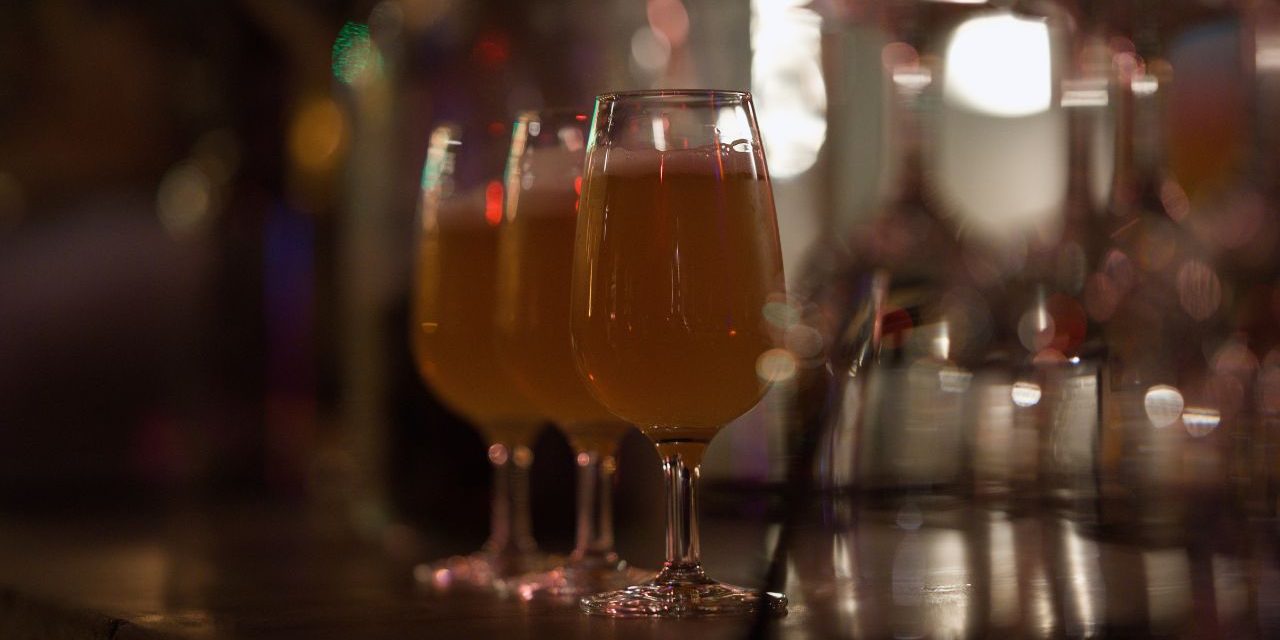
The electrification of 3 Ravens brewery in Melbourne could serve as a blueprint for other craft operations, as Nick Johns-Wickberg discovers.
If Melbourne is the hipster capital of Australia, then Thornbury might just be its hottest spot right now. Over the past few decades, the inner-north suburb has transformed from a semi-industrial, semi-residential area to a hub for cafes, restaurants and alternative nightlife, all while holding onto its working-class and multicultural roots. In 2024, Time Out named High Street – the suburb’s main thoroughfare – the coolest street in the world.
Nestled among the backstreet warehouses of Thornbury is 3 Ravens, the oldest independent brewery in Melbourne and one of the original producers of craft beer in Australia. Since it opened in 2003, 3 Ravens has been representative of the neighbourhood’s transformation.
A few years ago, the brewery underwent a transformation of its own. Here’s how 3 Ravens upgraded from an outdated, inefficient and disjointed brewing and HVAC&R setup to a revolutionary heat pump system that could provide a template for other craft producers around the country.
Time for an upgrade
3 Ravens began as a labour of love, with a self-described “nanobrewery” capacity of only 300L of production. It grew fairly organically from there – as demand for beer increased, so did the brewery’s need for production.
Bill Armstrong is the Production Manager at 3 Ravens, overseeing the day-to-day brewing processes.
“The original brewhouse setup was very organic,” Armstrong says. “We expanded it in 2013 to increase our brewing capacity, and while doing this latest upgraded we decided to keep the same brewing equipment while improving the systems around it.”
While 3 Ravens had always run an electric-only brewing setup, those electric processes were inefficient. A 15kW resistive element was used to preheat filtered water, then 55 kW of elements were used to further heat then boil the wort produced from that hot liquor and the mash ingredients. Two chillers operated independently to produce chilled glycol-treated water and chilled filtered water to operate all process and ingredient cooling services. There were several ageing electric reverse cycle R22 split systems to provide space cooling, as well as a cold storage facility.
In 2020, the brewers decided it was time to invest in revamping their equipment to improve efficiency and reduce their carbon footprint.
Jon Fettes is the founder of Regenerate Engineering, a Melbourne-based engineering consultancy that specialises in commercial and residential solar-integrated projects, including those that integrate with HVAC&R equipment such as heat pumps. He was the brains behind the brewery’s upgrade to an award-winning heat recovery and exchange system.
Fettes recalls his first impressions of the original equipment at the brewery.
“The scenario laid out in front of me on my fist visit was quite a shock, but in hindsight quite typical for a craft operation,” Fettes says. “I saw a large number of independent compressor systems, two chillers, a cool room DX system, five or six R22 split systems including two split ducted systems for office spaces (the company runs a co-working space on a mezzanine above the bar and brewery barrel room), a separate bar glycol tap system and limited heating or cooling in the bar area.
