Wooden performance
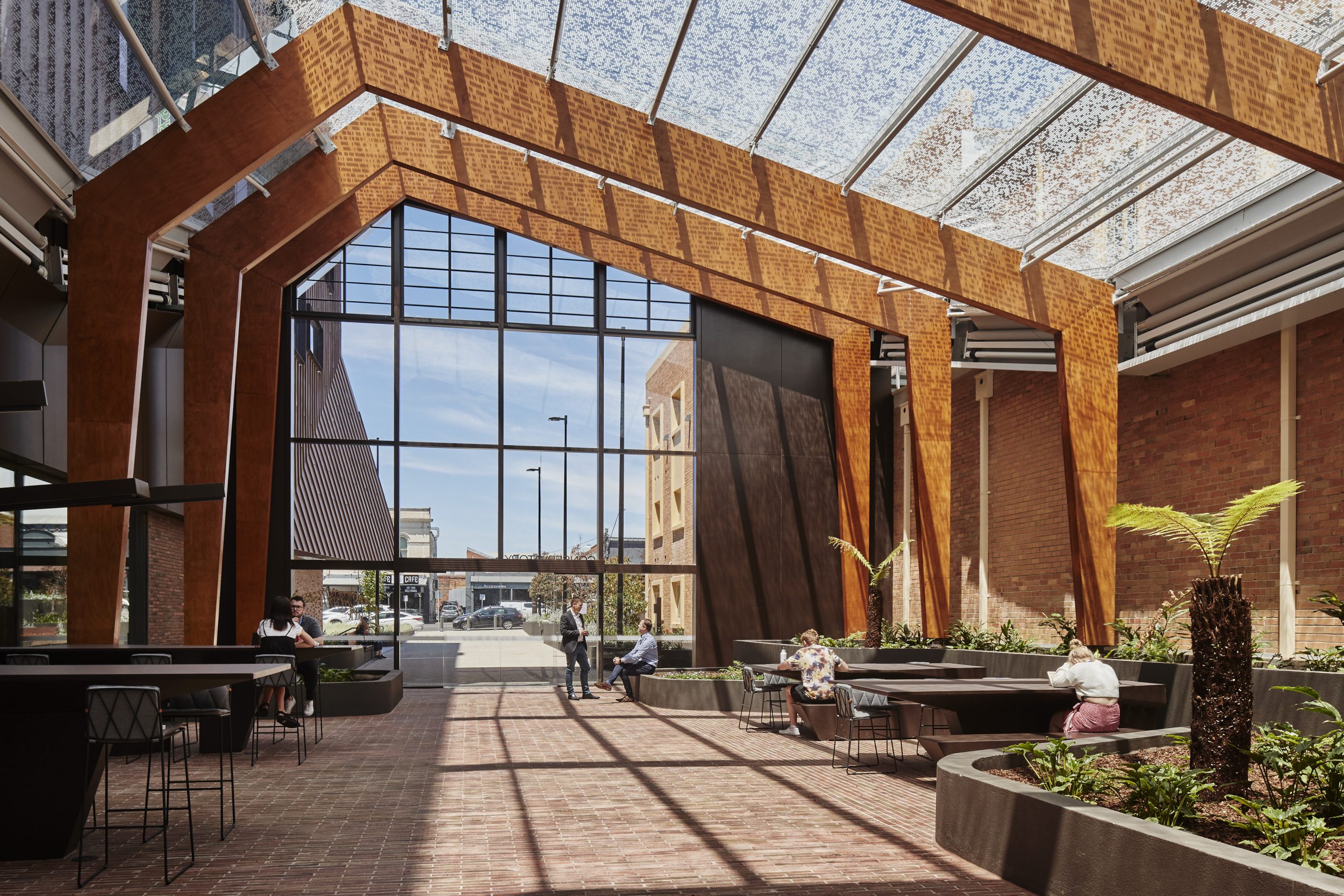
One of three similar facilities to be built in regional Victoria, the Ballarat GovHub is helping to revitalise the CBD of this regional centre and centralise government services in the area by accommodating up to 1,000 workers. Mass timber is at the heart of the building’s superstructure.
In 2017, the Victorian government announced the development of a new government office in regional centre Ballarat as part of Development Victoria’s GovHub program.
Following the establishment of a design competition, John Wardle Architects was selected as the lead designers for the $100m Ballarat GovHub project, with design of the building taking place during 2017 and 2018.
To be located on the eastern portion of the city’s iconic Civic Hall site, the brief called for a new, high-quality office building. The edifice needed to accommodate 1,000 workers, allowing for existing government offices to relocate and consolidate services in the one facility.
The narrow site dictated a long, thin building with a width of 24m and the ability to achieve 12m of natural daylight on either side of the floor plates.
“A 1,000-person office building requires a large spatial allocation,” says Luke Jarvis, principal at John Wardle Architects. “So, to minimise the overall height of the building the footprint was laid out along the length of the site.”
A number of key sustainability objectives were called for including 5 star Green Star base building and fitout, 4.5 star NABERS Energy and 4 star NABERS Water ratings – as well as the requirement for a high local content in both materials and labour.
