Computational fluid dynamics modelling of ventilation in road tunnels: enhancing air quality and safety
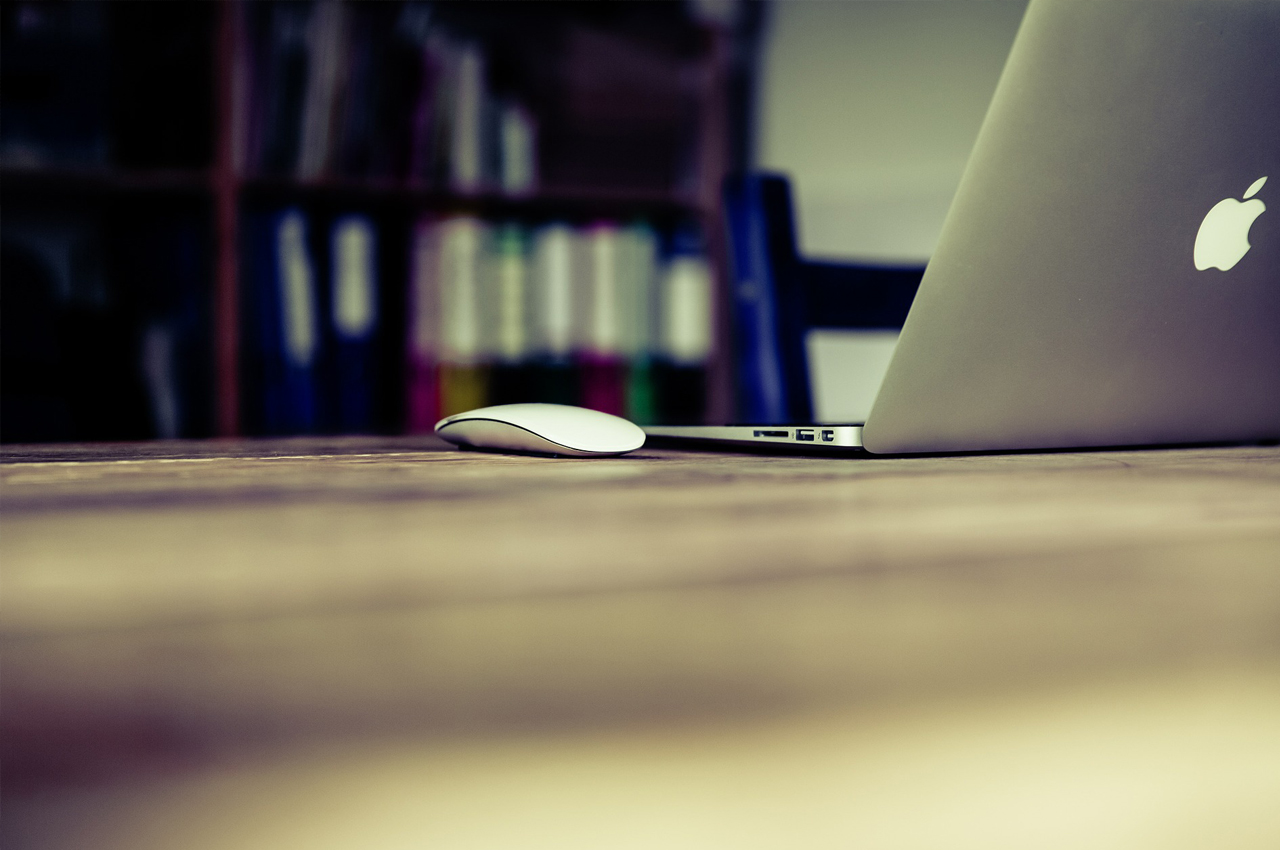
Ventilation units within vehicle tunnels play a pivotal role in ensuring safety and optimal air quality for occupants. These units are used to assist with propelling air from one end to the opposite end of the tunnel.
Computational fluid dynamics (CFD) has emerged as an invaluable design tool for engineers and stakeholders, offering simulated insights and data to optimise safety and efficiency in tunnel projects. This paper emphasises the advantages of CFD for road tunnel ventilation design, showcases a case study involving impulse fans, and highlights the positive effects on project costs and overall tunnel ventilation performance.
Introduction
Road tunnels constitute vital components of modern transportation networks, ensuring traffic flow and urban connectivity. Equipping these tunnels with well-designed ventilation systems is of utmost importance.
The ventilation system functions by drawing in fresh air and directing it towards the opposite end of the tunnel. This ensures that the tunnel is well ventilated and safe to occupy. Occupation of tunnels is typically described in one of two scenarios: normal and congested.
Maintaining an appropriate ventilation rate is crucial to keeping pollutant levels below critical thresholds for the health of tunnel occupants in normal and congested modes. Adequate capacity is also necessary to protect tunnel occupants from fire hazards during emergency mode. The design of the ventilation system should be based on either the traffic emission data or the peak air volume required in an emergency situation, with priority given to the higher value. Consequently, the equipment must possess the adaptability to meet immediate traffic demands over the next five years and be amenable to adjustments that align with changing traffic patterns and volumes throughout the facility’s operational lifecycle [1].
In normal mode, in tunnels with unidirectional traffic, vehicle movement assists the ventilation system by generating a piston effect. This effect enhances the ventilation system’s performance and should be thoroughly studied and considered during the tunnel’s design process. In some cases, this natural airflow might be enough to manage in-tunnel air quality [2]. In congested and emergency modes, however, it is the ventilation system that must solely manage tunnel ventilation, particularly in cases where there is no environmental pressure difference between the two ends of the tunnel.
