Semiconductor Heat Pumps – A New Approach to Zero Emissions Heating
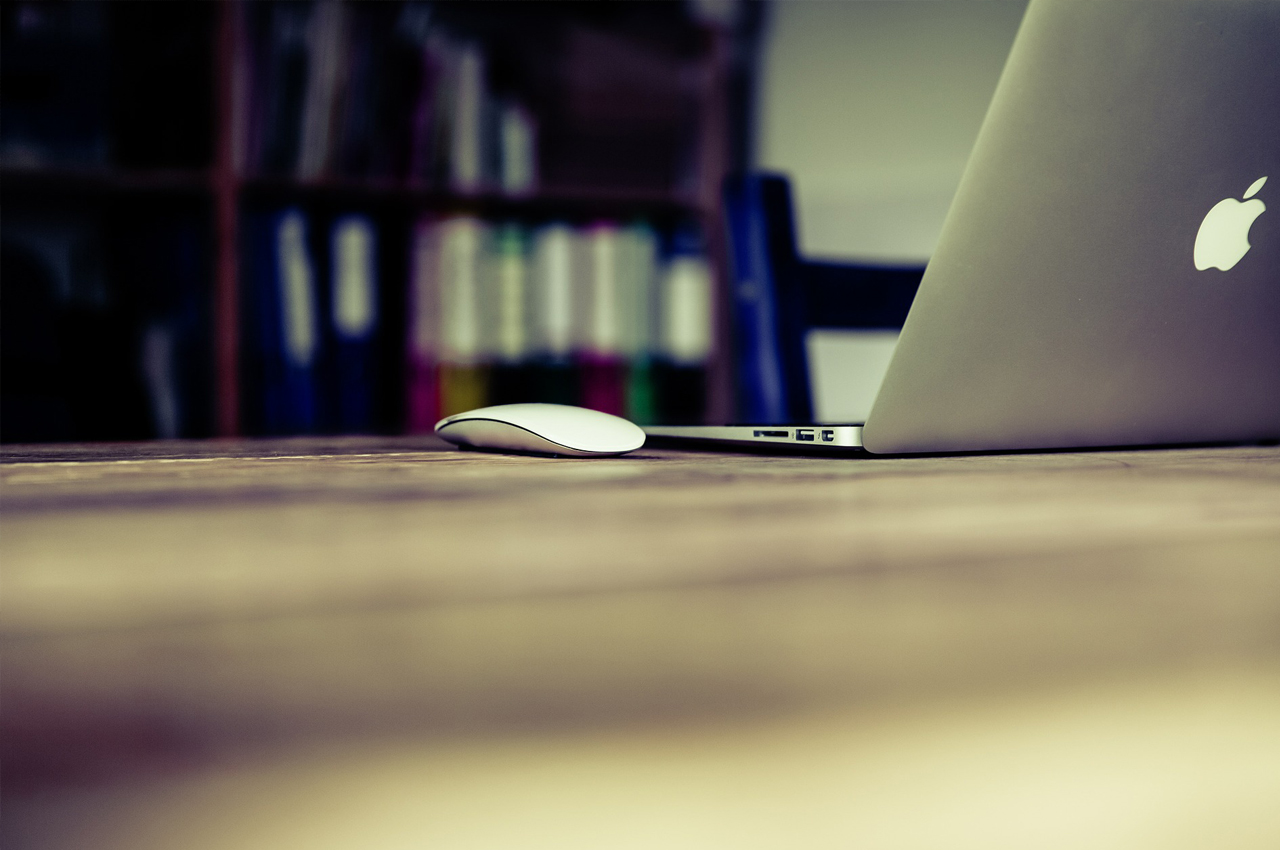
As a result of the increased contribution of renewable energy for electricity generation and rising gas prices, there has been a shift from natural gas to electric-based heating in recent times. Commonly used electric heating technologies in the built environment include electric resistance, and air- or water-source heat pumps (hereafter known as “conventional heat pumps”). However, a key concern in the industry has been the use of refrigerants that have high Global Warming Potential (GWP) and other refrigerants that are flammable and/or toxic.
This article reports on work conducted by the author that investigates water-source thermoelectric heat pumps (TEHP). The results highlight that this technology can achieve performance approaching conventional heat pumps when operating in low-temperature lift applications and when the input current is significantly less than the manufacturer’s rated values. The article also highlights some of the benefits of the TEHP, which include zero refrigerants and oils, no noise and vibration, compact size and no mechanical components.
The author intends to continue research into the subject, develop a reliable TEHP module that can be upscaled to several kW and be installed to the family home to provide in-slab heating utilising ground-source heat exchange. The demonstration scale system would allow both refinement to desired operating conditions within the performance envelope and serve a purpose as an educational tool.
Introduction
TEHP heating and cooling was discovered by the French physicist Peltier in 1834. Thermoelectric modules have traditionally been used for niche cooling applications that require limited amounts of cooling, mechanical robustness and compact size, examples being instrument cooling, the provision of solar/battery powered refrigeration to preserve medicine in remote areas, and portable food and beverage coolers.
This article provides background theory of the performance capabilities and limitations of this technology and a comparison with a conventional heat pump. The technology is currently not used for HVAC because the resulting coefficient of performance (COP) has been low using the traditional TEHP module assembly methods.
The main focus of this paper is the practical performance assessment of a TEHP assembled and tested by the author, the performance results achieved and suggestions for future research and improvements. There is also a discussion, with the aims of identifying suitable applications where this technology can be potentially deployed for HVAC use commercially.
A new approach to zero emissions heating
The Theory
Heat pumps transfer thermal energy from lower to higher temperature bodies through the input of work, typically mechanical or electrical. The instantaneous performance of a heat pump is characterised by the term COP, defined as the ratio of thermal output to work input.
In the study of thermodynamics, the Carnot cycle sets limitations to the highest COPs that can be achieved based on the temperatures of the hot and cold side; however, this is a theoretical limit not achievable by any real machine, due to process irreversibilities.
The relationship is expressed in equation [1]. A comparison of typical COPs is given in table 1 below.
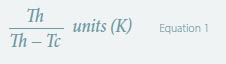
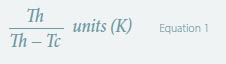
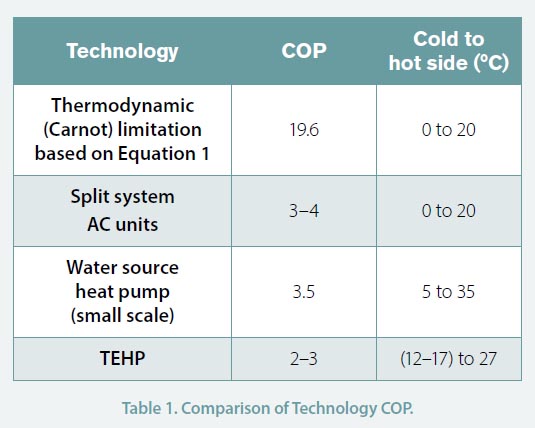
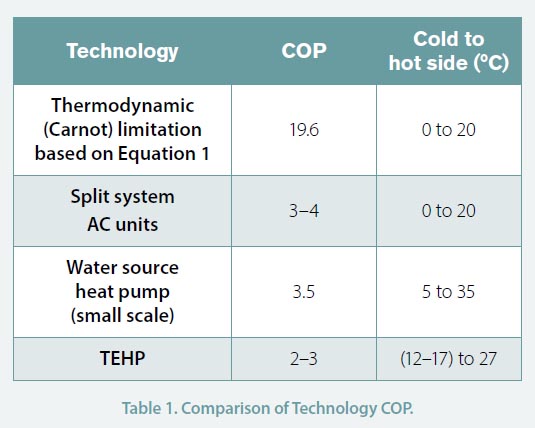
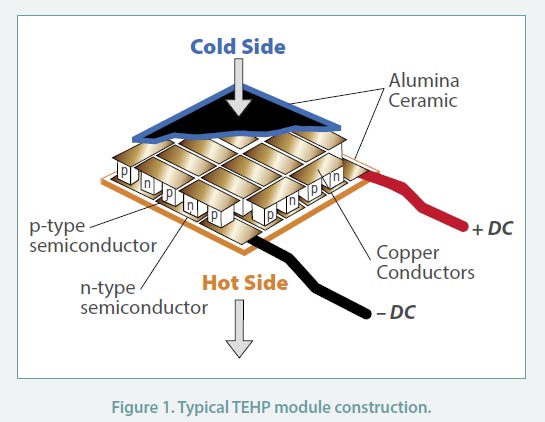
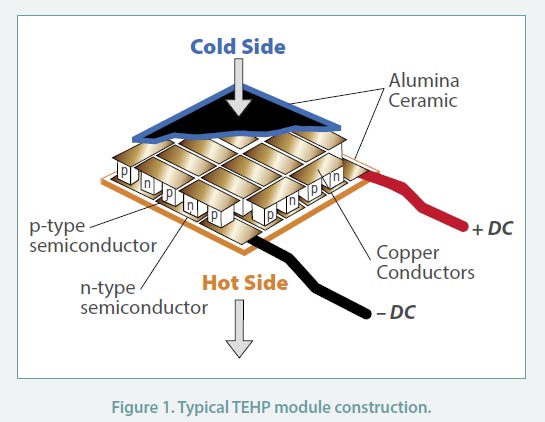
The thermoelectric modules were comprised of semiconductors sandwiched between two ceramic plates. DC current applied to the module produces a temperature difference between the upper and lower surfaces of the module. The operating principle is referred to as the thermoelectric effect or Peltier effect.
