The case for maintenance
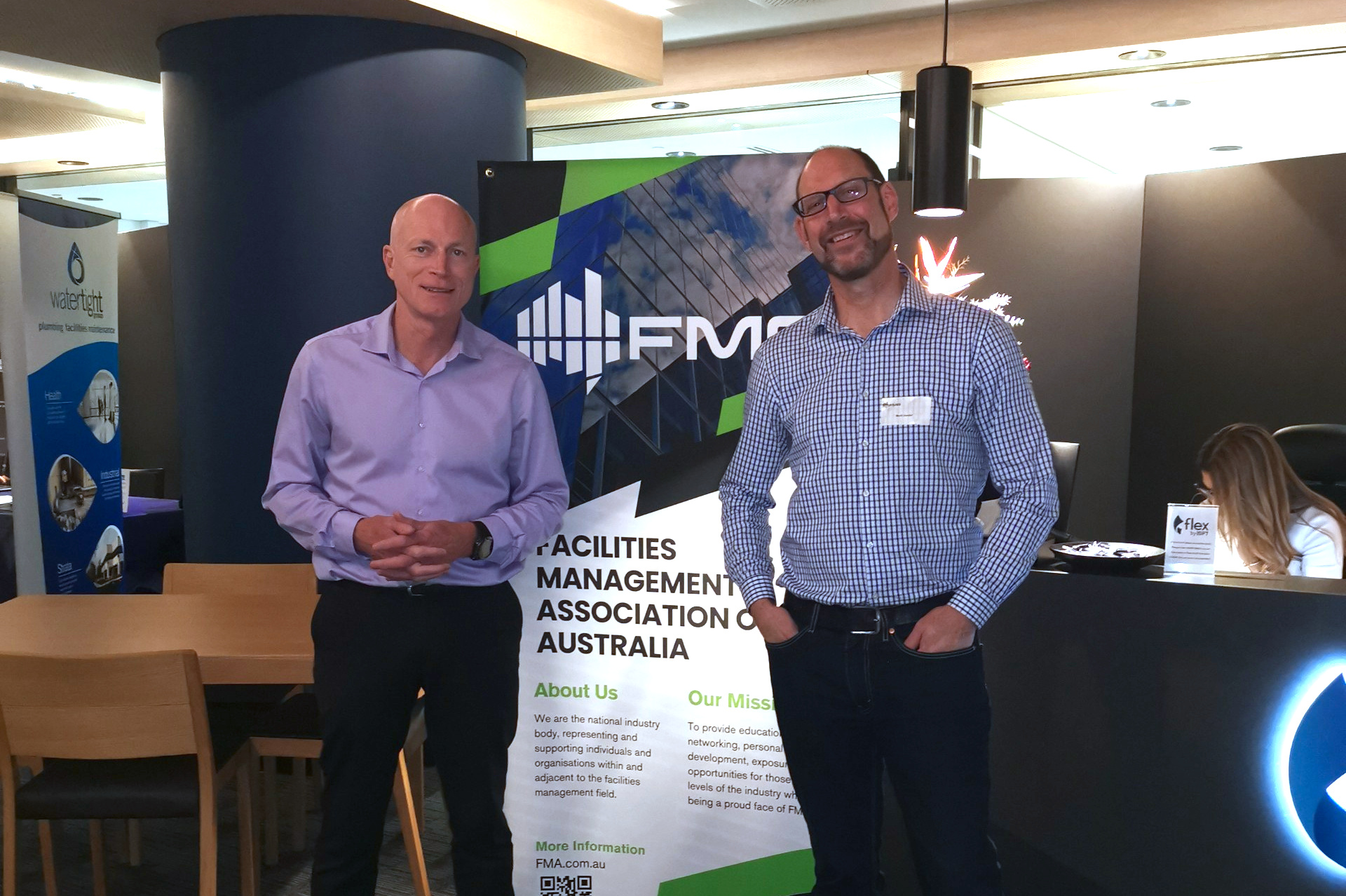
We know that looking after our buildings make sense, but in a world where new technology and innovation grab the headlines, how do we make it a priority?