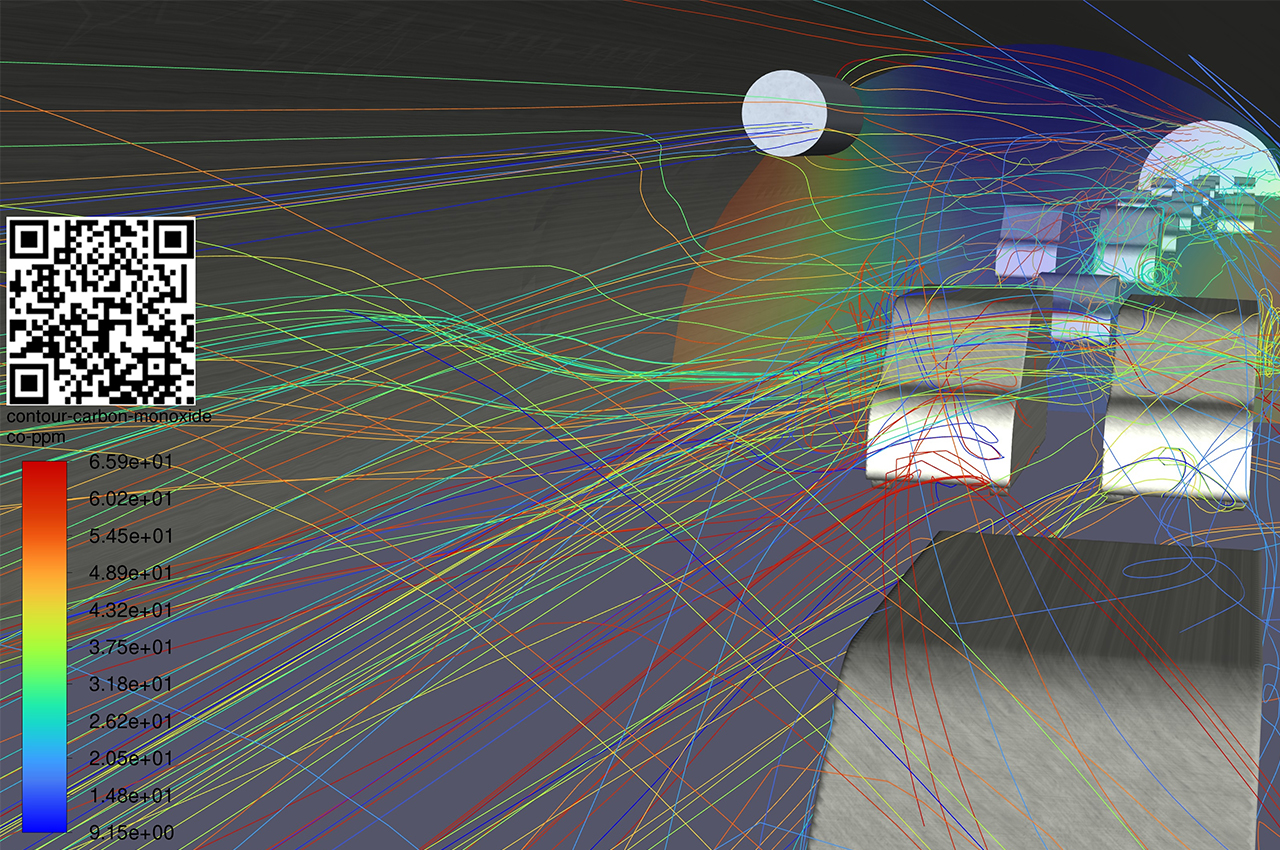
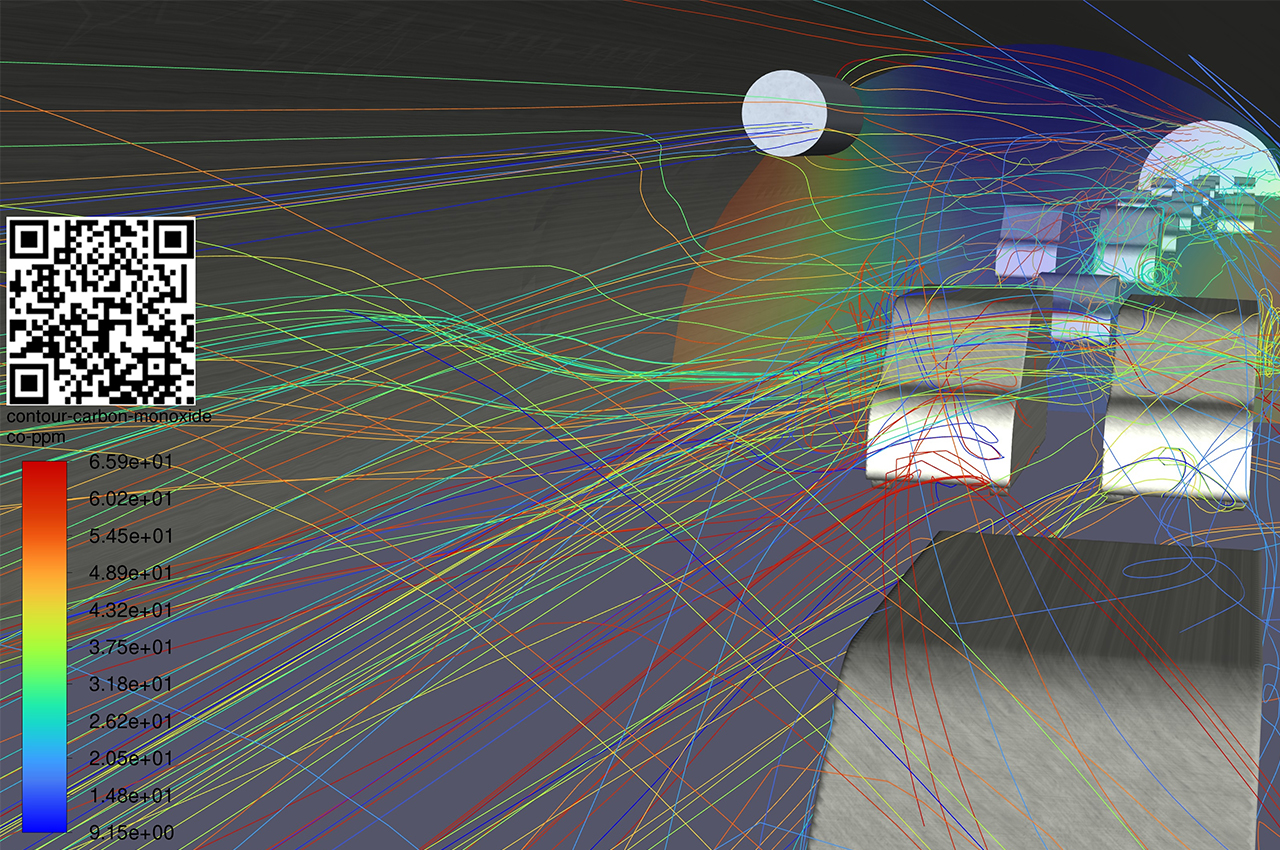
Design
Guidelines provide valuable assistance to designers in formulating ventilation system requirements for air quality and fire safety. An effective design must ensure that design factors such as emissions concentration – carbon monoxide (CO) and nitrogen oxide (NOx) levels – and visibility, remain in a safe range specified in local standards [3, 4]. These factors depend on predicted traffic load, predicted vehicle fleet emission rate, tunnel geometry, wind conditions and the design year.