“The operation was ripe for an upgrade!”
It was clear that things needed to change, and the 3 Ravens team was keen to upgrade in the most sustainable way possible. Turning that dream into a reality was Fettes’s job.
Off with a bang!
Fettes shares a vivid memory of the first time he visited the brewery.
“From time to time in the brewery a sound like a pistol shot rang out,” Fettes explains. “The first time I heard it I jumped in fright, but all the staff around me continued on as they were! It was one of the chillers starting up. Over the couple of years I visited the brewery, that sound seemed to get louder as the equipment deteriorated further.”
This disjointed setup combined with the poor building fabric caused problems not just for the beer production itself, but also for working conditions in the surrounding areas, including the bar and the upstairs co-working space.
“In summer, the brew hall was uncomfortable with a lot of heat coming through the roof and the skylights, plus all the heat coming off the chillers and refrigeration equipment’s condensers in the hall,” he says. “The coworking space was a little drafty and uncomfortable at times with the HVAC having to work hard to keep up.”
Pushing the envelope
Fettes planned the brewery’s transformation out in several stages. The first was to improve the thermal performance of the building, which was an uninsulated converted warehouse that had never been designed to house brewing equipment.
In 2020, the brewery installed a “cool roof” – a white, highly insulated roof that significantly cut reliance on mechanical heating and cooling. During this transformation, 3 Ravens also installed a 74kW rooftop solar array that now meets the majority of its electricity needs.
The next step was a building fabric upgrade of the co-working space in 2021. This included installing insulation and airtightness sealing measures.
Fettes says the building fabric upgrade reflected the team’s holistic approach to the project, whereby they looked for potential energy savings across all aspects of the brewing process, including heat recovery and thermal storage.
