Goal oriented
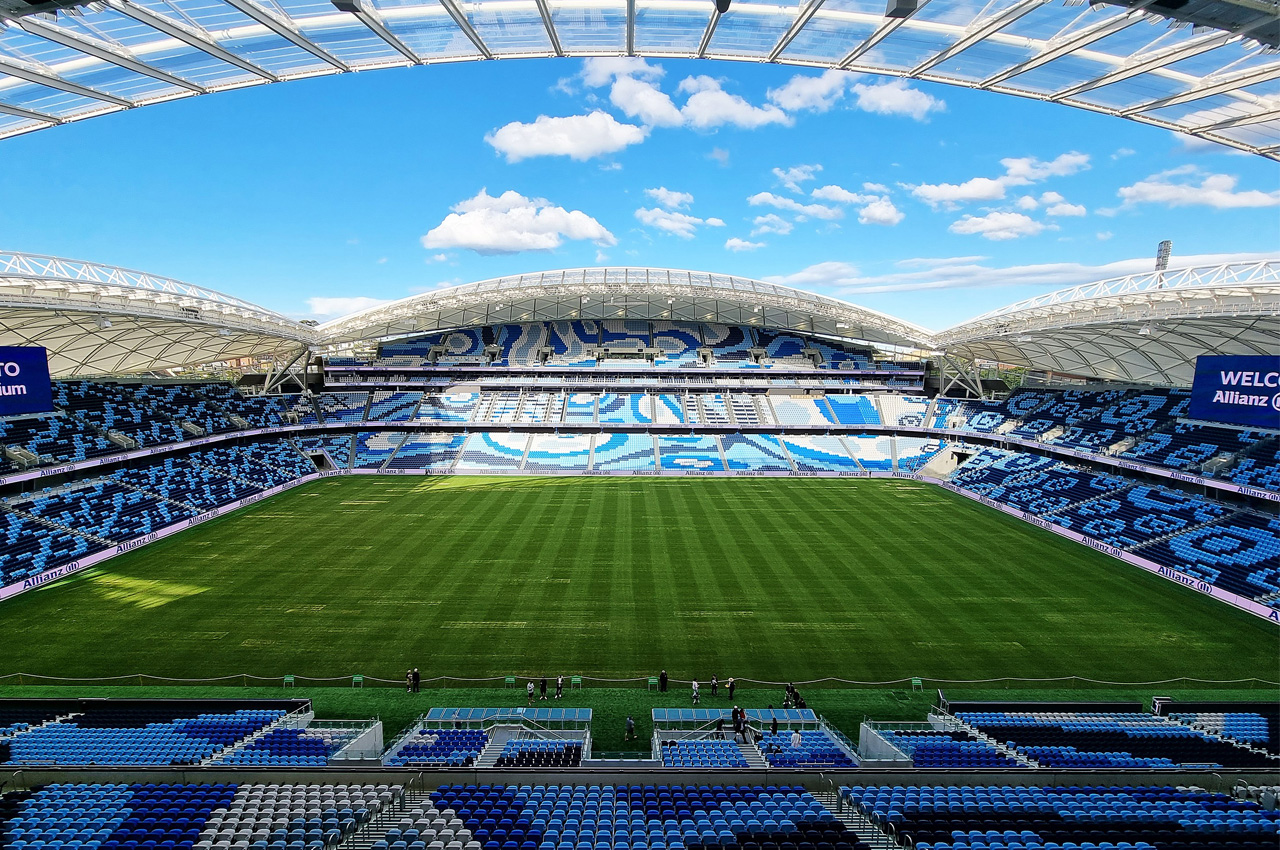
Since 1988 the Sydney Football Stadium has been the Harbour City’s premier rectangular field venue, regularly hosting internationals played by the Kangaroos, the Wallabies, Socceroos and Matildas as well as NRL, Super Rugby and A-League games. Find out how the design team had particular sustainability aspirations at heart.
Located at Moore Park, adjacent to the Sydney Cricket Ground (SCG), the original Sydney Football Stadium was built upon the former site of the Sydney Sports Ground and officially opened in January 1988.
Numerous expansions over time saw its seating capacity lifted from a little over 41,000 at opening to around 43,000 prior to numerous NSW state governments pledging to redevelop the stadium.
In 2019, aging infrastructure and poor spectator amenity led the Berejiklian NSW government to confirm plans for its demolition, with a new world-class venue to be built in its place.
A design competition was held to determine the architects for the project. Ultimately, a COX Architecture design was selected that “enhances the significant recreation and sports precinct of Moore Park”. The design built upon the legacy of the original stadium.
“More community value, more experience for teams and fans, and with better connection to surrounding parkland and amenity,” says COX director, Patrick Ness.
“It is something that is simultaneously sculptural and highly functional. It is lighter, kinder to the environment and more self-sufficient as a structure than any other major stadium in Australia.”