Backlayering is a phenomenon where smoke and hot gases move counter to the direction of the ventilation airflow [5]. The ventilation system must prevent fire backlayering, allowing occupants to safely evacuate the tunnel. ASHRAE guidelines provide equations to compute critical velocity for fire safety, considering fire load and tunnel geometry [6]. These guidelines encourage the use of CFD to accurately assess smoke and temperature distribution under steady and transient conditions.
Safety
Designing a ventilation system for fire safety is a delicate task, critical to safeguarding tunnel occupants from high levels of hazard. Although preliminary designs can be achieved using semi-empirical formulas, it is highly recommended to validate designs through CFD simulations in situations where the system’s effectiveness is not apparent from manual analysis. An effective ventilation system must prevent fire backlayering, as previously noted.
Figure 1 is an example that illustrates this concept using impulse fans in road tunnel ventilation.
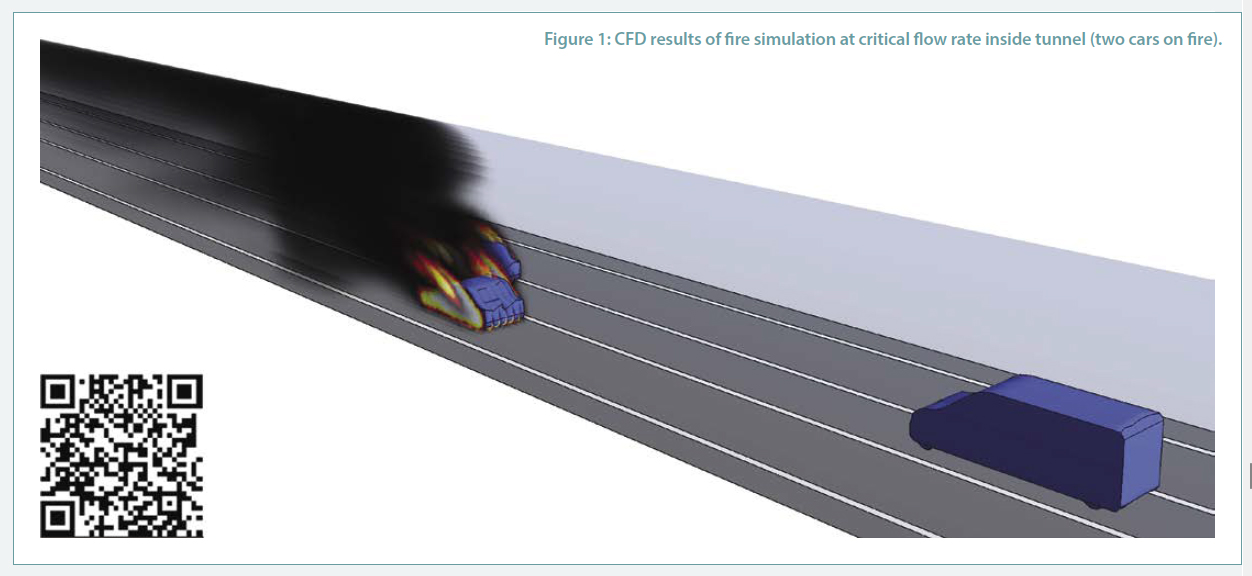
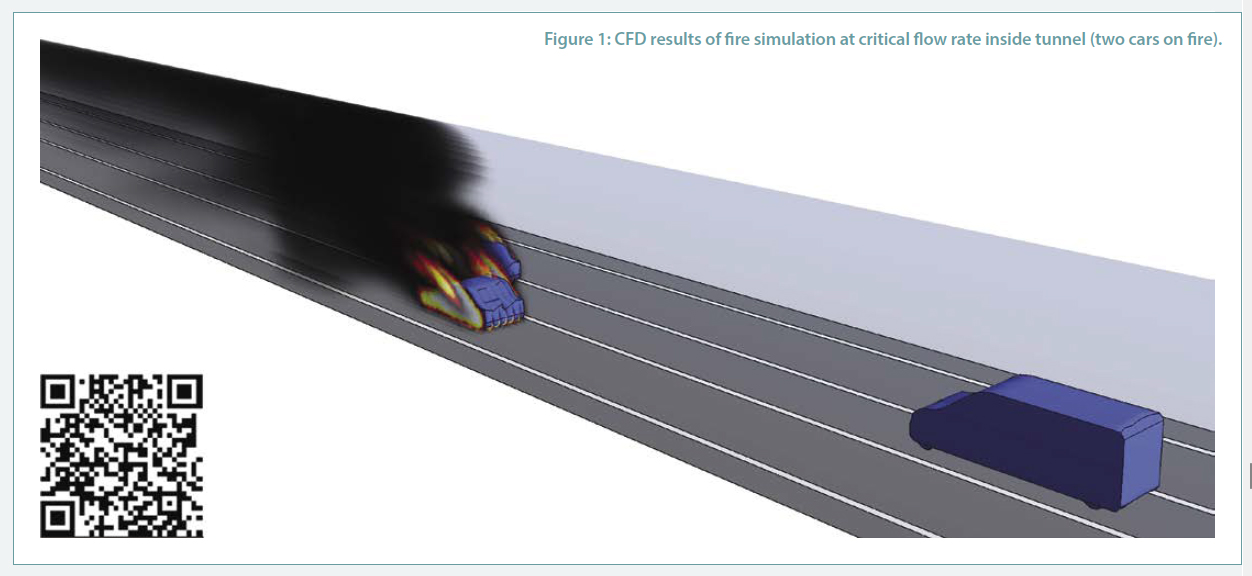
Results are derived from an in-house CFD simulation conducted on a sample road tunnel (geometries are to scale, though the tunnel section isn’t tied to a specific road). Modelling the tunnel under fire conditions (with burning cars) and comparing the results against ASHRAE design standard [6], which specifies the critical velocity as equations (1 and 2), demonstrates the system’s efficacy.