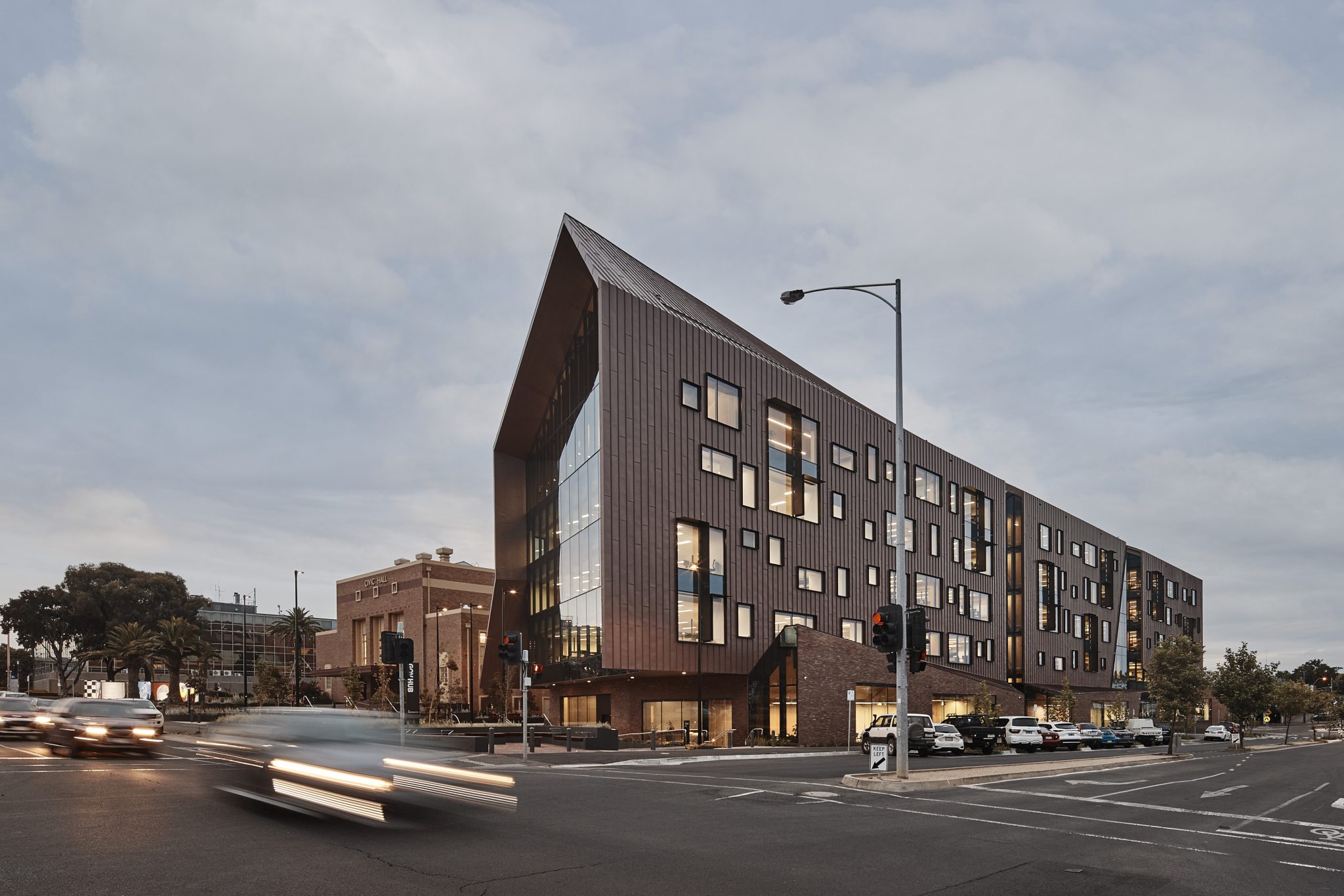
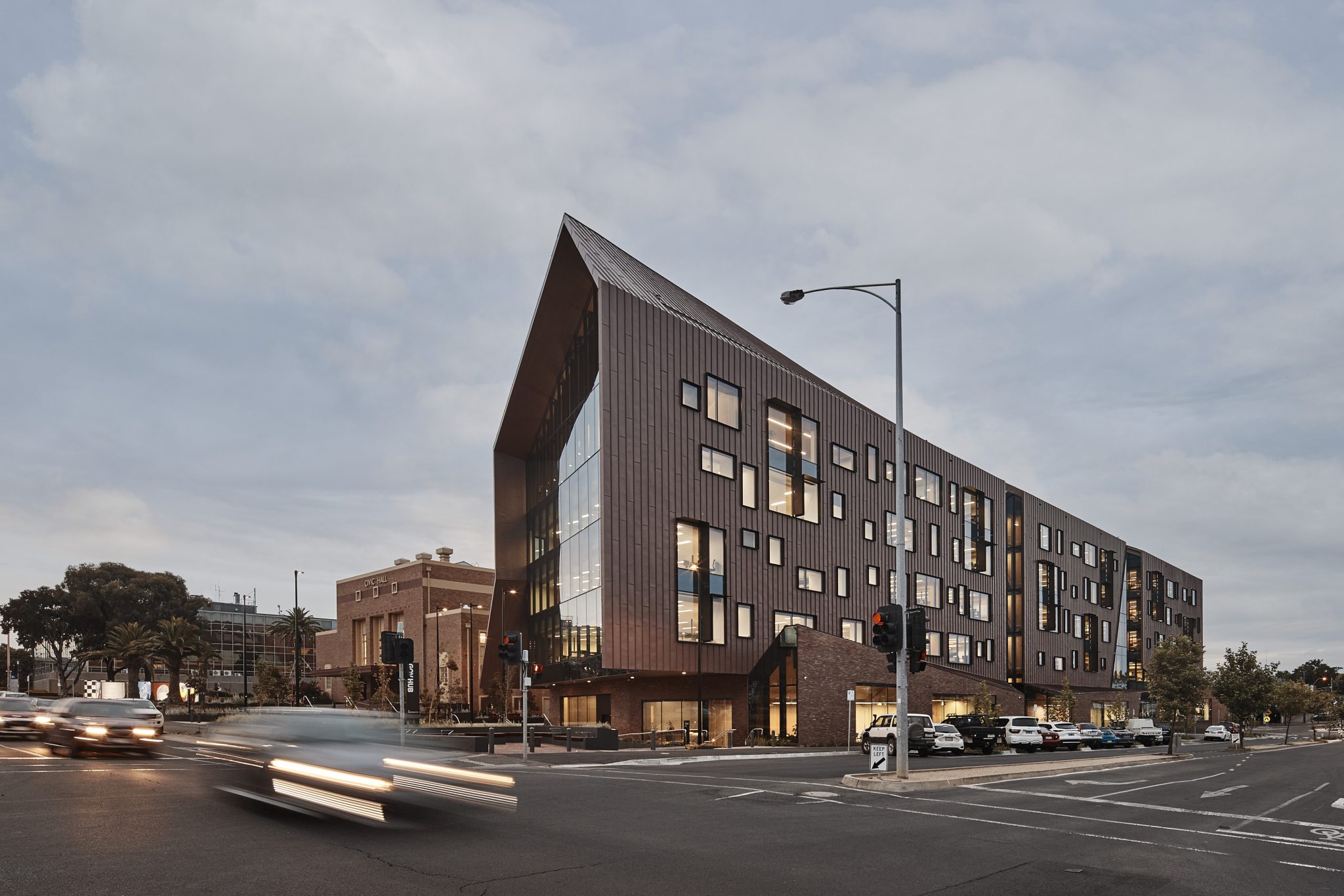
The word on wood
One of the unique elements proposed during design was the use of mass timber for the superstructure – a combination of CLT (cross-laminated timber) and GLT (glue- laminated timber).