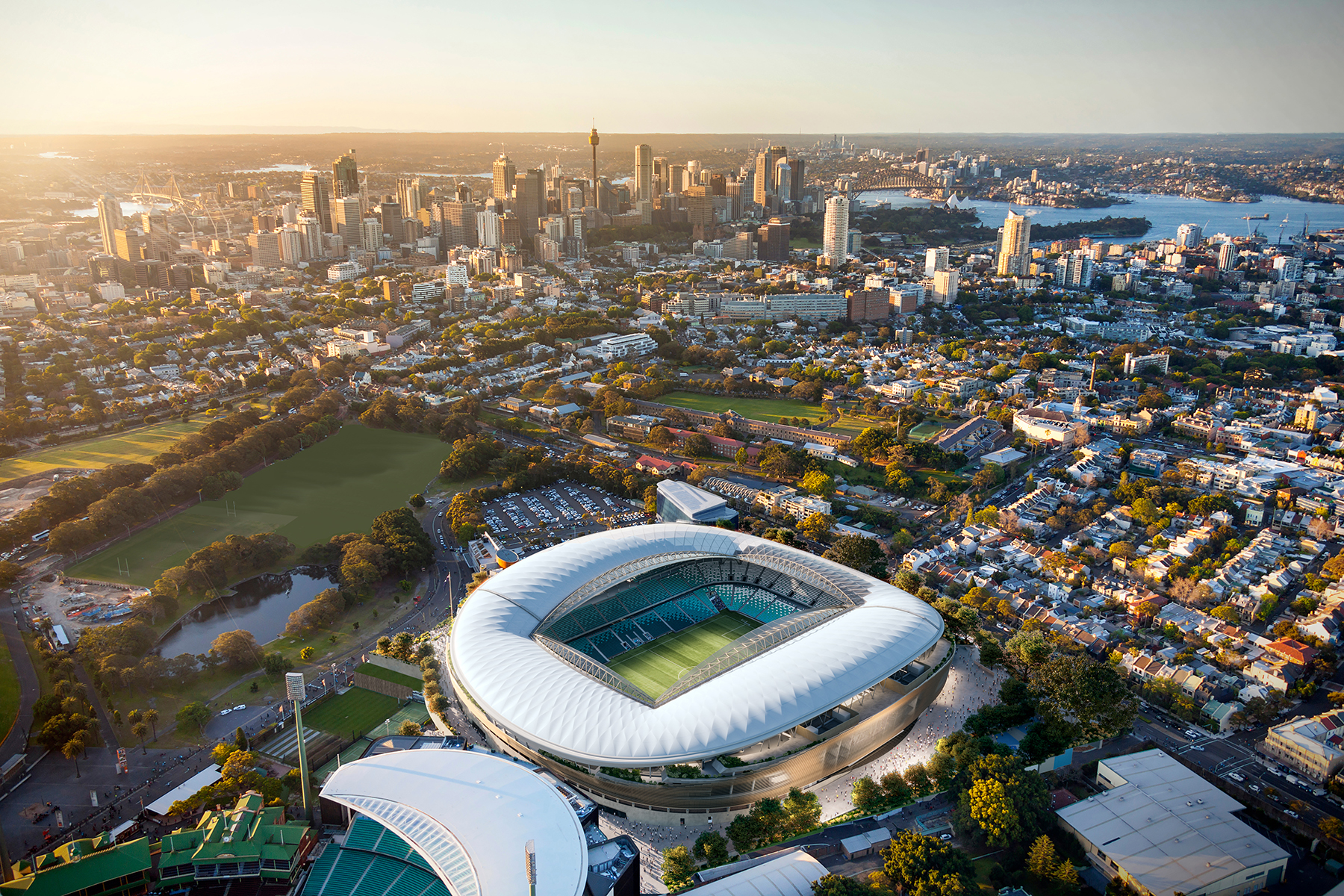
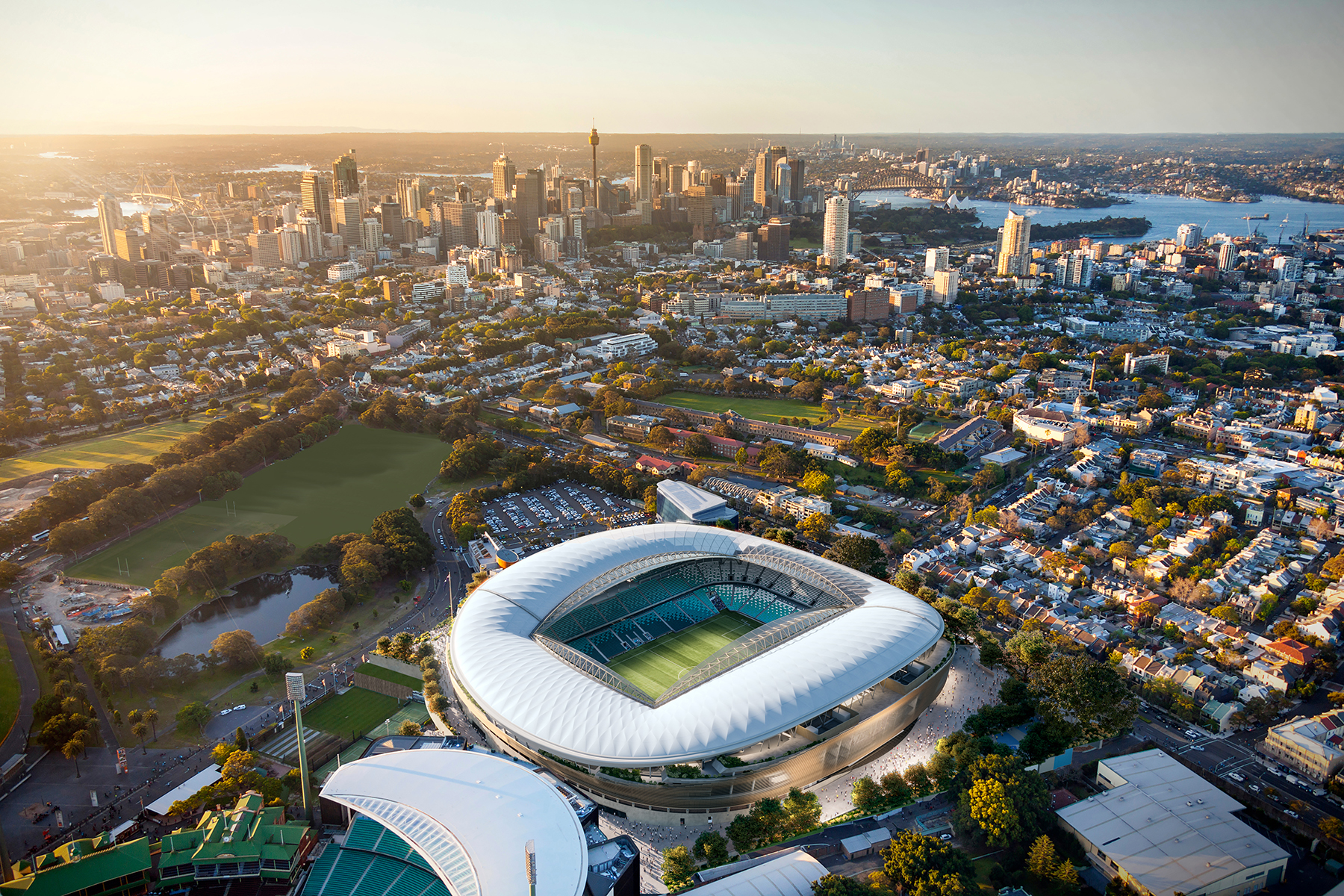
A key component of COX’s design is the dynamic roof structure. This uses 40 per cent less steel in its construction than normal stadium roofs while providing weather protection to all spectator seating. Importantly, the clever design works to contain noise in the precinct.
The façade, which COX describes as an “environmentally responsive skin”, enhances patrons’ sense of connection to place, and shields internal areas of the stadium while allowing it to blend into the surrounding parklands.
“This environmentally aware approach to design is at the heart of the project, designed to achieve LEED (Leadership in Energy and Environmental Design) Gold rating,” Ness says.
With a designed seating capacity of 42,500, the new stadium redefines the game-day experience for both teams and fans.
The arrangement of its tiered stands provides enhanced views of the playing field for spectators while creating a sea of faces for those on field.
The arrangement of its tiered stands provides enhanced views of the playing field for spectators while creating a sea of faces for those on field.