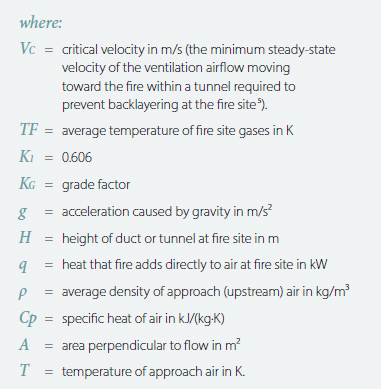
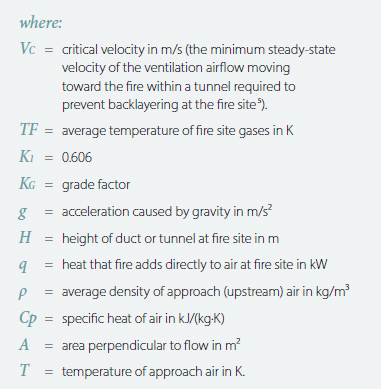
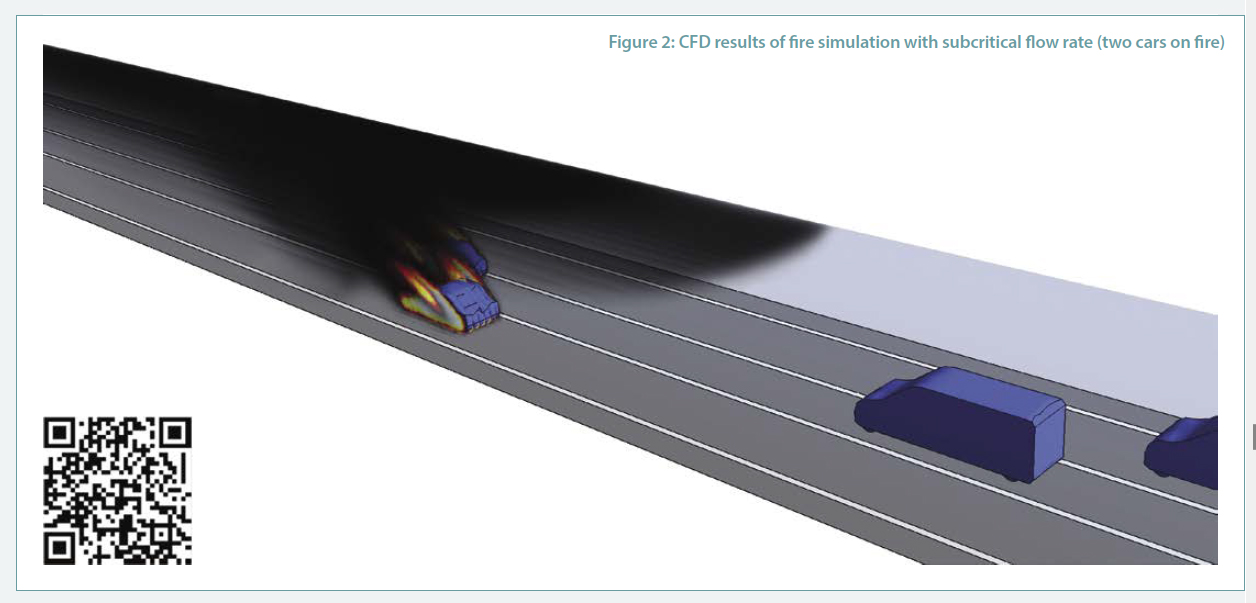
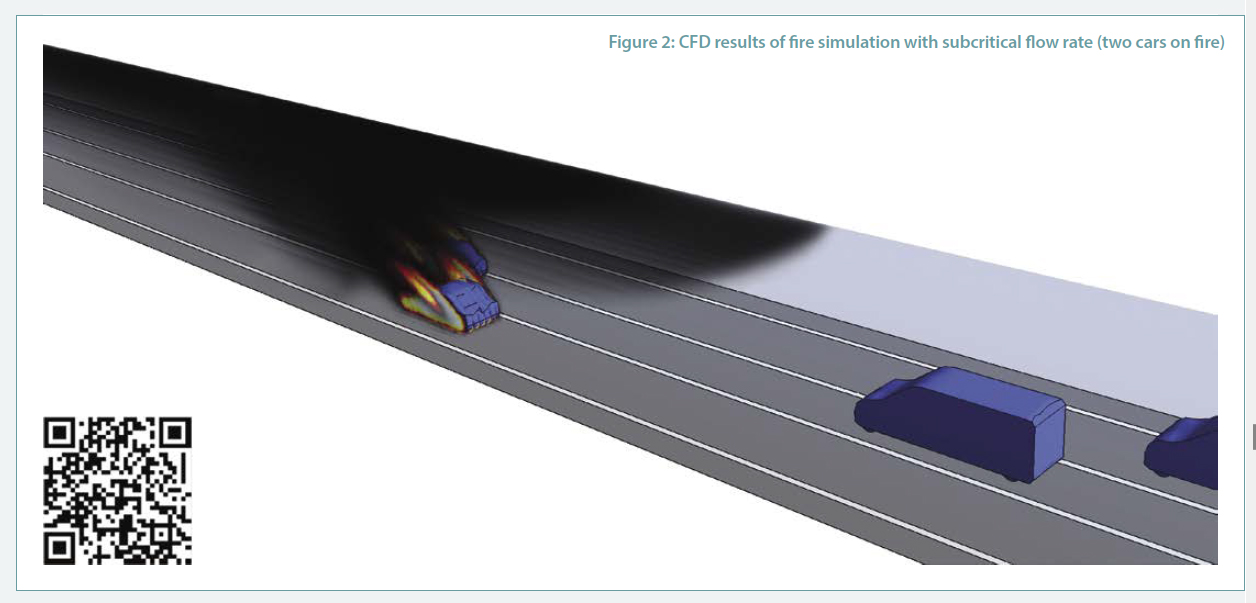
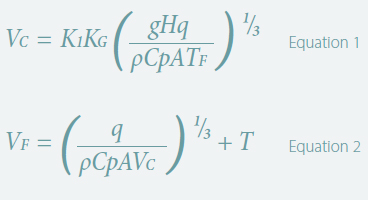
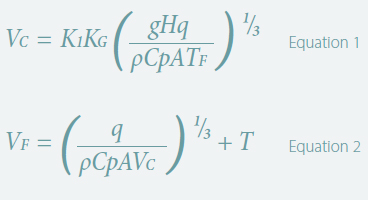
Theoretical calculations suggest a flow rate of 175m3/s is needed to prevent a 10MW fire from backlayering in the studied case. CFD simulations confirm this figure, ensuring occupant safety in the event of a fire of this magnitude. It’s worth noting that this alignment could be attributed to the tunnel’s straight configuration in this study. Figure 1 depicts the result of this simulation, showing the fire being directed towards the desired location. Figure 2 illustrates the consequences of inadequate flow rates, demonstrating the fire spreading in both directions. Some figures have embedded hyperlinks, or the video can be accessed via QR codes shown.