“Where the basic principle of using both ends of a heat pump’s output and sizing storage to suit variations of repeating use patterns is elementary, this project type requires holistic thinking to value-add, covering more end-uses and adding further savings as a result,” Fettes says.
“This worked in a number of ways, including upgrading the coworking space’s building fabric. This brought thermal demand down enough to make it feasible to run space heating off system waste heat within the system capacity boundaries.”
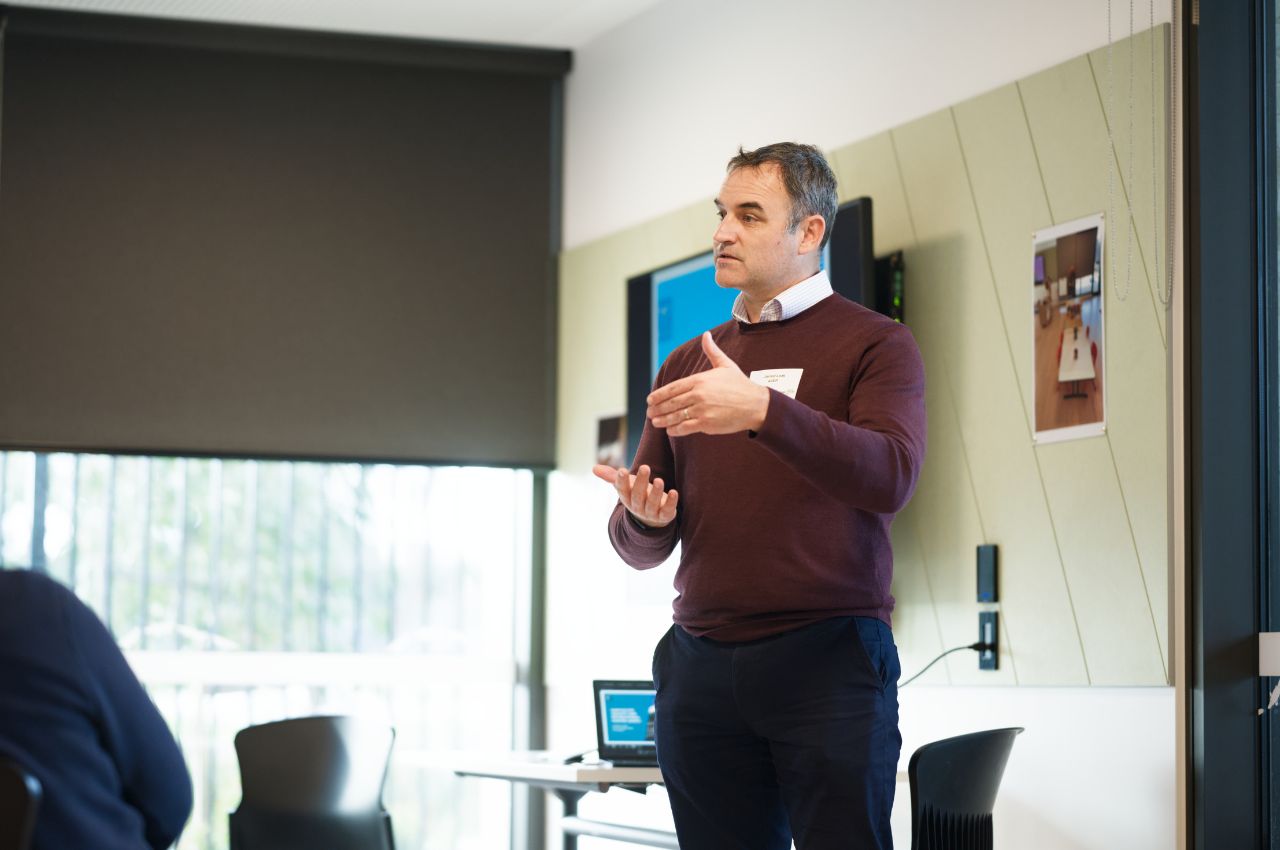
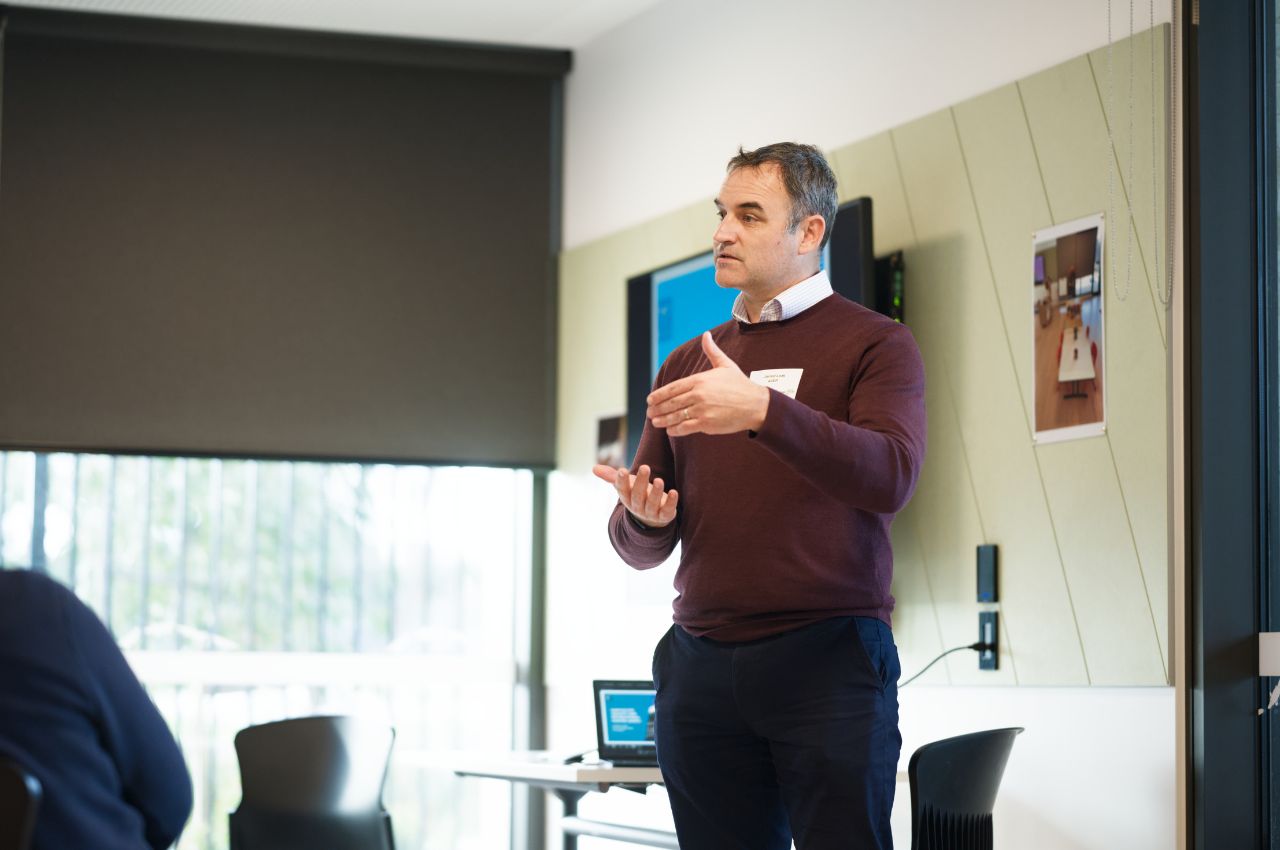
The changes
The final phase of the upgrade involved consolidating several pieces of old, inefficient equipment – two glycol chillers, two resistive elements and all the HVAC split systems – into one highly efficient 45 kW variable duty CO2 chiller heat pump. The system also includes an external adiabatic gas cooler to complete the CO2 cycle and an additional heat exchanger to intercept and use the mid-temperature thermal stream for HVAC purposes. To manage all this, the new brewing setup also includes a programming control logic (PLC) designed specifically for breweries.
The project involved updates to the brewery’s thermal battery and distribution systems:
- The standard-sized glycol tank had 29kWh of latent energy storage (phase change materials) added to increase storage size.
- Additional heat exchange coil in the cold liquor tank to facilitate further latent energy storage via ice building alongside glycol jacket.
- An inline heating heat exchanger to heat wort en route to the kettle.
- A new stratified hot liquor tank – additional to old hot liquor tank, which is now a batch tank
- Careful re-design of pipelines and tanks so that they can stratify correctly and the addition of multiple temperature sensors to monitor the state of charge of hot and cold thermal batteries.
There have also been changes to the brewery’s hydraulic thermal distribution and air handling systems:
- Fully redesigned balanced header glycol circuit, supplying cooling and fan coils for the hop freezer and cool room.
- Mid-temperature thermal loop and tempered cold glycol to supply fan coils in public spaces.