The thermoelectric module used in this study is a TEC12706 [1]. This module measures 40x40x3mm and is marketed as providing 60W of cooling or a 60°C temperature differential (TD) at the rated input current. The manufacturer’s performance data provide greater insight into the module performance. Performance data is provided by manufacturers as a function of hot to cold side TD and electrical supply current (Figure 2). These correlations have been re-arranged (Figure 3) to provide performance data more suited for use in the HVAC industry, expressing heating COP as a function of module TD and heating output.
Figure 2 shows that a competitive COP can be obtained at low-temperature differentials and low power levels, i.e., when operated between 1 and 2.5A, well below the manufacturer’s 6A rating. Under these conditions the required DC voltage is typically 3–6VDC.
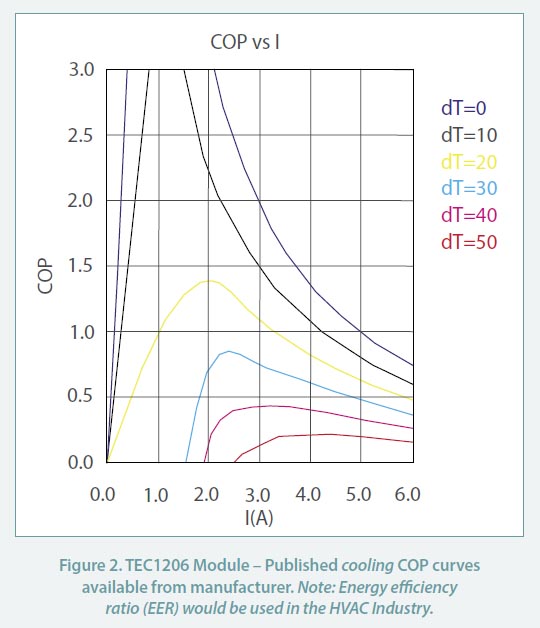
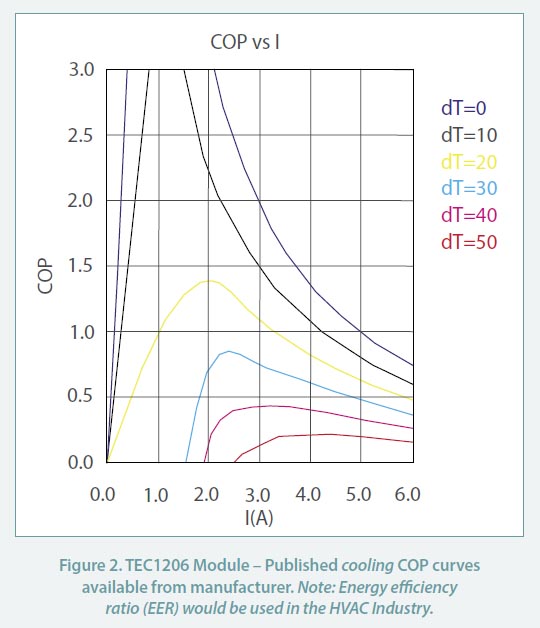
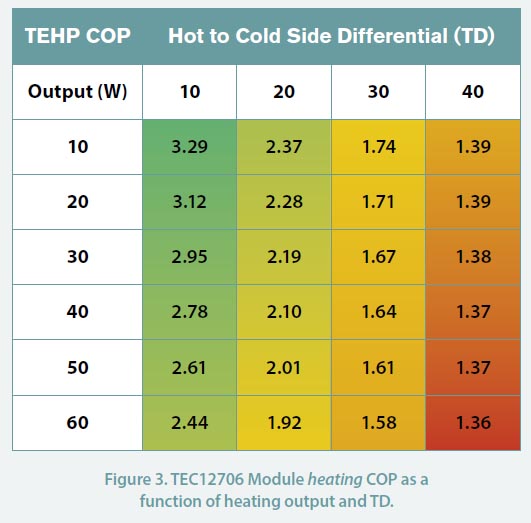
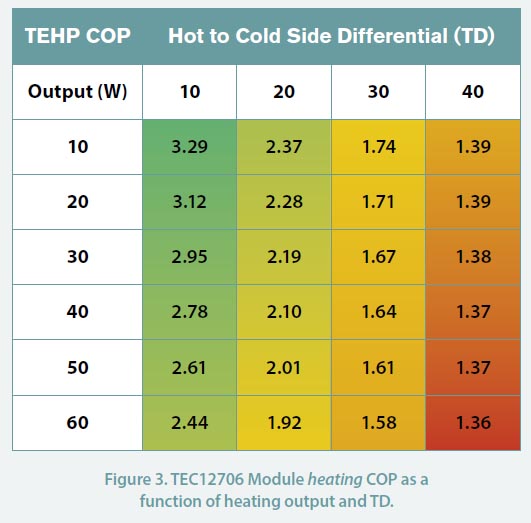
The Application
he thermodynamic COP of TEHP modules is less than for vapour compression refrigeration, for an equivalent temperature lift. A key limitation of the TEHP module is the loss of performance at high load (higher input current) and at higher temperature differentials. COP is only comparable to conventional heat pumps when operated such that load current is kept below 30–40% of nominal current rating and temperature differentials are maintained at less than 20°C TD. One of the reasons for this has been the challenge of finding semiconductors having the desired properties, which include a high Seeback Coefficient (induced thermo-electric voltage for a given temperature), a high electrical conductivity and low thermal conductivity.
With the above limitations in mind, a key innovation proposed is the adaptation of this technology for space heating and cooling in buildings using in-slab heating systems and ground heat exchange loops. In-slab heating applications allow low-temperature heating sources to be used. Optimum floor temperatures for comfort lie between 21°C and 28°C [3] with modern designs.
While flow water temperatures have traditionally been between 30–45°C, reducing in-slab pipework spacing, improving floor thermal design and with energy-efficient construction it is expected that flow temperatures between 22°C and 30°C will be satisfactory, especially if the building construction has good thermal insulation and minimal air leakage. Ground exchanger loops can be designed for most climates to keep this differential within 20°C TD.
In-slab heating systems, in particular in-screed systems rather than dry type systems (e.g., fitted under timber floors) usually have significant thermal mass. This allows the heating temperature set-point to be elevated during the day, when solar energy is available, thus providing energy storage and reducing evening loads. In the event of temperature overshoot due to solar loads, the electrical polarity can be reversed, and with good zoning could provide immediate cooling.
Since the modules should be operated at less than 30–40% of the rated current for optimal efficiency, there is opportunity to overdrive the modules for higher thermal output. When the modules are operated at the rated current with higher temperature differentials, the COP will approach one, which is equivalent to the performance of electric resistance heating.
