The comfort of family
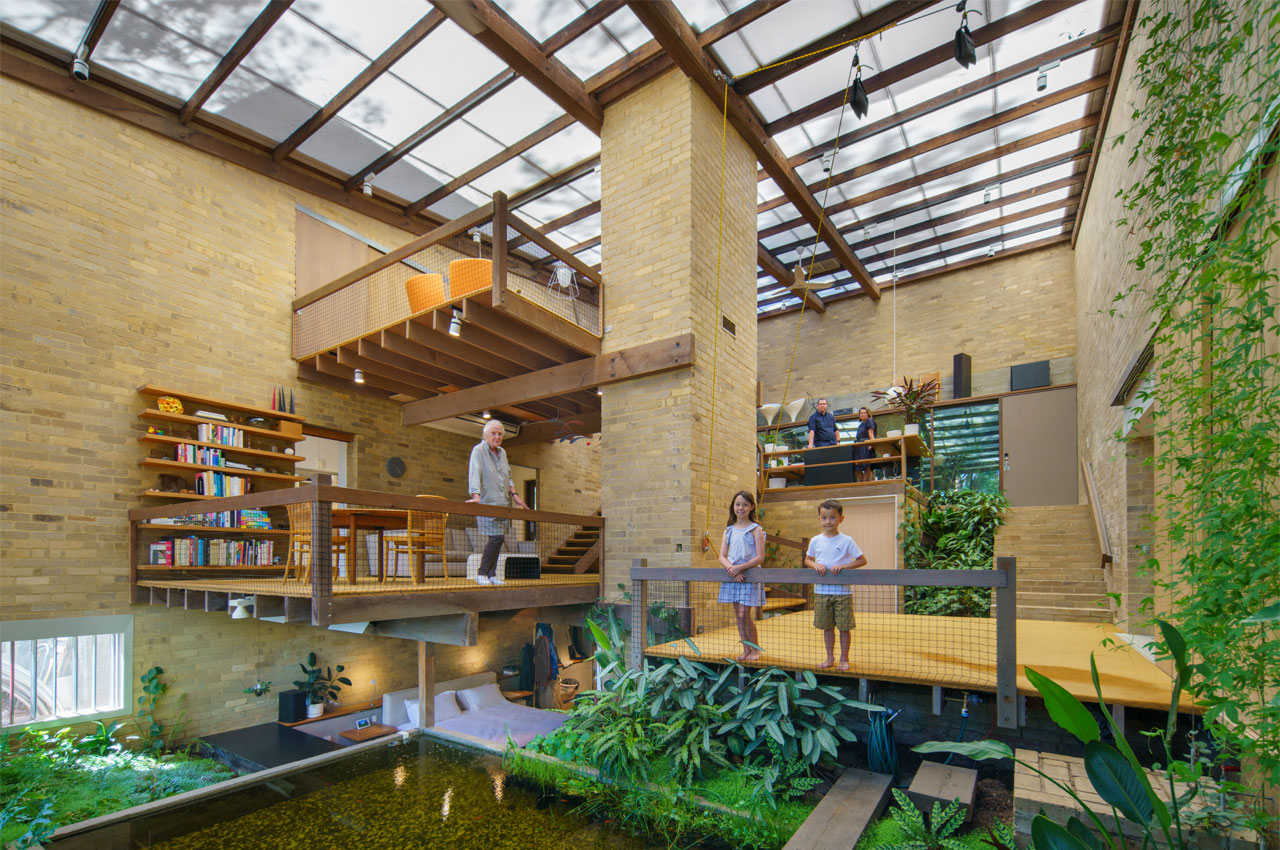
The development of a sophisticated control system for an iconic home in Melbourne’s leafy suburbs has not only provided greater comfort to its occupants but broken new ground in predictive climate control systems. Sean McGowan reports on a house that has been home to four generations of the Featherston extended family, having evolved every step of the way.
Located in Ivanhoe, Featherston House was designed by leading Australian architect Robin Boyd in 1967 for Grant and Mary Featherston.
Prolific designers in their own right, the Featherston name became synonymous with furniture, interiors and learning environment design for decades. The duo’s more high-profile work included the fit-out of the National Gallery of Victoria in 1966 and the Children’s Museum of Victoria from 1984 to 92, as well as various furniture ranges for Aristoc Industries and Uniroyal/Bridgestone.
Based around the theme of living within a garden, the design of Featherston House reflects the freedom afforded to Boyd by his clients.
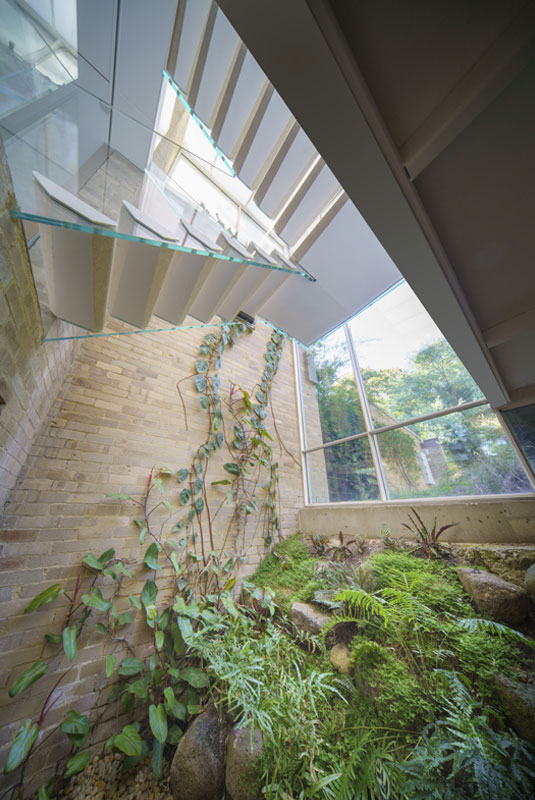
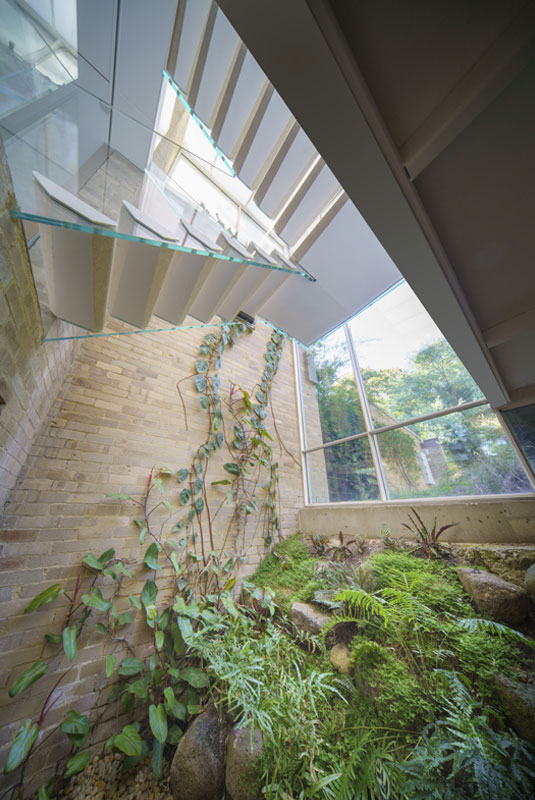
Considered radical for its time when completed in 1969 (and still pretty “out there” now), Featherston House is famed for an interior design that incorporates home with a professional workplace.