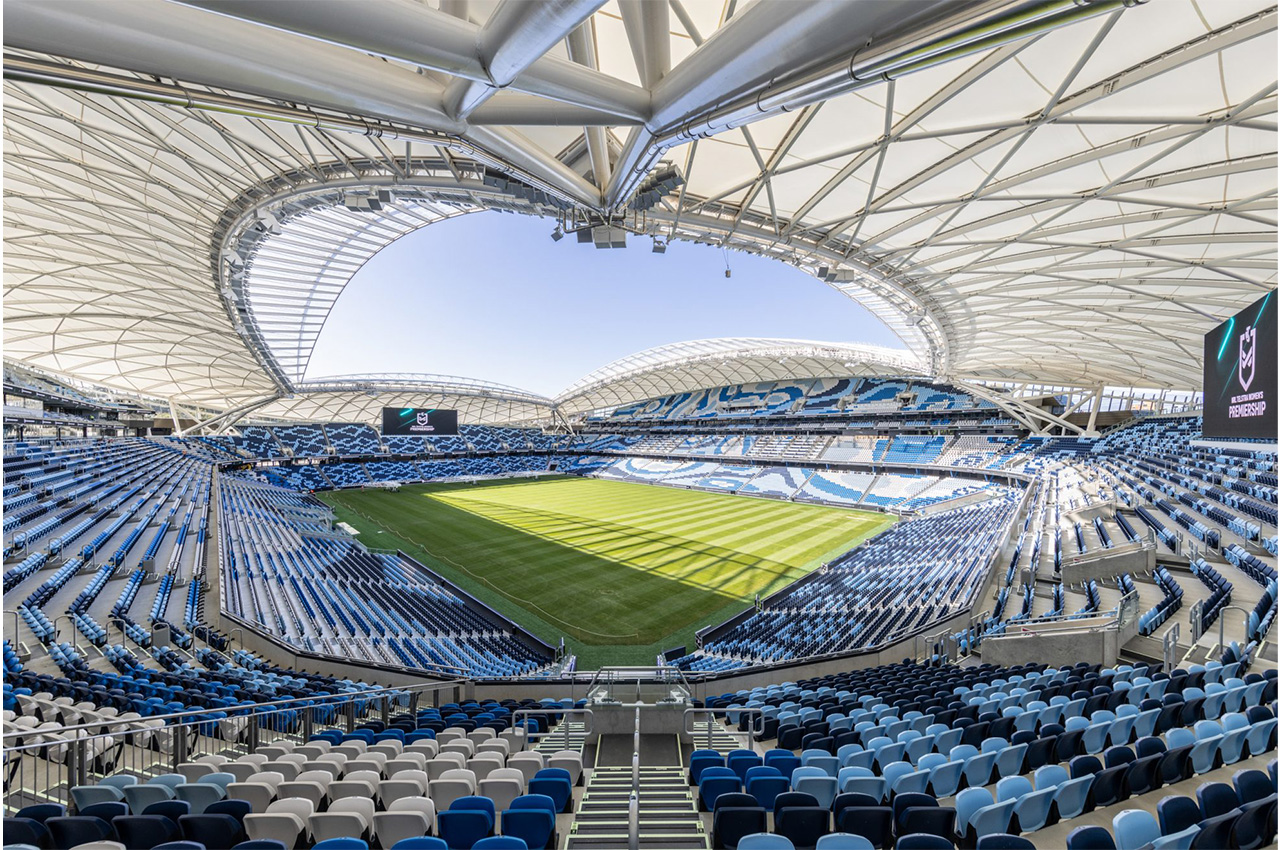
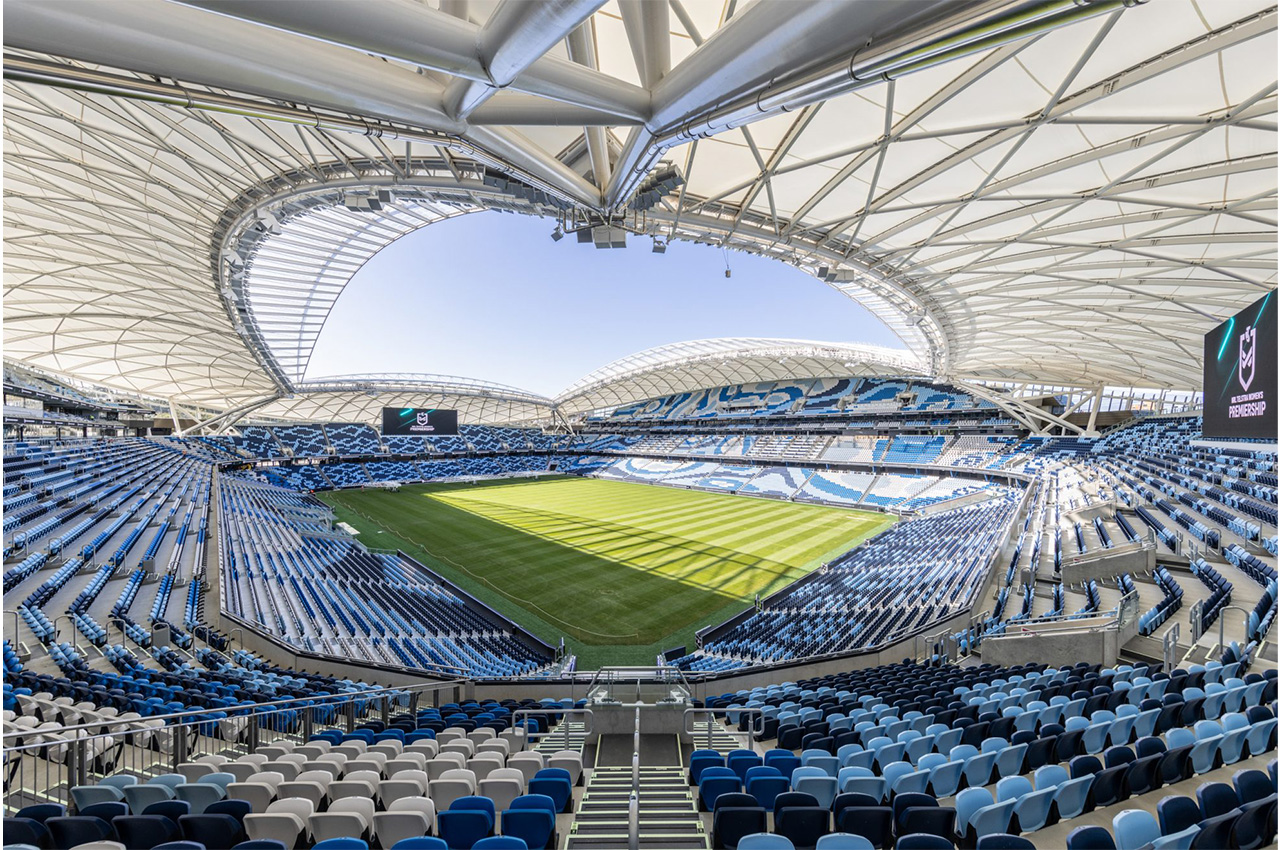
An increased number of amenities include clear wayfinding and easy circulation around the ground, the provision of more than 48 food and beverage outlets, and improved media and broadcast facilities.