Since the TEHP operates on direct current, it is conceptually straightforward to couple a TEHP to a photovoltaic (PV) electric power source. A characteristic of PV solar energy generation is its variable power output, typically not coinciding with building demand. However, overdriving of the TEHP allows peaks in PV energy to be stored within the slab. Although the TEHP COP is lower under these conditions, the TEHP can utilise the power rather than export to the grid at modest “feed-in tariff” rates. Furthermore, a conventional heat pump may not be able to operate in such an “overdrive” manner.
PV arrays can be directly coupled to TEHPs, with DC power conditioning equipment thus not requiring the complexity and cost of grid connection inverters and associated AC-DC converters. Dedicated PV arrays serving TEHPs may provide heating options where the building electric infrastructure is unable to accommodate additional load or the location for conventional air-source heat pumps is unsatisfactory.
Table 2 provides a summary with comparisons of various aspects of TEHP vs conventional heat pumps, other than performance. The cost comparison should be regarded as high level, with a broad range deliberately given, because there could be significant variance depending on module housing materials and assembly methods.
Electrification projects having zero-emissions objectives must consider that all refrigeration-based equipment have inherent emissions, through age related leakage of refrigerant gas typically quoted in terms of several percent per year, during maintenance and disposal. The TEHP eliminates the possibility of refrigerant emissions.
The prototype
Thermoelectric modules are typically “sandwiched” between metal heatsinks, resulting in an associated joint thermal resistance, which in turn requires a higher temperature differential to drive the heat transfer. This reduces the COP. The resultant thermal resistance is too high to permit operation within the higher COP (green area) of the performance envelope (Figure 3) as highlighted by the thermal network analysis example as shown in Figure 4.
In this study, the use of a circulating heat-transfer fluid in direct contact with the alumina ceramic of the module eliminated thermal contact resistance.
A prototype TEHP heat exchanger was constructed with a 3D printer using PLA plastic media. The assembly described in this article comprised four commercially available TEC 12706 modules arranged side by side such that the fluid streams on each side passed in a counterflow manner, as shown in Image 1 and 2.
