Meet this cool new (meta)film star
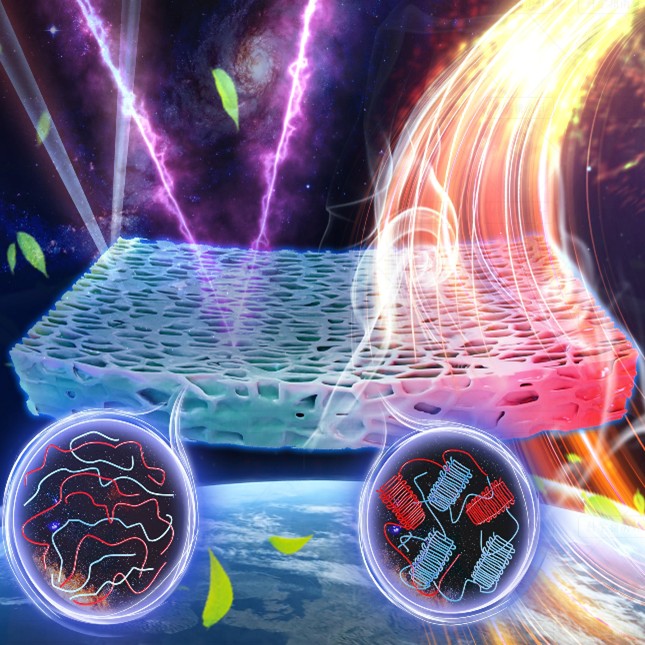
Ecolibrium speaks to Yangzhe Hou, part of a research team that recently developed a bioplastic metafilm with fascinating cooling properties.
The team consists of researchers from the University of South Australia (UniSA) and Zhengzhou University in China. Their study – published in Cell Reports Physical Science – shows that the prototype bioplastic metafilm is a sustainable and long-lasting material that can passively reduce temperatures by as much as 9.2°C during peak sunlight hours.
Constructed from polylactic acid (PLA) – a common plant-derived bioplastic – the fully biodegradable metafilm is fabricated using a low-temperature separation technique that reflects 98.7% of sunlight and minimises heat gain.
The metafilm can be applied to buildings, equipment and other surfaces. Modelling by the research team shows that it could reduce building energy consumption by up to 20% per year in some of the world’s hottest cities.
Yangzhe Hou, the UniSA PhD candidate who led the research, spoke with Ecolibrium about the bioplastic metafilm, its potential real-world applications, and what still needs to be done.
Ecolibrium: How is the bioplastic metafilm applied to surfaces? Can it be seen or felt, or is it too thin to notice?
Yangzhe Hou: This bioplastic metafilm has a thickness of approximately 500 microns and appears uniformly pure white. Internally, it features a network structure with a mesh size of around 5 microns or smaller, making it both visibly distinct and tactile. It is suitable for application on surfaces of cooling-demanding facilities, such as buildings or mechanical equipment. To ensure effective adhesion, the use of commercial-grade adhesives is recommended during installation.
How physically resilient is the metafilm?
While we do not yet have direct tensile or elasticity measurements for the metafilm, its tactile properties and handling behaviour suggest a certain degree of flexibility – it can be bent or folded without cracking, indicating sufficient mechanical compliance for potential surface applications. Additionally, we have conducted preliminary durability tests under accelerated conditions, including UV chamber aging and acid treatment, which the metafilm withstood without significant degradation. These results support its initial physical resilience in controlled environments.
However, outdoor weathering tests under real-life conditions have not yet been completed and remain a key focus for future work. As this study represents a proof-of-concept at the laboratory level, further mechanical and environmental evaluations are needed to validate long-term performance in practical applications. The current results are promising, but this is an early-stage success that lays the groundwork for subsequent development and scaling.
What further research is required before you could start to look at practical applications of the bioplastic metafilm?
In practical applications, cost reduction is a key priority. PLLA (poly-L-lactic acid) is the most commonly used form of polylactic acid on the market, whereas PDLA (poly-D-lactic acid) is its stereoisomeric counterpart. High-purity PDLA is significantly more expensive than PLLA, while lower-cost commercial PDLA often has reduced stereochemical purity, which can adversely affect the crystallisation behaviour and thus the structural performance of the metafilm.