At the time the building was to be constructed, it was the largest timber frame structure in Victoria, and the third-largest commercial timber frame in Australia.
“We like timber, as it has several advantages over other building materials that combine to make it a markedly more sustainable building material,” says Jarvis. “And a timber structure also has the advantage of a highly aesthetic finished form where the structure itself is also the finish within an integrated fitout.”
Jarvis also points to studies that have shown being surrounded by wood has a positive effect on occupant health and wellbeing.
In addition to the sustainability benefits, a number of constructability advantages were able to be realised from the timber superstructure. These included a significant level of offsite fabrication and a reduction of on-site waste, the speed of construction to improve the overall project program, reduced footing requirements, and a cleaner, quieter construction site reducing impact on the neighbouring properties.
Another key sustainable design principal embraced by the architect was the reduction of glazing to the external building envelope.
Jarvis says the extent of glazing on a façade has a significant impact on the mechanical requirements to heat and cool the building. From the outset of the design, a reduction in the window-to-wall ratio was targeted to reduce the energy demands of the building.
“The windows were carefully arranged to curate significant views, while still providing a high level of natural daylight to the workspaces,” he says. “A scattered window pattern acts like a viewfinder from within, providing occupants with glimpses of many city landmarks and the landscape beyond.”
By reducing the amount of glazing in the design, a more intimate, domestic scale within the office space was able to be achieved.
Jarvis says this was further enforced by the reduced span widths required from the timber structure.
External sun-shading devices contribute to the high-performing building envelope.
“We like timber, as it has several advantages over other building materials that combine to make it a markedly more sustainable building material”
Civic sensitivity
The architectural design of the Ballarat GovHub is sensitive to its context, recognising the important cultural and community significance of the existing 1950s-built Civic Hall and Library on the site.
“The masterplan for the precinct is centred around the Civic Hall – a building strongly characterised by the use of brick and masonry, which is particularly evident at ground level where the texture of brickwork imbues the building with a sense of being hand-built,” says Jarvis.
Consequently, the architectural design of the GovHub incorporates brick as the paving material at ground level. This is also drawn up and wrapped around a series of enclosures that extend around the building’s perimeter.
Considered as a place for both workers and the community to gather and meet, open plazas, a laneway and wintergarden provide outdoor and indoor public zones. And in the tradition of Ballarat’s famed botanic gardens, the glazed infill building called The Conservatory acts as an arrival and orientation space.
Taking reference from the region’s agricultural activity, the gable-roofed form of the GovHub building appears similar in shape to a rural shed. It features an outer skin of bronze zinc, appearing to completely wrap all five storeys.
“A gabled roof has the practical purpose of concealing the mechanical roof plant,” says Jarvis. “It also alludes to a different type of office building – one that is more domestic in its configuration reflecting the changing nature of work.”
Internally, the layout is organised into “neighbourhoods”, with each defined by primary timber columns and beams. Two lift cores provide independent address points for flexibility, while interconnecting stairs offer occupants with a choice of routes between each level, and promote a team environment.
Working around timber
According to D&E Air Conditioning design manager Peter Hatty, M.AIRAH, working within a timber frame building creates tight spatial conditions, and typically restricts reticulation in one direction.
Consequently, he says a decision was made early on in the project to run with concealed ceiling services.
“This worked well with the structural primary beam and secondary joist timber design,” Hatty says. “And it also certainly assisted in both the services design and coordination as well as acoustic performance of the floors.”
The timber construction also brought with it new learning opportunities for the D&E Air Conditioning team.
“Be it the type and length of screw fixings to meet the fire properties, to thermostat installation and placement in open-plan areas, to structural design requirements for penetrations – the project put us all on a new learning curve,” he says. “Research and discussion of these details with the design team, prior to beginning the site installation, was essential.”
Early engagement
AECOM was engaged on the project from late 2017, when the tender process was initiated by Development Victoria. The early engagement allowed for engineering input during the concept design phase.
“What was clear from the design competition was that the proposed building was to have a lot of engineering elements exposed, from the timber structure to the services,” says Henry Yuen, principal mechanical engineer at AECOM.
“Having exposed services meant very close coordination with the architect to ensure the aesthetic vision was not compromised.”
AECOM’s mechanical services design was taken to a detailed design level in order for the main contractor, Kane Nicholson Joint Venture (KNJV), to be engaged.
“The main challenge anticipated from the outset was coordinating the service design with the engineered timber structural design,” says Yuen.