A key practical challenge was constructing a watertight assembly so that the semiconductor between the ceramic was not damaged.
The schematic in Figure 5 shows the experimental set-up. A building automation controller was used to datalog the flow and return temperatures on the hot and cold side, which were calibrated with thermocouples. A digital turbine meter was calibrated with a known volume of water and the constant volume flow rates and electrical energy input in Watts were manually entered into the building automation controller. In real time the controller computed the temperature differentials, log mean temp difference (LMTD), heating output (Watts) and COP.
A variable voltage power supply and digital power meter were used to set constant input power at 10, 20 and 30 Watts respectively.
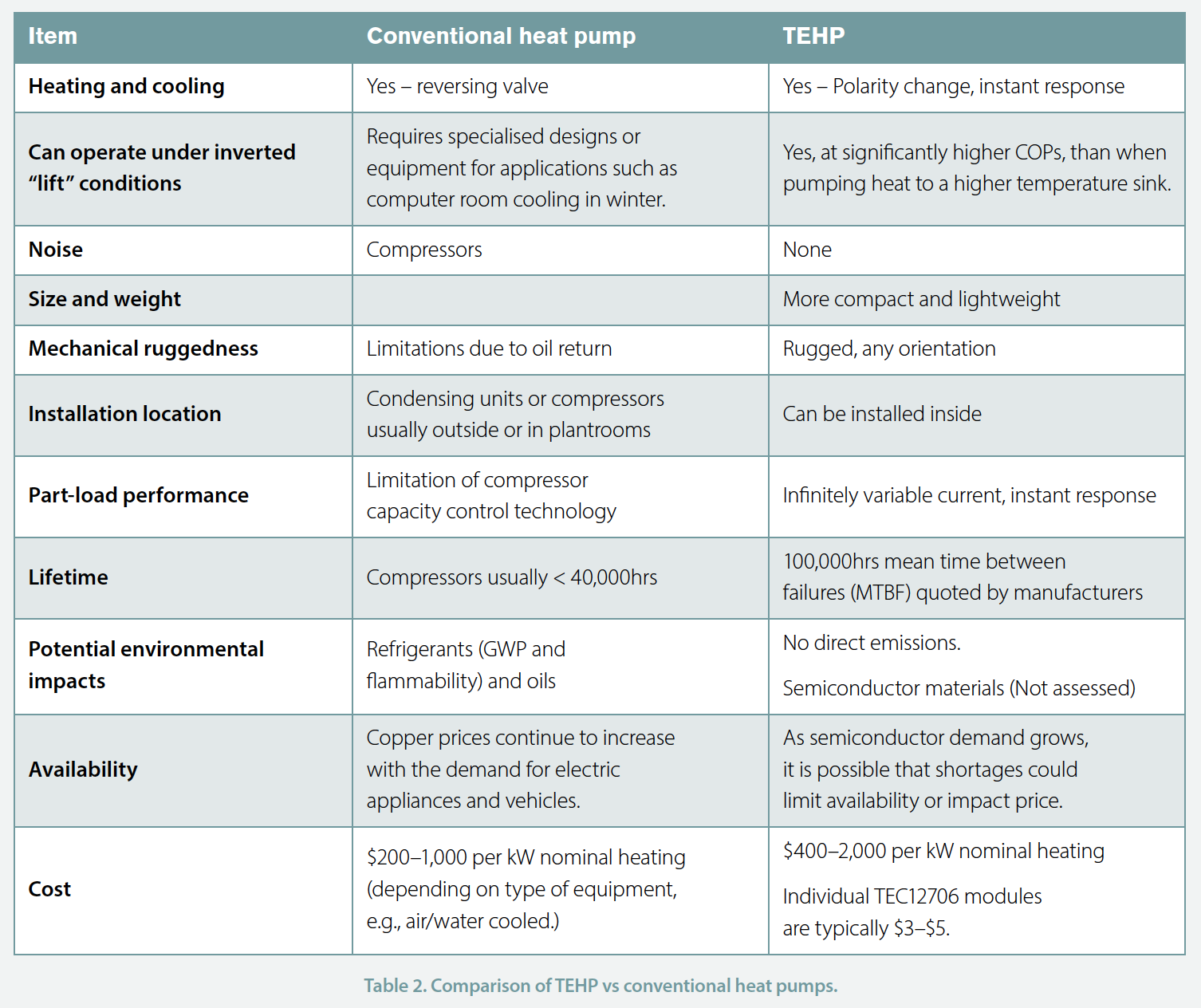
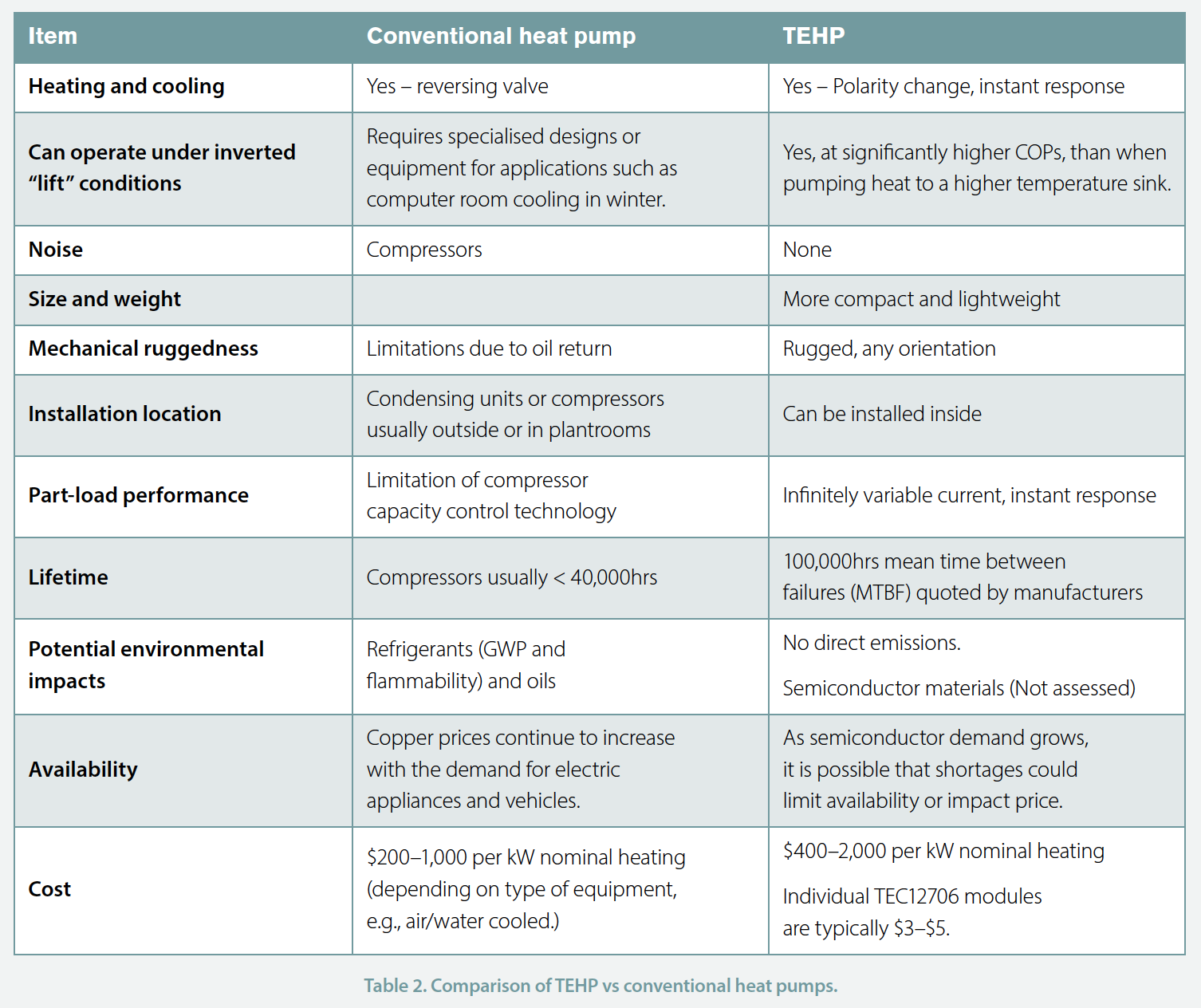
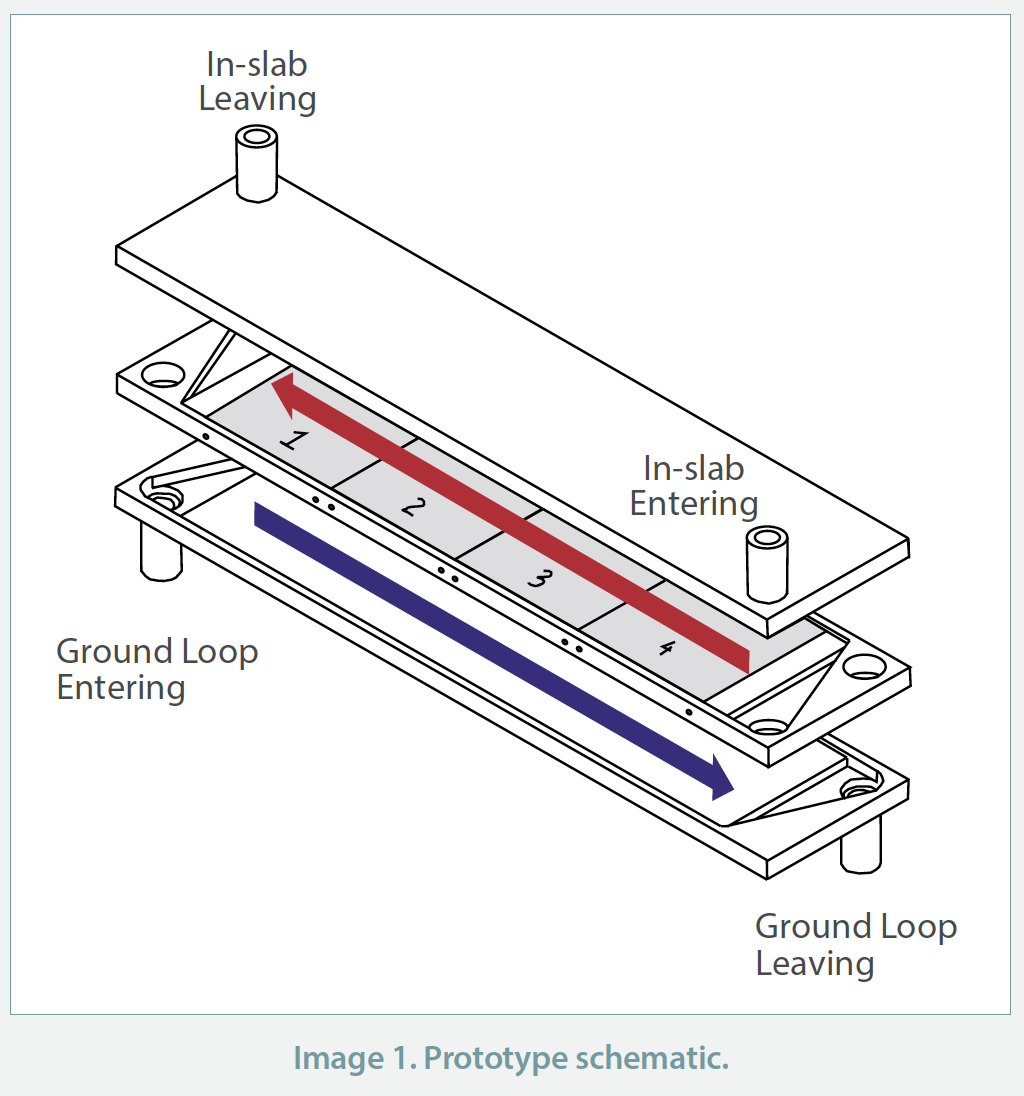
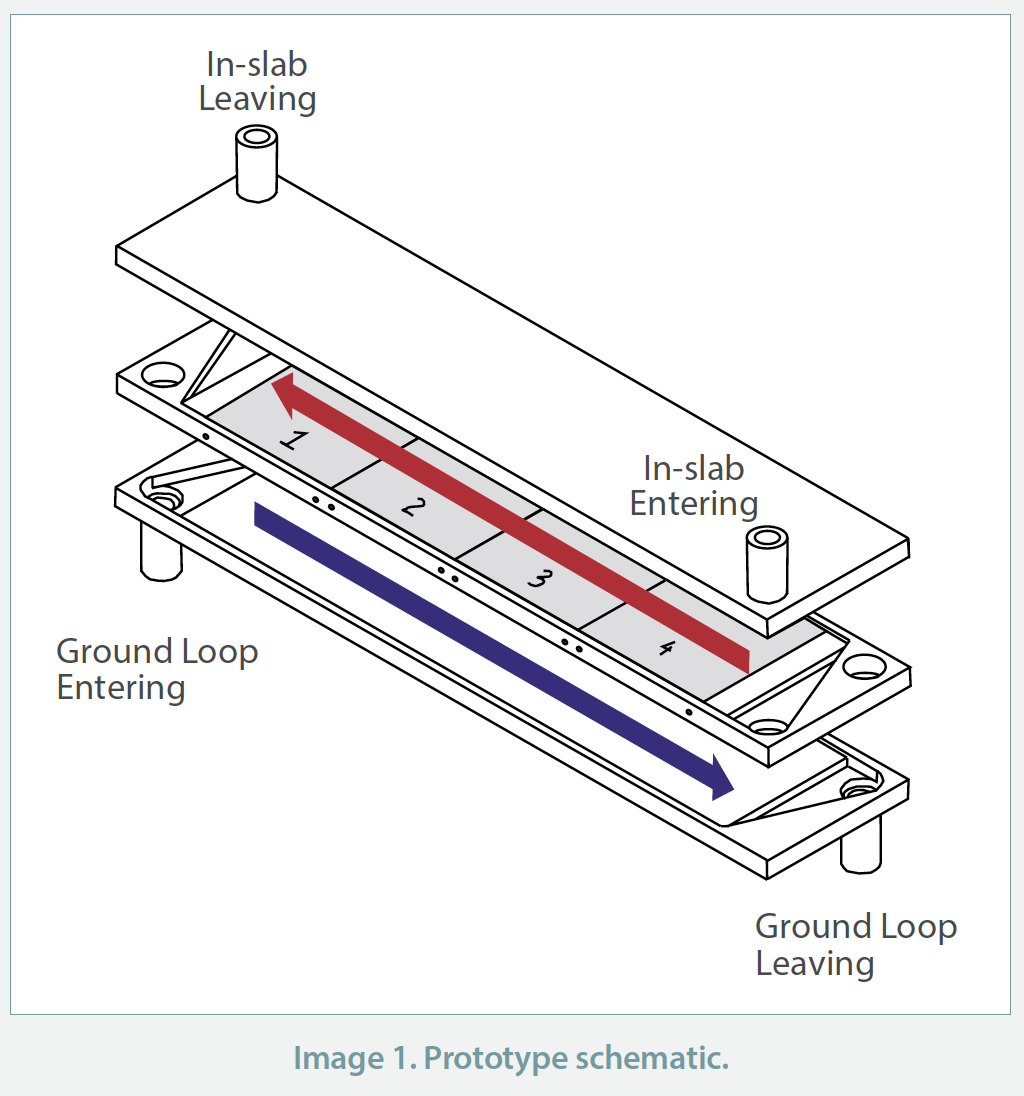
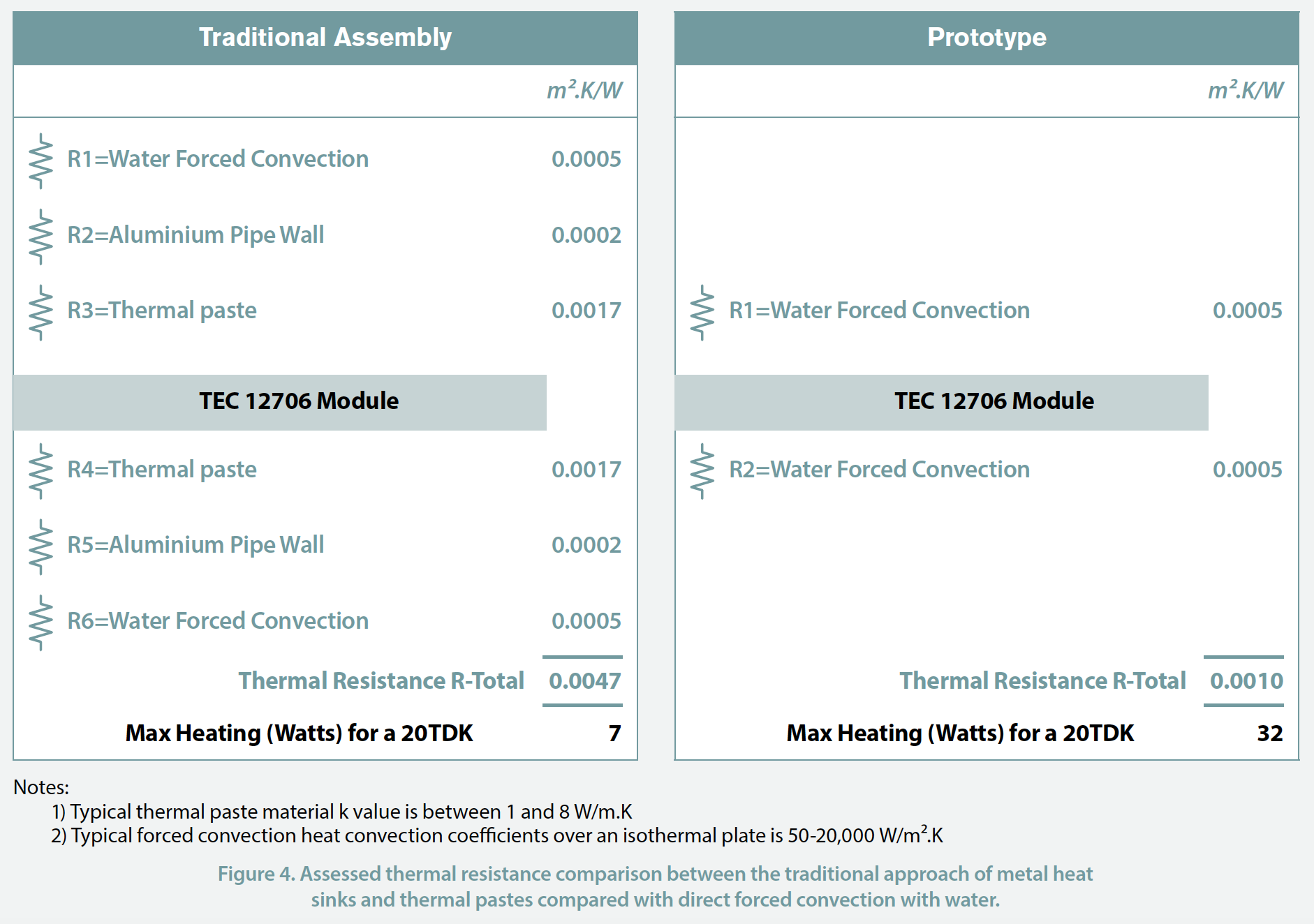
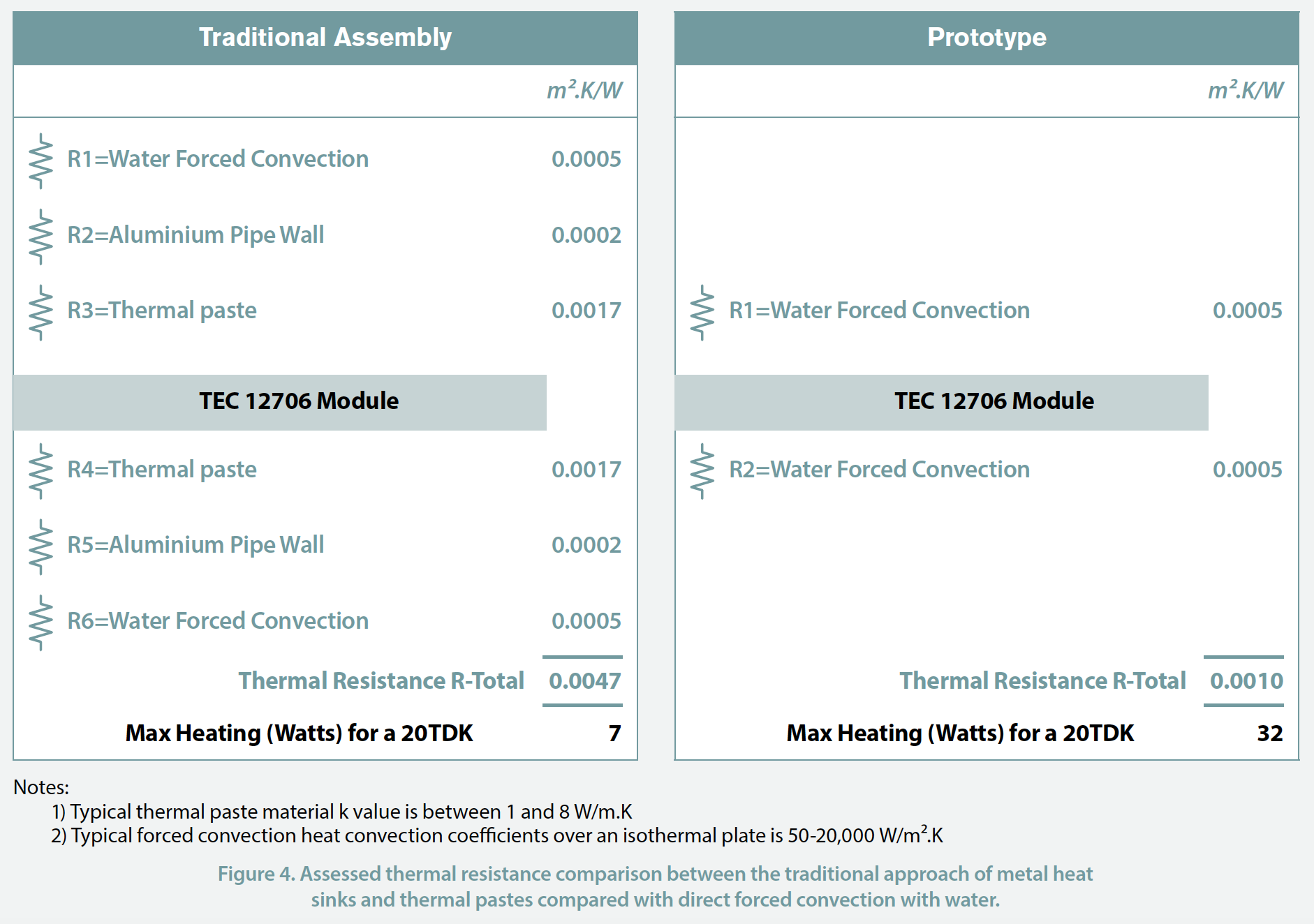
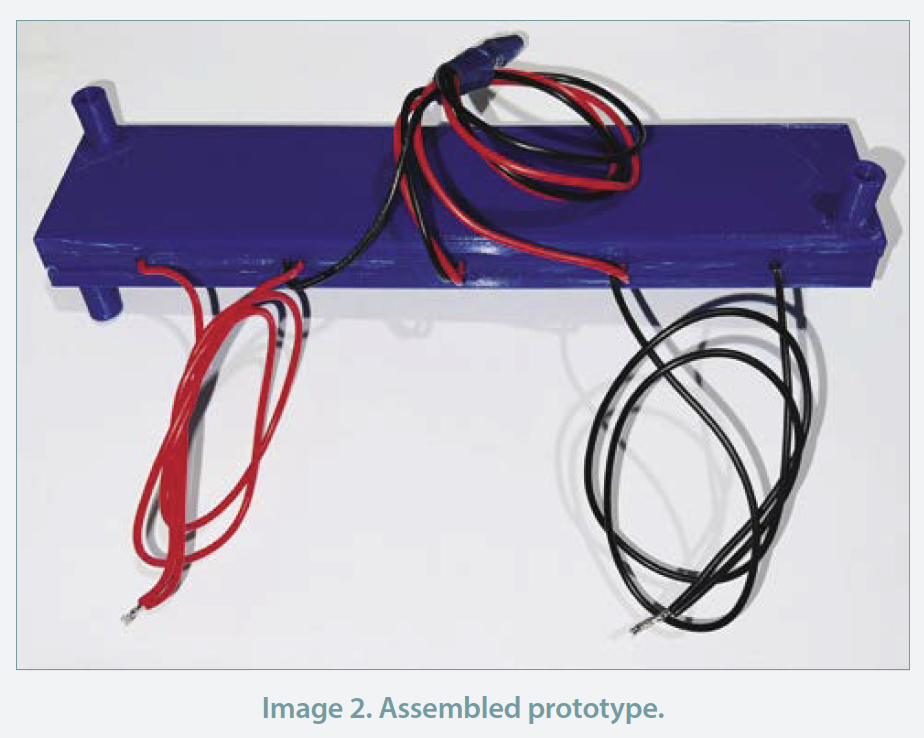
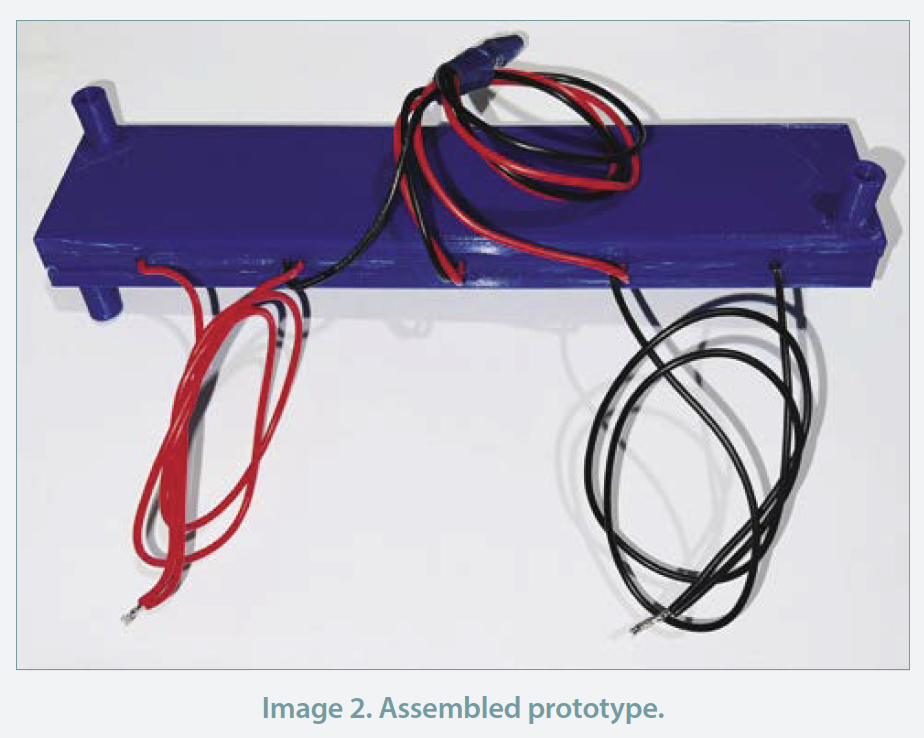
The results
The results below indicate COP in the range of 2.2 to 3.2, with the highest performance at the lowest heating output. While this set of results is based on an average “lift” (i.e., LMTD between fluid streams) of between 9°C–10°C, testing has indicated that performance tends to reduce quickly beyond 15°C–20°C. LMTD represents the mean temperature difference between both fluids, based on the entering water temperatures (EWT) and leaving water temperatures (LWT), for both fluids as shown in figure 6.
Although pumping energy has not been quantitatively analysed, it is noted that circuit pressure drop was less than 30kPa on the ground-heat exchange loop, and less than 60kPa for the in-slab loop. Higher flow rates and pressure drops would cause increased turbulence and further improve COP, at the expense of increased pumping energy.
The results were promising and in general agreement with the manufacturer’s performance data, considering the challenges:
- There were significant inconsistencies in the application of adhesives used in the TEHP assembly.
- Rudimentary plumbing with use of “poly” (PE) piping and fittings, and combined with the simple open-loop makeup filling tube, collectively resulted in frequent leaks and air entering the loop, thus impacting thermal measurements.
