Triple treat
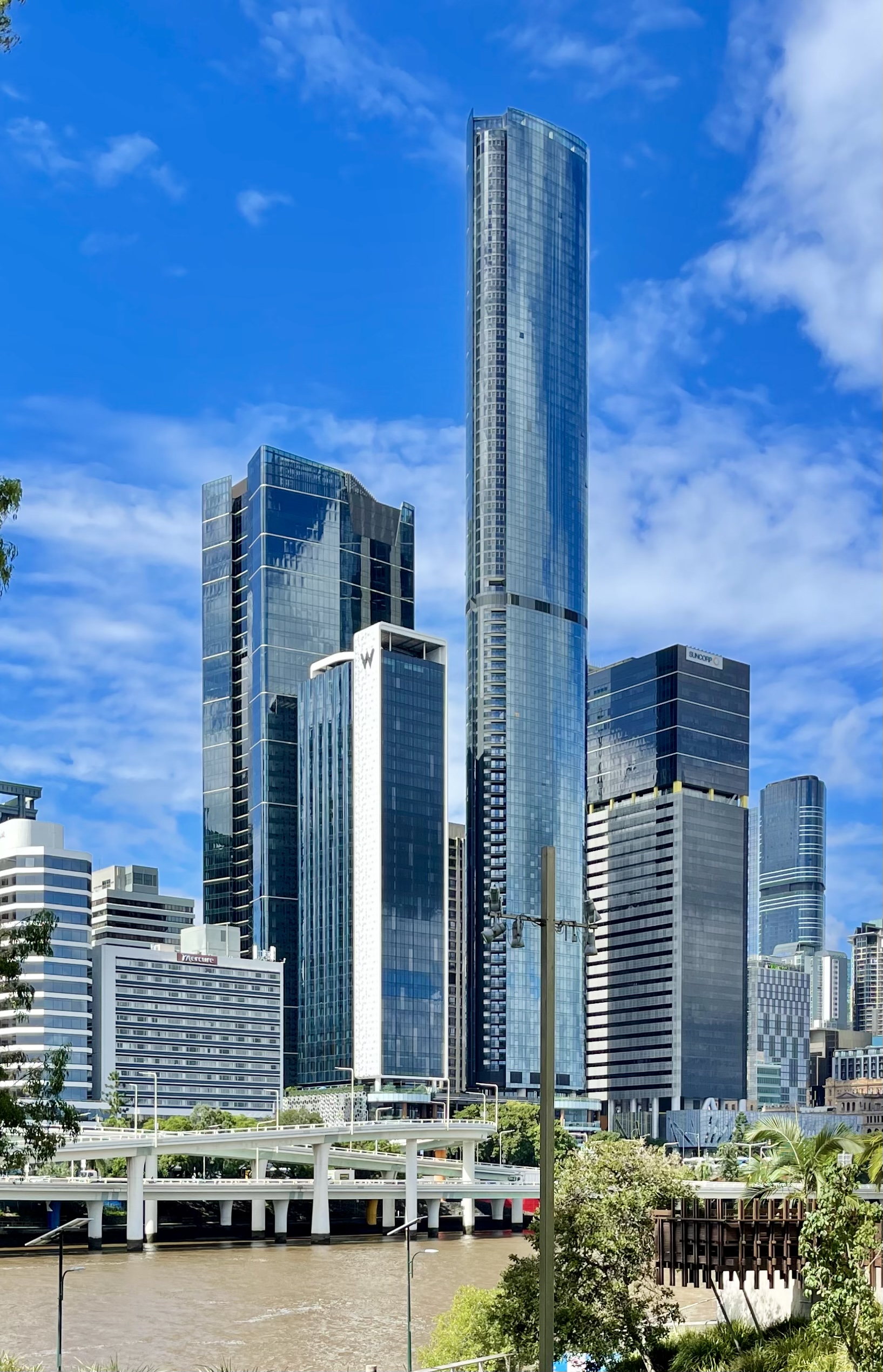
Located in the heart of the CBD and overlooking the river, Brisbane Quarter is Brisbane’s first truly integrated, world-class mixed-use precinct. Consisting of three buildings, the project presented the ideal scenario for a district-style heating and cooling scheme. Sean McGowan reports on the design and construction of the HVAC systems serving this $1 billion development.
Consisting of three buildings – a residential apartment tower, commercial office tower and hotel tower – and occupying almost 8,000m² of land, Brisbane Quarter is located on the old Law Courts site in Brisbane’s CBD.
Developed by the Shayher Group and built by Multiplex, Brisbane Quarter represents the city’s largest integrated development, with its three shimmering towers transforming the city skyline.
The tallest of the three buildings is the residential tower known as The One – now Brisbane’s second-tallest building. Designed by DBI and Group GSA Architects, the 81-storey building reaches 264m high and features 467 luxury two- and three- bedroom apartments.
Beside it stands the 182m, 41-storey high commercial office tower at 300 George Street. Designed by DBI and COX Architects, it features a total net lettable area (NLA) of 48,409m² and floor plates up to 1,472m² in size.
The 126m high, 34-storey W Brisbane hotel by DBI and Zenx Architects completes the trio. Located on the corner of George and Ann Streets, the 5-star hotel features 312 guest rooms and suites – many offering panoramic views over the Brisbane River and Southbank.
All three towers sit on a shared multi-level podium featuring a mix of retail and hospitality venues, as well as the hotel’s reception and lobby. A basement carpark sits below.
Almost a decade in the making, Brisbane Quarter was completed in three stages culminating in the completion of The One residential tower in September 2021.
Front and centre
Following a competitive tender process, Ellis Air was engaged by Multiplex as the D&C (design and construct) mechanical services contractor for Stage 1 works in July 2015.
The company was subsequently awarded both Stages 2 and 3 throughout the lifetime of the project.
Commencing with a schematic design by consulting engineer Floth, Ellis Air was initially charged with the design and construction of mechanical services including a central energy plant (CEP) to serve the entire precinct, the podium and basement carpark, and the 34-storey hotel tower.
“When tendering the early stages of the project, including the CEP, it was important for us to fully and comprehensively understand the project scope in its entirety,” says Ellis engineering manager Air Scott Cahill, M.AIRAH.