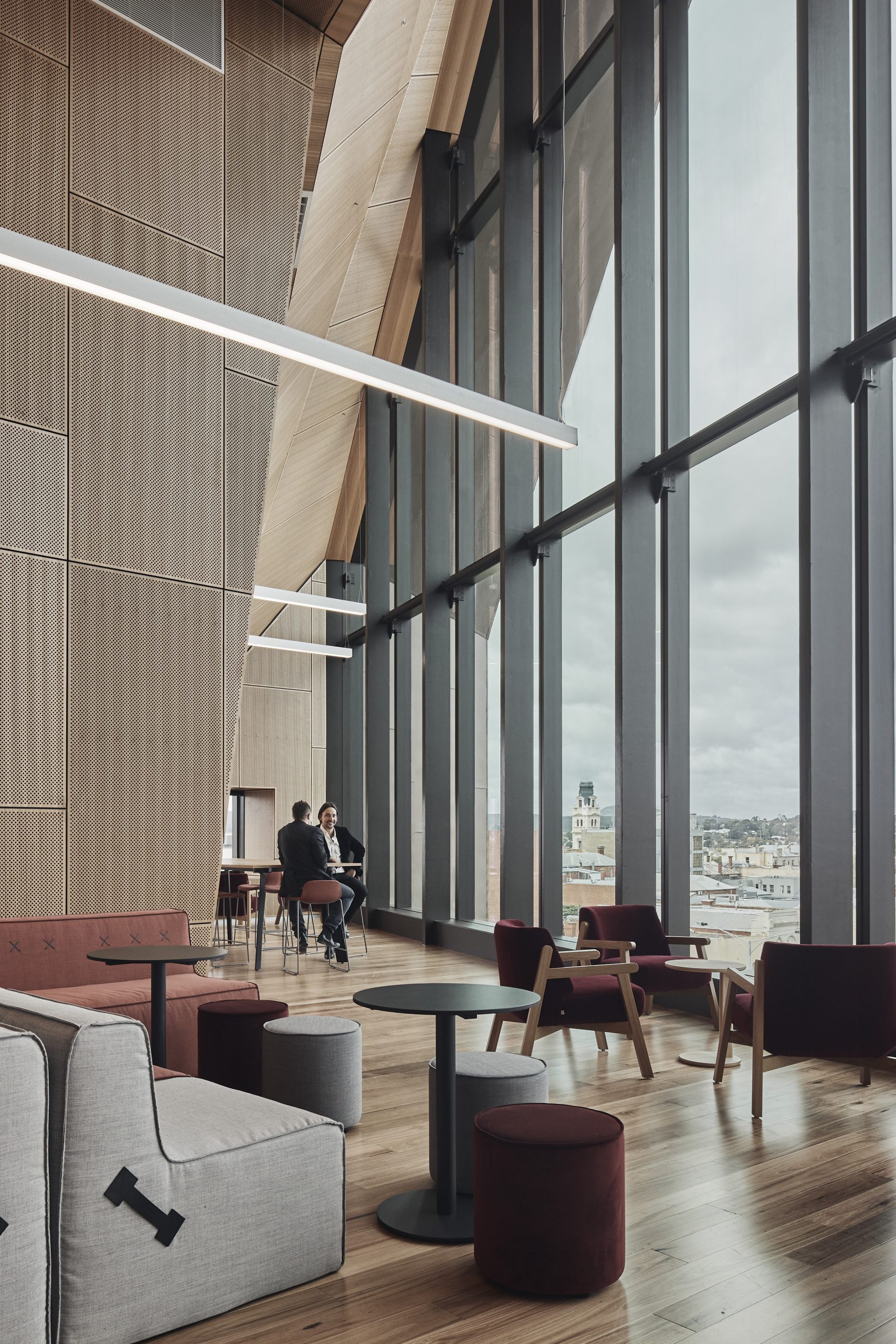
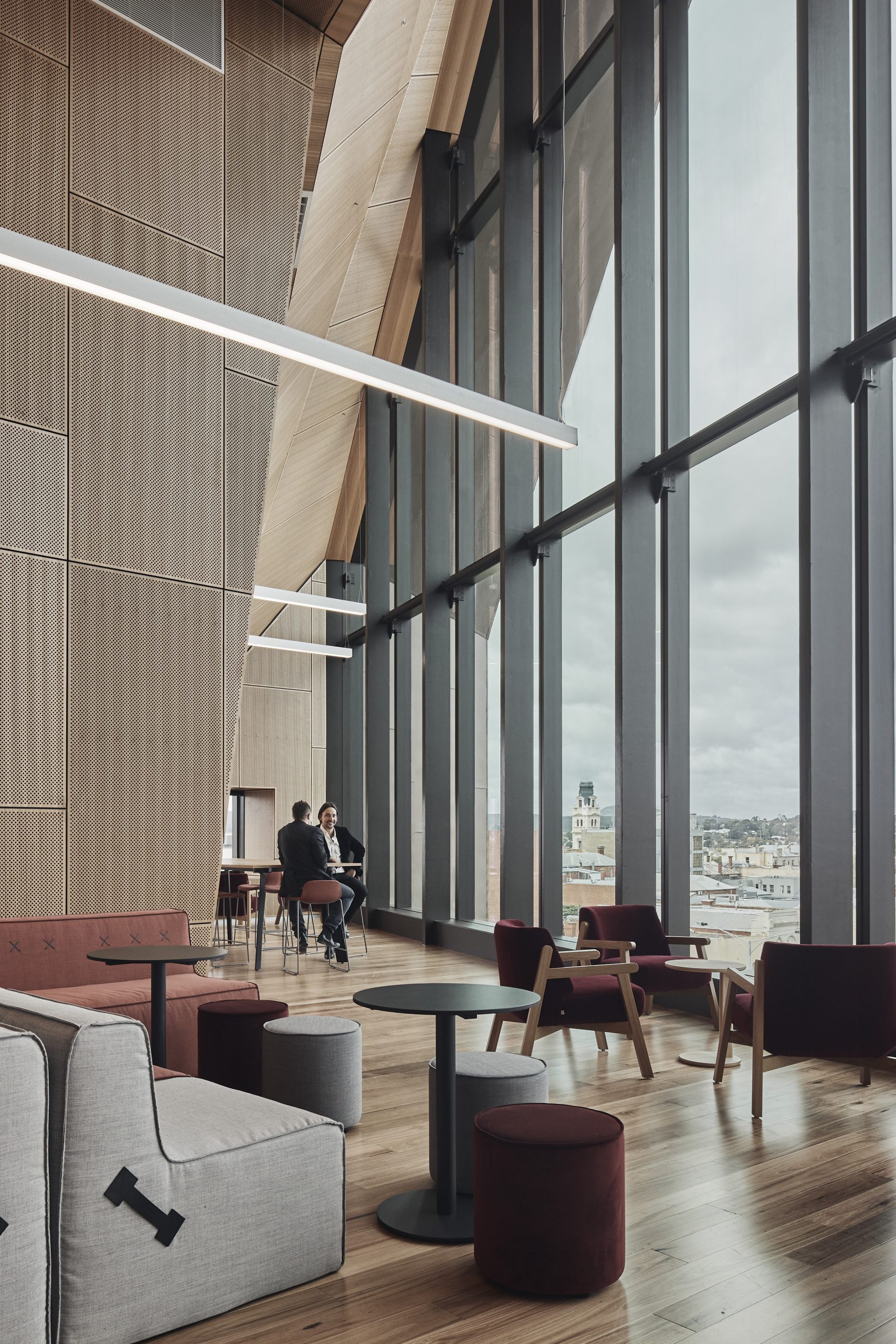
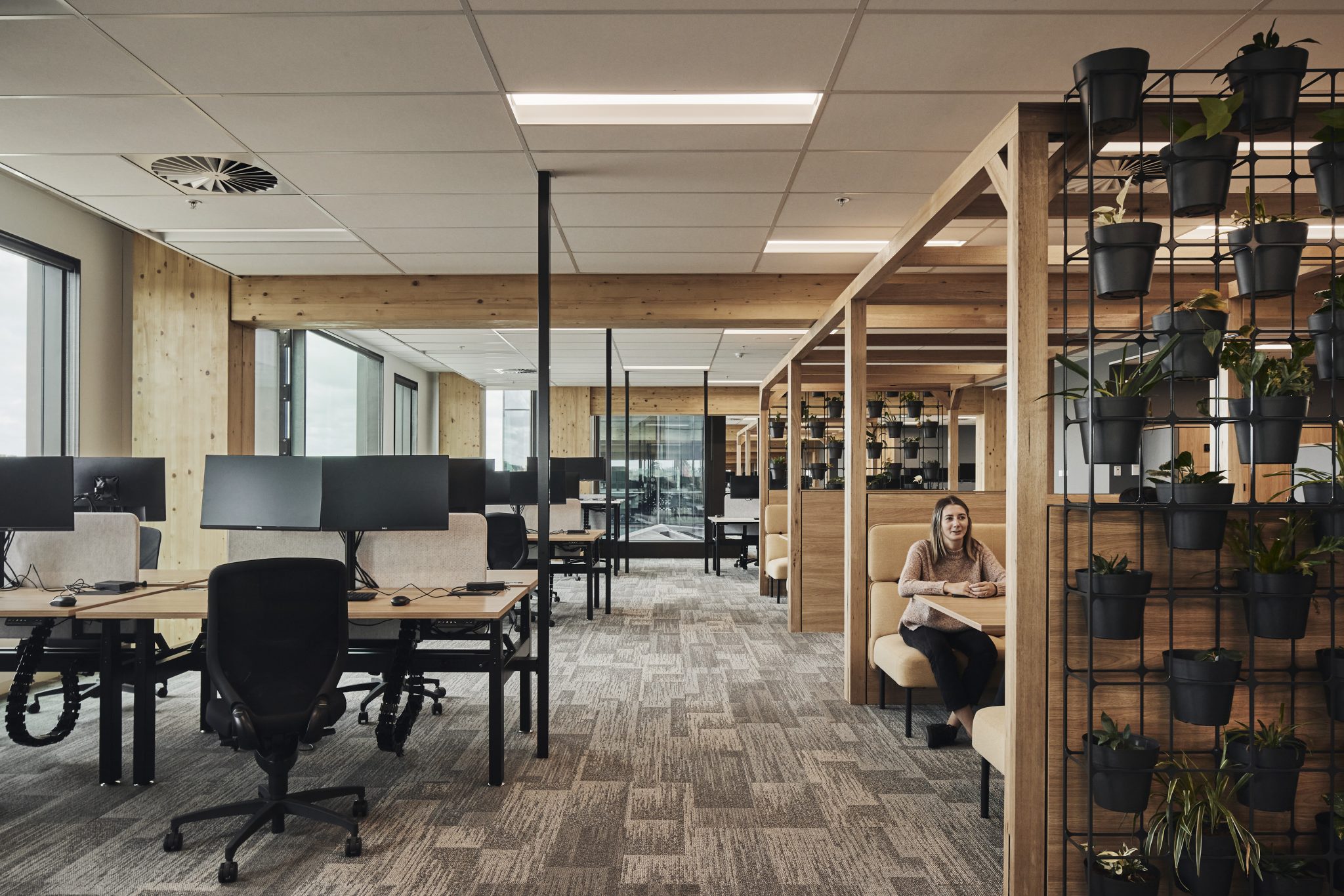
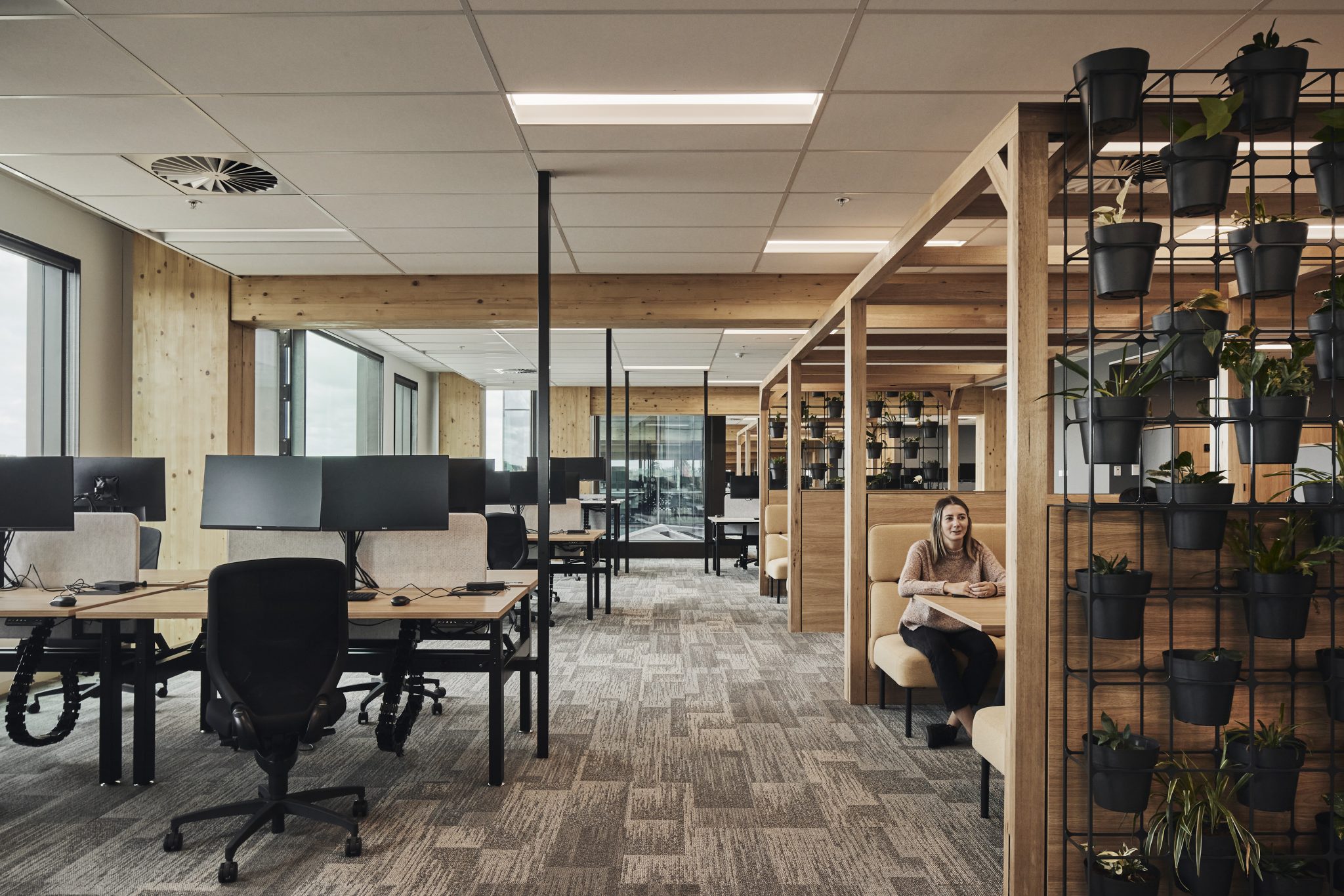
“Engineered timber is not flexible in regards to changes to penetration locations after the design has been developed in detail, and the beam depths required meant careful coordination was critical to achieve the architectural vision of the project and maintain head clearance heights.”
He says the level of coordination needing to be undertaken very early in the conceptual design phase was much more detailed compared to a conventional design utilising a concrete or composite structure.
Because AECOM was also engaged to provide structural engineering, 3D modelling software was utilised from the outset to test and coordinate multiple services and structural options.
“The reduction in façade heat gain due to the punch windows meant a reduction in installed thermal plant and a reduction in on-floor duct sizes,” says Yuen.
He says to this end, the AECOM mechanical and ESD teams worked closely with the architectural design team to determine the extent and properties of the glazing. Their aim was to sufficiently limit heat loads in order to facilitate the mechanical services design.