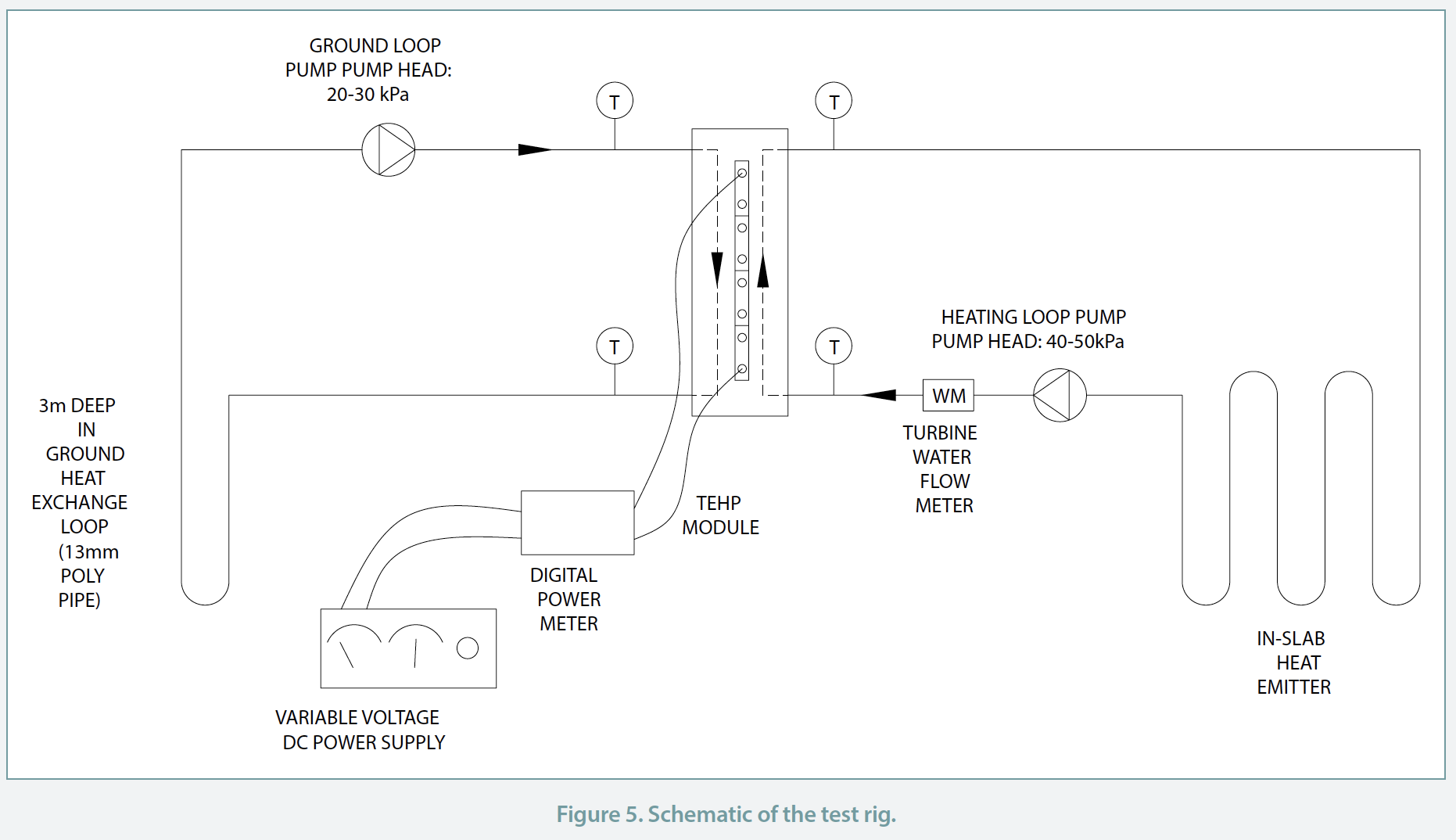
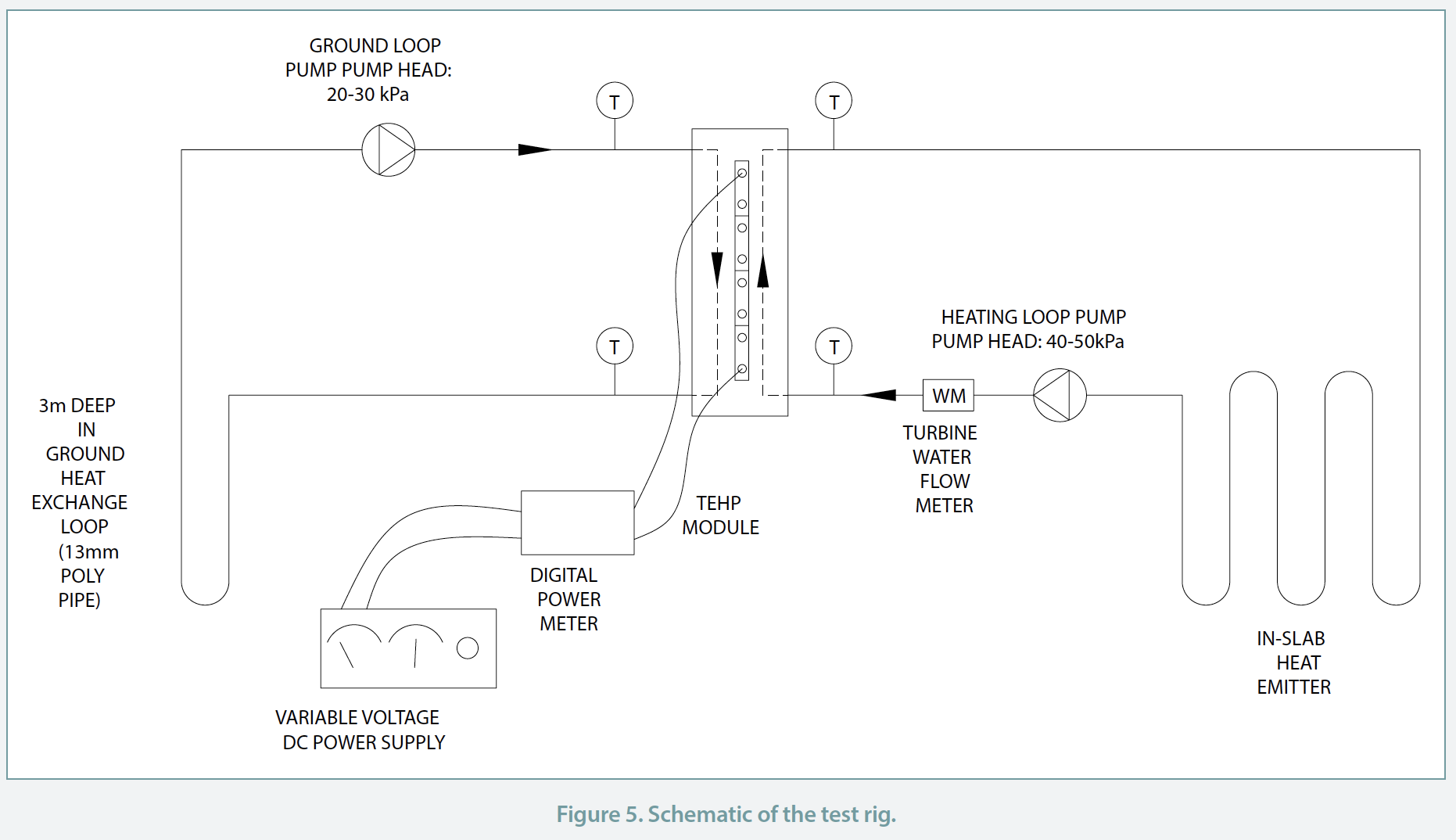
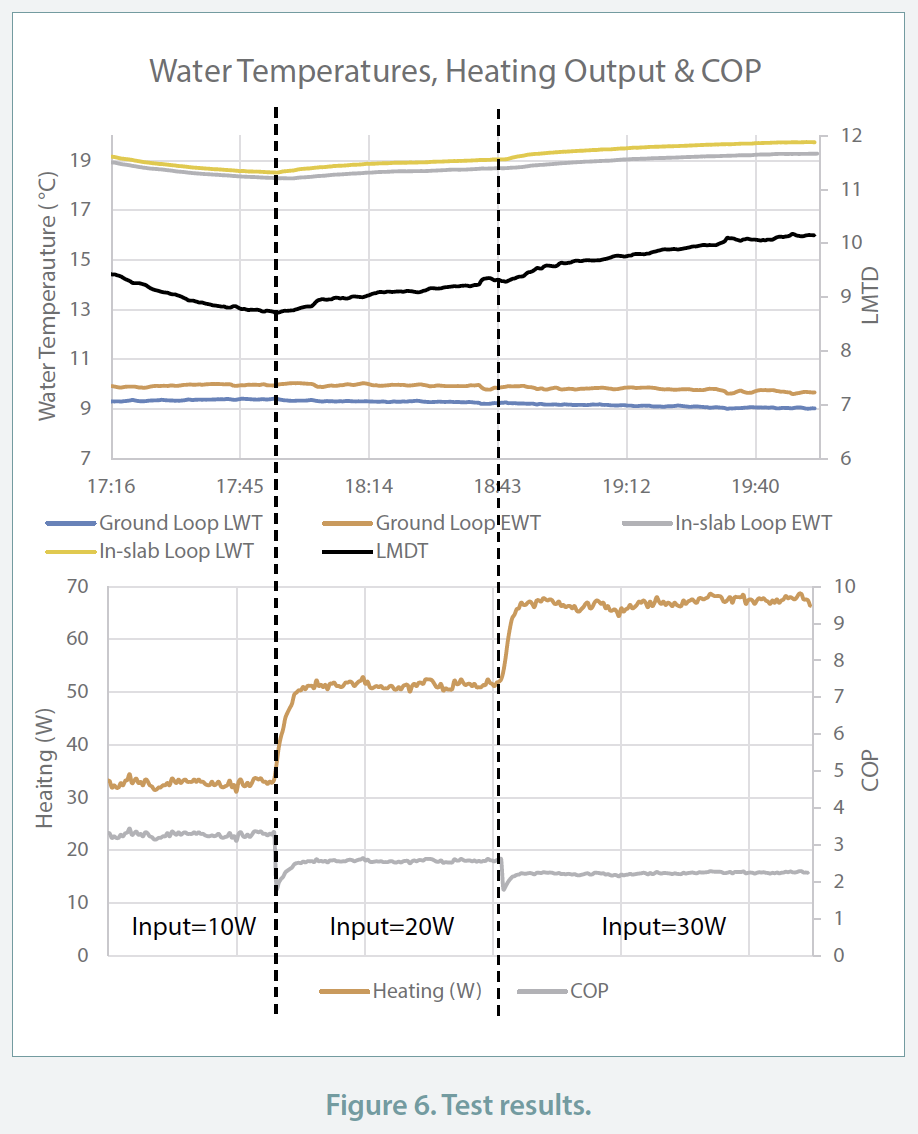
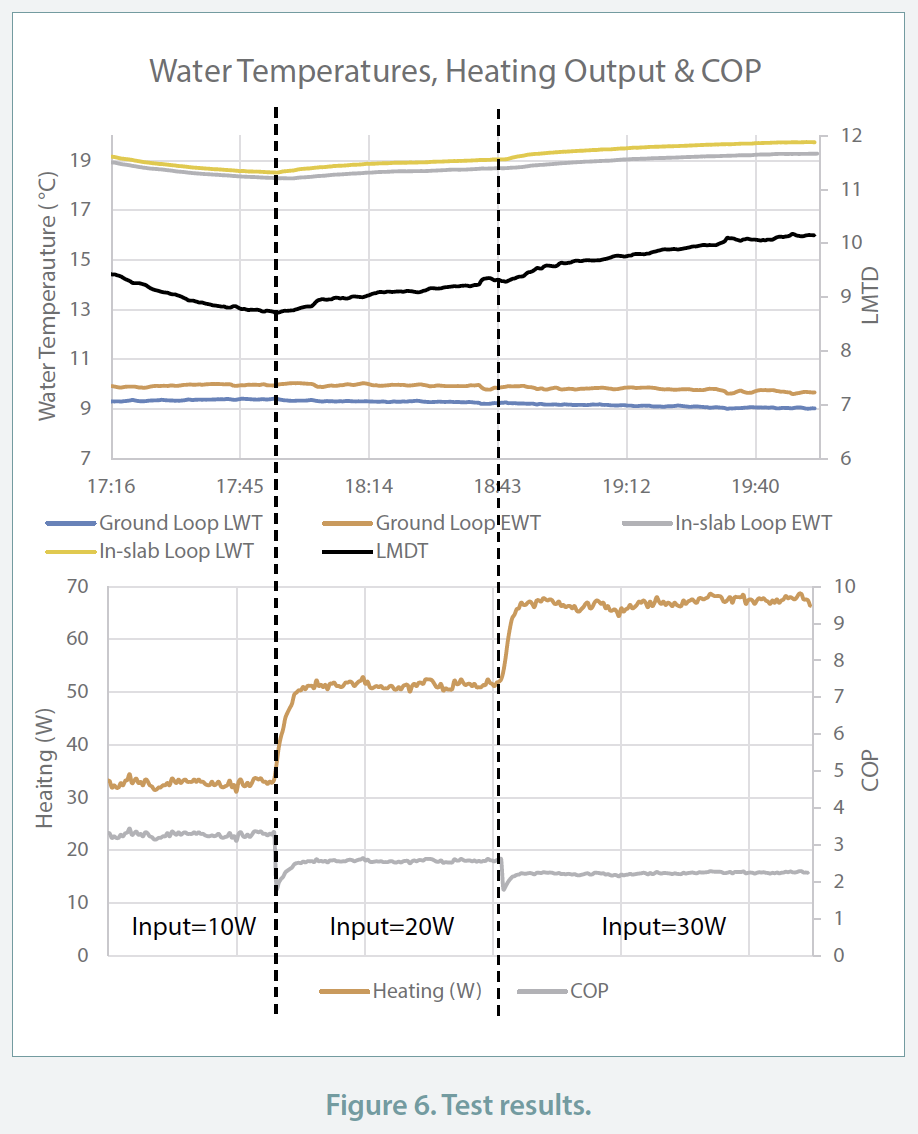
Discussion
It is exciting that based on the results from this study, the TEHP could present an alternative technology to heat pumps based on the traditional vapour compression cycle which have been awaiting for a long time for the development of a safe and environmentally friendly alternative to CFC based refrigerants. With further development and mass production the TEHP could have the potential to play a part in the transition of the HVAC industry to decarbonisation.
Considering the COP values achieved in this study with the basic experimental arrangement and limitations, there is a significant opportunity to improve the performance, assembly reliability and develop a cost-effective zero refrigerant heat pump.
Further testing carried out demonstrated higher COPs achieved under inverted operation. This refers to “pumping” of heat from a higher temperature source to lower temperature sink, and generally requires specific refrigeration designed for those conditions. A potential application could include a residential swimming pool having solar hot water heating, which is then used as the energy storage and the source for the home’s TEHP heating system.
The TEHP initially operates under inverted conditions with a high COP which seamlessly transitions to normal heat pump operation as the pool water falls in temperature. As a result, the technology is well suited for “charging” or “discharging” thermal energy sources under either positive or negative temperature lift conditions, including frequent “reverse-cycle” transitions.
In contrast, conventional heat pumps have inherent limitations, which include minimum differential pressures for oil return, and thermal inertia associated with reverse-cycle transitions.
Where multiple TEHP systems exist in a building, heat recovery can be achieved when some systems are in heating and others in cooling.