- Full HVAC in occupied spaces, which controls heating and ventilation levels with CO2 and temperature sensing sized by use of analytical energy modelling of spaces post building fabric upgrade.
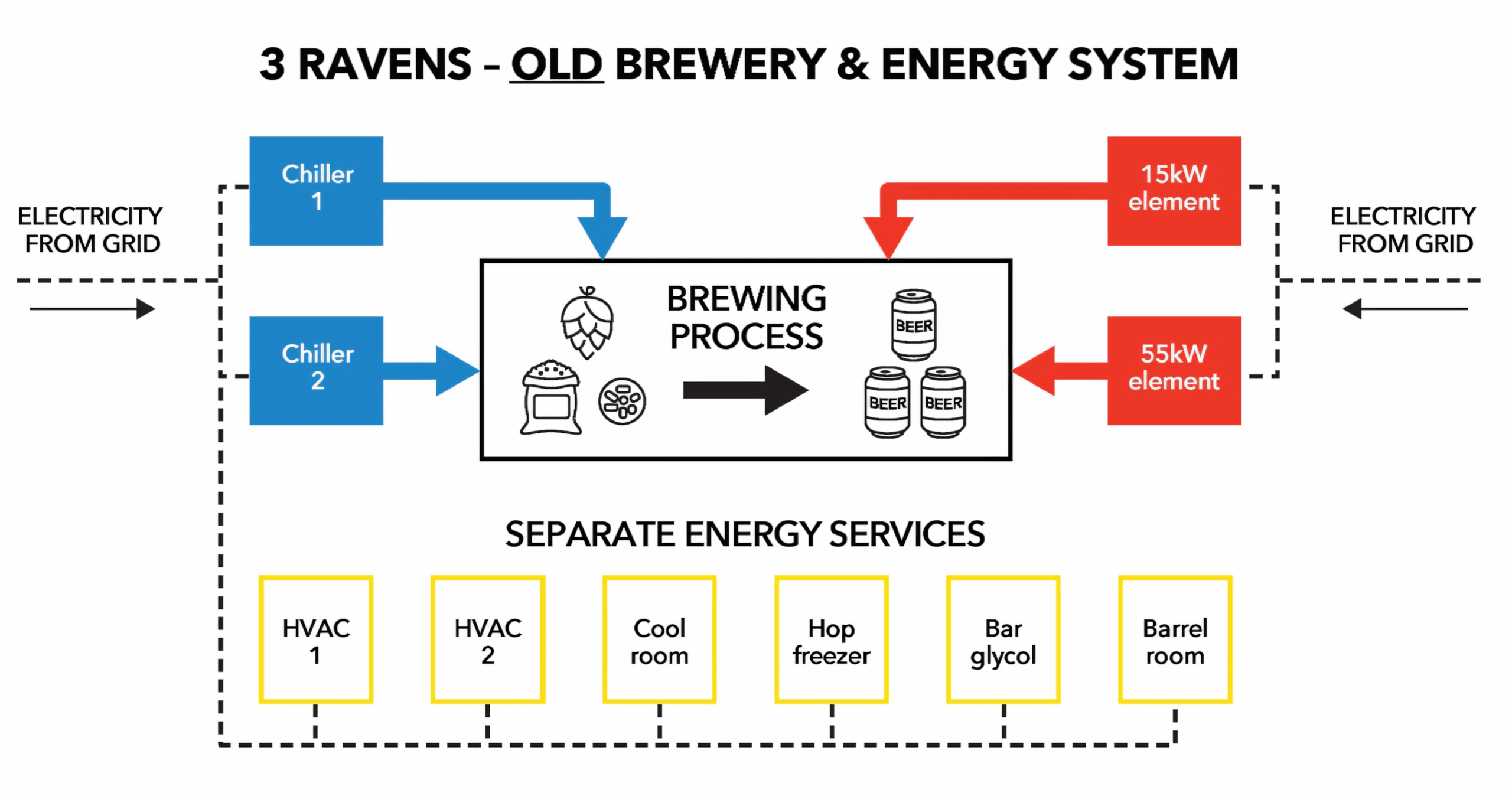
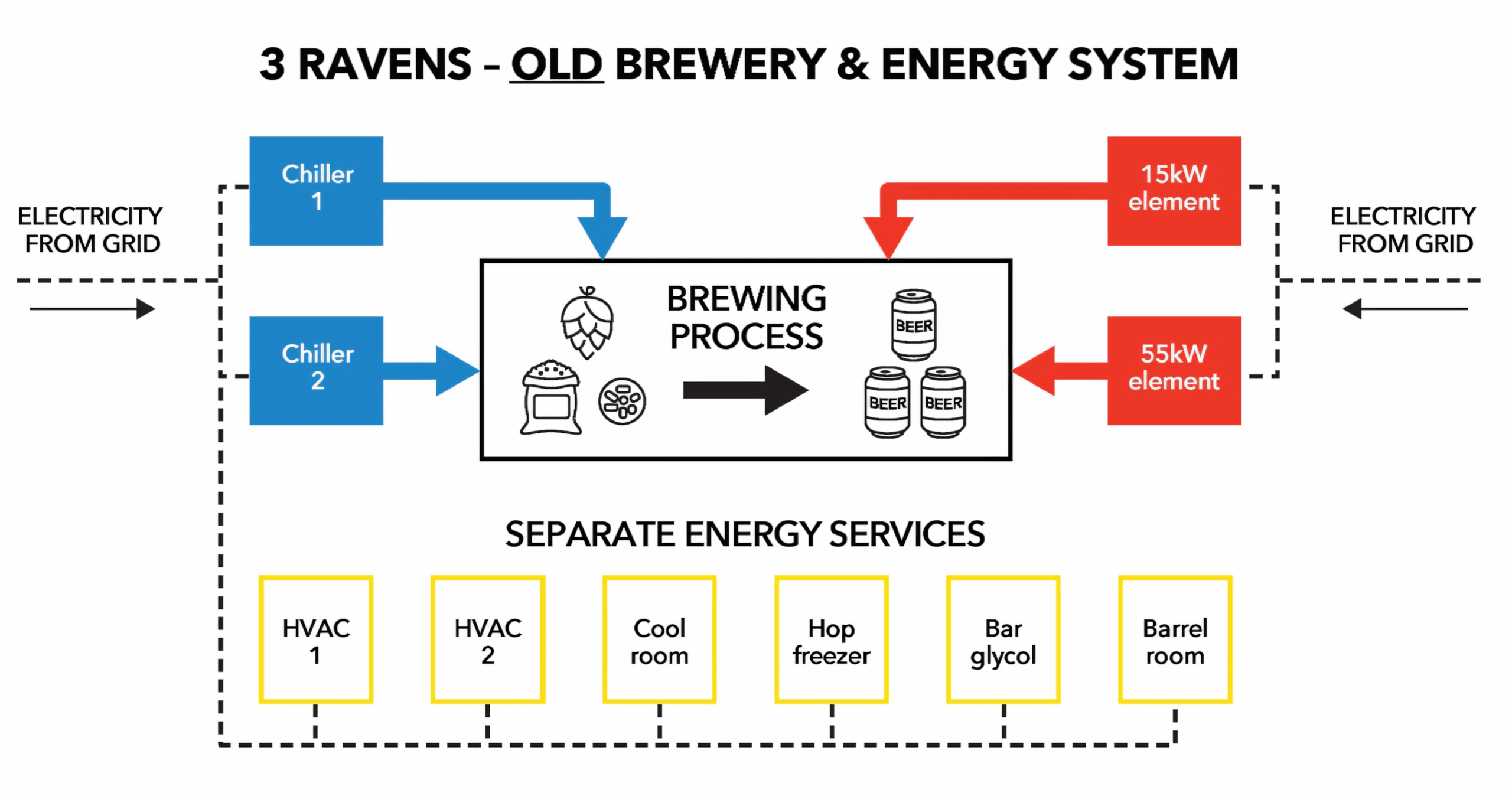
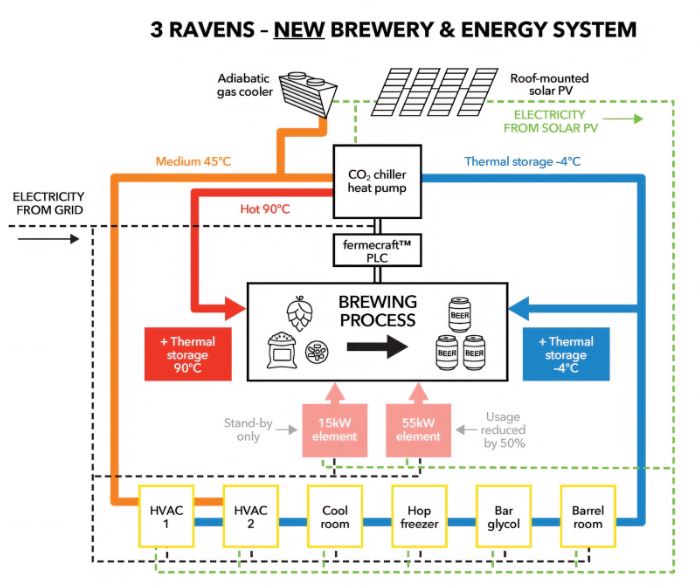