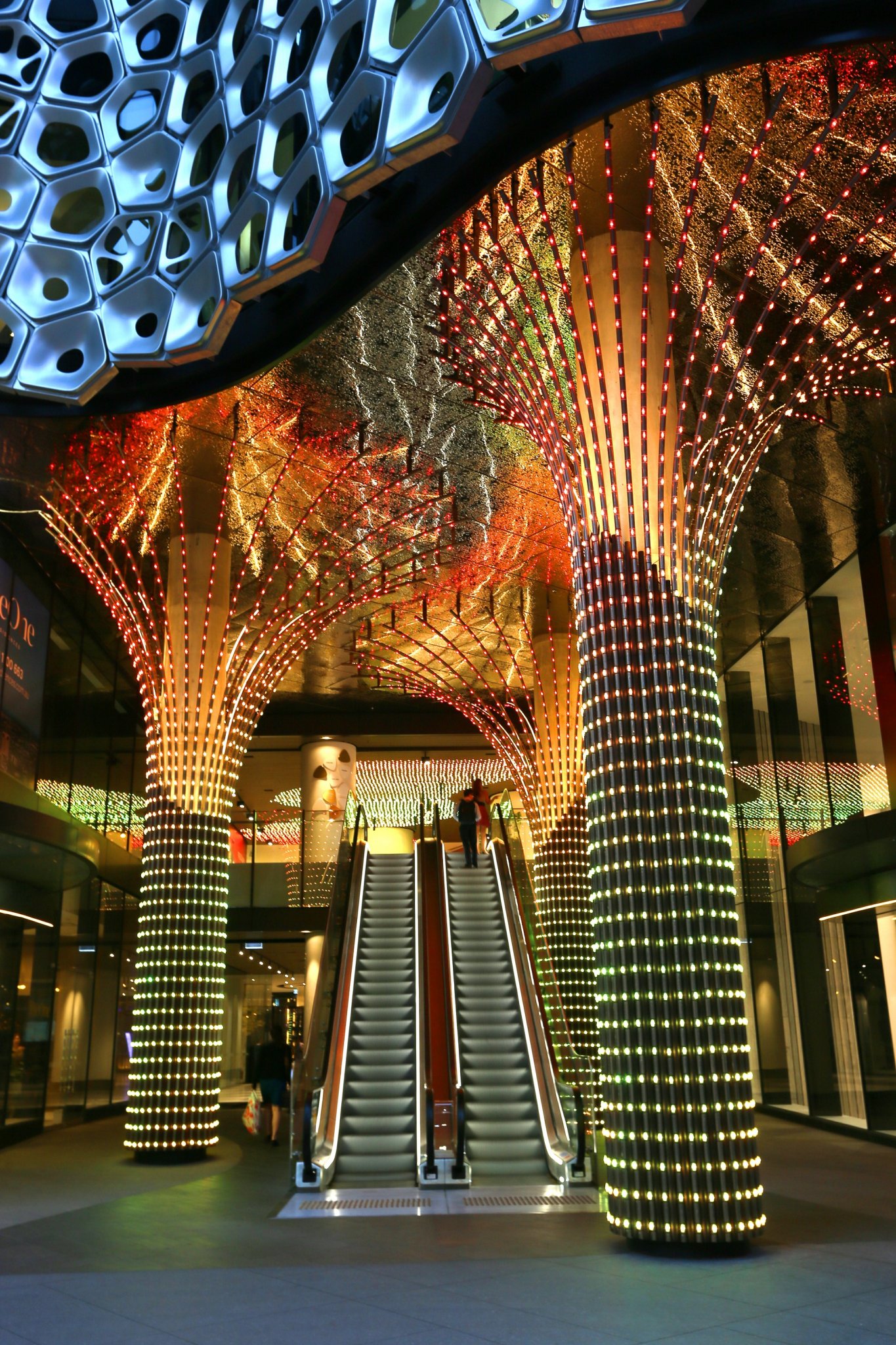
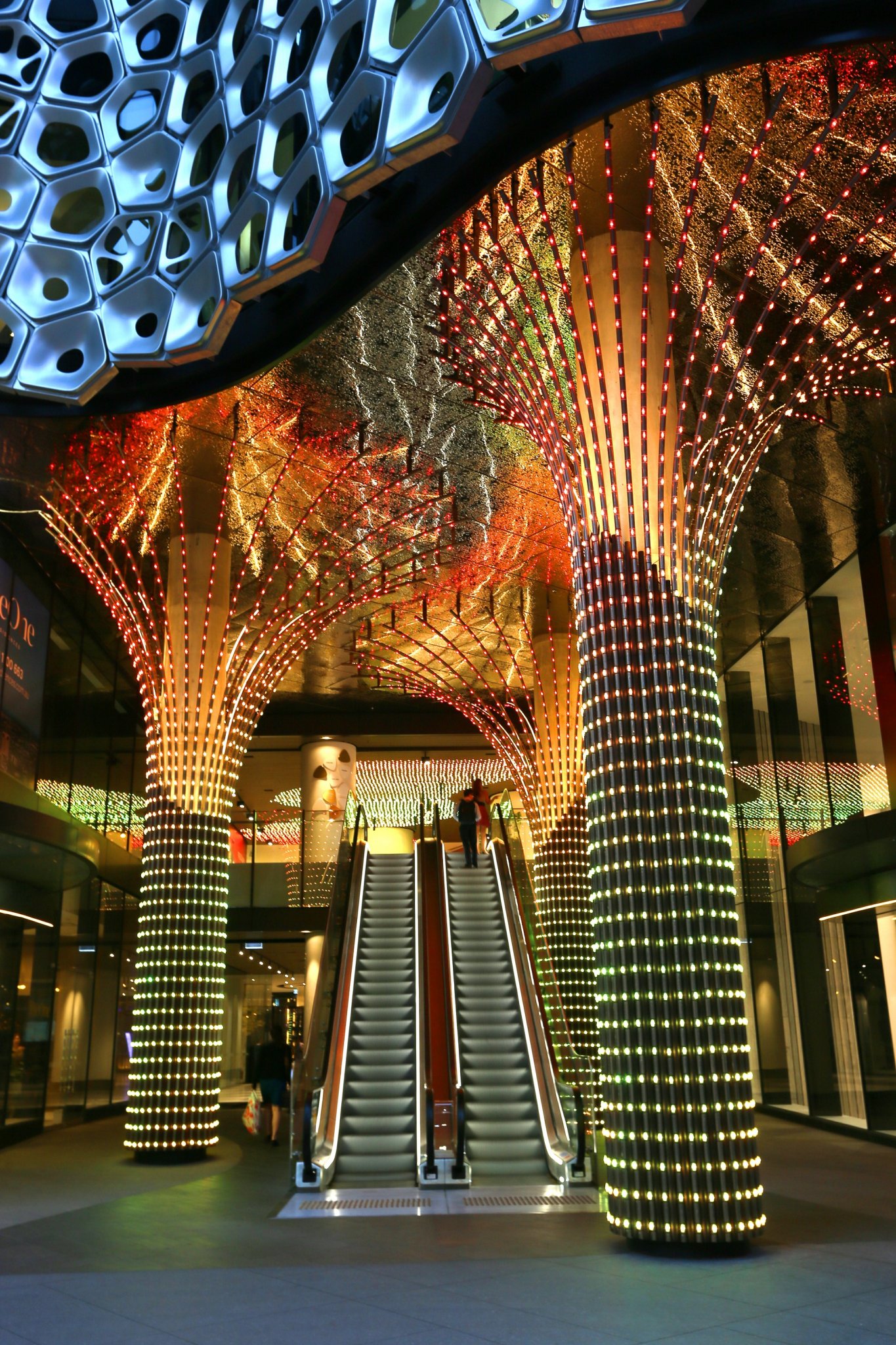
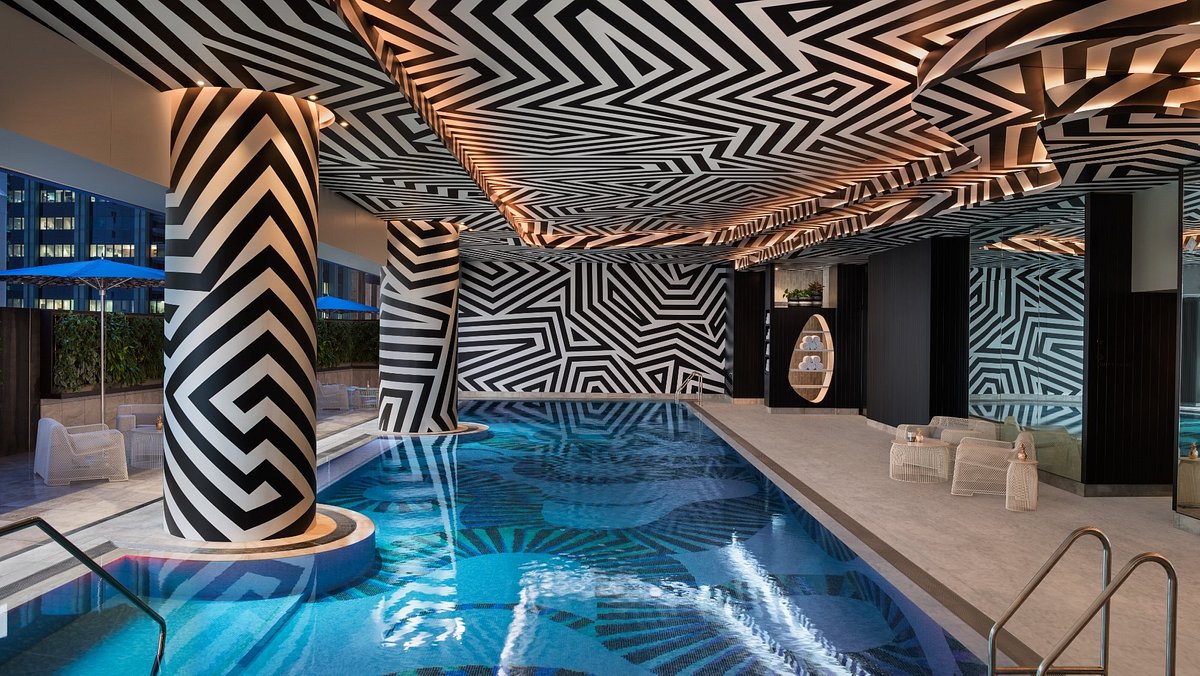
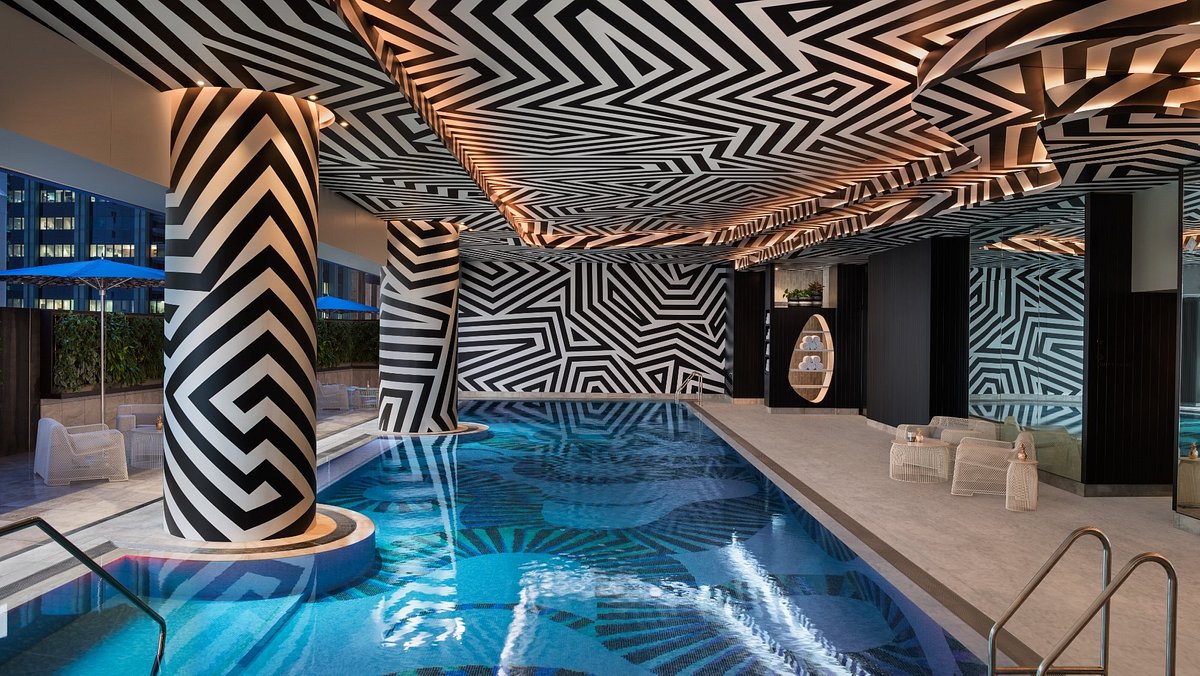
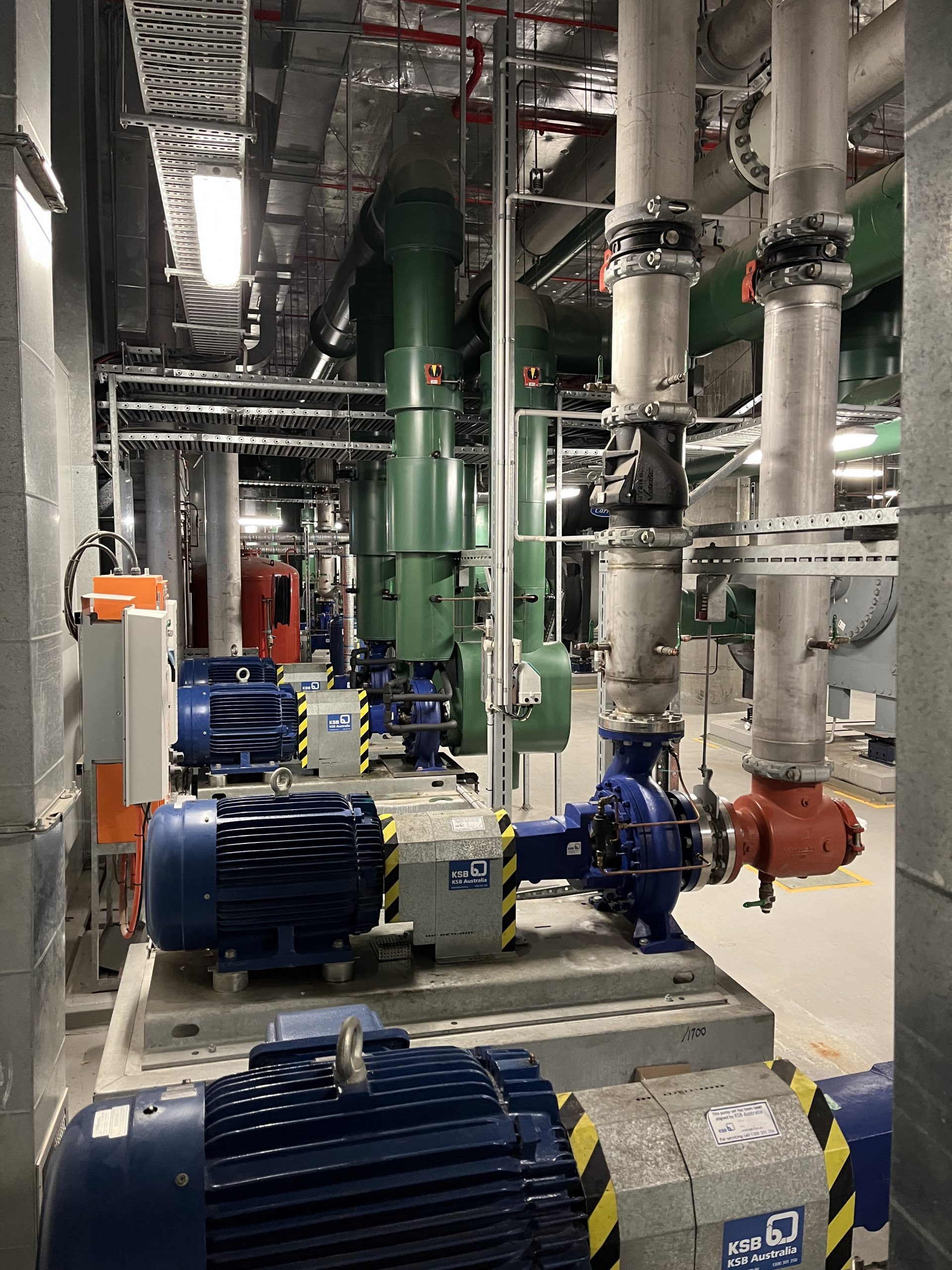
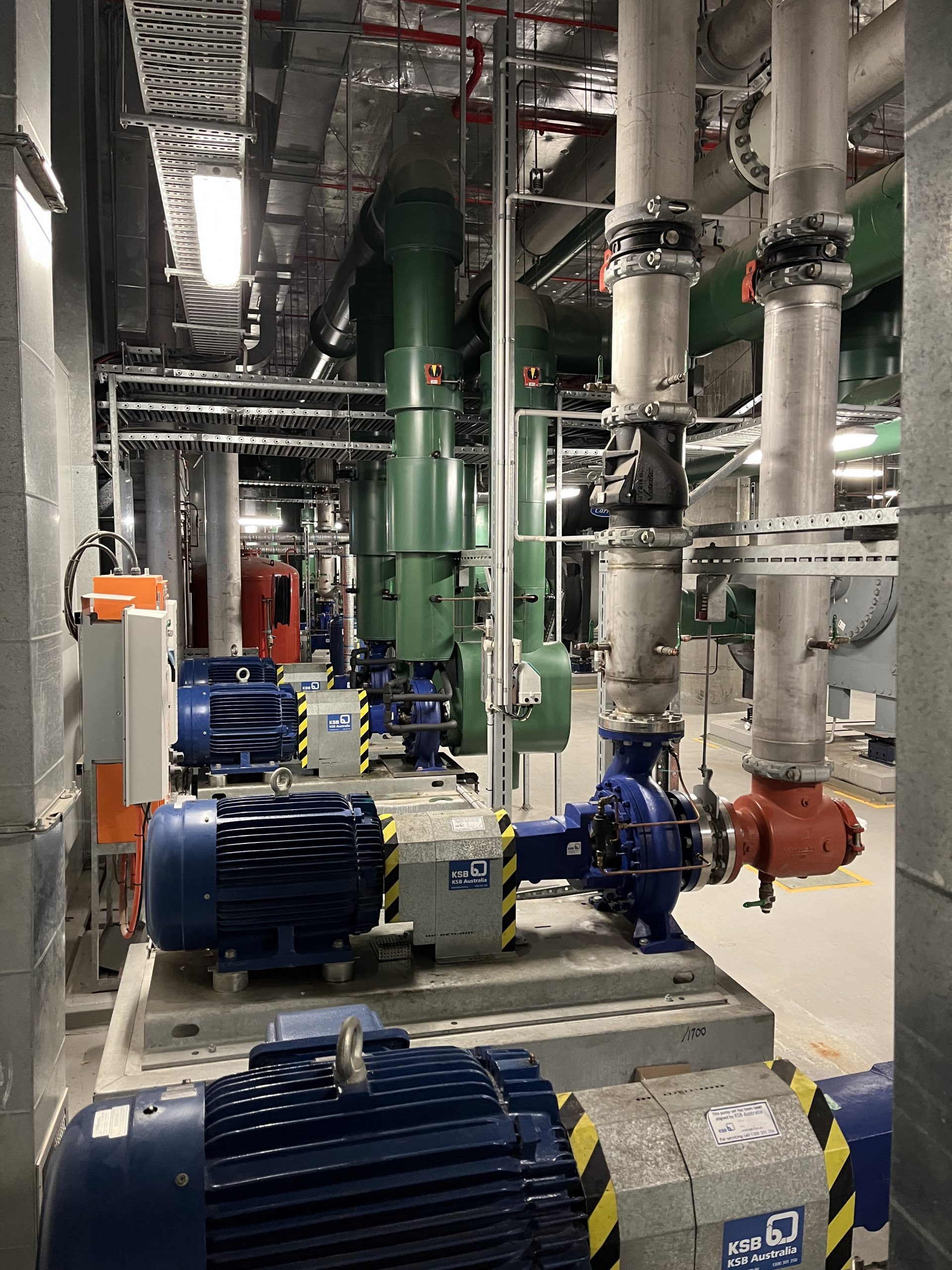
“While it was known that there were three separate buildings, the final services concepts were not yet completed, and subject to change based on the client’s final requirements. Therefore, it was vital we carried out a thorough engineering review to ensure we had confidence in our proposed changes when compared to the original Floth design, and that we had all the scope covered for the future stages.”
The Floth design included plantroom spatial allocations, riser locations and services routes in single line format, allowing Ellis Air to understand the design intent. Similarly, main plant and equipment had been nominated with performance requirements noted.