The detailed design was then completed in conjunction with mechanical services contractor D&E Air Conditioning. D&E was engaged under a D&C contract, and began working with the project team from February 2019.
Local flavour
Ballarat-born Luke Jarvis, associate at John Wardle Architects, shares some of his favourite features of the Ballarat GovHub.
“As a local resident, who was born and grew up in Ballarat,” he says, “I held dear the opportunity to be involved with a project like this a project that was a great marker of civic value to the City of Ballarat.”
Having attended many events at the Civic Hall, Jarvis was well attuned to the hall’s cultural significance.
“Importantly, the project was a major step forward in the revitalisation of the centre civic precinct, once at the social heart of the community,” he says. “This building is purposely made for Ballarat, and over time will become a navigational marker to this new civic heart.”
And he says the form of the building is an important addition to the regional city.
“A timber building of this scale is unique to Ballarat,” he says. “It demonstrates a sensibility towards a sustainable outcome for this regional precinct, and has the advantage of a highly aesthetic finished form, environment credentials and significant construction advantages.”
Floor by floor
Ballarat GovHub’s office floors are typically serviced by low-temperature, variable-air-volume (VAV) air-handling units (AHUs) zoned per façade, with heating hot water reheat on the perimeter VAV boxes.
The internal zone AHUs contain heat-wheel recovery, and are designed to deliver 100 per cent outside air.
This design was considered to be one of the most cost-effective methods of reducing mechanical services energy consumption, and contributes to the building’s 5 star NABERS Energy rating target.
Meeting rooms and comms rooms are supplemented by ducted water-sourced heat pumps (WSHPs) fed via the building condenser water loop. Due to the mixed-usage areas, the ground floor is served by a combination of technologies – chilled (CHW) and heating hot water (HHW) fan coil units (FCUs), perimeter zone VAV boxes and WSHPs.
Chilled water is supplied by oil-free magnetic bearing water-cooled chillers arranged in a variable primary-flow system connected to induced-draft cooling towers, located in the rooftop plantroom. Thermal heating is provided by condensing gas-fired boilers, also arranged in a variable primary-flow system.