Two worlds colliding
One of the more striking features of the new stadium is the artwork displayed across the seating pattern, titled “Two Worlds Colliding – Water and Land”.
Designed by award-winning Indigenous artist Tony Albert, the design was chosen for the story it tells about place and country.
It also provides a nod to the two competing teams, with each end of the stadium separated and distinguished by two different designs – the land through geometric diamond designs taken from nature and the bubble of concentric circles depicting the water.
Early engagement
Following the former stadium’s demolition and commencement of ground-piling works in 2019, managing contractor John Holland was awarded the contract to deliver the new stadium in March 2020.
Engaged by John Holland as the first contractor on the project during the “early contractor involvement” (ECI) period, A.G. Coombs was commissioned to deliver all mechanical services for the stadium under a design and construct (D&C) contract.
A.G. Coombs also performed the role of lead services and building information modelling (BIM) coordinator.
“Being one of the most influential stakeholders on the project, it was important to get in early and confirm all our plant and riser spatial requirements – not just for our services reticulation but also to ensure they met minimum clearances for performance, access and to maximise prefabrication opportunities,” says A.G. Coombs senior design engineer Ryu-Jin Lee.
By modelling mechanical services early, Lee says the architects and structural engineers were able to accommodate these requirements upfront, rather than having to evaluate later. Mechanical services design is frequently designed later in the design process.
“Involvement in the ECI stage also provided the opportunity to clarify some of the project brief requirements with the client upfront, and provide value engineering options.”
One of the options presented was to remove the general kitchen exhaust system in lieu of condensate recovery dishwashers. This not only saves the stadium energy but also reduces plant and operational costs.
Off-site prefabrication was also able to be maximised, including the prefabrication of risers, pump skids, valve sets and fan coil unit (FCU) modules. This addressed the majority of risks as identified during A.G. Coombs’ Safety in Design workshops.
“The benefits of this prefabrication strategy were further realised when the COVID-19 pandemic hit in March 2020, and onsite labour was significantly reduced,” adds Lee.
Significant work was also undertaken during the project’s detailed design phase to refine mechanical services systems and solutions, particularly in light of the LEED Gold certification target.
The benefits of this prefabrication strategy were further realised when the COVID-19 pandemic hit in March 2020, and onsite labour was significantly reduced.
Designed to perform
The mechanical services design of the new Sydney Football Stadium features natural ventilation whenever possible while meeting the performance criteria as specified in the project brief.
“From the brief it was clear that we would have to validate our design via modelling – through CFD (computational fluid dynamics) and wind studies – to ensure comfort conditions were met and that we were achieving the best outcome for a project of this nature,” says Lee.
Highlighting the global collaboration of stakeholders on the project, this modelling was carried out by overseas engineering firms. Future Facilities from the UK completed CFD modelling, while German firm Wacker Ingenieure completed wind modelling.