“Floth had spent a considerable amount of time and effort in regard to the best option for the CEP and its operation to provide an energy-efficient solution for the project as a whole,” says Cahill.
“Obviously, each building would have significant cooling requirements alone – but putting these buildings together created an ideal scenario for a district-style scheme.”
Through the design review, Ellis Air worked to optimise the size of the CEP to ensure both the precinct’s cooling and heating requirements were met.
Agreeing on building diversity with the Floth team, Ellis Air selected the main plant and equipment to ensure high levels of energy efficiency could be achieved.
Cahill says that when reviewing the overall precinct’s load profile, each building was considered as a stand-alone project, with its own load profile and usage. Ellis Air then compared all three buildings’ load profiles at differing times of the day to determine the peak load for the entire precinct.
“Through this process, and calling on our in-house engineering expertise,” he says, “we were able to reduce the specified cooling load by approximately 15 per cent.”
Tower changeover
To minimise any interruption to building cooling, the process of changing over the cooling towers from the temporary plant was given enormous consideration.
As well as completing the works overnight to coincide with a low cooling load, the final condenser water system was flushed and water quality testing carried out to ensure the new system could be opened up to the existing operational system.
Additionally, functional testing of the cooling towers, valves and sensors located on the rooftop plant was also completed prior to the changeover.
“The chilled water system for both the commercial tower and residential tower had to be flushed, tested and commissioned utilising temporary pumps as these circuits were isolated from the operational system while still being constructed,” says Ellis Air’s Scott Cahill.
There was also the added complication of the system being a variable primary design, not affording the luxury of a secondary circuit.
“Therefore when each building reached practical completion,” Cahill says, “the commissioning teams were required to fine-tune and adjust the system to ensure it was operating at its optimal performance.”
A quiet night’s sleep
The mechanical services design serving the W Hotel features several central air handling systems – both constant and variable air volume (VAV) serving the podium – with chilled water (CHW) and heat hot water (HHW) coils in all AHUs.
HHW is provided by three 500kW gas-fired boilers located within the hotel tower plantroom to serve heating requirements within the hotel and across the podium spaces.
Cahill says a fire-engineered solution was provided for the smoke exhaust systems located within the podium retail areas and hotel restaurant circulation spaces with ventilation openings coordinated and integrated as part of the ceilings and partitions.
“Being the first W Hotel brand in Australia, there were a number of stringent internal acoustic requirements,” says Cahill.
These included a required noise level of no more than 35dBA across the hotel, while maintaining conditions at a peak cooling load – creating a number of challenges for Ellis Air.
To solve this, the team constructed an offsite mock-up room, and spent considerable time working with fan coil unit (FCU) manufacturers to provide a solution. Consequently, FCUs were custom-designed, utilising EC motors to achieve the stringent noise requirements.
“The EC fan-powered FCU was developed with a Brisbane manufacturer to provide the required flexibility and also work in with the overall hotel room control system that controls HVAC, lighting, audio/visual, curtains and room occupancy detection,” Cahill says.
Custom-made cushion head boxes were also developed to produce a more linear pressure drop across the grille façade to further improve acoustics.
The Ellis Air team then constructed an onsite test hotel room with the final proposed solution installed. This was thoroughly and independently tested before the commencement of the hotel fitout.
“Upon the fitout being completed,” Cahill explains, “we fine-tuned the system during commissioning when we were able to control the fans to ensure both airflow and noise levels were achieved.”
300 George Street
The commercial office tower at 300 George Street offers PCA A-Grade office spaces served by a low-temperature variable-air-volume (VAV) system with high-efficiency swirl diffusers.
Plantrooms located on Level 5 and Level 40 serve 10 AHUs across the building, with each floorplate is configured into three perimeter zones and two internal zones.
Additional tenant auxiliary condenser water loop heat rejection is provided to all office floors, as is additional tenant toilet exhaust, outside air and general exhaust via dedicated centralised systems.
300 George Street has targeted 5 star Green Star and NABERS Energy ratings.


District cooling
Located on Level 5 of the podium, the CEP comprises a total installed cooling capacity of 13,580kWr in an N+1 configuration.
Four 2,770kW duty centrifugal water-cooled chillers have been paired in a series counter-flow arrangement, along with two 1,100kW duty screw water-cooled chillers also paired in a series counter-flow arrangement.
An additional 300kW screw heat machine is used to provide domestic hot water (DHW) pre-heating to reduce gas consumption. It is capable of co-generating hot water and chilled water.
The whole system utilises a variable primary pumping strategy with pressure sensors located through the piped systems.
The chilled water system serves the entire precinct, with all air handing units (AHUs) and fan coil units (FCUs) serving the hotel, podium tenancies, commercial office tower and residential apartment tower.
A pressure break on Level 44 of the residential tower minimises the working pressure of the system.
Importantly, all major plant and equipment are located above the flood level for risk mitigation. Additionally, this location minimised the chilled water (CHW) system working pressure.
Access to the CEP is provided via removable panels on the George Street façade, allowing for the future removal and replacement of the chillers to be completed at street level.
“We were fortunate to have a client who had the vision to commit to a central energy plant to serve the precinct, which represents a large, longer-term investment where the benefits are only seen at the completion of the entire development,” says Cahill.
A total of six crossflow cooling towers, totalling 16MW and installed in an N+1 configuration, are located on the rooftop of the commercial office tower. They provide heat rejection to the water-cooled chiller plant, and tenant condenser water for the entire precinct.
Remembering Mark Vigors, M.AIRAH
The late Mark Vigors, M.AIRAH, who sadly passed away earlier this year, was Ellis Air’s lead engineer for the Brisbane Quarter project.
Mark led the design for both Stage 1 and Stage 3, and was instrumental in the successful design and delivery of the project.
Temporary solution
Given the staged construction of the Brisbane Quarter precinct, three of these cooling towers were installed in a temporary location on Level 4 of the podium, surrounded by the construction site.
This temporary solution provided heat rejection to the operational hotel and podium retail spaces that were handed over at the completion of Stage 1 works in March 2018, and allowed construction of the commercial office and residential towers (Stages 2 and 3) to continue uninterrupted.
“The practical completion dates of the stages varied over about five years and thus, chilled water demand on the development increased gradually throughout this period,” says Cahill.
“It was only once the structure of the commercial tower was completed, that the three additional cooling towers could be installed in their final location.”