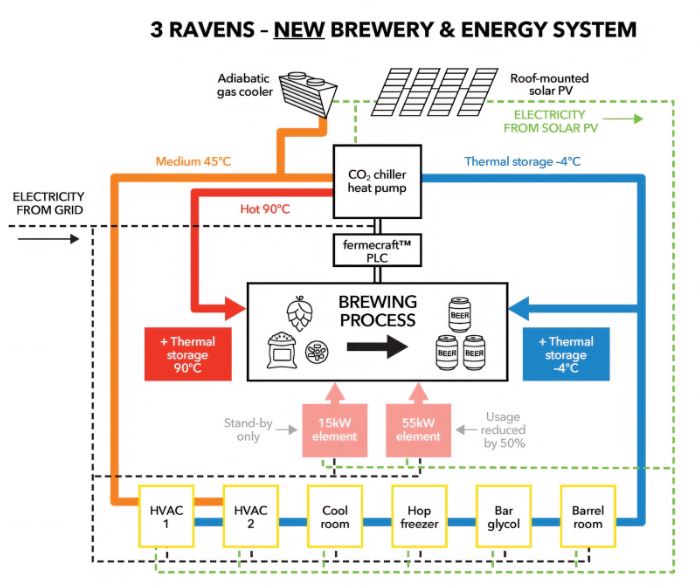
Licence to chill (and heat)
Where the old setup let process heating and cooling go to waste, the new chiller heat pump can capture and use waste heat and cooling from the brewing process to supply other heating and cooling needs in the brewing process and wider facility.
