Telling the whole story
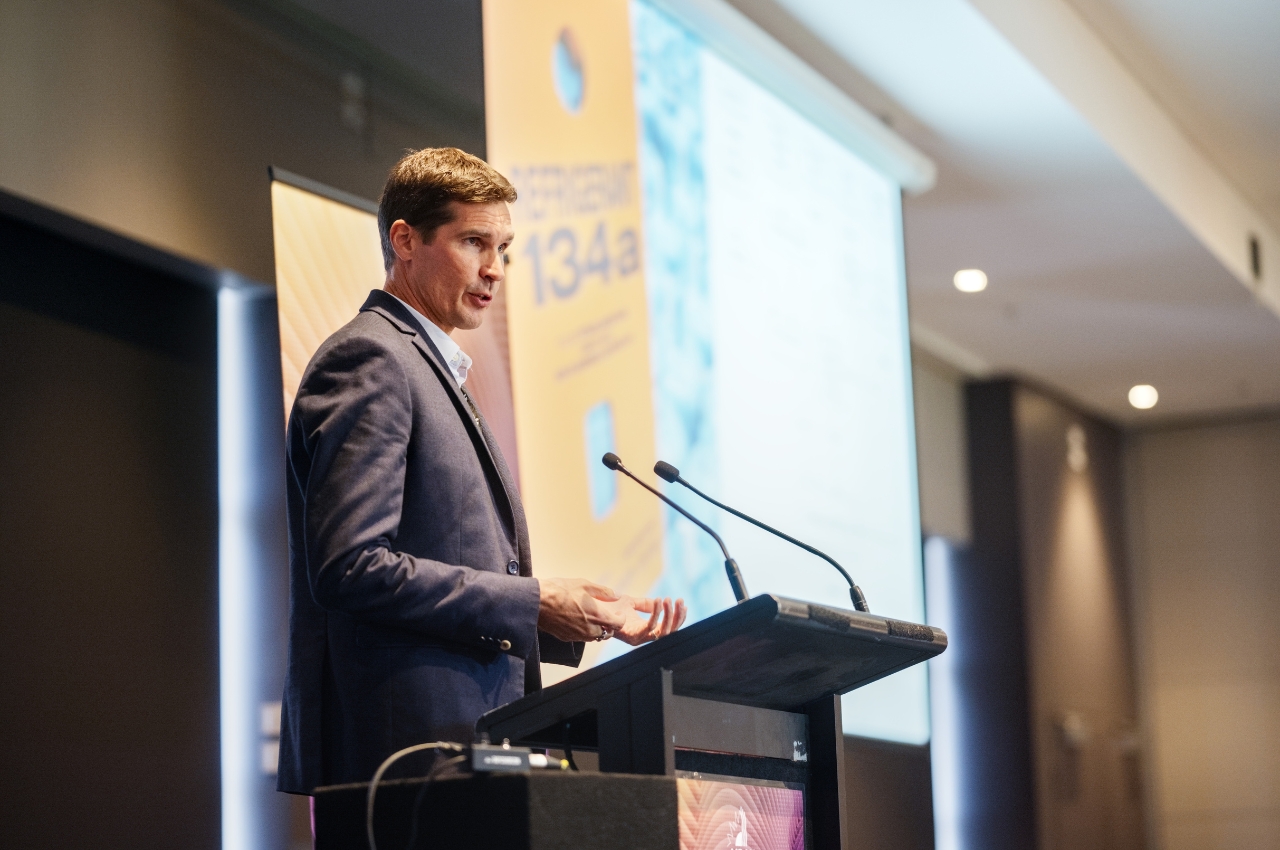
What gets measured gets managed is a truism of our age. But in the case of refrigerant gases, could a heavy reliance on one specific measurement be concealing the full sustainability story? Mark Vender reports.
They may be an invisible part of an often-invisible industry, but refrigerants and their environmental impacts have been getting attention for some time.
First, when chlorofluorocarbons (CFCs) were found to be ozone-depleting substances, the Montreal Protocol was established to replace them with alternatives – predominantly hydrofluorocarbons (HFCs). Later, when the high global warming potential (GWP) of these HFCs came into sharp focus, we made plans to phase them down.
In 2016, the parties to the Montreal Protocol penned the Kigali Amendment, which added HFCs to the list of controlled substances and approved a timeline for their gradual reduction. By the late 2040s, the plan is to reduce their use by 80–85 per cent, which is expected to avoid up to 0.5°C of global temperature rise by 2100.
Because these goals are based on the GWP of the refrigerants, so too are many of the controls. But as we concentrate on GWP as the most important measure, are we oversimplifying the matter?
Adrian Bukmanis, from Veridian Refrigerant Management, believes so. He presented at AIRAH’s recent Future of HVAC Conference on the topic “No longer immaterial: The life-cycle impact of refrigerants.”
Material concerns
Bukmanis notes that when it comes to low-GWP refrigerants, the current focus is on emissions in use. That is, the impact of refrigerant leaking from active HVAC&R equipment.
“This tends to give us a tunnelled view,” he says. “We should also consider the manufacturing emissions and the disposal emissions.”
For common high-GWP refrigerants, such as HFCs, Bukmanis agrees that the bulk of the emissions are probably in the use phase, and the manufacturing and disposal emissions could be considered as relatively immaterial.
“However, if we’re looking at low-GWP refrigerants, and especially if we’re looking at synthetic or HFO refrigerants, we might find that the manufacturing and disposal is greater than the in-use emissions,” he says.
“We also have pollution impacts, both upstream and downstream, for synthetic refrigerants, that I would consider are not immaterial.”