Another major consideration is scalability. At present, the metafilm has only been demonstrated at laboratory scale. Although the low-temperature phase separation (LTPS) process requires no complex equipment – only a refrigerated chamber – scaling up production is constrained by mould dimensions and cooling chamber volume.
To address this, we plan to explore coating-based fabrication methods – such as casting or doctor-blading the formulation onto clean substrates like glass or flexible plastic films. This strategy may offer a more scalable and continuous pathway for future industrial production.
Further research will focus on optimising the parameters required for such coating processes, ensuring microstructure control and functional performance over large areas, and validating long-term durability under realistic environmental conditions. These steps are essential before practical deployment can be considered.
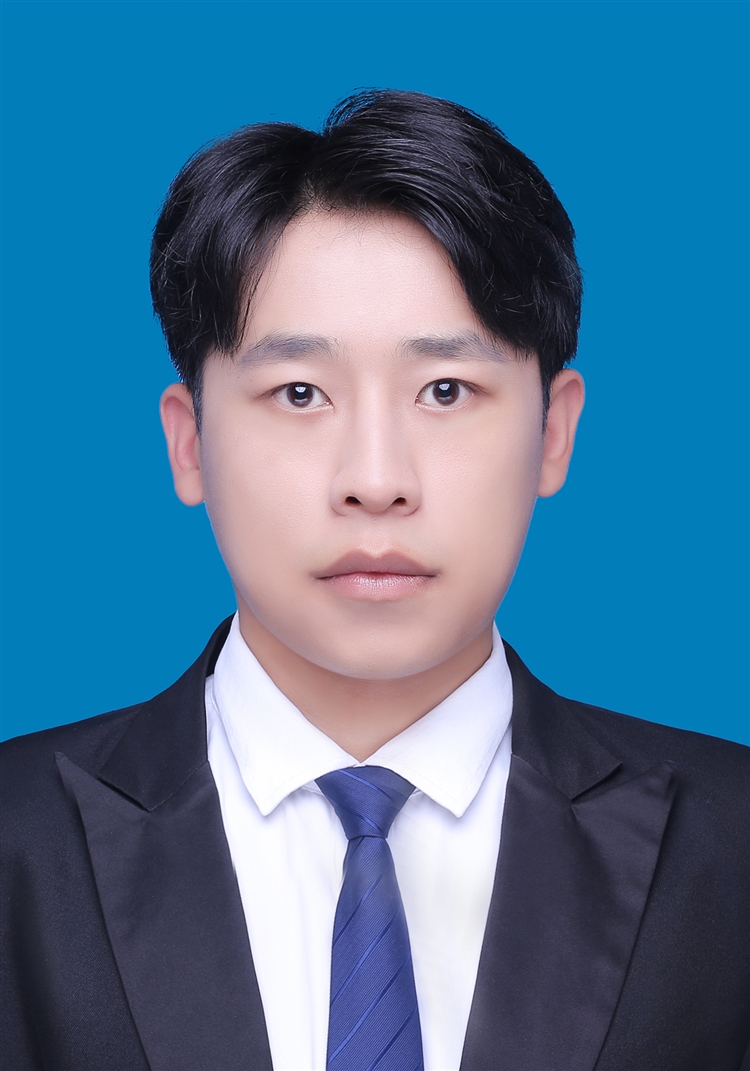
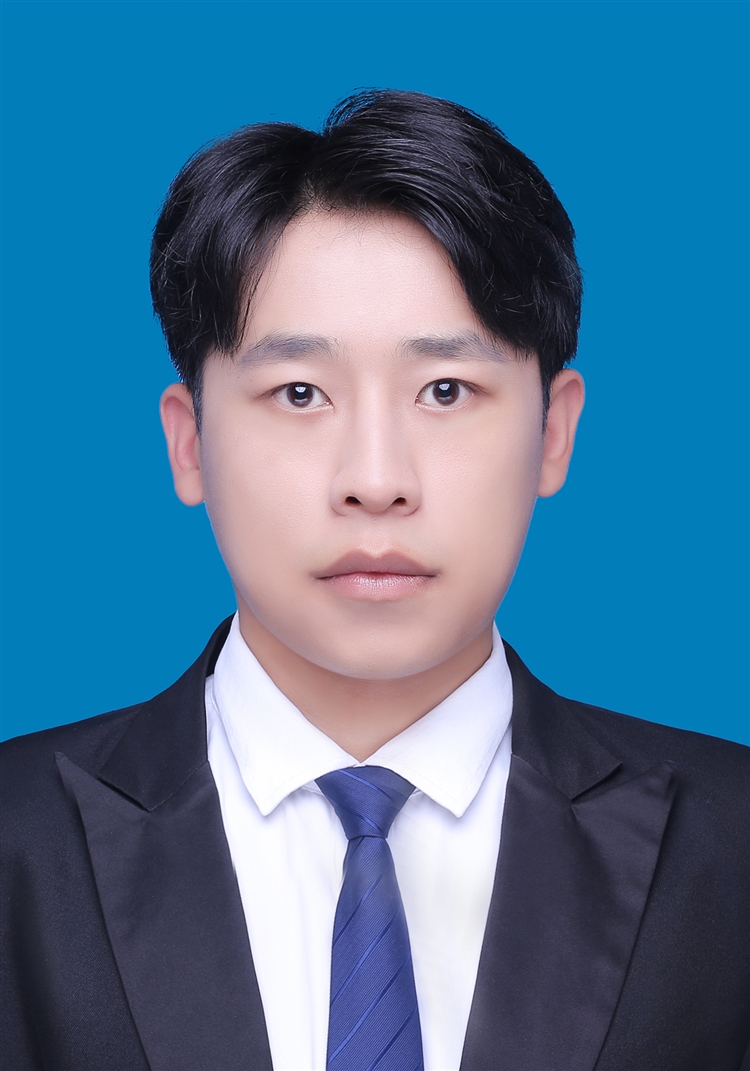
What kind of safety tests do you still need to conduct? Are there any potential issues around flammability, toxicity to humans, or the compounds that the metafilm biodegrades into?
Flammability testing is necessary for this metafilm. Since the initial research design did not account for fire resistance, its use in architectural applications is currently limited. Like most organic polymers, the metafilm remains inherently flammable, which presents a potential safety concern.
Furthermore, although the fabrication process involves organic solvents, these are fully evaporated and removed during film formation. Importantly, polylactic acid, the base material of the metafilm, is a commercially available and widely recognised biodegradable polymer that poses no environmental risk after use.
Do you envisage that this bioplastic metafilm could one day become commercially available? Could it eventually be spray-coated or painted onto existing buildings, or incorporated into new building materials?
While the bioplastic metafilm shows significant promise for architectural applications, it is important to note that this work is still at the stage of fundamental research. The current study demonstrates a proof-of-concept success at the laboratory scale, offering valuable insight into the structural design and radiative cooling potential of such materials. However, several key challenges must be addressed before commercial implementation can be considered.
One of the main hurdles is the relatively high cost of high-purity PDLA. Exploring the feasibility of lower-cost, industrial-grade PDLA – without compromising functionality – will be essential for future scalability.
In terms of application, while the current fabrication relies on mould-based casting, we are planning to explore transforming the metafilm into a coating or paintable form.
Such a strategy could enable surface integration onto existing building structures or incorporation into next-generation construction materials through scalable manufacturing methods like roll-to-roll processing or spray coating.