“The fantastic thing about the type of chiller heat pump used in this project is that it can simultaneously create heating and cooling at useful temperatures for various parts of the brewing process from a single refrigerant cycle,” Fettes says. “In this instance, it is also delivering a further waste heat stream to other rooms to help manage internal temperatures and comfort.”
The new system uses process heat for:
- Hot liquor production for steeping and mashing beer ingredients
- Heating up and vigorously boiling worth.
- Cleaning in place (CIP)
It uses process cooling for:
- Fermentation cooling (glycol system)
- Cold liquor production (potable system)
- Crash cooling processes (glycol)
- Cold conditioning (glycol)
Given that brewing is a batch process, with simultaneous heating and cooling needs across the brew hall, having a system that can make the most of process heat and cooling is a huge boost for efficiency.
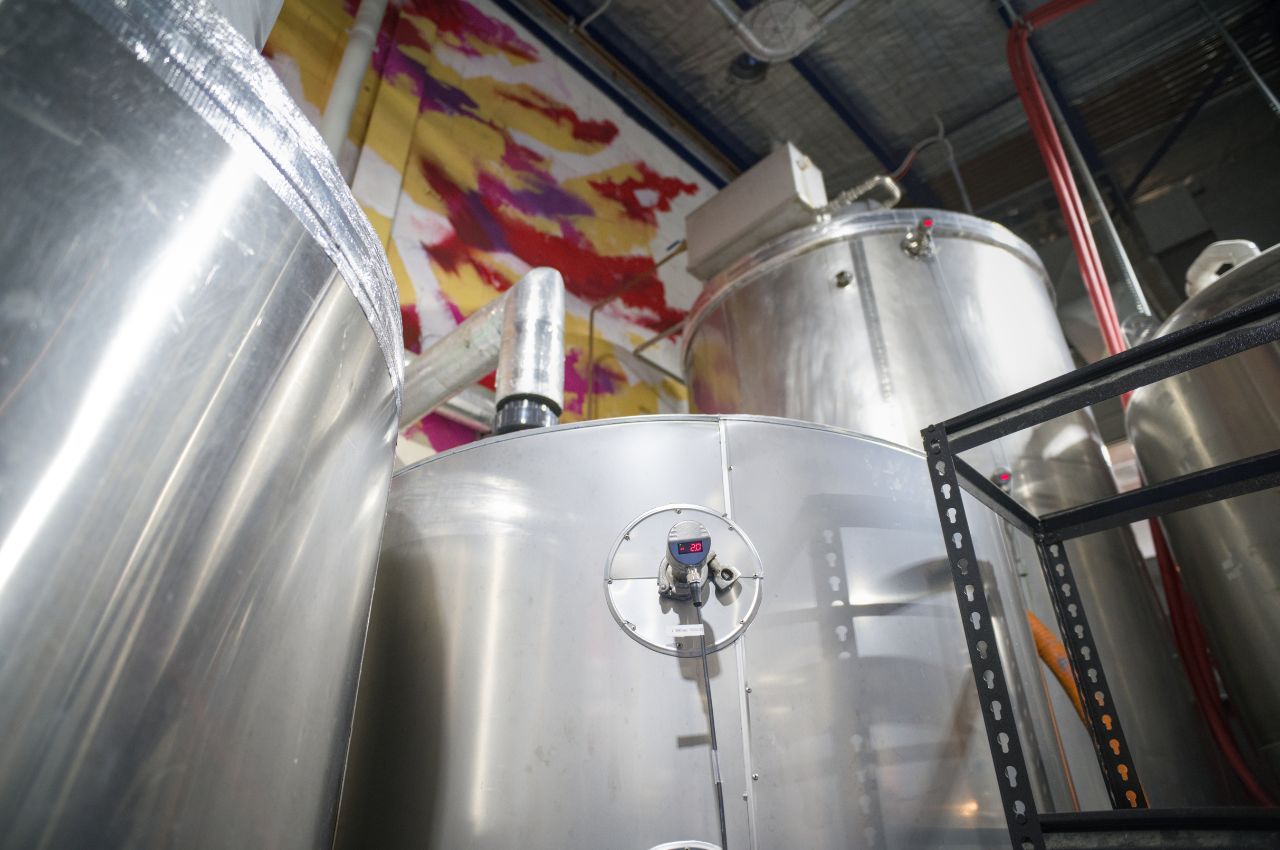
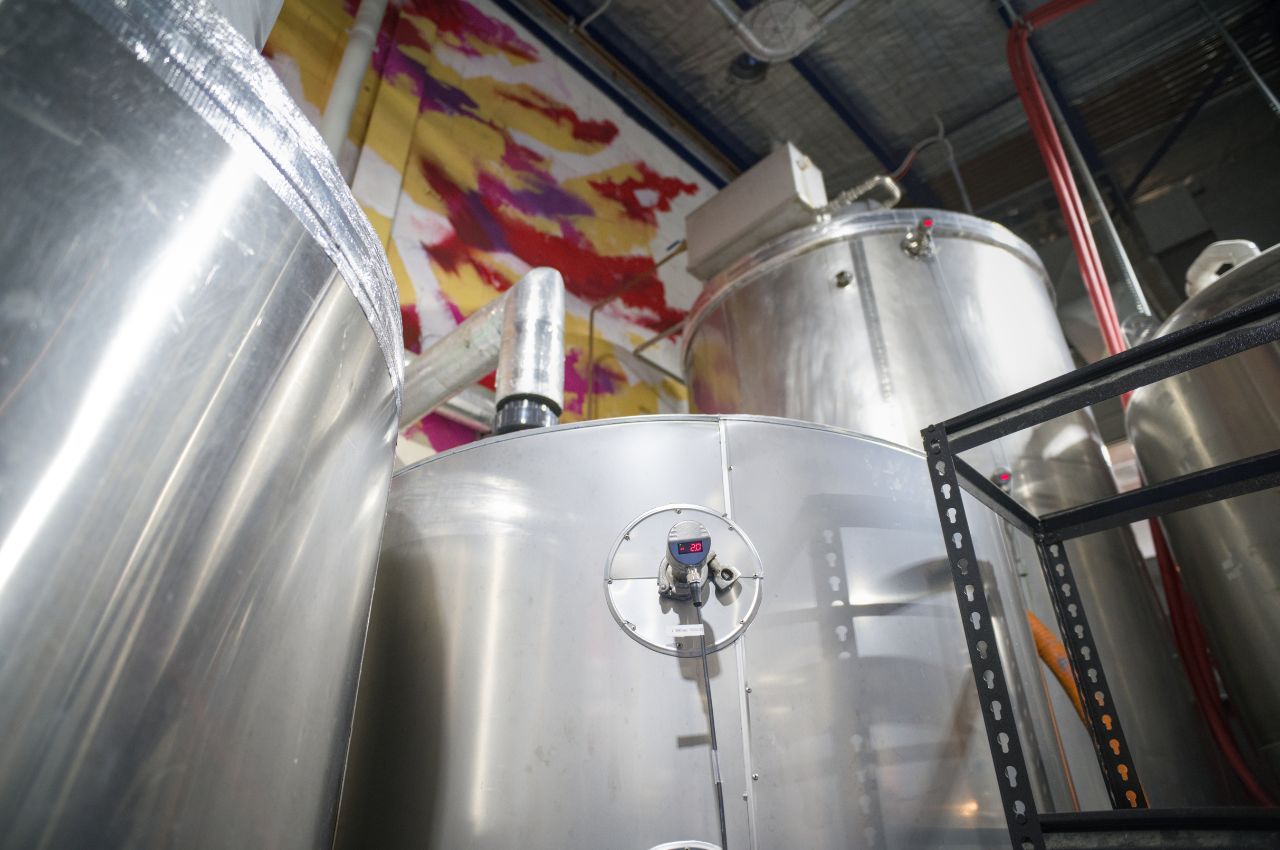
Worts and all
If you’re not familiar with brewing processes, you probably haven’t heard of wort before. Wort is the liquid extracted from the mashing process. In layperson’s terms, it’s essentially unfermented beer.
Managing the temperature of wort is vital, and different types of beer require the wort to be cooled to different temperatures. This is where the heat exchange and recovery system really comes into its own.
“While all breweries utilise heat exchangers to cool wort before fermentation, and preheat filtered water for mashing, this project expands on heat exchange as well as heat recovery,” Fettes says.
“The main heat recovery is from transcritical operation, where water is heated and stored at 90°C. For efficient operation, any CO2 refrigeration cycle requires the gas to cool to around 31°C before entering the compressor. Rather than relying on the mandatory gas cooler to do this for all situations, we chose to add an additional heat exchanger to produce mid-temperature water from this cooling operation, to be used when required for space heating.”