There are a number of tools available for evaluating refrigerants: GWP, total equivalent warming potential (TEWI), life-cycle climate performance (LCCP), and life-cycle assessment (LCA). Bukmanis says that if we want to look at all environmental impacts, LCA is perhaps the best tool available.
“But it’s hard to get this data, and hard to find the refrigerants in the databases,” he says. “You need to know their chemical names or structures. And it’s not consistent across the databases.
“There’s information for example for R134a, but it’s very hard to find information on R1234yf given it’s heavily patented and there is little transparency in the manufacturing process.”
LCA is a useful tool, Bukmanis says, but it doesn’t provide all the answers.
“As we home in on GWP as the most important measure, are we oversimplifying the matter?”
Look under the bonnet
As an alternative, Bukmanis suggests we can consider how refrigerants are made.
Manufacturing HFCs is a complex process. They require fluorine, a base hydrocarbon such as ethylene, and for some pathways, sulphur, lime and chlorine – all of which must be extracted. Electricity, steam and nitrogen also go into production.
Partly because of this complexity (as well as the variables that come into play depending on where a refrigerant is manufactured), embodied emissions in refrigerants can vary widely. Estimates from the few studies that exist suggest that 1kg of R134a could contain anywhere between 5kg and 87kg of CO2e. In this case, upstream emissions are relatively minor compared to potential in-use emissions.
For newer low-GWP refrigerants such as R1234yf, which are shrouded in patents, the numbers are even harder to confirm. Bukmanis says, however, there are some well-established issues that should be considered in refrigerant selection.
“We do know that ozone-depleting chemicals are used to make low-GWP fluorinated refrigerants, in particular the feedstocks HCFC-22 (R22) and carbon tetrachloride.”
Although ozone-depleting substances are being phased out under the Montreal Protocol, their production is allowed for feedstocks, because in theory they are not emissive during the manufacturing process. But as Bukmanis points out, there is a small percentage that escapes.
Moreover, we are producing increasing quantities of these feedstocks – 800,000 tonnes of HCFC-22 in 2022, up from 200,000 tonnes in 2002. Hence even small fugitive emissions are starting to stack up.
“It surprises a lot of people that we’re now producing more ozone-depleting substances than we’re actually producing HFCs,” says Bukmanis. “It’s becoming a material concern.”
There are also unwanted byproducts of the production process, for example HFC-23 (GWP 14,600) and PFC-318 (GWP 10,200). Global emissions charts for these chemicals show that they are both increasing. It is worth noting that another ozone-depleting substance, dichloromethane, can be used as a feedstock in the manufacture of R32, which has become the default refrigerant for many types of air conditioners.
“Depending on how we do our assessment,” says Bukmanis, “we can end up with quite a large upstream impact.”
“We need to get to real zero, and not the bad net zero with a slow transition.”
Going with the flow
As well as looking closely at upstream impacts, Bukmanis says the same scrutiny must be applied to the downstream: refrigerant disposal.
Australia is lucky to have a world-leading program and cutting-edge plasma arc facilities for destroying refrigerants at end of life. But that is not the case in the rest of the world, where most of the six million tonnes of the global refrigerant bank are found. And even in the best facilities, refrigerant destruction uses energy.
“The thing that makes synthetic refrigerants so good and gives them their stability and inertness also makes them really hard to break down,” says Bukmanis. “It can take more than a thousand kWh of electricity just to destroy one tonne of fluorinated refrigerant.”
Again, for high-GWP refrigerants, this downstream impact may be relatively minor compared to in-use emissions, but for low-GWP options, it is more significant.
Finally, other environmental impacts need to be considered, says Bukmanis. This includes manufacturing, transport and distribution emissions, byproducts, and toxic releases.
In September 2021, the US EPA published an impact analysis of phasing down HFCs, which contemplated the toxic releases found near synthetic refrigerant manufacturing facilities.
“The health impacts are not immaterial,” says Bukmanis.
Similarly, refrigerant destruction can produce acid gases, dioxins/furins, particulates, CO2 off-gas and carbonyl fluoride.
And this is all before considering the environmental impacts during the operational phase. Concerns have been raised about HFO refrigerants breaking down into TFA – an ultra-short-chain PFAS – which is highly persistent and highly mobile in the environment.
“We should also consider the manufacturing emissions and the disposal emissions.”
Real zero
“We need to get to real zero,” says Bukmanis, “and not the bad net zero with a slow transition.
“All emissions need to be considered and we need to look beyond just the climate impacts. We also need to look for more transparency where we can. Those who have leverage and the ability to put some pressure on their suppliers should ask questions about where their refrigerants are coming from, and where and how they’re produced.
“And there needs to be a quick move away from fluorinated refrigerants to non-fluorinated alternative natural refrigerants. The production process and the disposal process are much easier with non-fluorinated refrigerants.”
Bukmanis gives the example of CO2, which in some facilities requires about 0.5kg to produce 1kg of CO2 at refrigerant grade.
“It shouldn’t be released to atmosphere either, but there is lots of global effort on how to repurpose it,” he says of CO2.
“We need to look upstream and downstream, and then proceed carefully with our refrigerant selection.”
Need to know
A version of this article was originally published on HVAC&R News.
Go to www.hvacrnews.com.au
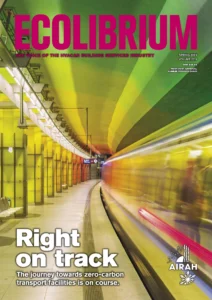
This article appears in Ecolibrium’s Spring 2023 edition
View the archive of previous editions
Latest edition
See everything from the latest edition of Ecolibrium, AIRAH’s official journal.