In modern well-insulated houses having low heating requirements, a likely solution may involve a TEHP system designed to provide background heating, which can be supplemented with direct electric heaters for short periods during peak winter days.
The author intends to continue research into the subject, develop a reliable TEHP module that can be upscaled to several kW and be installed to the family home to provide in-slab heating utilising ground source heat exchange. The demonstration scale system would allow both refinement to desired operating conditions within the performance envelope and serve a purpose as an educational tool.
References
- Manufacturers technical data – Roßmann Electronic GmbH, MODEL: RO6.0-51.4 (TEC1-12706), https://cdn-reichelt.de/documents/datenblatt/C800/TECB1.pdf
- Figure 1
- ASHRAE: ASHRAE Handbook – 2020 HVAC Systems and Equipment, American Society of Heating, Refrigeration and Air-conditioning Engineers Inc., pp.48.1, (2019)
- CIBSE: CIBSE Design Guide B, 2005, Heating, Ventilation, Air Conditioning and Refrigeration Section 1.4.3.4
- ASHRAE: ASHRAE Handbook – 2017 HVAC Fundamentals, American Society of Heating, Refrigeration and Air-conditioning Engineers Inc., pp.4.1, (2017)
Acknowledgements
I would like to acknowledge the following individuals who made the project possible:
- Kylieann and Matthew Holland – For tolerating the time spent on this project, often at the expense of family time.
- Lasath Lecamwasam, F.AIRAH – Colleague and Director of ESBS, for the exchange of technical ideas and providing the motivation to write this article.
- Dr Mike Dennis – For the exchange of technical and practical ideas and providing various plumbing components.
- Gerry Hackett, M.AIRAH – For his review of the article and provision of technical feedback.
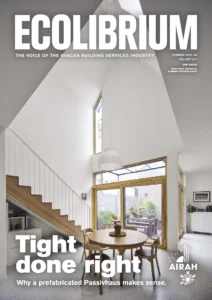
This article appears in Ecolibrium’s Summer 2023-24 edition
View the archive of previous editions
Latest edition
See everything from the latest edition of Ecolibrium, AIRAH’s official journal.