Efficiency
Efficiency in the design pertains to power consumption and capital cost by selecting appropriately sized fans or accurately estimating required power. Here, CFD proves invaluable in studying real scenarios, comparing theoretical designs with numerically solved equations considering tunnel shape and the impact of stationary and moving vehicles.
Optimisations can be made to reduce pollutant accumulation and fine-tune the design at the minimum possible cost. For example, modelling a tunnel section and comparing the results with theories. The design goal is to maintain an average CO content at 40 parts per million (ppm) throughout the tunnel, targeting an average CO content of less than 50ppm [5]. Theoretical calculations indicated a flow rate of 61m3/s, while CFD simulations yielded 48m3/s, resulting in a 21% reduction in flow rate and subsequently fan energy. It’s worth noting that this reduction factor cannot be generalised to all designs; it depends on the specific conditions of each case. Unlike theoretical design, CFD models the pollutant accumulation at all levels/locations, facilitating the adjustment of impulse fans distancing to optimise their capacity for ventilation performance. Figure 3 showcases a sample result providing designers with performance insights.
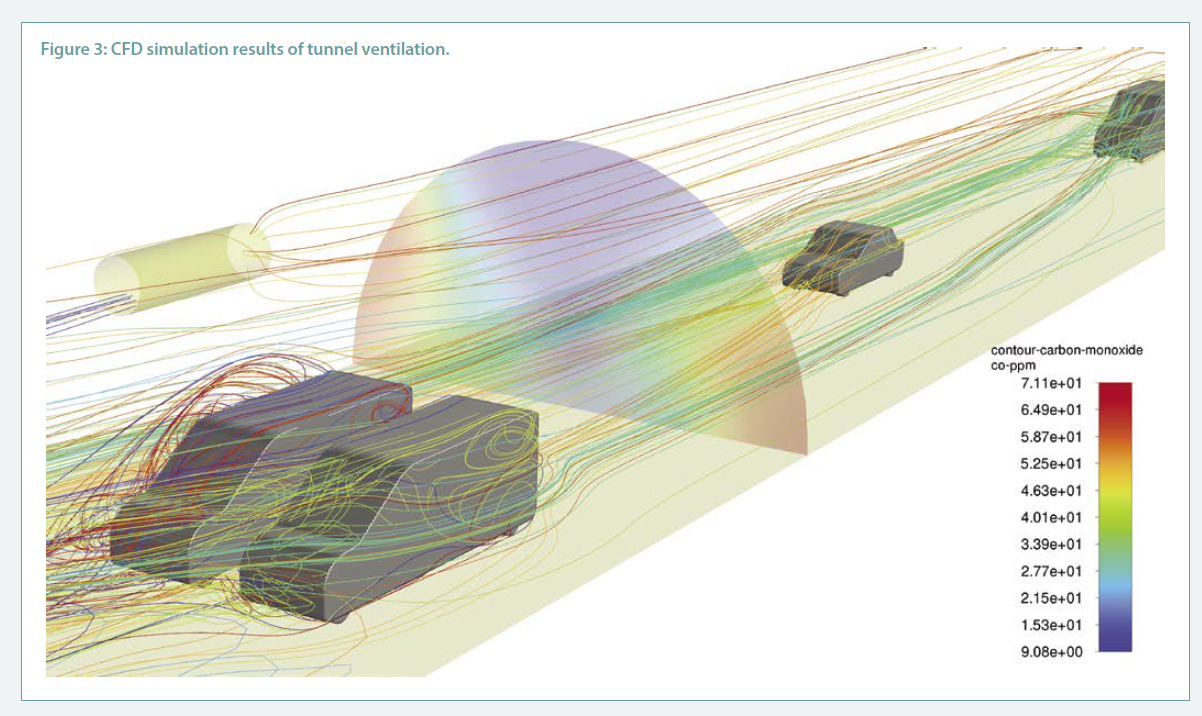
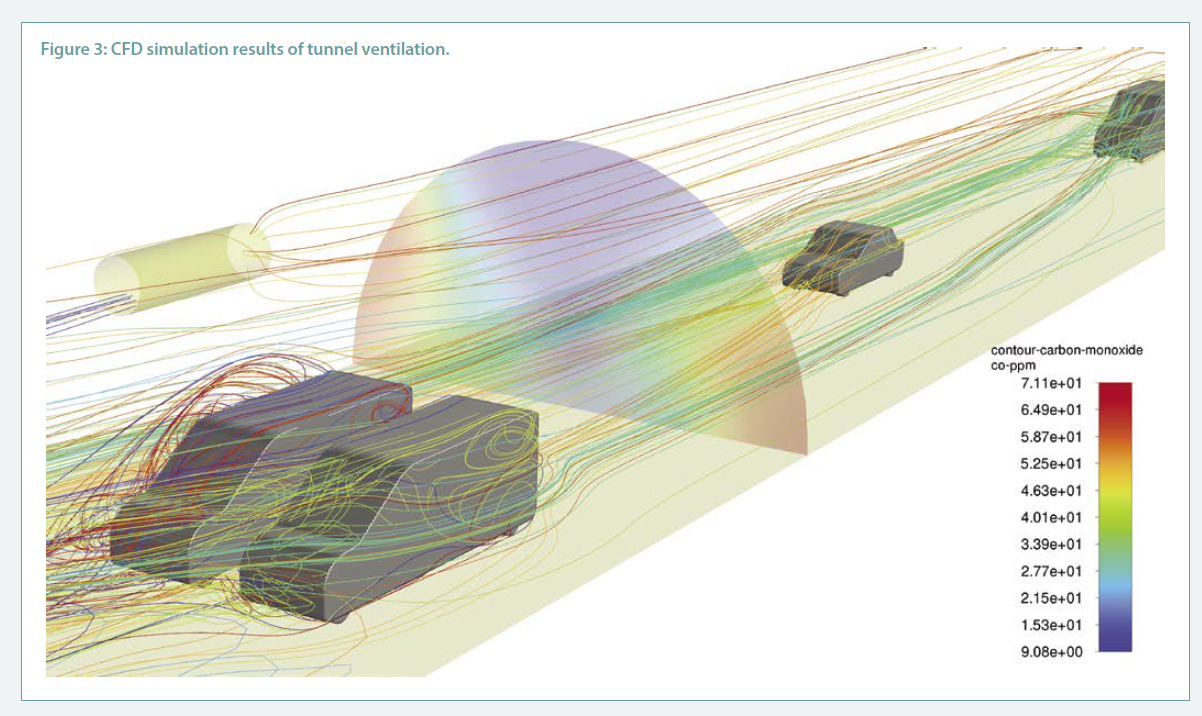
Time-Dependent Results
Transient study of the ventilation system is crucial, accounting for car movement within the tunnel and unsteady fire behaviour. Such assessments cannot be achieved through theories alone, necessitating the application of CFD simulations.
These time-dependent results can illustrate and evaluate design effectiveness when moving cars are considered, and also more accurately assess the ventilation system’s initial response to a fire.
Moving vehicles significantly enhance tunnel ventilation capacity. Simulation indicates that the steady-state flow rate with stationary cars is approximately 210kg/s. The influence of moving traffic modifies the flow rate, as depicted in Figure 4, resulting in an over 50% increase in the actual ventilation capacity.