These spaces are configured across floating platforms placed strategically from the building’s brick core. They overlook an expansive indoor garden on the ground floor that connects the indoors to the eucalypt forest outside, which is framed by a large wall of windows.
An adjoining flat was designed to accommodate Mary’s parents at the time.
Fast-forward 50 years, and Featherston House is now home to Grant and Mary’s son Julian, and his wife Vicky – directors of multi-disciplinary building and design consultancy Two Feathers – and their two children.
They are now the fourth generation to live in the iconic house, following Mary’s decision to relocate to the adjoining flat – now known as Featherston Studio.
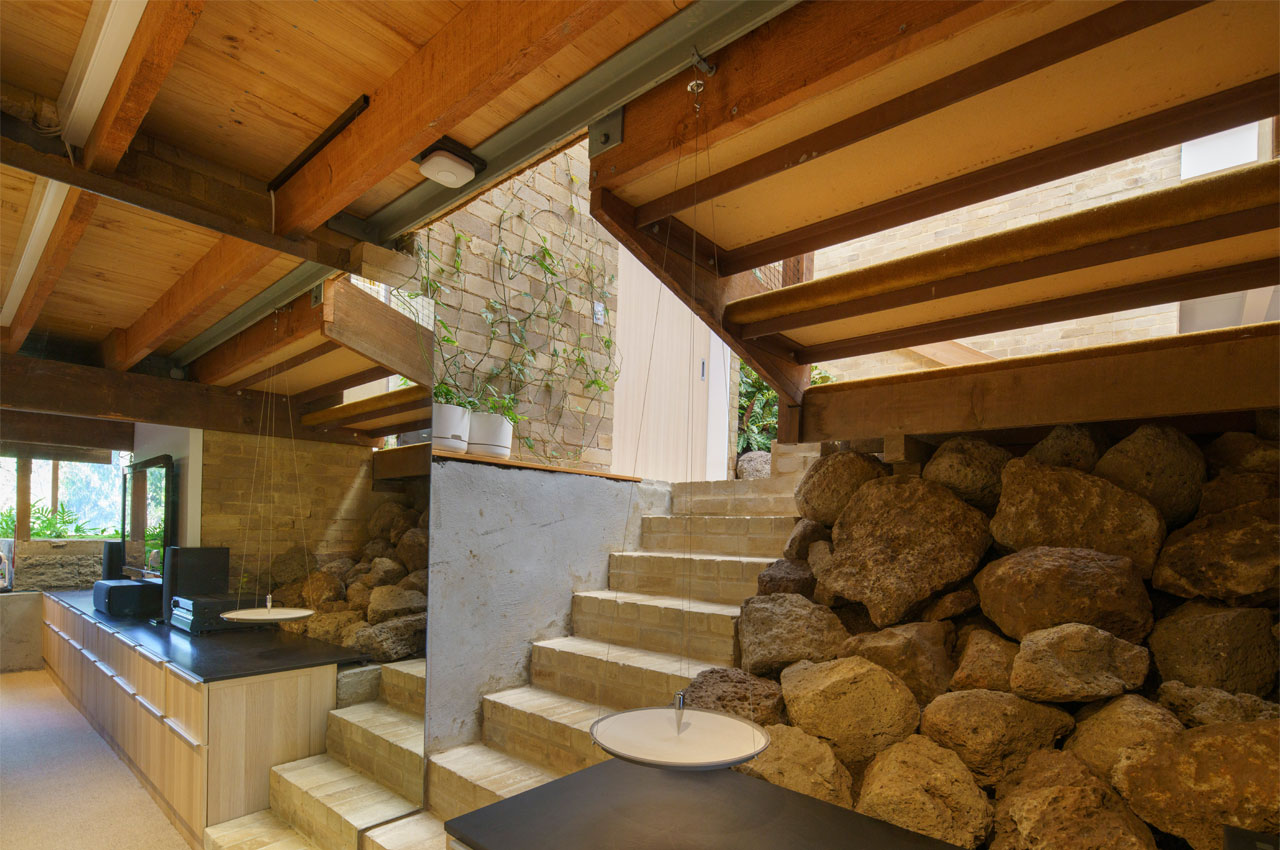
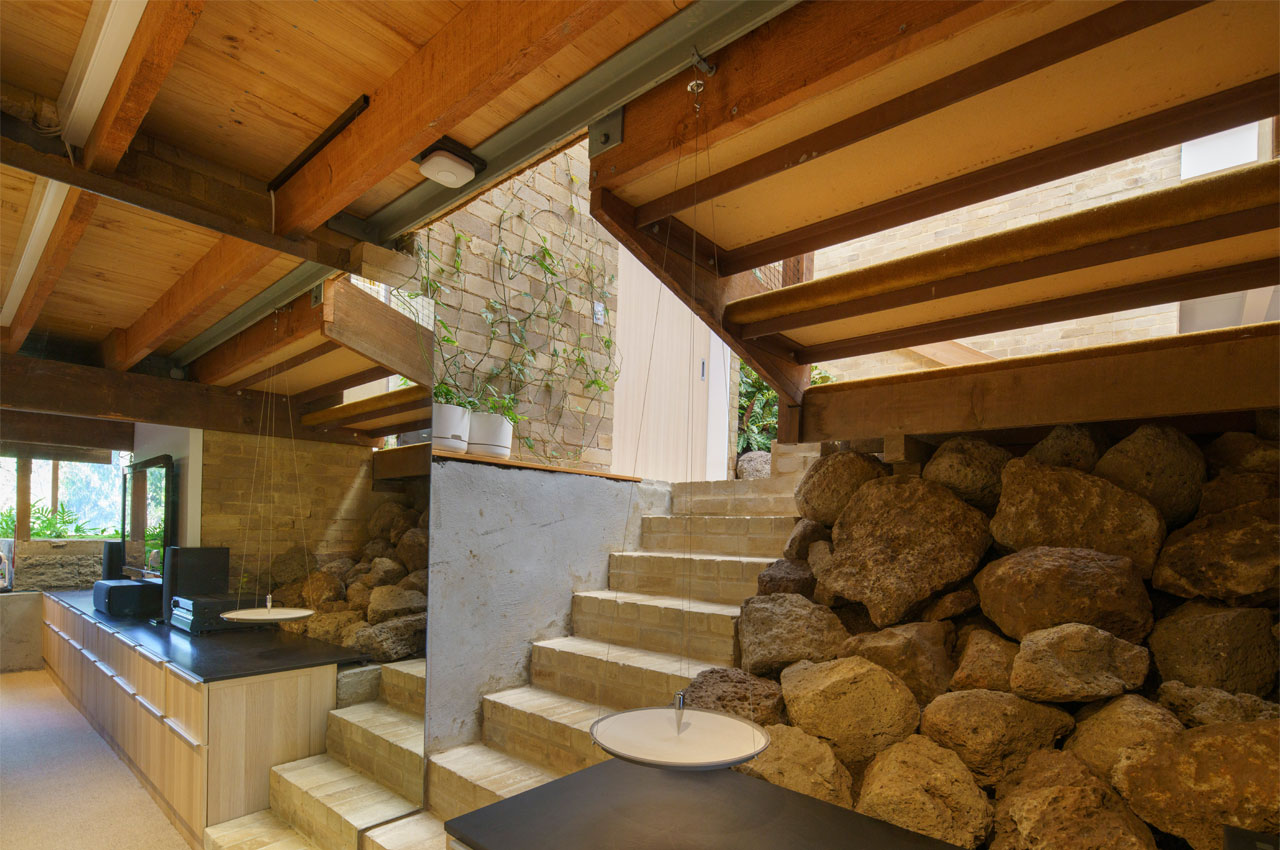
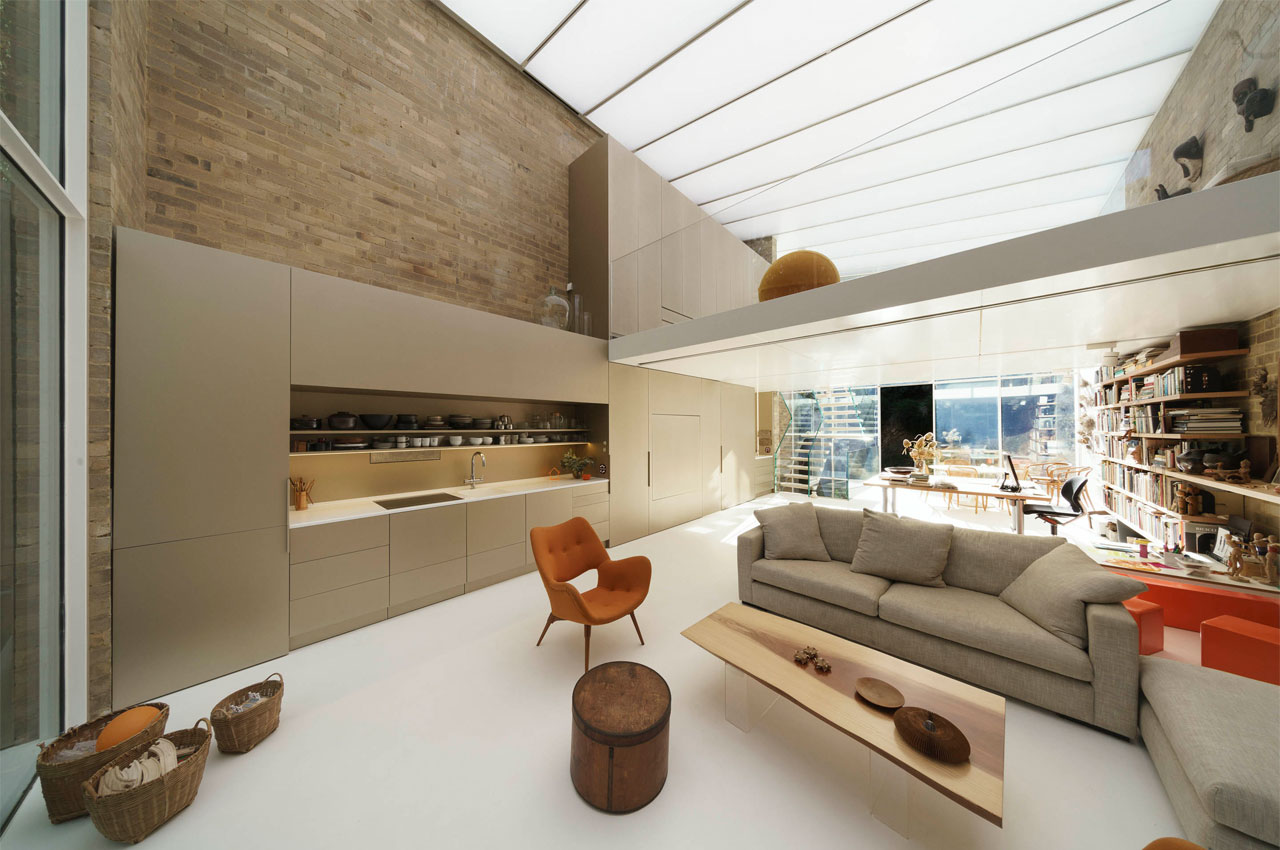
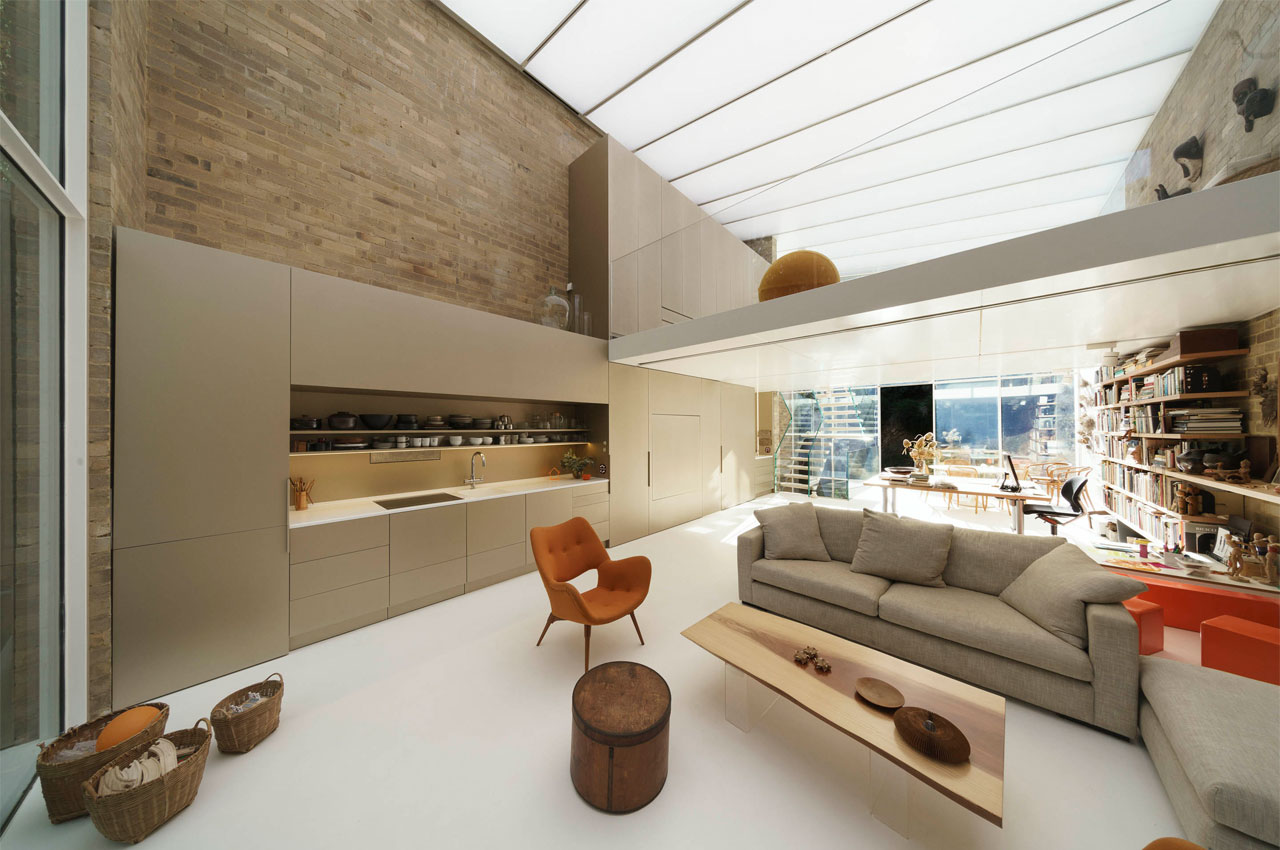
Updated and renovated
Both spaces have been updated and sensitively renovated, with great care and attention given to maintaining the legacy design of the home while adapting it for a modern lifestyle. In doing so, some of Boyd’s original concepts have been able to be fully realised thanks to advances in technology.