The plantroom layout required careful coordination due to the bronze zinc gabled roof. The solution was to make sure the openings for exhaust air discharge and cooling tower heat rejection were carefully coordinated to maintain the architectural vision.
Where possible, the VAV zoning was aligned to suit the neighbourhoods created by the structural timber. The diffuser layout was also coordinated and spaced to create a consistent feel.
The double-height spaces on the north and south-facing facades of level four are conditioned via long-throw drum louvres. This accommodates an open space without visible ductwork.
Due to the openness of the neighbourhood interior layout, the base building systems can provide air conditioning and ventilation to the fitout without significant modification.
The building utilises a full building management system (BMS), complete with weather station. Conditions are typically maintained between 21˚C and 24˚C.
Key control strategies implemented include variable primary flow for the chillers and boilers to reduce pumping power; economy cycle to provide free cooling; and fan speed control of EC motors in the VAV air distribution system.
CO2 control is used to maintain adequate ventilation without “over-providing” outside air during periods of low occupancy, thereby reducing demand on the central energy plant.
Beyond the energy-efficient HVAC system, the Ballarat GovHub is fitted with a 130kW rooftop solar PV array for the generation of on-site renewable energy. Also, 50kL of rainwater is collected and stored to provide water to amenities and landscaping.
“What was clear from the design competition was that the proposed building was to have a lot of engineering elements exposed”
Highly rated
Since reaching practical completion and being handed over to Development Victoria in April 2021, the building has successfully achieved 6 star Green Star Design and As-Built ratings, and obtained a 5 star Green Star Interiors rating.
The NABERS rating assessments are currently on hold because minimum occupancy levels are yet to be met due to a slower than anticipated return to work post-pandemic.
Yet Hatty says the building has performed well since opening, with the 12-month building tuning period now complete.
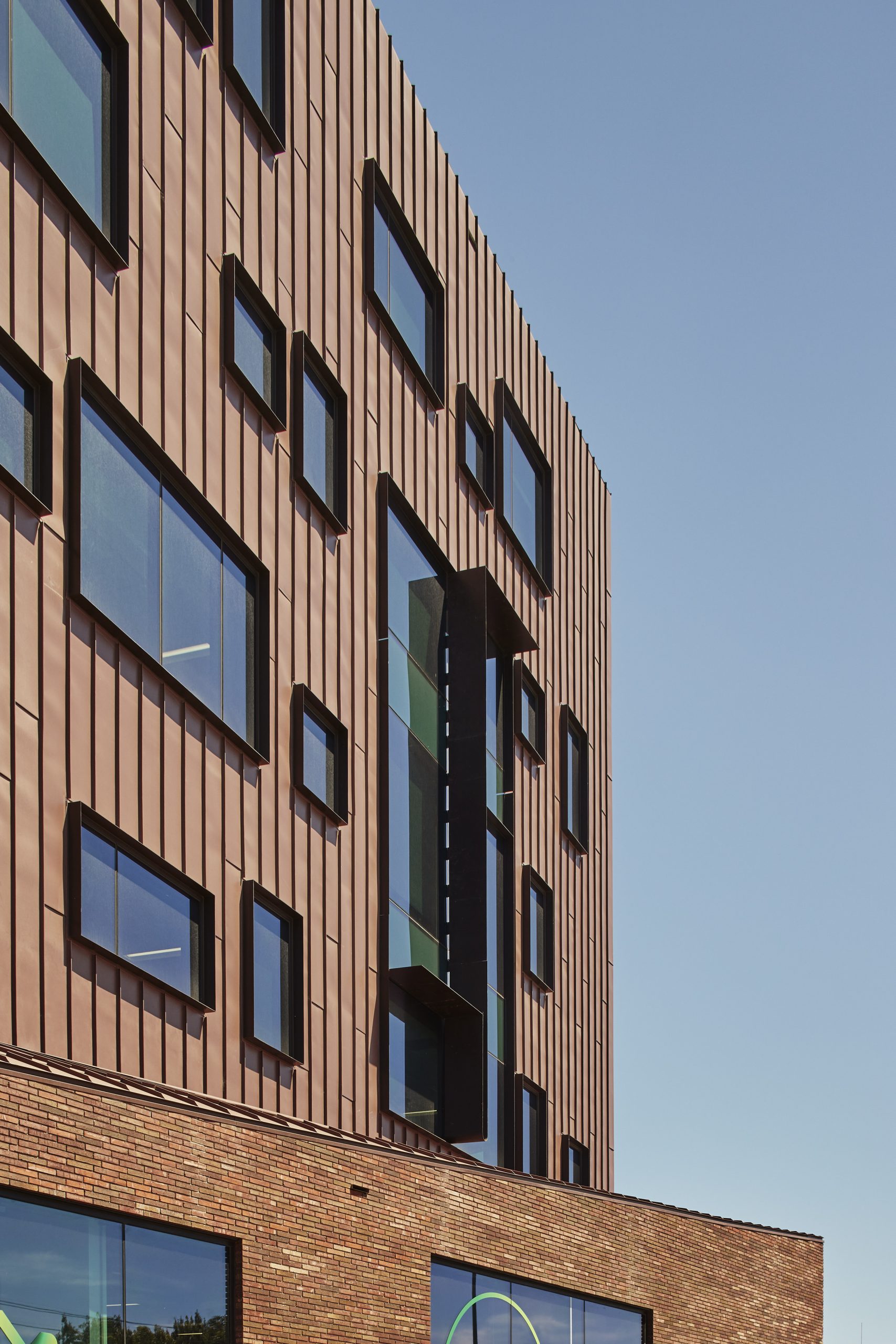
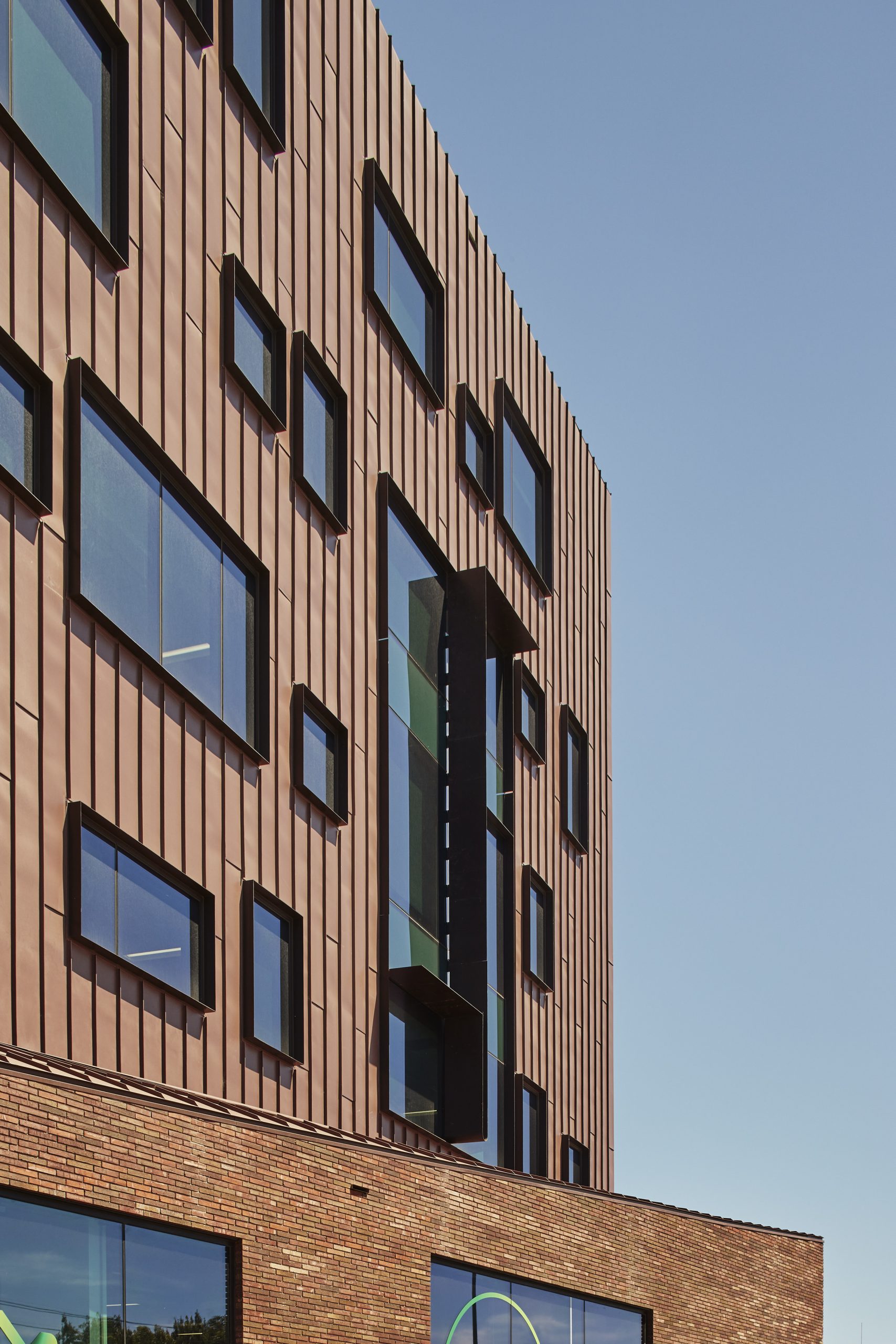