A.G. Coombs’ final mechanical services design sees a combination of FCUs and variable air volume (VAV) terminal units used to provide localised temperature control and zoning to the stadium’s interior corporate hospitality spaces.
These spaces, as well as other interior spaces requiring temperature control, are served by three air-cooled chillers that provide a combined cooling load of 4,300kW. Three condensing hot water generators provide a combined heating load of 3,200kW.
The control strategy implemented, and the arrangement of the chillers and central energy plant, reflect the variation in load that these systems experience as a consequence of the stadium’s event scheduling and non-event days.
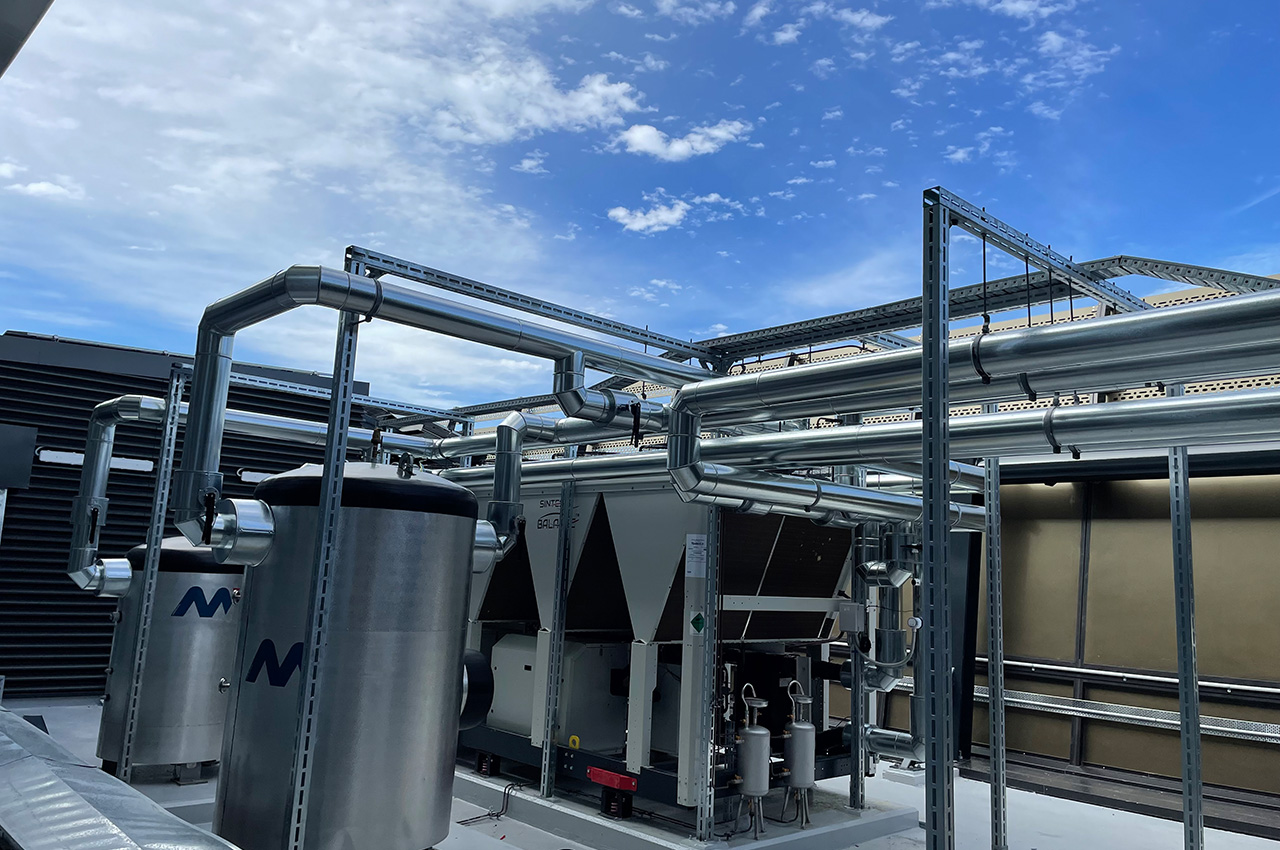
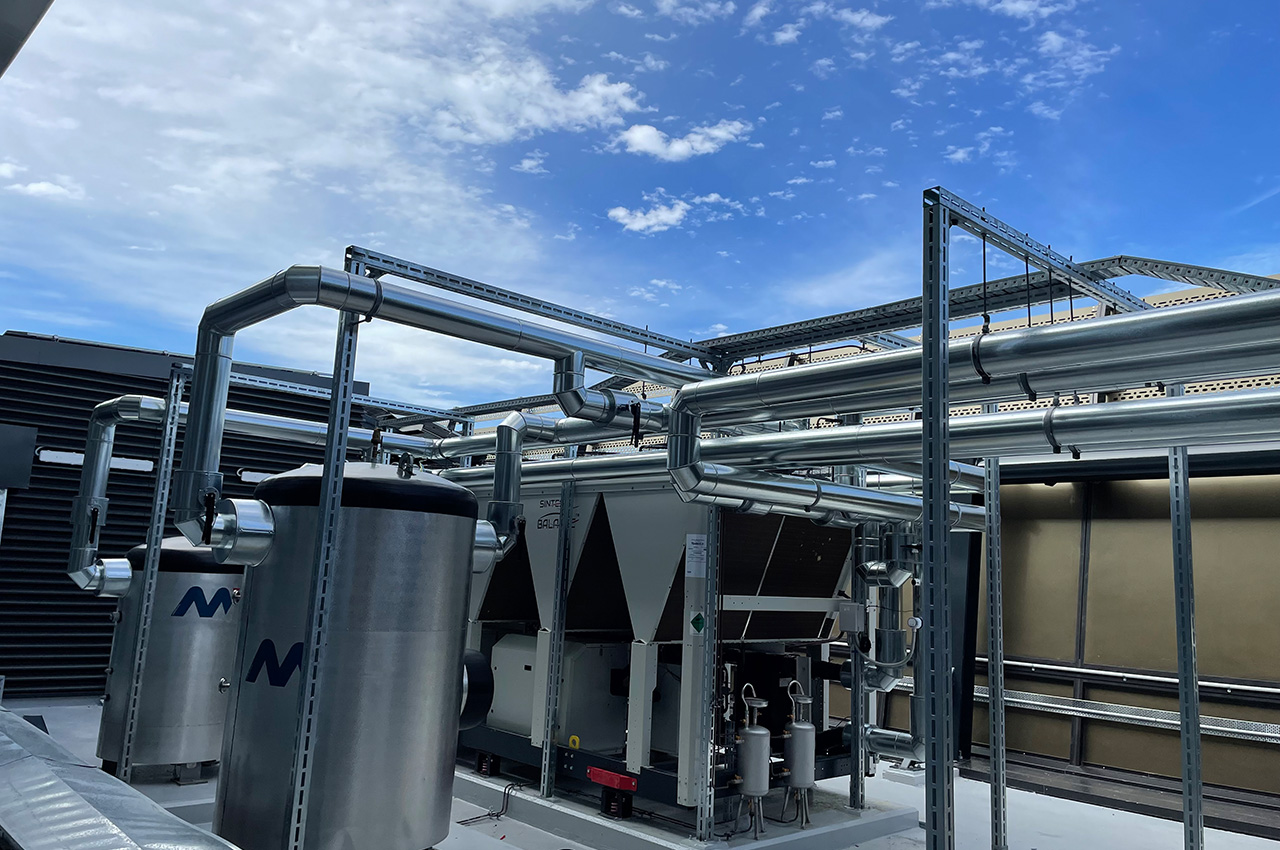
According to Lee, the design had to take into account system performance during non-event days in winter, outside business hours to that of a major event.
Consequently, as part of the design approval process the performance of the chilled water system was reviewed against the load profile of the building throughout the year.
“Thermal simulations were undertaken by the mechanical services consultant LCI, which detailed the load steps throughout the year,” says Lee. “These simulations determined that the stadium would mainly operate at 10 to 25 per cent of the calculated peak load.”
From this data, A.G. Coombs was able to select and present to project stakeholders, through a whole-of-life analysis, that a chilled water system would achieve the best outcome when reviewed against life cycle, maintenance and operational cost.
The design of the resulting central energy plant, and use of air-cooled chillers, also eliminated the need for cooling towers for heat rejection and contributed to the project’s water saving initiatives.
Insane membrane
The new Sydney Football Stadium features a 26,000m² tensile membrane roof, made up of 48 massive white PTFE (polytetrafluoroethylene) fabric panels.
According to roof manufacturer, MakMax Australia, the largest panels are 14.5m wide and more than 40m long with each panel fixed to the steel roof trusses and support beam using high-strength aluminium tensioning hardware.
The inner ring of the roof is covered with 3,500m² of clear, ultra-lightweight EFTE (ethylene tetrafluoroethylene) panel sections. Offering 90 per cent light transmission, this is designed to allow sunlight penetrate onto the grass playing surface to promote natural turf growth while still providing weather protection for fans.
A further 900m² of vertical PFTE panels have been installed to interface at various points in the roof where the clear EFTE sections overlap the white PTFE sections.
Prefabrication maximised
According to A.G. Coombs, maximising prefabrication became a key element in successfully delivering the project on time.
“As well as implementing prefabrication on our pump skids, duct and pipe risers and FCUs – all as is typical on A.G. Coombs projects – we also prefabricated smaller elements off site that had just as much impact on reducing our on-site labour,” says Lee.
This included the assembly of FCU valve sets, which were off-set ready for connection via flexible hose to the FCUs on site. Valve sets for the AHUs were piped internally in the factory, also freeing up valuable plant space in an otherwise congested plant room.
Event integration
Since the new stadium’s completion, A.G. Coombs has overseen the service and maintenance of the mechanical services at the stadium during the defect liability period (DLP).