“The original building design called for a translucent roof and very large window wall, [but being] constructed in 1969 this was a real stretch for the materials available at the time,” says Julian Featherston, Affil.AIRAH.
The first attempt at the roof successfully achieved waterproofing but suffered from internal condensation, resulting in internal “rain” when it internal conditions were humid and it was cold outside.
“The second design solved both waterproofing and insulation challenges but suffered UV deterioration,” he says. “However, in a case of ‘third time’s a charm’, the current roof solves all requirements and now performs very well for a translucent roof.”
Another of the ongoing challenges associated with the open-plan design of the home has been temperature control.
Originally, the home was heated by an oil-fired boiler serving a water loop feeding two fan coil units (FCUs) in a central ducted heating system. A separate water-to-water heat exchanger provided domestic hot water.
According to Featherston, the return air path was incredibly poor.
“No one seemed to have considered that the return air path involved a door with no register in it,” he says.
This resulted in the rooms beyond the door being positively pressurised, and he surmises that most of the supplied air leaked to atmosphere.
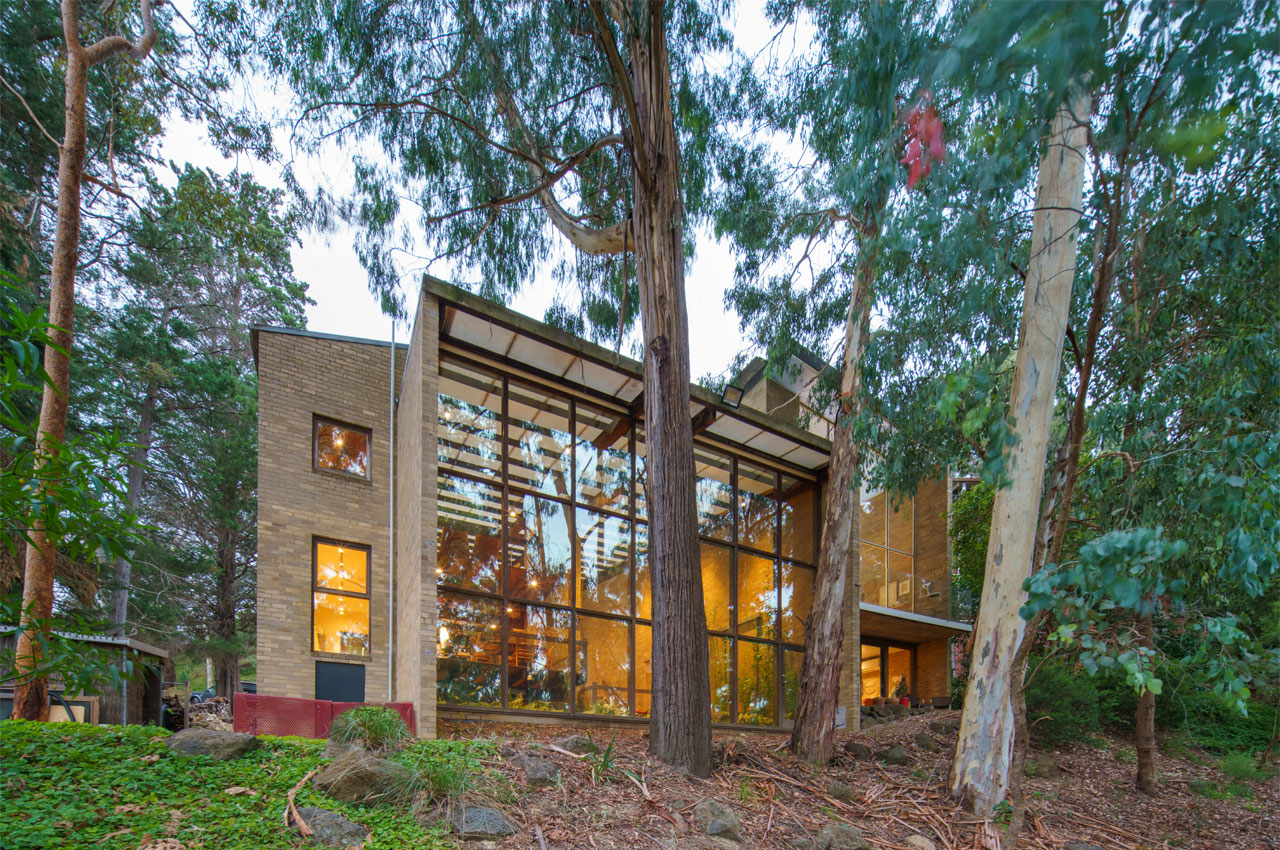
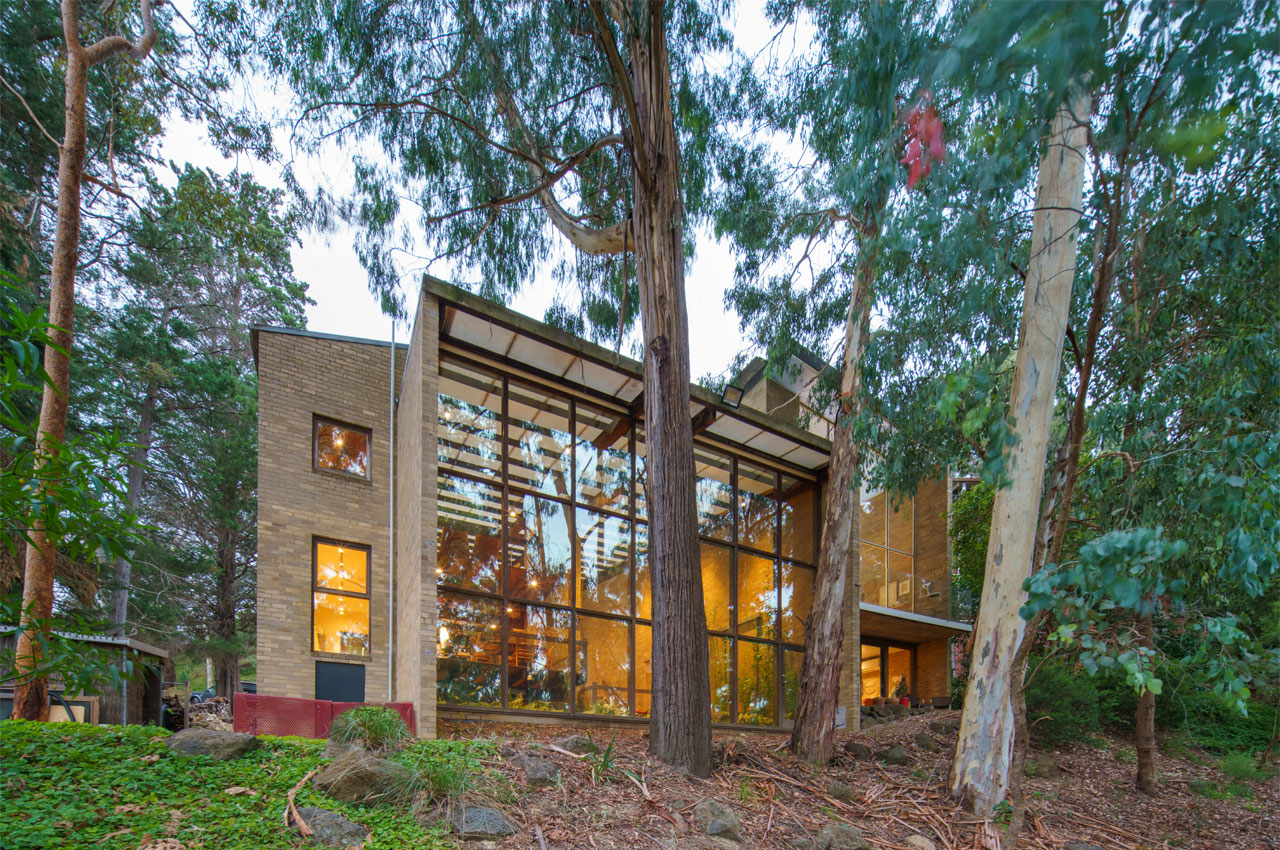
Prior to the most recent renovation by Julian and Vicky there was no active cooling system, with hot outside conditions leading to significant stratification in the open-plan design and resulting in some spaces being temporarily uninhabitable.