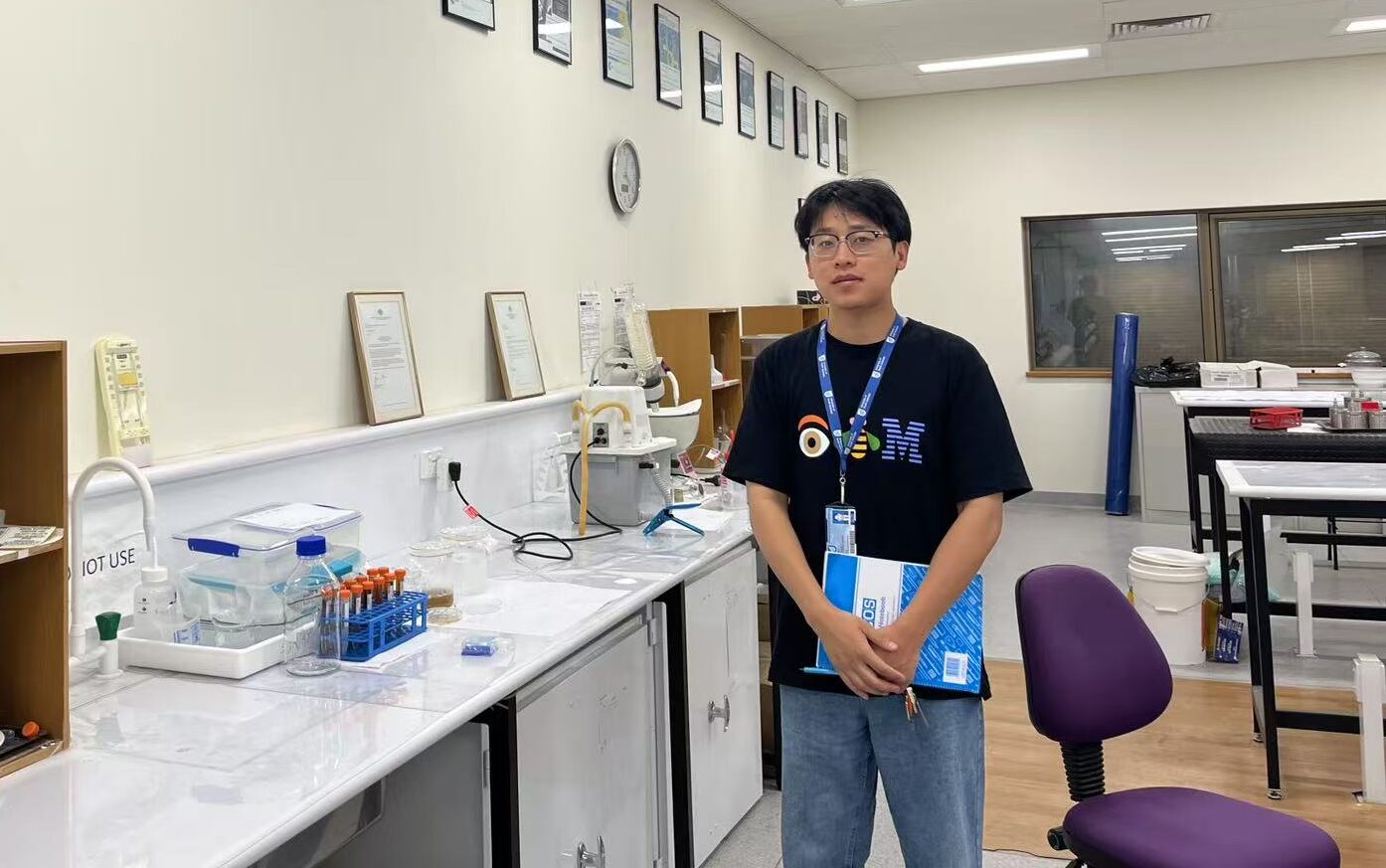
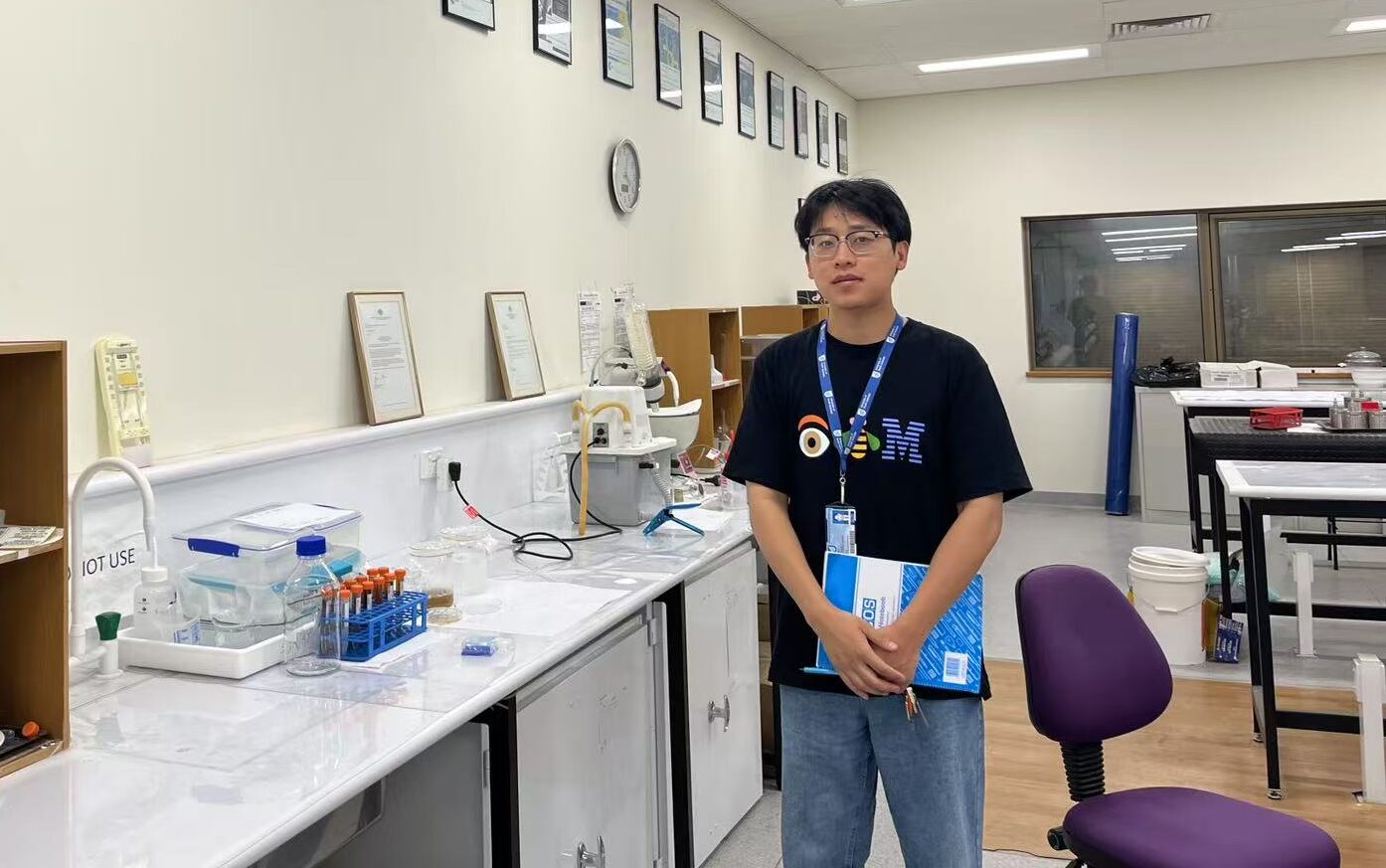
Overall, the metafilm holds strong long-term potential for building energy efficiency and climate resilience. However, realising commercial viability will require further research in materials formulation, scalable processing, and long-term durability under real-world conditions.
If the metafilm were to be widely adopted in the future, how do you predict this would affect phenomena like the urban heat island effect?
The metafilm was originally designed for applications involving direct sunlight exposure. Its optical properties allow it to emit heat through the atmospheric window into cold outer space, thereby helping to mitigate – rather than worsen – the urban heat island effect.
This effect arises in part because materials like concrete and asphalt differ from natural landscapes in their thermal (e.g., heat capacity and conductivity) and radiative (e.g., albedo and emissivity) properties, disrupting the urban energy balance and leading to elevated temperatures. By reflecting most incoming solar radiation and efficiently emitting thermal energy, the metafilm is intended to help restore that balance and reduce urban heat buildup.
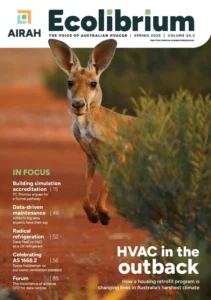
This article appears in Ecolibrium’s Spring 2025 edition
View the archive of previous editions
Latest edition
See everything from the latest edition of Ecolibrium, AIRAH’s official journal.