Additionally, A.G. Coombs Advisory has successfully developed a simple, non-typical integration system between Venues NSW’s event management software and the new stadium’s building management control system (BMCS) using a middleware solution.
“This is a frequently specified requirement that is often overlooked due to its difficulty,” says A.G. Coombs Advisory building technologies leader Michael Sue.
Sue says that many venues require venue staff to ask their facilities management (FM) team to specifically program services such as HVAC plant to operate during each event.
“A typical stadium requires services to be staged, with the facilities and kitchen hours beginning well before patron areas,” he says.
“The required scheduling of services becomes somewhat complex, as the operator schedules each area under a separate time schedule specific to each event. Then once the event is completed, the operator is required to return the operation of services to normal.”
A.G. Coombs’ integration solution solves many of these challenges for Venues NSW, their staff and their operators by creating a secure, automated connection between venue operations booking system and the BMCS.
Other advantages include:
- Energy savings because different plant functions are automatically staged to start and stop only as required
- Time savings at the operational level
- Minimisation of human error
- Automatic individual zone control of all HVAC plant based on the event booking system inputs
Plant acoustics
The layout of the main plantroom on Level 5 evolved several times during the design process.
Originally, it was designed to have a single path of egress on the façade side and mainly catered for the mechanical services plant. However, as the design progressed, Level 5 had to be completely redesigned to accommodate the electrical infrastructure, including transformers and switch rooms, which had originally been planned for a basement location.
“This infrastructure obviously takes up a lot of real estate, which added to the challenges of ensuring adequate attenuation to our plant located directly under the top-tier seating,” says Lee.
The positioning of discharge duct and generator flues also posed a challenge, as their location was required to be out of public view. The aforementioned wind modelling was also required to validate that the discharge location did not pose any problem to the spectator experience.