“Cross-ventilation was also attempted (as part of Boyd’s design), and was good in principal but could only deliver about 10 per cent of the volume required,” Julian says, “and meant we had flyscreens [installed] to some of the windows offering the best views.”
Consequently, the most recent renovation has seen all HVAC systems in both buildings replaced.
The Studio is now served by a commercial heat pump system, dedicated mechanical ventilation, destratification fans and external blinds fitted to the north and west-facing windows.
Similarly, Featherston House features a large, commercial heat pump system with mechanical ventilation and destratification fans installed.
Predictive control
A key outcome of Julian and Vicky’s renovation of Featherston House has been the development of a customised, predictive climate control system.
Desiring the new HVAC systems to respond to the weather conditions in real-time in order to maximise energy efficiency, the couple expected this type of intelligent, automatic control system to be readily available on the market.
To their surprise, it wasn’t.
“We assumed there would be an existing – and expensive – commercial solution that would be capable of achieving what we wanted, but we couldn’t find it,” Julian says.
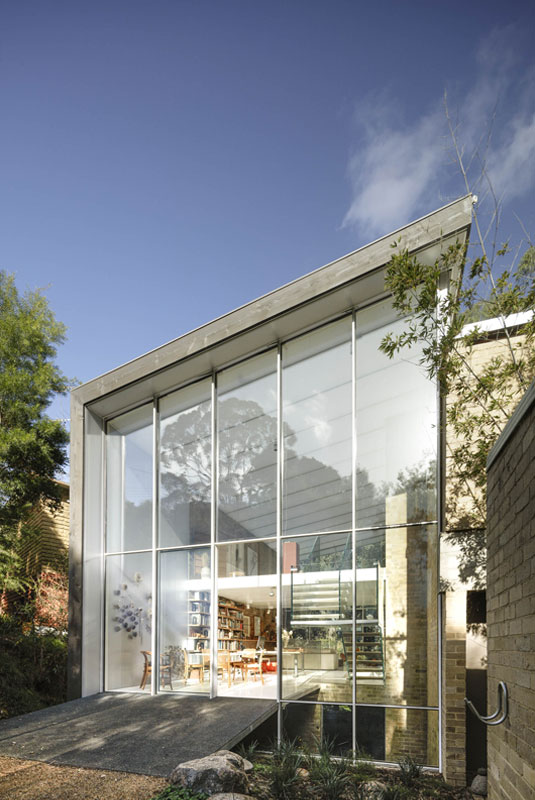
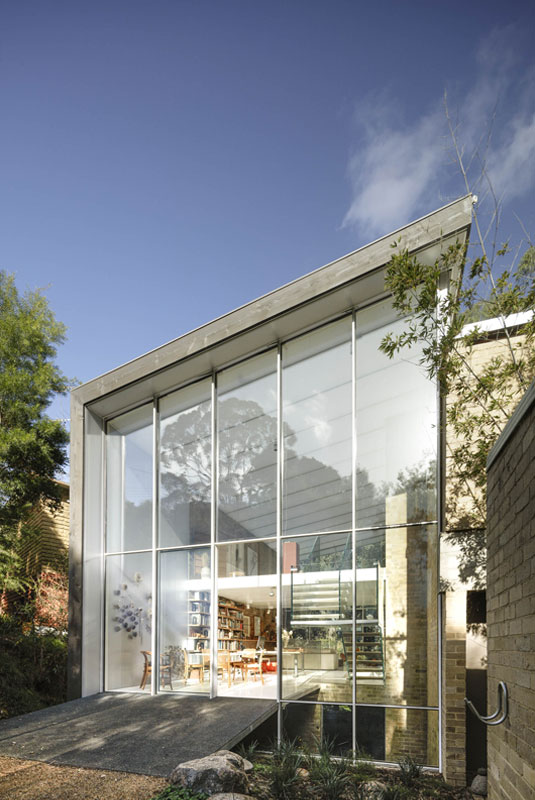
It led them to develop their own, customised climate control system known as HAL, which they have since begun the process of commercialising.
“The project began in parallel with the design of the Studio,” he says. “We wanted to create an active building – one that actively responds to its environment and future conditions.”
