gas grid from urban areas while retaining pipelines connected to industrial nodes and other points where the transition takes longer will be critical.
Pears: Transgrid in 2021 did a study of overall electricity costs of various scenarios, though that would not consider behind-meter wiring, etc
“Improving the passive thermal performance of all buildings avoids unnecessary investment in oversized systems and avoids paying oversized energy bills.”
Ecolibrium: In northern states, all-electric seems to have already taken hold in new builds but what about southern states like Victoria where heating demand is greater?
Carden: Is Victoria really that cold when some of the largest heat pump markets are in northern Europe? We already do heat pumps really well – we just call it air conditioning. Unlike the US, most (all?) of our AC units are reversible, so heating is already a feature.
However, the question is also about new builds and the solution is as much about build quality as it is with electrification, perhaps more so. This doesn’t mean Passivhaus for everyone. Our buildings, in what are relatively mild climates, could be so much better. Get the building right and the passive thermal systems will do most of the comfort work for you. Mechanical thermal systems, including ventilation and heat pumps, are then just there to be complementary rather than a matter of survival.
Pears: My impression is that commercial building envelopes at present are not designed to minimise winter heating – annual and summer issues seem to dominate.
Moyes & Witts: There are some wonderful reasons to live in Victoria, but warm climate isn’t one of them. We can still achieve all-electric buildings in Victoria – the grid has some catching up to do in terms of emissions but that doesn’t mean we shouldn’t be trying. The technology exists and it is only going to get better.
With that said, there are many examples of new builds in Victoria where all electric is being pursued and implemented including new hospitals currently in feasibility, design and construction and a host of other new commercial buildings. The appetite is there, and design is happening. Victoria is not falling behind the rest of Australia in any way – it just has some additional issues to deal with.
It is the existing building stock that is the tricky area, especially those which are currently in use. It’s the people in the industry, like our readers and colleagues and everyone else with an interest that need to work together, keep pushing the agenda to inform influential clients and decision makers and assist in solving the climate crisis we’re facing together.
Pears: And close liaison with building designers will be critically important for minimising electrification costs and optimising overall performance. Retrofits will need to place much more emphasis on building envelopes and appliances/equipment.
Precious: Leading property developers and owners are already developing new buildings that avoid gas connections. Green Star has been leading the way on electrification since 2020. Projects registering from that date and aiming for a 6 star Green Star Buildings rating have had to be fossil-fuel-free, highly efficient (20 per cent more efficient than NCC 2019) and powered by renewables.
From January 1, 2023, those requirements apply to projects wanting a 5 star Green Star building rating, and from 2026 the requirement ratchet down further to include 4 star Green Star buildings. Fossil-fuel free means no fossil fuel use in heating, hot water, general power or cooking.
There are several Victorian new-build examples of all-electric detailed earlier. Others include Fraser’s Burwood Brickworks shopping centre that is fully electric right down to the cooking in retail tenancies, and Mirvac’s The Fabric residential developments in Altona North.
In the ACT, where winter conditions can be harsh, the government is planning new regulations to be introduced in 2023 that will prevent new connections of buildings to the gas grid while expecting homeowners to make transition plans during 2023–2024 to move away from fossil gas. The last fossil gas consumers should have fully transitioned by 2040–2045.
Supporting these regulations, the ACT government moved into new, all-electric government offices in 2020. Also in 2020, the ACT government announced that the new additions to Canberra Hospital would be fully electric. It’s important to note that the ACT government has contracts in place to ensure that renewable electricity is purchased for all electricity consumers in the territory.
In many parts of Europe, where winter conditions can be much harsher than Victoria’s, there are similar moves to electrification, with dependence on Russian gas a contributing incentive. Austria recently introduced a ban on new gas boilers from 2023.
New York City has joined the move away from gas, banning new connections for buildings seven stories and lower from 2023 with taller buildings having a further four years to comply.
The move to net zero emissions is a global one – scientists tell us it’s urgent, and it means that fossil gas has a rapidly declining role to play in the built environment.
“We already do heat pumps really well – we just call it air conditioning.”
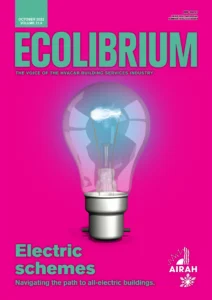
This article appears in Ecolibrium’s October 2022 edition
View the archive of previous editions
Latest edition
See everything from the latest edition of Ecolibrium, AIRAH’s official journal.