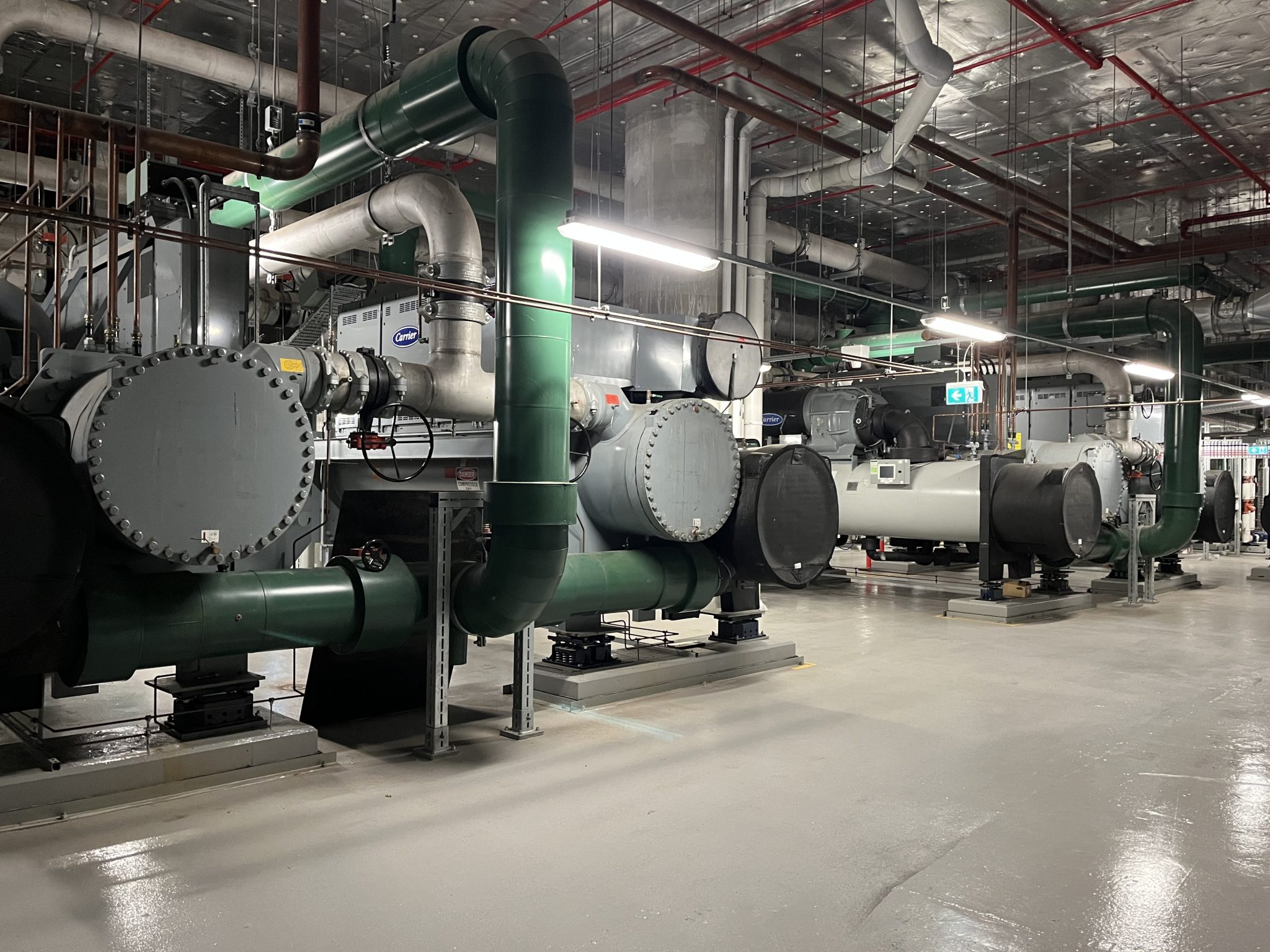
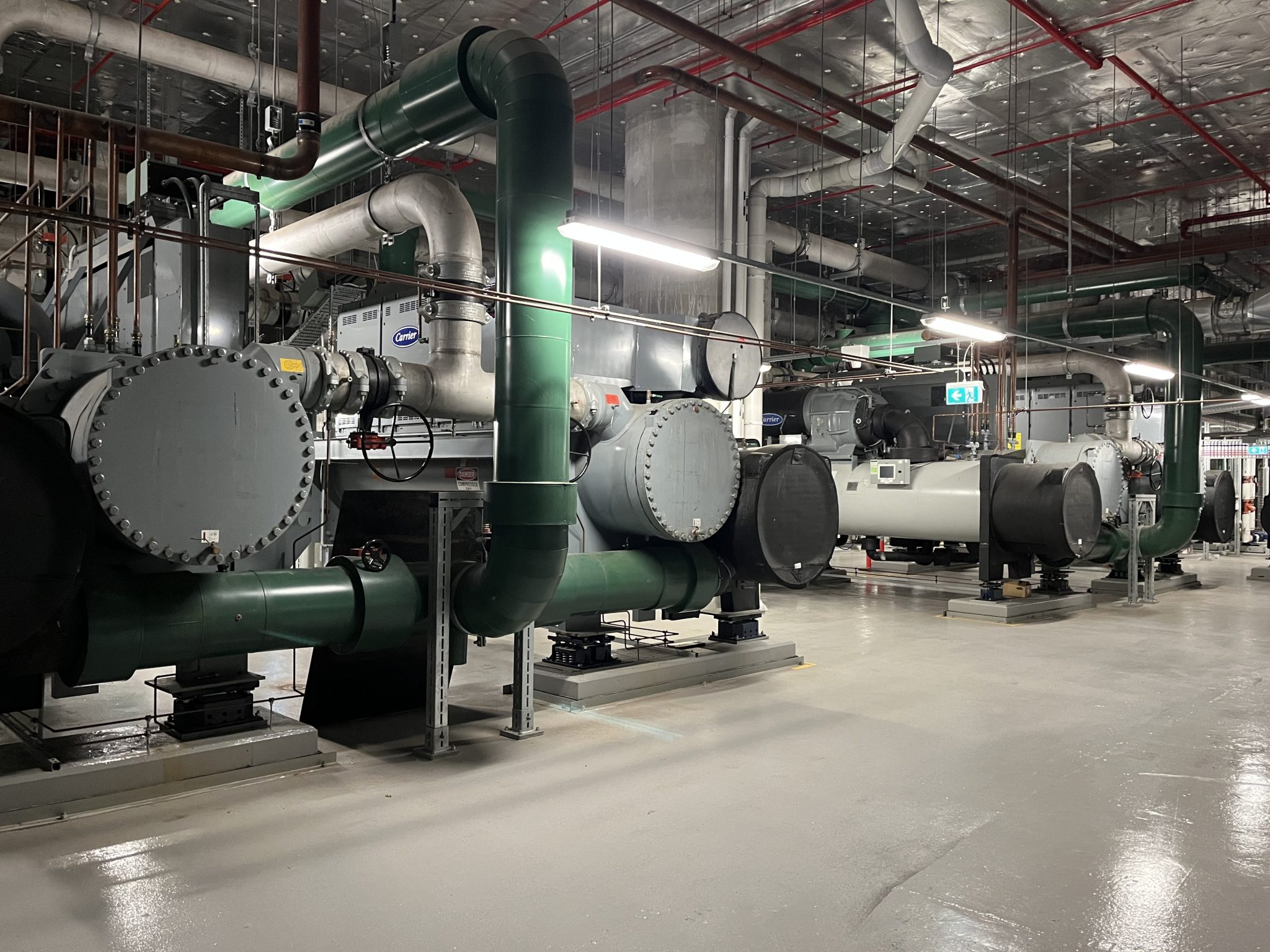
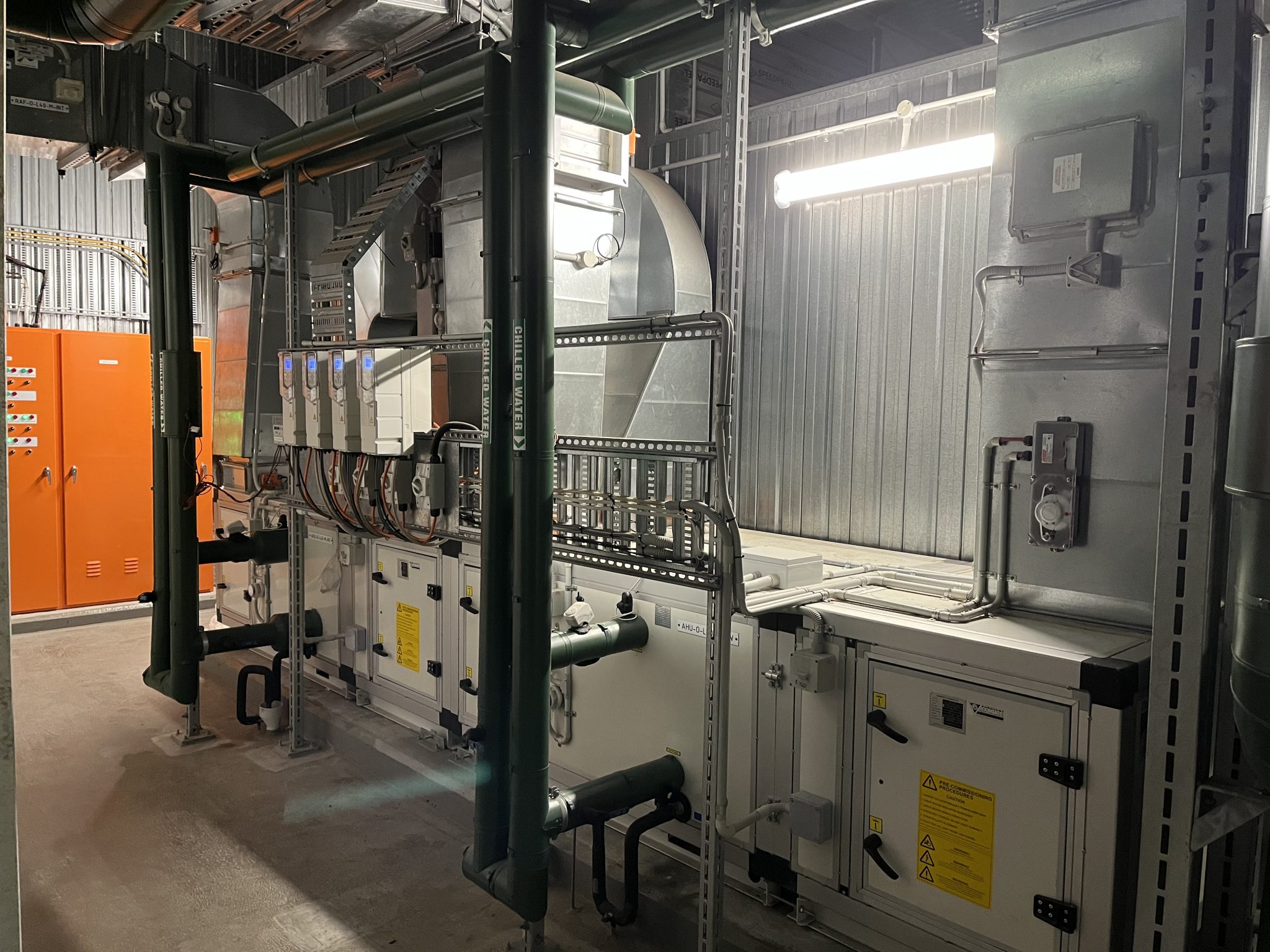
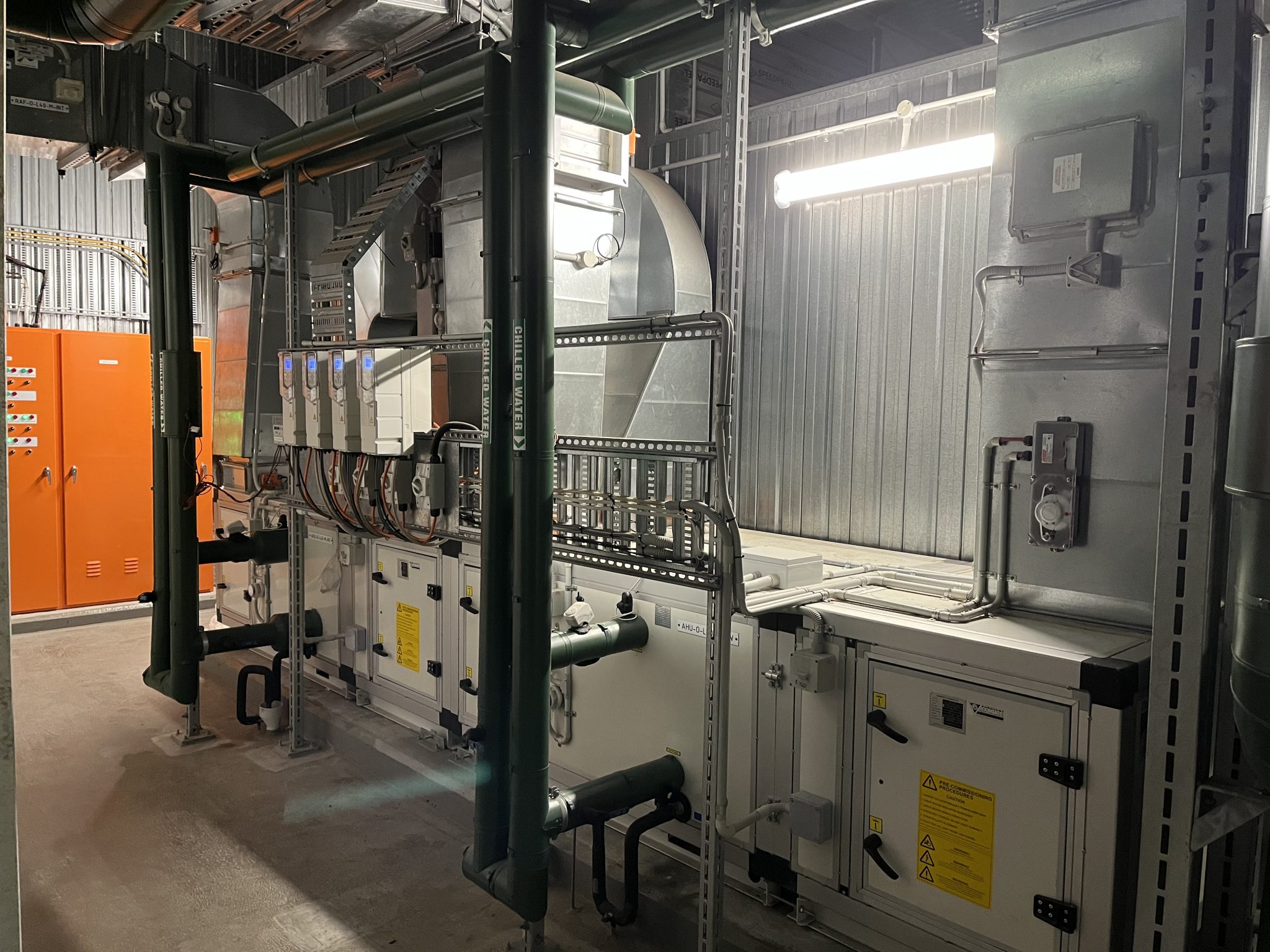
When all pipework and ancillaries were completed on the rooftop plant of the commercial tower, Ellis Air disconnected the towers from the temporary location on Level 4 and changed over to the cooling towers installed on the roof.