To ensure the effective acoustic treatment of the externally located chiller plant on Level 5, A.G. Coombs applied its experience from the previous construction of the Western Sydney Stadium at Parramatta.
“From our experience at Parramatta, we knew the noise generated from the chillers had to be addressed early on,” says Lee.
“Not only were the acceptable noise limits critical for the top tier seated spectator experience, but it was also critical outside, around the public areas.”
The use of acoustic attenuators located off the top of the chillers was discounted, because they created structural challenges and impeded future plant replacement.
Rather, A.G. Coombs engaged with the acoustic consultant, Acoustic Logic, to develop an acoustic screen. The brief called for a screen that not only attenuated the noise but, because it was exposed to view, had to be aesthetically acceptable.
The design of this screen offered the advantage of supporting the installation of a solar PV array, especially given the case that available real estate on the stadium was scarce.
“Positioning our chillers relative to the screen was critical also,” Lee says, “Because it impacted on air-flow performance.”
A.G. Coombs also worked with its suppliers to ensure the quietest chillers fit-for-purpose were able to be sourced. The compressors were acoustically wrapped in the factory before being delivered and installed onsite.
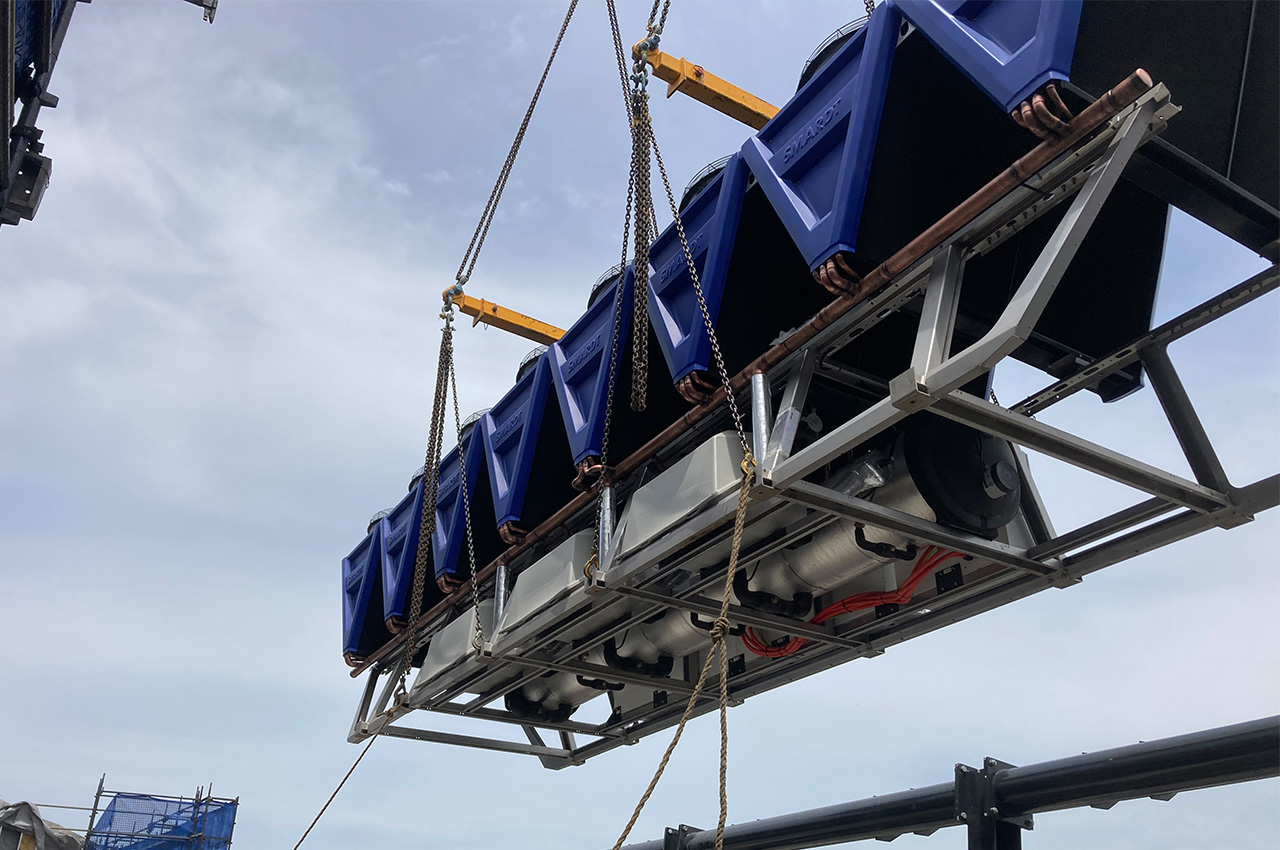
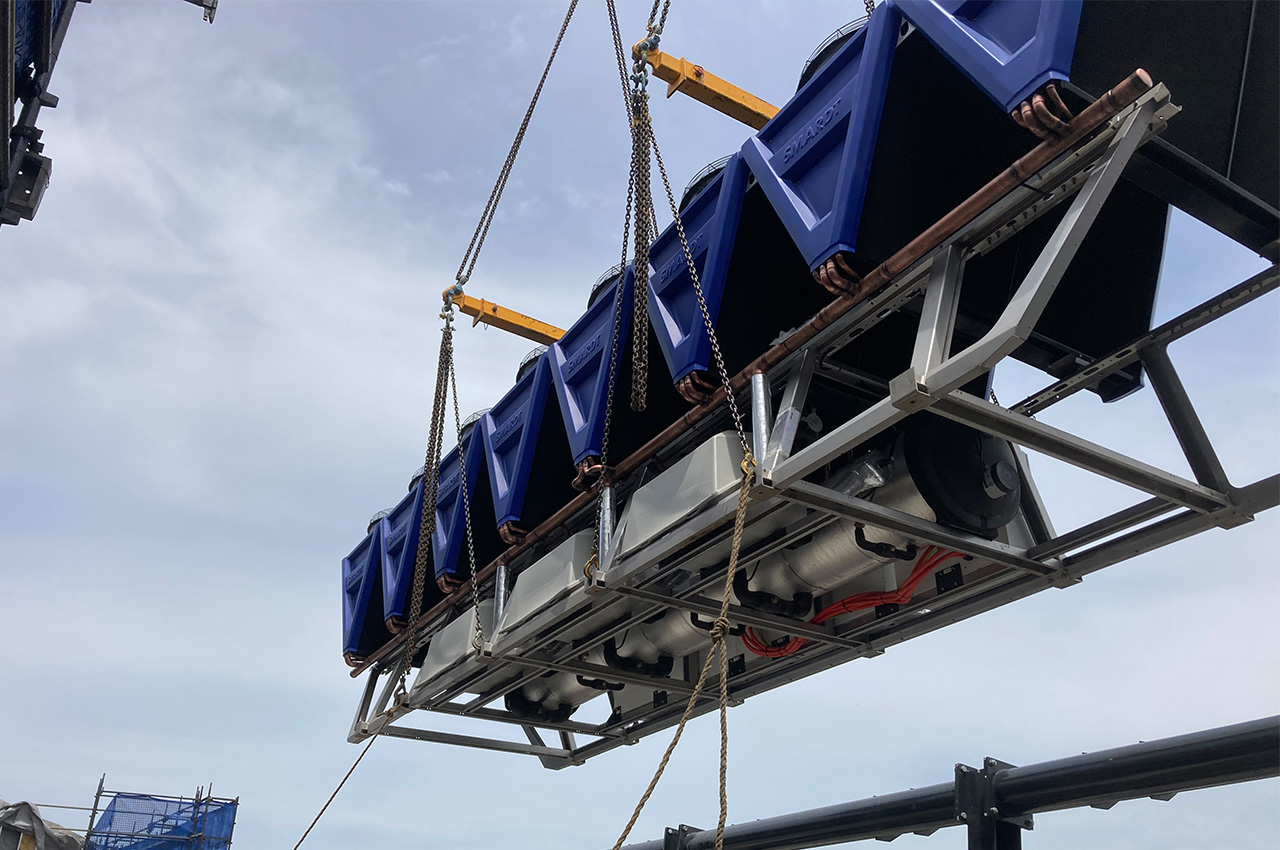
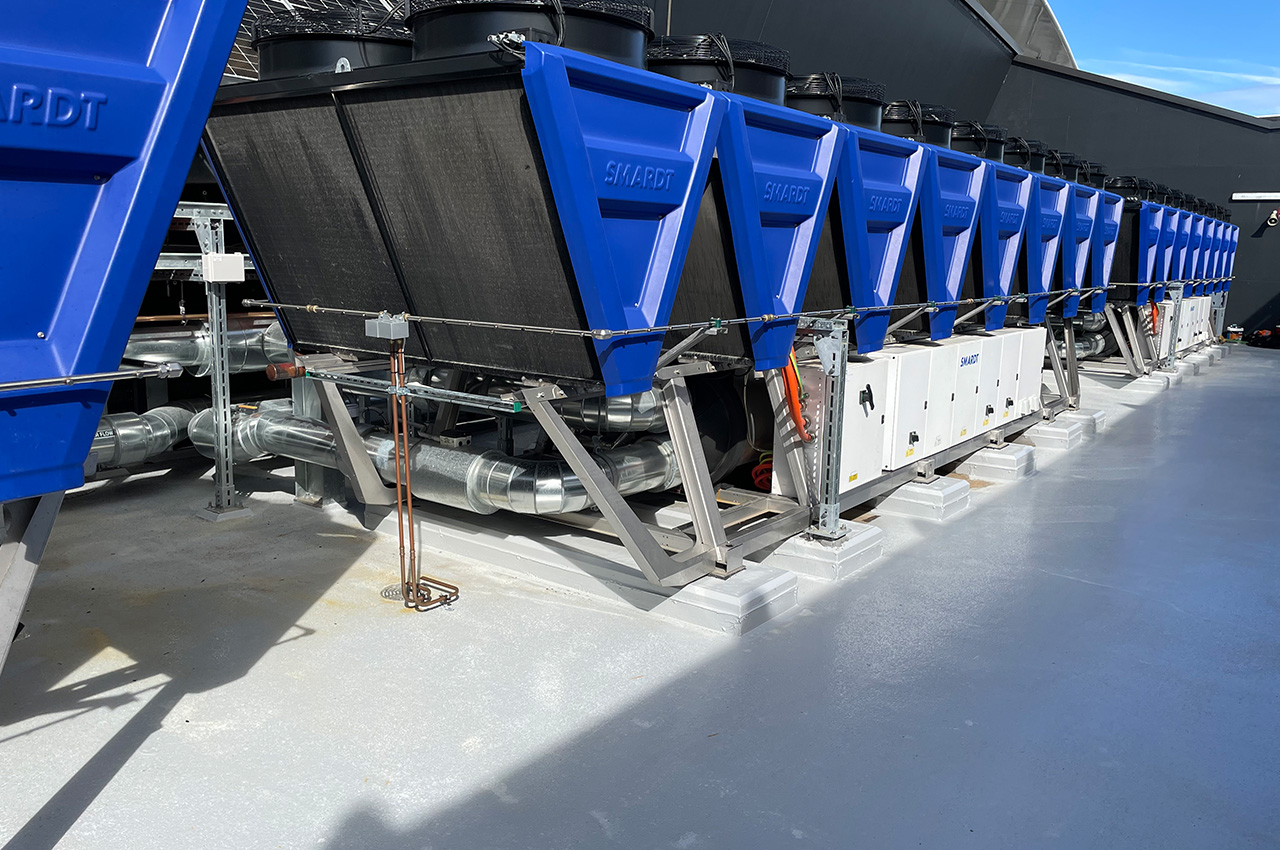
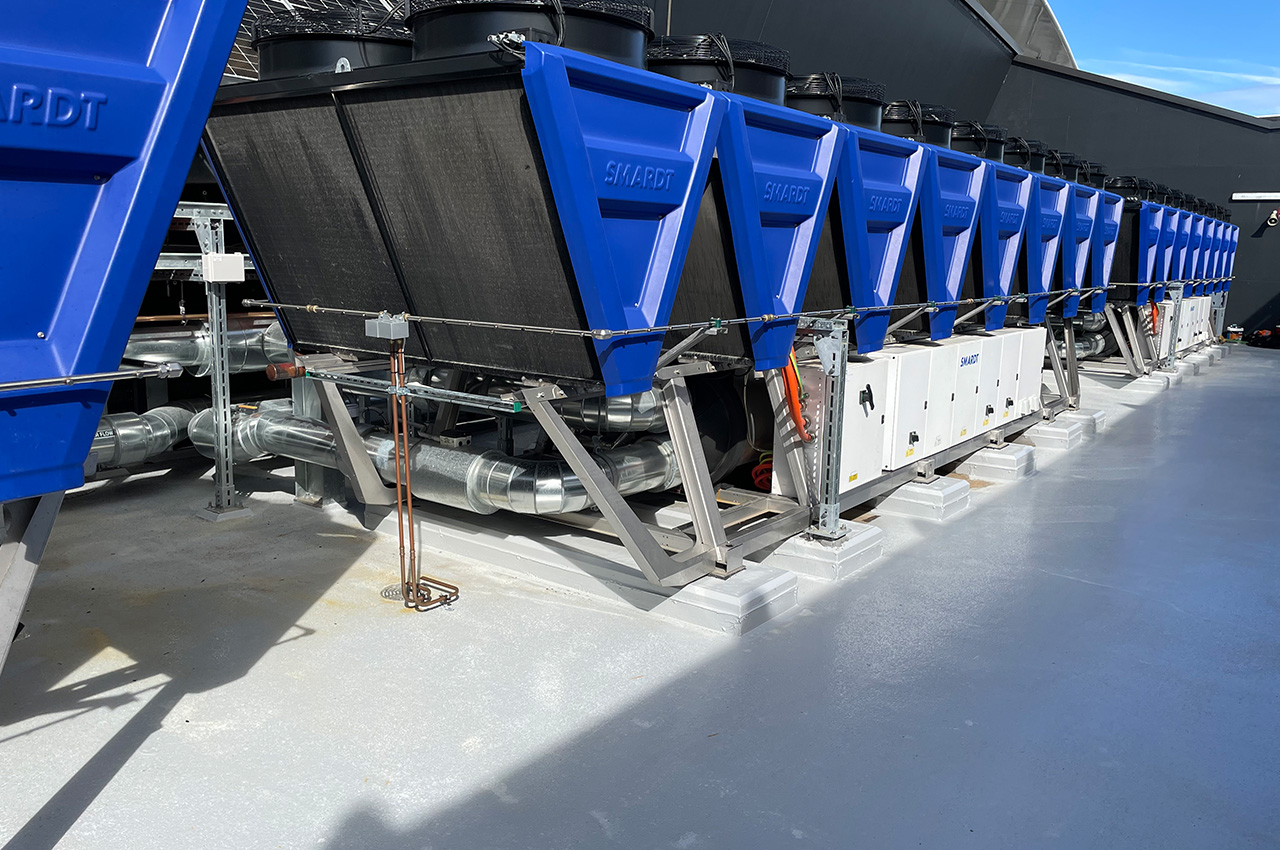
Ready for kick-off
Practical completion of the new Sydney Football Stadium was reached in August 2022 ahead of the stadium’s official opening on August 28, which featured a free community open day and night concert.
The stadium’s first sporting event was held a few days later on September 2, when the stadium’s NRL tenants, the Sydney Roosters, hosted the South Sydney Rabbitohs in front of 41,906 fans.
A day later, the stadium hosted game three of the Rugby Championship Test Series between the Wallabies and South Africa, followed by an international friendly between the Matildas and Canada that rounded out a festival of the codes.