“Given the large amount of heating required in Ballarat’s climate, optimising the system to minimise gas consumption will continue to be a key focus,” he says.
The completion of the $100 million Ballarat GovHub is the culmination of about 350,000 work hours, with 500 jobs created during construction and more than 30 local and regional suppliers involved.
Development Victoria says the project’s completion represents a significant milestone for Ballarat, enabling the provision of hundreds of new and relocated jobs to the regional centre.
Lessons from the contractor
D&E Air Conditioning design manager Peter Hatty, M.AIRAH, offers several lesson learned from the Ballarat GovHub project.
- A collaborative and cooperative project team can assist greatly in achieving the overall project goals and provide opportunities for cross-profession learning.
- Early focus on areas of the building with different usage profiles, such as building lobbies, can assist in ensuring the correct performance without impacting on the other base building systems or energy consumption.
- A structured coordination process within a 3D modelled environment is beneficial for all.
- Timely appointment of the services trades can assist the consulting team with early input and resolution of tricky areas within the building and avoid last-minute problems with installation.
- Ballarat can be cold!
Project at a glance
The personnel
Architect: John Wardle Architects
Builder: Kane & Nicholson Joint Venture
Client: Development Victoria
Controls: Elliot Air Conditioning Controls
ESD Consultant: AECOM
Mechanical Services Consultant: AECOM
Mechanical Services Contractor: D&E Air Conditioning
The equipment
AHUs: Euroclima & PACAIR BMS: Johnson Controls Boilers: Automatic Heating Chillers: Smardt Cooling towers: Mesan Dampers: Bullock Diffusers: Shape Air Duct: Mega HVAC / Roo & Oz Sheetmetal Fans: Fantech Filters: Camfil (Airepure) Heat exchangers: FluidPro Pumps: Wilo Split air conditioning units: Daikin VAV boxes: Elliot Air Conditioning Controls VSDs: Danfoss< WSHPs: Air Solutions Water treatment: Hydro-Chem
(Source: D&E Air Conditioning)
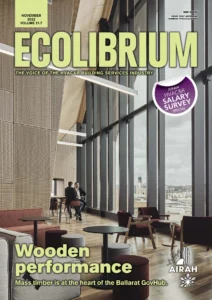
This article appears in Ecolibrium’s November 2022 edition
View the archive of previous editions
Latest edition
See everything from the latest edition of Ecolibrium, AIRAH’s official journal.