“There were a number of concerns in regards to losing the heat-rejection circuit, and in effect the cooling systems, for the entire precinct during this process,” adds Cahill. “It was therefore agreed that we carry out this changeover in a low-load scenario to minimise the effect should cooling be lost.
“Happily however, we were able to carry out this process successfully, and cooling requirements were continuously met without interruption and with no impact to building tenants and occupants.”
Once this changeover was completed, the three temporary cooling towers on Level 4 were disconnected and relocated to their final position on the rooftop. Following a vigorous maintenance and cleaning process, they were connected to the final system.
Commissioning challenges
The staged construction at Brisbane Quarter created a number of challenges for the commissioning of the mechanical services systems, with load gradually increasing as each stage was completed.
“The main strategy for the hydronic plant was to enable decoupled commissioning of Stages 2 and 3 to ensure no interruption to Stage 1 spaces,” says Cahill.
The commissioning of Stage 2 (residential tower) required a pump rig to be installed on the roof of the tower to allow the water system to be flushed and commissioned prior to integration, with a similar strategy utilised with Stage 3 (commercial tower).
“Located halfway up the residential tower is a secondary chilled water plant, which was configured to allow the pump sets to serve both the primary and secondary circuits within the building. Flushing and verification works were completed utilising this pump set.”
When it came time for integration, valves were opened and operating set-points checked.
Ellis Air set the chilled water system up as close to the design operating point (for the entire precinct) as possible to ensure that when other stages were brought into the system, the plant would be capable, preliminary set-points had been established and integration would be seamless.
To do this, the Ellis Air team made provisions to simulate flow rates at design pressure to the stages not yet built.
Additionally, the chiller configuration of two series counter-flow chiller sets and a low- load chiller required a large amount of load to commission the plant in accordance to its final operational strategy. Multiple plans were put in place to enable the plant to functionally work with the reduced load.
The BMS staging strategy of the chiller and heat rejection plant was also modified to accommodate this.
Learning lessons
Ellis Air engineering manager Scott Cahill, M.AIRAH, shares some of the lessons learned from a project the scale of Brisbane Quarter.
Build relationships
It’s important to build good working relationships with all members of the design and construction team to enable them to be able to work in a collaborative environment over a significant duration.
Assign responsibility
Ensure the project team is broken down into differing responsibilities (i.e., a different team for different building types). The project, from inception to completion, lasted five years, and utilising different teams enabled a large proportion of our in-house engineering and drafting team to take pride in the final product.
Staging and handover
Consideration for staging and handover requirements cannot be underestimated. Each separable portion shall have its own specific requirements that need to be brought to everyone’s attention as early as possible to ensure all parties understand the final deliverables.
Commissioning
Commissioning and fine tuning is vital to projects of this type and needs to be considered from the start to ensure items are incorporated at an early stage of the design to ensure rework is avoided in the installation process.
Service complements construction
You need to rely on a great service team that can provide high-quality maintenance and building tuning to the completed separable portion stages. They also need to have ability to complement the construction team’s advances to ensure a future seamless staged handover.
Tuning (and COVID)
The completion of the residential tower in September 2021 signified practical completion of the $1 billion Brisbane Quarter development.
For Ellis Air, however, a significant amount of fine-tuning of systems across the precinct, including the CEP, has continued post-completion.
“Much of the handover period coincided with the COVID-19 pandemic, which has brought its challenges and items not considered as a risk when we first carried out the design,” says Cahill.
Like most projects completed during the past few years, the ongoing low-load scenario could not have been foreseen.
“Low load was considered, and low-load chillers provided,” Cahill says. “However, when the hotel has minimal occupants, large areas of the podium are not in use and the commercial tower has no tenants the scenario has changed to one that no one could have imagined.”
Despite these challenges, Ellis Air has continued to work through the fine-tuning process. With the hotel becoming fully operational again, workers returning to the office and residents moving into their new apartments, load has gradually increased.
“Throughout this five-year long project, the Ellis Air service team have been instrumental in providing quality essential services maintenance (ESM) testing and certification, specialist testing and certification of the complex and multi-faceted fire and smoke control systems, and completed scheduled preventative maintenance to all HVAC equipment,” says Gary Ward, M.AIRAH, senior contract manager at Ellis Air.
Post completion, the contractor has been engaged to provide ongoing mechanical services maintenance of the precinct.
“When combined with ongoing building tuning,” Ward says, “this work will ensure HVAC performance, energy efficiency, life expectancy and indoor air quality and conditions are maintained without disruption to the occupants and users of Brisbane’s newest destination.”
Project at a glance
The personal
Architect (Base Building): DBI
Architect (Fitout): Zenx, COX, Group GSA
BMS contractor: LEA
Client: Shayher Group
Managing Contractor: Multiplex
Mechanical Services Consultant: Floth
Mechanical services contractor: Ellis Air
The equipment
AHUs: GJ Walker, Daikin
Chillers: Carrier
Cooling Towers: BAC
Fans: Fantech
FCUs: GJ Walker, Daikin
Grilles: Shape Air
Heat Exchangers: Alfa Lavel, Sondex, Fluid Pro
Kitchen Exhaust Treatment: AOM
Pumps: KSB
(Source: Ellis Air)
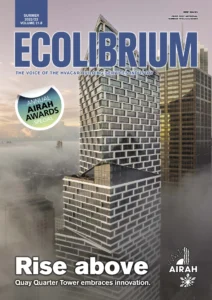
This article appears in Ecolibrium’s Summer 2022-23 edition
View the archive of previous editions
Latest edition
See everything from the latest edition of Ecolibrium, AIRAH’s official journal.