The wort heater heats the wort post-mash by 30°C to 85°C using the stored renewable heat in the thermal battery. Due to this process (lautering) having a relatively slow and steady flow, it is well suited to this heat exchange process.
“This is brand new territory in small-scale brewing,” Fettes says. “By saving 20 minutes or so per brew, it presents productivity as well as energy cost benefits at a relatively low cost.
The results
Having invested so much energy and creativity into designing this revolutionary CO2 heat pump brewing setup, Fettes was keen to see the fruits of his labour. So far, the results have spoken for themselves.
“The brewers are delighted with the wort heater, and volumes are up, as expected,” Fettes says. “Our design of the glycol loop with its balanced header has made adding brewing vessels easy.”
He also points out that the thermal storage system is working as planned, not only improving performance and energy use, but making the whole process quicker and more efficient.
“The extra insulation we added to the re-purposed brewing vessels has made the thermal storage tanks excellent, with very little drop in temperature over a weekend. This means they can go straight into a mash in on Monday morning using stored heat.”
3 Ravens is also thrilled with how the system has turned out.
“From a brewer’s perspective, the biggest outcome of the upgrade has been an increase the amount we brew in one day,” Armstrong says. “Depending on the type of beer, we’ve tripled our capacity to make wort, mainly due the heat storage and recovery systems.”
“We have also seen a fairly large reduction in energy consumption per litre brewed,” Armstrong adds. “We’re looking to better measure quantify this saving in energy and emissions in the future.”
A worthy investment
As Fettes points out, the 3 Ravens upgrade required not just blue-sky thinking, but lots of planning and significant financial support from several parties.