Due to the site and climate, the vast majority of HVAC energy is associated with heating the spaces. This led to the renovation being designed to passively capture lots of solar heat through the large window wall on the north-facing façade. The application of external solar control (an automated blind system) is capable of reducing solar gain by an impressive 96 per cent.
“These would only work if they were brought down well ahead of the conditions that would cause overheating, and this would have to happen without user intervention,” Julian explains.
“So, like all good software projects, it rapidly grew in scope to also control the dedicated mechanical ventilation and commercial heat pump system installed as part of the renovation, and then to include a sophisticated comfort model.”
Refined and developed over time, the HAL system bucks the convention of analysing how effectively a system is able to hold conditions within a temperature band. Rather, multiple factors are used to measure comfort, including solar impact, humidity and external temperature.
“Having a dynamic, multi-factor model of comfort allows the system to adapt to better reflect real-world comfort, rather than simply accepting a fixed predicted mean vote band and measuring how much time the temperature is outside that band,” says Julian.
“So the most important measure is how accurately our model is describing real-world user comfort. If our comfort model says people are comfortable when they actually are not, there is an opportunity for us to improve the comfort model for all building and zones.”
Operation of the system therefore differs from day to day – but the one constant is that it is always “looking into the future to inform decisions in the now.”
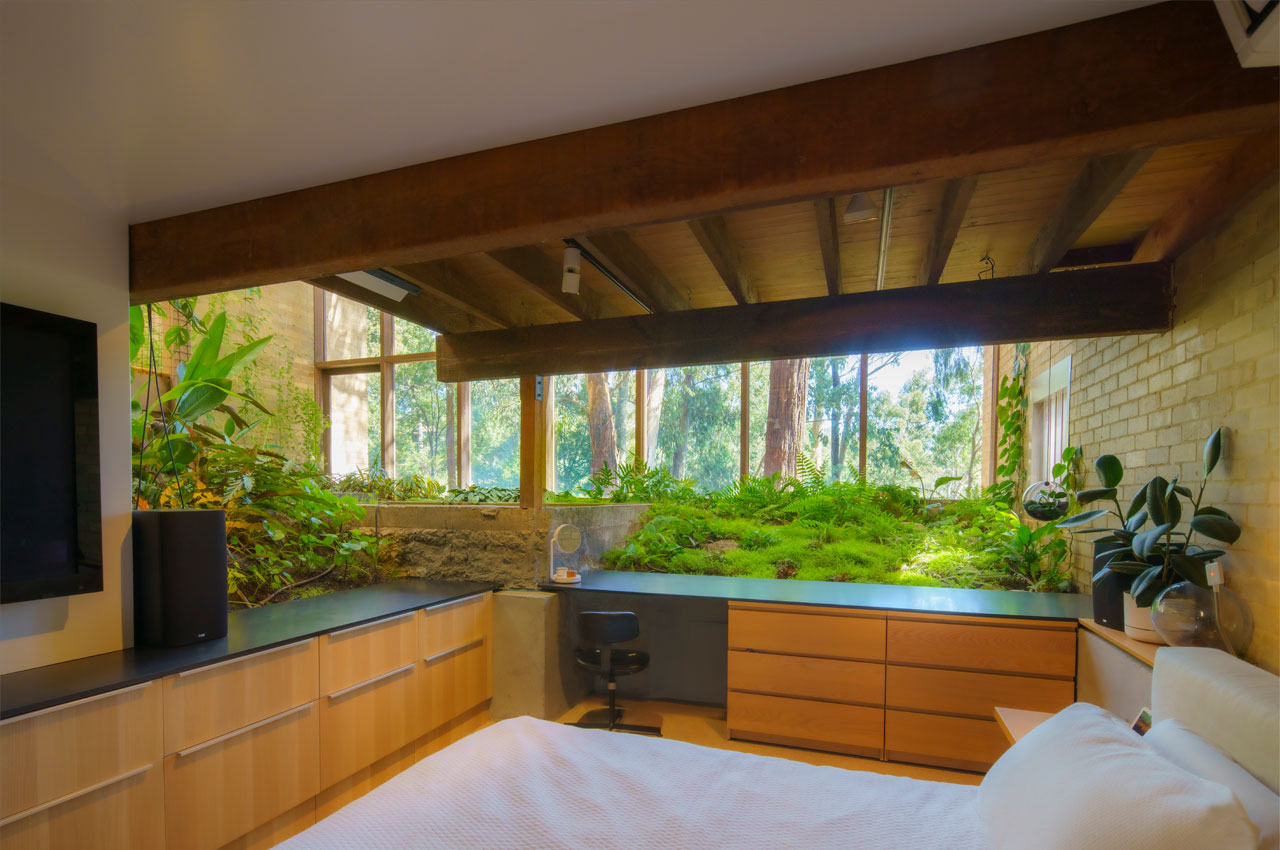
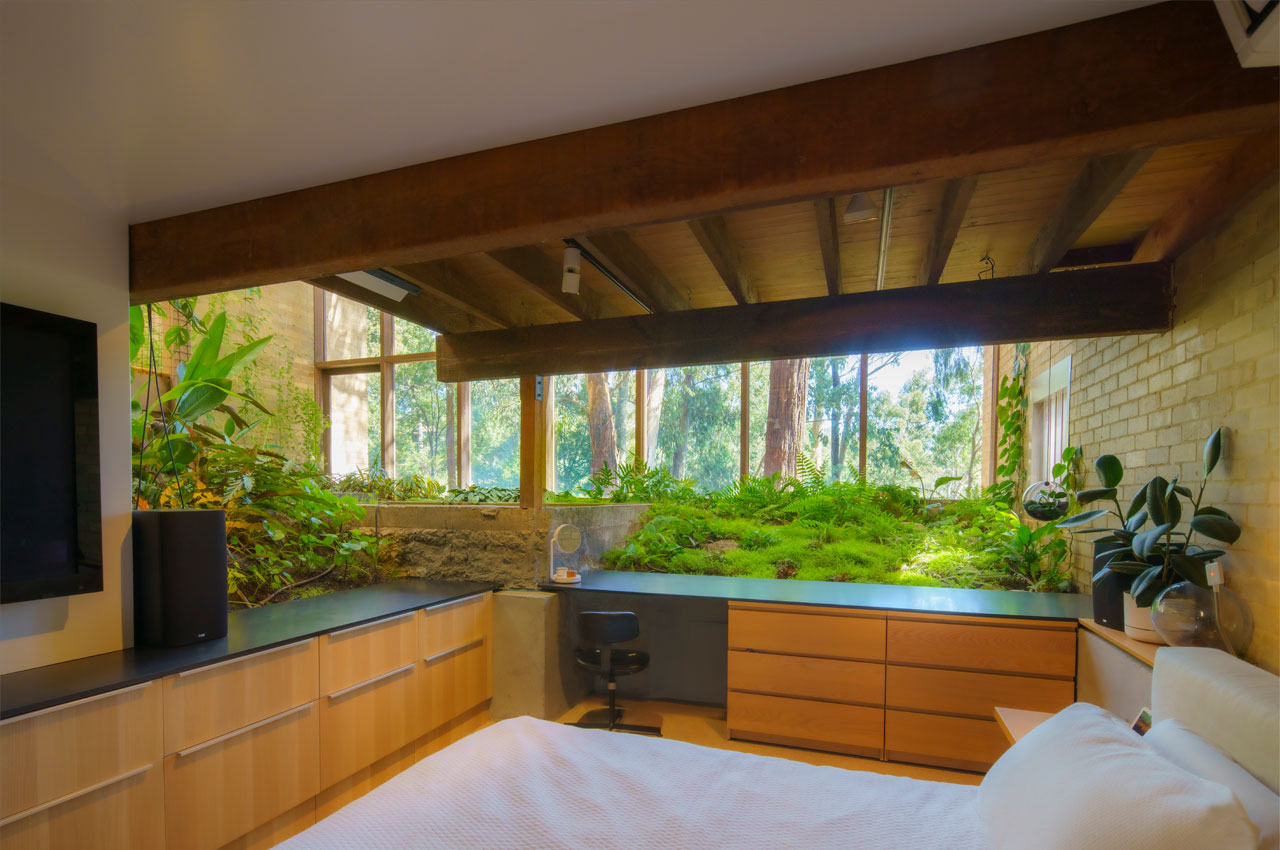
For example, consider if at midday the system monitors the weather forecast for temperature, humidity, sun position, cloud density, building insulation and thermal mass effects. It may determine that the internal temperature will get very close to the cold comfort limit the following morning followed by a hot day where internal conditions will approach the hot comfort limit.