Since then, the venue has hosted multiple A-League, NRL and Super Rugby matches, as well a number of major concert events.
The new Sydney Football Stadium will be a centrepiece venue for the coming FIFA Women’s World Cup 2023 – hosting six matches including an important Round of 16 match in August.
Stadium insights
Stadium Insights
- The construction of the Sydney Football Stadium included:
- 980 curtain wall bronze-coloured panels that surround the external façade.
- 42,500 seats being installed (all undercover)
- 40,000m³ of concrete poured (the equivalent of 16 Olympic swimming pools)
- 90,000m² of concrete slab poured (the size of about 11 football fields)
- Almost 1,500 piles drilled into the ground to support the structure
- Approximately 25km of electrical cable laid
- 10,500m² of “ready to play” turf laid
- 4,000 pieces of steel in the roof, lifted into place by six tower cranes and three crawler cranes
- 325 precast concrete panels surround the stadium at the base, totalling 773.5m in length and 1560 tonnes in weight
Improved amenity
The new Sydney Football Stadium has been designed with fan experience at heart, offering spectators an improved experience on game days with enhancements to amenity, safety and accessibility.
Old stadium | New stadium | |
Female toilets | 113 | 670 |
Male toilets | 291 | 570 |
Universal access toilets | 4 | 49 |
Total seating capacity | 43,100 | 42,500 |
Universal access seating | 14 | Approximately 747 (including companion and easy access seats) |
Dripline coverage | 55 per cent | 100 per cent |
Project at a glance
The personnel
Acoustics consultant: Acoustic Logic
Architect: COX
Client: Infrastructure NSW/Venues NSW
Managing contractor: John Holland
Mechanical services consultant: LCI
Mechanical services design and construct: A.G. Coombs Projects and Advisory
Structural and civil engineer: Aurecon
The equipment
AHUs: GJ Walker
Chillerss: Smardt
Fans: Fantech
FCUs: Temperzone, G.J. Walker, Euroclima
Grilles: Ideal Air
Kitchen exhaust treatment: Camfil
Pumps: Masterflow
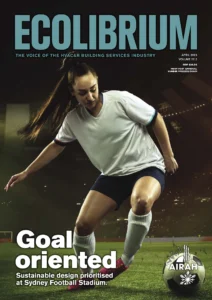
This article appears in Ecolibrium’s April 2023 edition
View the archive of previous editions
Latest edition
See everything from the latest edition of Ecolibrium, AIRAH’s official journal.