Figure 5 illustrates the wake pattern of vehicles within the tunnel. It’s evident from the figure that a significant portion of the tunnel’s air is being carried by vehicles toward the exit portal. Replacing this air with fresh, clean air enhances the ventilation system’s performance. This is known as the “piston effect”.
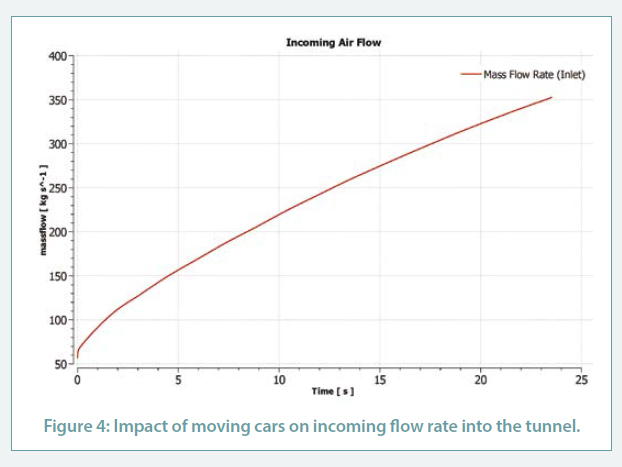
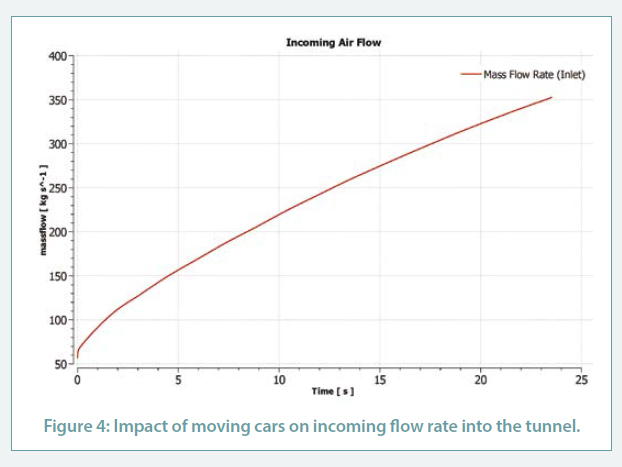
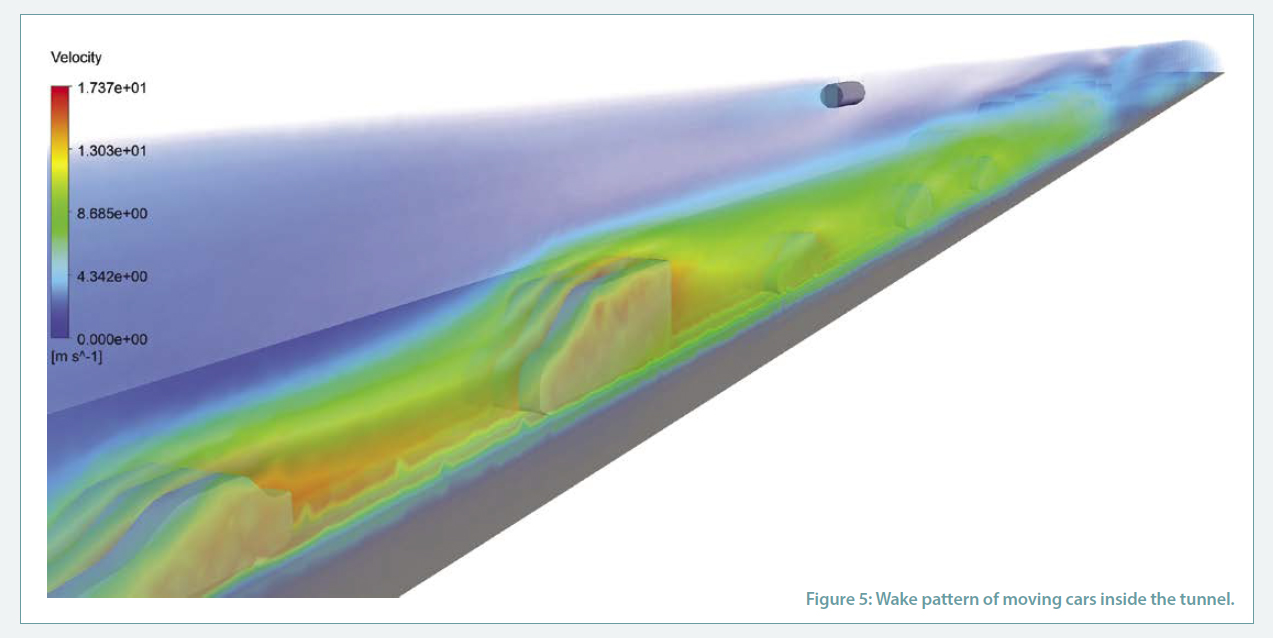
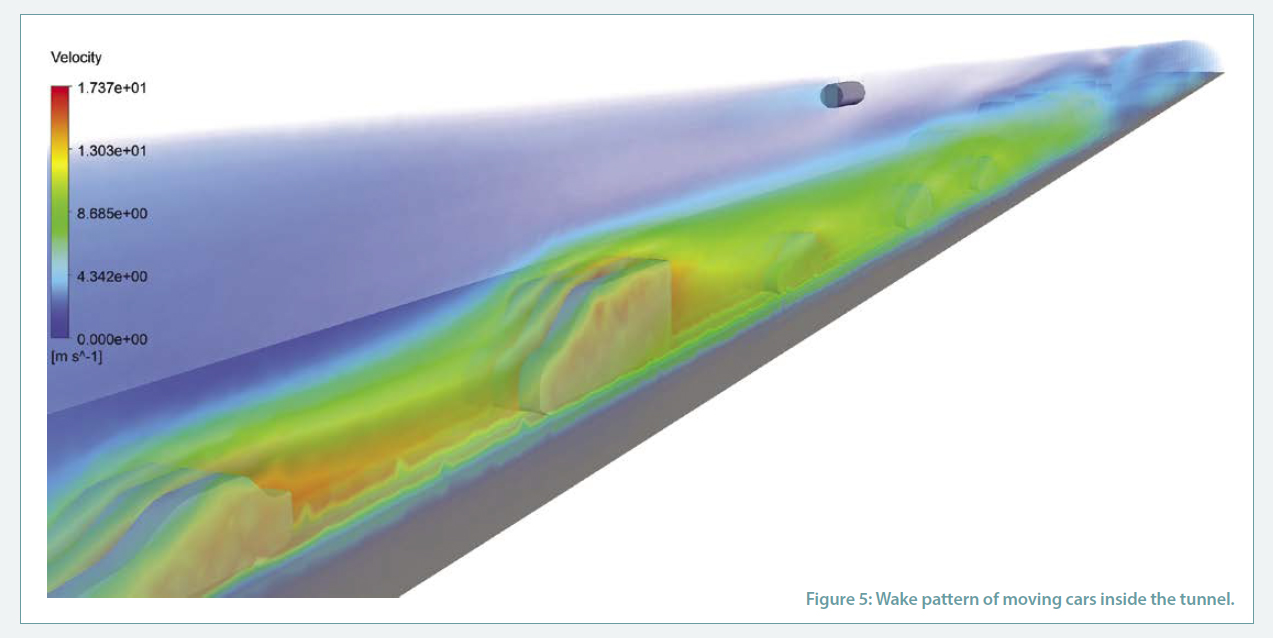
Transient fire simulation reveals the fire’s initial moments (Figure 6), demonstrating the ventilation system’s ability to push the fire forward from the start. This is a clear demonstration of the ventilation system’s performance in directing the fire from the very beginning.
By leveraging CFD, road tunnel ventilation systems can achieve optimal air quality, enhance safety against fire hazards, and maximise efficiency, ultimately contributing to the success of tunnel projects.