With this knowledge, it will allow afternoon internal temperatures to climb a little higher so that the building will hold just enough heat to minimise heating load in the morning. Once internal temperatures begin to “climb away” from the cold comfort limit, heating is immediately stopped to ensure the building fabric is kept as cool as possible for the hot day known to be coming.
“By contrast, constant set-point strategies fight to get the internal temperature to the set-point,” Julian says, “only for the internal temperature to overshoot and the system then fights in the opposite direction.”
Positive outcomes
As well as transforming Featherston House to better suit the needs and modern lifestyle of their young family, Julian and Vicky have created a living laboratory for their predictive climate control technology.
“It’s been a very interesting process,” says Julian. “While in early development there were many unexpected consequences when all the factors interact into one algorithm, it has since developed into a capable system such that it is very rare for us to interact with it.”
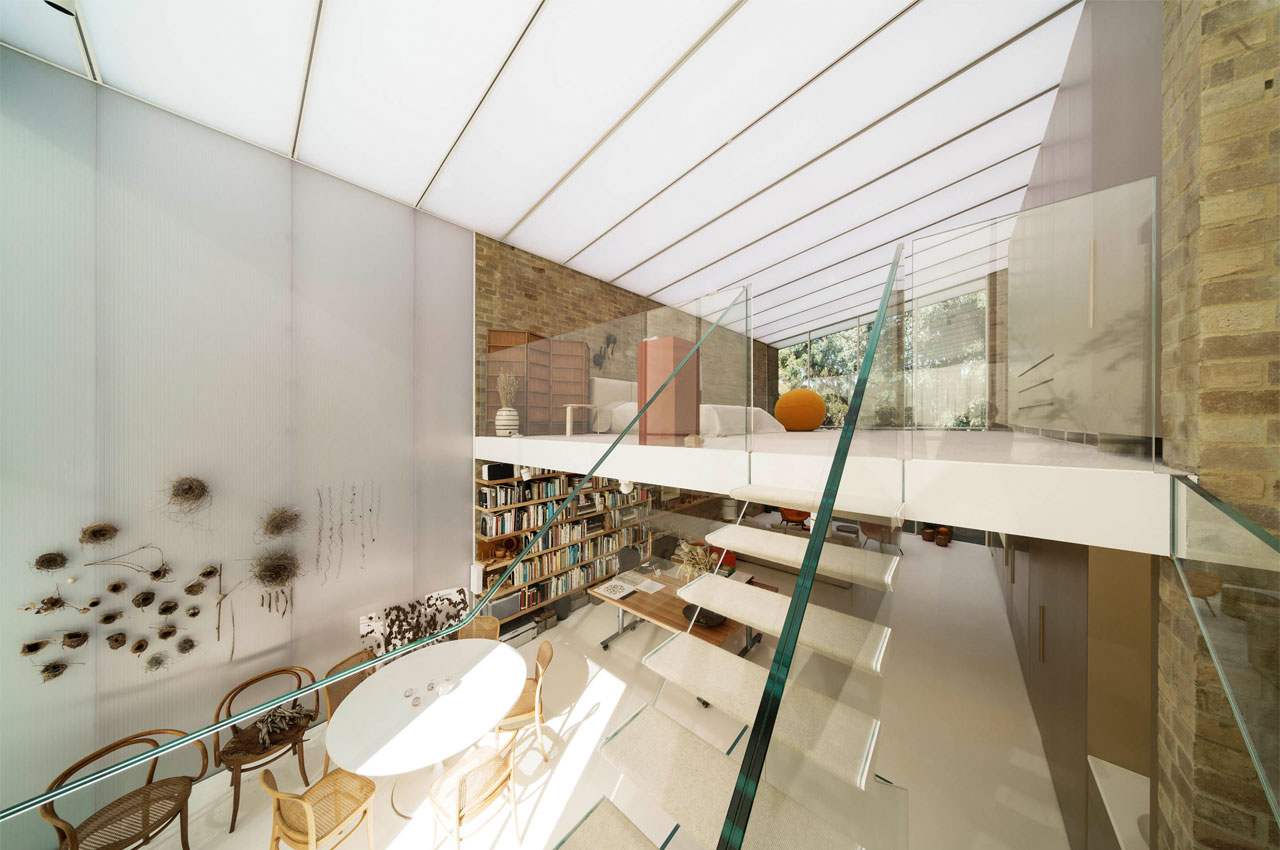
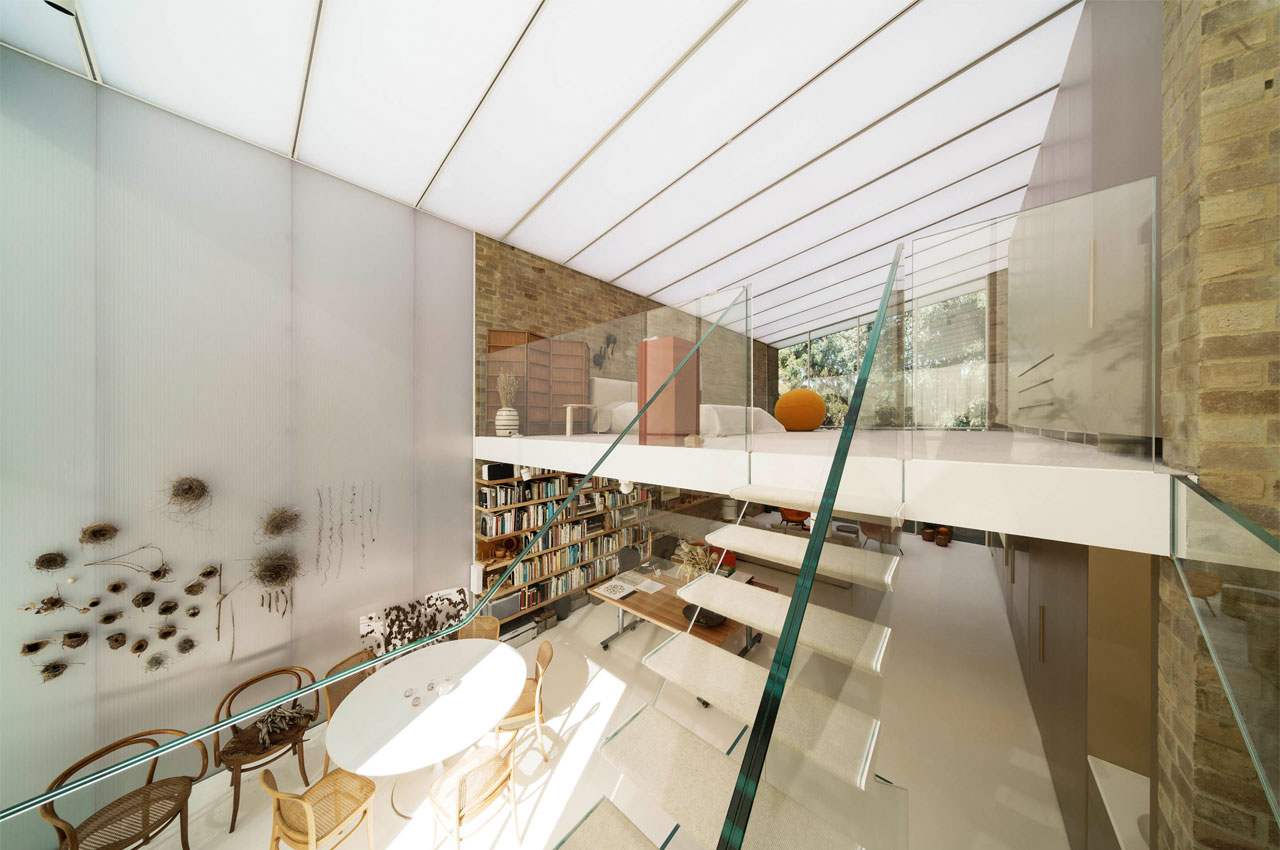
Recorded energy consumption is now lower than when the home had heating only and no cooling. And the family has found that both the house and studio are significantly outperforming the typical energy consumption of comparable buildings.
“It’s not hard to see why,” Julian says. “When you look at historical data, it just makes for much better control decisions.”
Sitting down with Julian Featherston, Affil.AIRAH
Did you have a performance criteria or comfort temperature band in mind when you designed the predictive climate control system?
In relation to the predictive control component of the system, the most important performance indicator is the quality of the decisions it is making in real time. In other words when we look back at the decisions it made, do they appear intelligent and logical, or not?
To achieve this, we need to gather the information required to make accurate predictions – i.e., the cloud forecast – and information about the building zone – i.e., we need to automatically learn how well insulated the zone is. Then finally we need to approximate the characteristics of the equipment servicing the zone – i.e., is it more efficient at half load? These parameters are different in each zone of a building zone, and may vary with season.
Measuring the quality of the decisions allows us to compare alternative control strategies and improve the system. But it is a relative rather than absolute measure, unlike raw power consumption, for example.
However, we know that a quality of decision is directly correlated to whatever absolute measure you are optimising for. Instead of simply reducing total power consumption, you might want to maximise use of renewables, or push your consumption away from peak demand periods.
In relation to the comfort performance metric, we reversed the convention of analysing how well the system was able to hold conditions within a band. We use a multi-factor measure of comfort including solar impact, humidity, external temperature. So, the most important measure is how accurately our model is describing real-world user comfort. If our comfort model says people are comfortable when they actually aren’t, that’s an opportunity for us to improve the comfort model for all building and zones.