“When I met them, 3 Ravens already had the beginnings of a plan to double or triple their production – which would require a significant upgrade – but hadn’t firmed up technical details,” Fettes says. “The stars aligned with an agreement that if I could help secure the additional funding via grant assistance then we could do the centralised renewable heat system.
“I conceived the project and arranged funding for feasibility studies before project managing the design by my team, which included subcontracted refrigeration expertise,” Fettes says. “The 10-hour engagement with my company that resulted basically had the whole process mapped out through some key recommendations.”
Jarrod Leak is the CEO of the Australian Alliance for Energy Productivity (A2EP). A2EP conducted the pre-feasibility study and part of the feasibility study for the 3 Ravens upgrade, which were funded in part by an ARENA grant that supported more than 25 energy efficiency projects.
Leak notes that, without funding from bodies like ARENA, Darebin Council, and AusIndustry, it would be extremely difficult to get a project like the 3 Ravens upgrade off the ground.
“Grant support programs are essential when you want to kickstart a new industry like industrial heat pumps,” he says. “The outcomes from the pre-feasibility studies are quite uncertain, making them hard to fund by companies, and there is no ‘first mover advantage’ either.
“These-first-of-their-kind projects are typically 20–30 per cent higher in costs than later projects, as they require learnings from all parties involved: the engineers, the suppliers and the owner. First-off designs often need to be more conservative as well, which means having more instrumentation, more conservatively sized equipment and larger contingency to allow for some unforeseen costs.”
A viable blueprint
This revolutionary heat recovery system is designed specifically for a small brewery. Fettes points out that, with many craft breweries looking to decarbonise, there is huge potential for this approach to be replicated.
“Since the brewing process is built around a well understood chemical reaction, solutions that work in one can be transferable to others,” Fettes says. “In this vein, we have used our thermal and mass balance model to develop a small brewery kit for craft breweries. This includes the simplified chiller strategy.
“Moving to a slightly larger scale there is promise in micro-scale mechanical vapour recompression, which would increase the scope of the technology suite to include the boiling and distillation processes at extremely high COPs. But this has yet to be fully developed.”
Leak agrees that cleverly designed heat pump systems are a great option for breweries that are looking to reduce both their bills and their carbon footprint.
“Many breweries are looking to reduce their energy costs and emissions with heat pumps,” he says. “We expect there to be a steady increase of technology adoption over the years as existing equipment reaches the end of life or breweries expand.”
However, he points out that no two projects are the same; they require careful planning and feasibility studies to determine whether they should go ahead and what the best approach should be.
“There are over 600 craft breweries in Australia and most of them could make this change. But is it an economic no brainer? No,” Leak says.
“For the investment to make sense, a full energy productivity business case needs to be done to incorporate factors such as the value of increased production, the cost of replacing the existing equipment, the value of the cooling available from the heat pump, the safety and reliability aspects, the carbon credit certificates, and the potential new sales markets with lower-carbon beer.
“A simple payback on energy savings alone for a like-for-like replacement will almost never make business sense.”
For 3 Ravens, the project has not only made sense, but has revolutionised the brewery’s operations while helping it meet its sustainability goals.
“We’ve always tried to use local ingredients and do things as sustainably as possible, so reducing our carbon footprint is something we’re passionate about,” Armstrong says.
“This whole project started off as an exercise in resurfacing decayed concrete, and it snowballed from there once Jon Fettes got involved. We realised that we had the opportunity to do something unique in terms of making the craft brewing process more sustainable and efficient. To have an end result like this is incredible.”
Transferrable skills
While it’s clear that the principles that underpin the 3 Ravens heat recovery and exchange system could be applied to other craft breweries, a similar approach could also make sense in different applications.
“There are plenty of other industries where heating and cooling processes are required concurrently, and this kind of system would work well,” Fettes says. “This includes bakeries, where dough proving and refrigeration fit well together, as well as dairies and other food processing facilities where heating or cooking complements cold storage. It all starts with the need to develop a thermal mass, energy and power balance model for the process in question.
Fettes points out that a similar philosophy could also improve efficiency in applications beyond food and beverage production.
“Widening the scope further there are complimentary systems like building a cold store next door to a swimming pool, where essentially you get one half of the service for free. This is part of the future of heat pump technology – finding smarter ways to use both sides of the heat pump’s output.”
Project at a glance
The personnel
Client
3 Ravens Brewery
Project design/ideation
Regenerate Engineering
Building fabric thermal modelling for HVAC system
Regenerate Engineering
Energy consultant
Regenerate Engineering
Refrigeration engineering
Minus40
Refrigeration installation
Minus40 Projects
Feasibility studies
Australian Alliance for Energy Productivity (A2EP)
Concept funding
Darebin City Council
Feasibility funding
The Australian Renewable Energy Association (ARENA)
Project funding
AusIndustry, Agriculture Victoria
The equipment
CO2 chiller heat pump
Enex
Adiabatic gas cooler
Enex
Programmable logic controller (PLC)
Fermecraft
Hydraulic fan coils for space heating and refrigeration
Temperzone, Bitzer
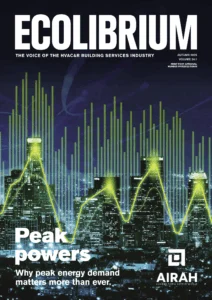
This article appears in Ecolibrium’s Autumn 2025 edition
View the archive of previous editions
Latest edition
See everything from the latest edition of Ecolibrium, AIRAH’s official journal.