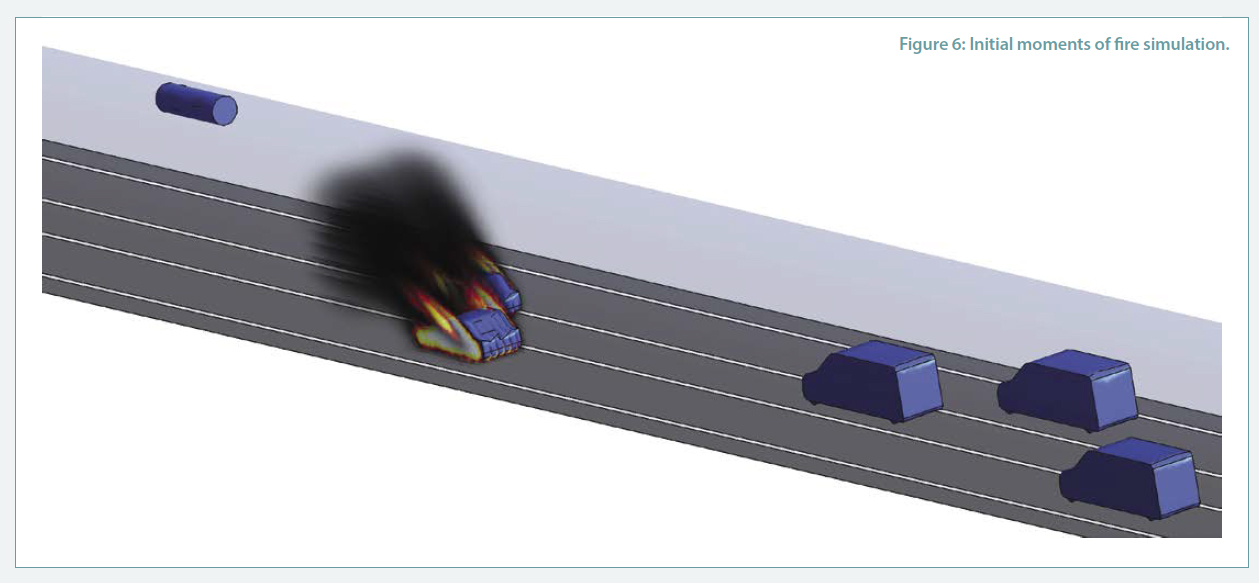
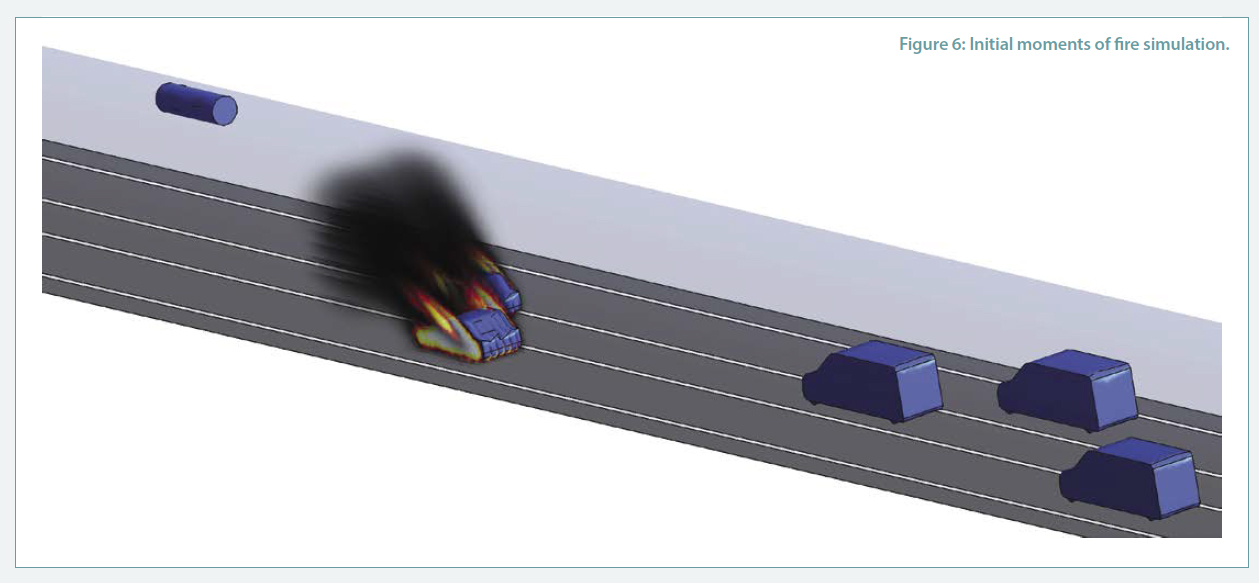
Conclusion
- In the realm of road tunnel ventilation, computational fluid dynamics (CFD) provides significant benefit, enhancing design precision and optimising tunnel performance. This report showcased CFD’s transformative impact through a sample impulse fan case study, revealing safer, more efficient, and cost-effective ventilation solutions.
- CFD’s predictive prowess ensures ventilation systems meet rigorous criteria across all tunnel operation modes, preventing hazards like fire backlayering. CFD enhances efficiency by assisting designers in fine-tuning fan capacities, placements and also the distances between fans to achieve acceptable levels of pollutant removal. Additionally, time-dependent analyses reveal real-world responses to moving cars and the unsteady nature of fire.
- Incorporating CFD in road tunnel design enables informed decisions, better air quality, minimised capital cost and safer tunnels. This synergy between technology and innovation propels us towards smarter, greener, and more effective transportation networks.
Disclaimer
The information or advice contained in these technical papers is intended for use only by professionals who have had adequate technical training in the field to which the paper relates. At the time of publication, these technical papers have undergone a formal peer-review process.
These documents have been compiled as an aid only, and the information or advice should be verified before it is put to use. The user should also establish the applicability of the information or advice in relation to any specific circumstances. While the information or advice is believed to be correct, no responsibility is taken by AIRAH for any statements made within.
AIRAH, its officers, employees and agents, disclaim responsibility for any inaccuracies contained within the documents, including those due to any negligence in the preparation and publication of the said technical papers.
References
- Guide to Road Tunnels Part 1: Planning, Design and Commissioning, Austroads, (2021)
- Sturm, Peter-Johann; Road Tunnel ventilation Systems: Technical Paper TP04, (2019)
- Guide to Road Tunnels Part 2: Planning, Design and Commissioning, Austroads, (2021)
- Road Tunnels: Vehicle Emissions and Air Demand for Ventilation, World Road Association, (2019)
- NFPA Standard: NFPA 502, “Standard for road tunnels, bridges, and other limited access highways”, National Fire Protection Association, (2020)
- ASHRAE: ASHRAE Handbook – Heating Ventilating and Air-Conditioning Applications, American Society of Heating, Refrigerating and Air-Conditioning Engineers, (2019)
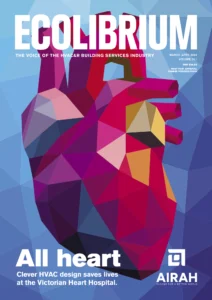
This article appears in Ecolibrium’s March-April 2024 edition
View the archive of previous editions
Latest edition
See everything from the latest edition of Ecolibrium, AIRAH’s official journal.