What lessons were you able to take from the renovation of Featherston Studio in relation to climate control?
The system was developed to enable the design of the Studio but we really discovered the broad application of it when we deployed the same system in another building that has strong parallels with conventional commercial spaces.
The main building (Featherston House) features large volumes with high solar gains and commercial HVAC equipment. It’s occupied as an office and residence. In this context it also performed very well, and it became obvious that it had huge application in centrally controlled commercial buildings.
What were some of the challenges in refining the system for Featherston House given the home’s unique layout and design?
The biggest challenge was the complexity of marrying all the competing factors in a way that leads to elegant decisions. For example, a strictly logical model can generate a lot of “bouncing” such as blinds going up and down frequently. This calls for improvements to the prediction engine to catch subtleties in the behaviour.
So the really difficult stuff is not the basic functionality, it’s getting all the basic elements to come together into a single strategy that really delivers on the human experience side, not just the efficiency side.
This approach moves away from the idea of several “strategies” that you might turn on and off – i.e., optimised start/stop – towards a model of one single strategy that considers as many factors as possible all the time.
How have you optimised the various HVAC systems to reduce energy?
We plan for the best mix of devices depending on what we are optimising for. You can think of it as cascading from low consumption devices to higher ones. However, it’s possible that we might run the heat pumps before the blinds or ventilation because we might be in a rare period of negative electricity cost and high percentage of renewables in the grid or locally. One might push the building in a direction that will be beneficial later. This kind of arbitrage is only possible if you have foresight and therefore know which direction to push.
You are now developing the predictive climate control system designed for Featherston House for commercial building applications under HAL Systems. How is that process going?
The idea of predictive control applied to HVAC has been well researched and proven for many years. The difficulty lies in creating a viable commercial control system and business model.
We are on the road to developing our prototype into an elegant light-touch solution for commercial buildings. We would encourage readers with an interest to reach out to us; we’d love to meet more industry members with an interest in predictive real-time control.
To contact Julian Featherston directly, go to halsystems.com.au/contact
Project at a glance
The personnel
Client: Featherston family
Controls consultant: HAL Systems
Design consultant: Two Feathers
The equipment
Destratification fans: Haiku DC Fans
Controls: HAL Systems
External blinds: Custom ZipTrack
External blinds motor: Selve
Field controllers: HAL, Advantech ADAM, CoolMasterNET Bridge and custom i2C units
Metering: Custom CT-based sensors
Sensors: Siemens
VRV heat pumps: Mitsubishi Electric
(Source: Two Feathers, HAL Systems)
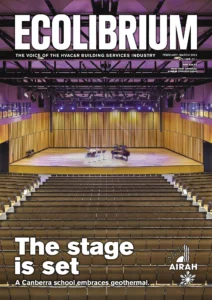
This article appears in Ecolibrium’s February-March 2023 edition
View the archive of previous editions
Latest edition
See everything from the latest edition of Ecolibrium, AIRAH’s official journal.