As professionals in the HVAC&R industry, we are facing one of Australia’s big challenges on the road to net zero: decarbonising our building stock.
That said, the path for our sector is clearer than others. Many of the technologies we need are already on the market, rather than on the drawing board.
We have energy-efficient appliances such as heat pumps that allow us to switch from fossil fuels in buildings to electricity, slashing our Scope 1 (generated onsite) emissions.
As the grid decarbonises, the electricity we use in our buildings will also be less emissions intense, lowering our Scope 2 (offsite) emissions.
Embodied emissions – Scope 3 – are more of a challenge, but new materials and design approaches are coming to the fore.
So, plenty of reasons for positivity, even excitement. New technology captures our imagination. Heat pumps, EVs, engineered timber … when these are mentioned in industry forums, audiences sit up and take notice.
And yet, there are other excellent decarbonisation measures that don’t attract as much attention. For example, maintenance.
Can maintenance be sexy?
Unlike the buzzwords mentioned above, when maintenance is mentioned in group discussions, people’s eyes immediately seem to glaze over. Once or twice, I may have seen a stifled yawn.
Do they imagine someone tightening bolts on a piece of machinery? Ticking off a checklist? Reviewing the settings of a BMS? Maybe it all seems a bit ordinary.
And yet, that is one of its great advantages. If we are talking about technologies that are ready to be implemented in our buildings right now, better maintenance is top of the list. And the case for it is strong.
In terms of Scope 1 emissions, once we take fossil fuels out of buildings, the next item on the hit list is refrigerants. According to the Climate Change Authority’s Sector Pathways Review, in 2022 refrigerants represented about 9Mt CO2e or 32 per cent of the built environment sector’s Scope 1 emissions. A great way to address reduce refrigerant leakage is better maintenance.
We also know that maintenance has a massive impact on energy use – Scope 2 emissions. The Department of Climate Change, Energy, the Environment and Water (DCCEEW) has published excellent reports about the energy penalties of common faults in HVAC&R equipment. And the success of the NABERS Compulsory Building Disclosure program has shown how quickly energy use can be brought down in buildings when we take action.
Better maintenance can even help us reduce Scope 3 emissions. A well-maintained system lasts longer, meaning fewer replacements containing embodied carbon.
Defining maintenance
Why the apparent apathy then?
Perhaps it’s because people don’t have a clear idea of what maintenance is. As mentioned above, it covers many different activities.
AIRAH is keen to develop a case for maintenance, in the form of a fact sheet that can succinctly explain the benefits to government and other stakeholders. One of the challenges is incorporating all the different aspects of the topic.
For example, as AIRAH’s Big Data STG has told us – and as can be seen in this issue’s cover feature – improving the logic of a BMS can have a huge impact on energy use. Over at the Building Physics STG, they are investigating how fire safety maintenance can impact airtightness – and therefore overall system efficiency. The IAQ STG is working on HVAC hygiene, which affects the health of building occupants as well as emissions. There are many angles to this.
In late October, I attended a maintenance summit organised by the Facilities Management Association of Australia (FMA) to get a better feel for the topic. This is in line with AIRAH’s strategy to break down industry silos and strengthen connections with allied associations. Many thanks to the FMA team for facilitating my attendance.
The event was valuable in seeing more aspects of maintenance, in particular the parts that impact building owners, operators and occupants. During the breaks I asked other attendees how they defined maintenance, and I received many different answers.
For a long time, AIRAH has been a leader in this space through the development of DA19. We will continue putting forward the case for better maintenance, and would welcome the input of our members on the issue.
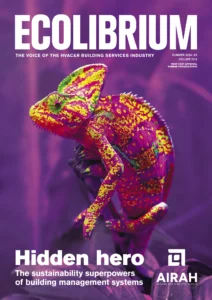
This article appears in Ecolibrium’s Summer 2024-25 edition
View the archive of previous editions
Latest edition
See everything from the latest edition of Ecolibrium, AIRAH’s official journal.