Honour and duty
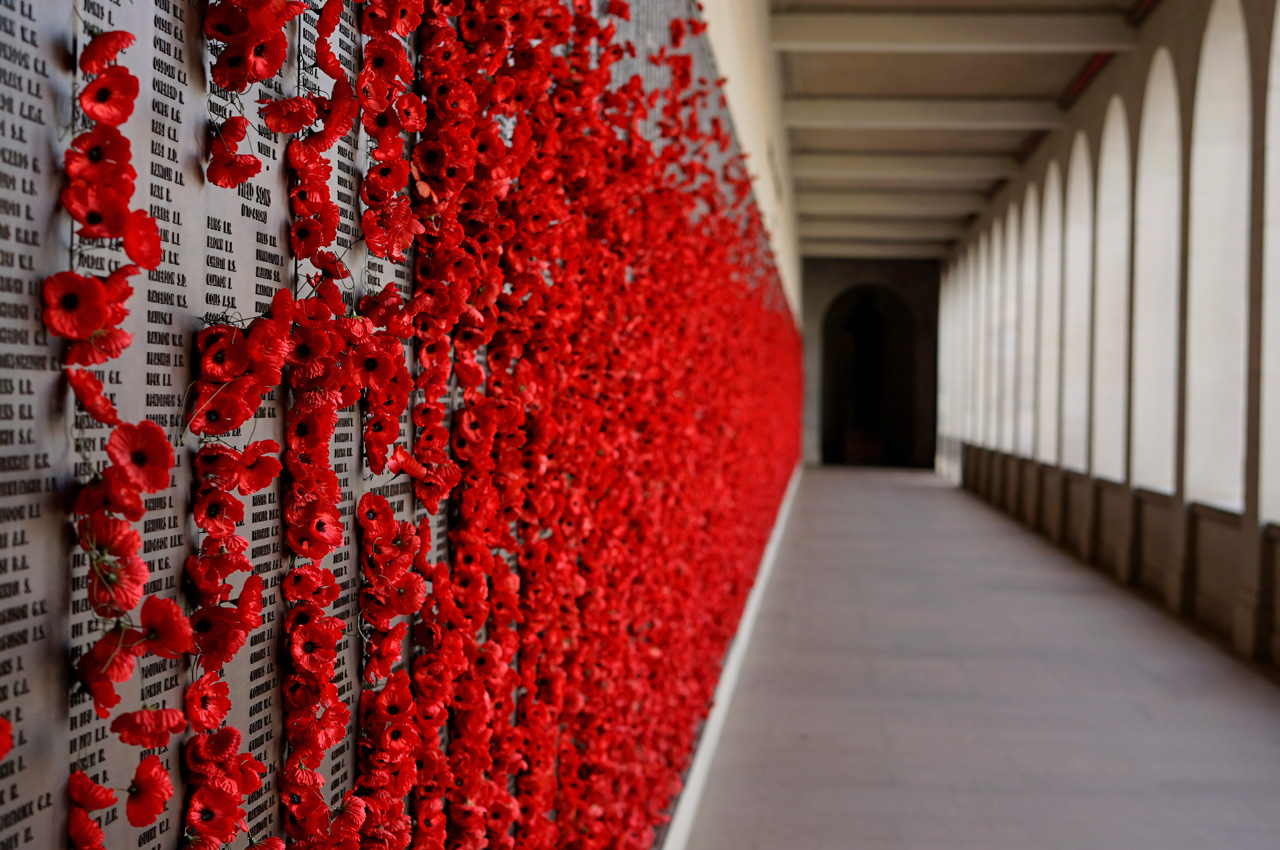
At Canberra’s Australian War Memorial, a geothermal heating and cooling system goes beyond traditional methods to accommodate extreme temperatures. The largest of its kind in the southern hemisphere and using world-first innovations, the geothermal system powers a 145,000m² site that honours lives lost through war while taking seriously its duty to future generations by implementing sustainable solutions.
Located on the outskirts of Canberra’s CBD in the foothills of Mount Ainslie, the Australian War Memorial (AWM) aims to fill visitors with the right note of solemnity, sombreness and peacefulness in a setting designed to honour those lost in war.
NDY was engaged to deliver consulting engineering services for its development and expansion. The project period was agreed at nine years, culminating in a June 2028 completion, and at a cost of AUD$550 million. It will expand gallery spaces and modernise buildings on the site.
GeoExchange Australia was engaged to provide geothermal services, with Benmax employed as the mechanical contractor.
Project brief and considerations
The project brief called for a central energy plant bringing together mechanical, electrical, fire and hydraulic services for the precinct. A fully electrified central plant provides heating and cooling to the main building, clad in 80-year-old heritage stonework, and new buildings.
There was to be a new two-level Anzac Hall gallery of about 10,000m², with a subterranean southern entrance including theatre, event space and flexible gallery space.
A glazed link will connect the existing memorial building and the new two-level Anzac Hall gallery.
The project also involved refurbishment of the existing heritage building including galleries and education spaces, and refurbishment and extension of the CEW Bean Building archives and Research Centre.
Completing the brief, a sitewide services and public realm refresh was stipulated, and as part of the initiative there was to be a project sustainability strategy.
Senior Associate and Technical Manager Rafe McAuliffe led NDY’s mechanical design team.
“With an 80-year heritage, the building needs sensitive and considered design,” he says regarding those project-specific considerations that had to be kept in mind. “Visitors come to pay their respects, and any mechanical solution needs to be peaceful.
“The museum is AAA-graded and holds precious historical artefacts. It needs heating and cooling at a constant temperature of 20–23°C and humidity of 45–55 per cent.”
McAuliffe says some of the gallery areas are 12m high and surrounded by heritage stonework – a challenging space for temperature regulation.
“Our heating and cooling solution needed to work within the parameters of an electrical design that’s already been approved,” McAuliffe explains. “Since the heating and cooling system loads don’t change, this needs a solution that’s extremely efficient.”
And of course, Canberra has a net-zero electrical grid and is transitioning away from the use of fossil fuels. Any solution therefore had to be future-proof.
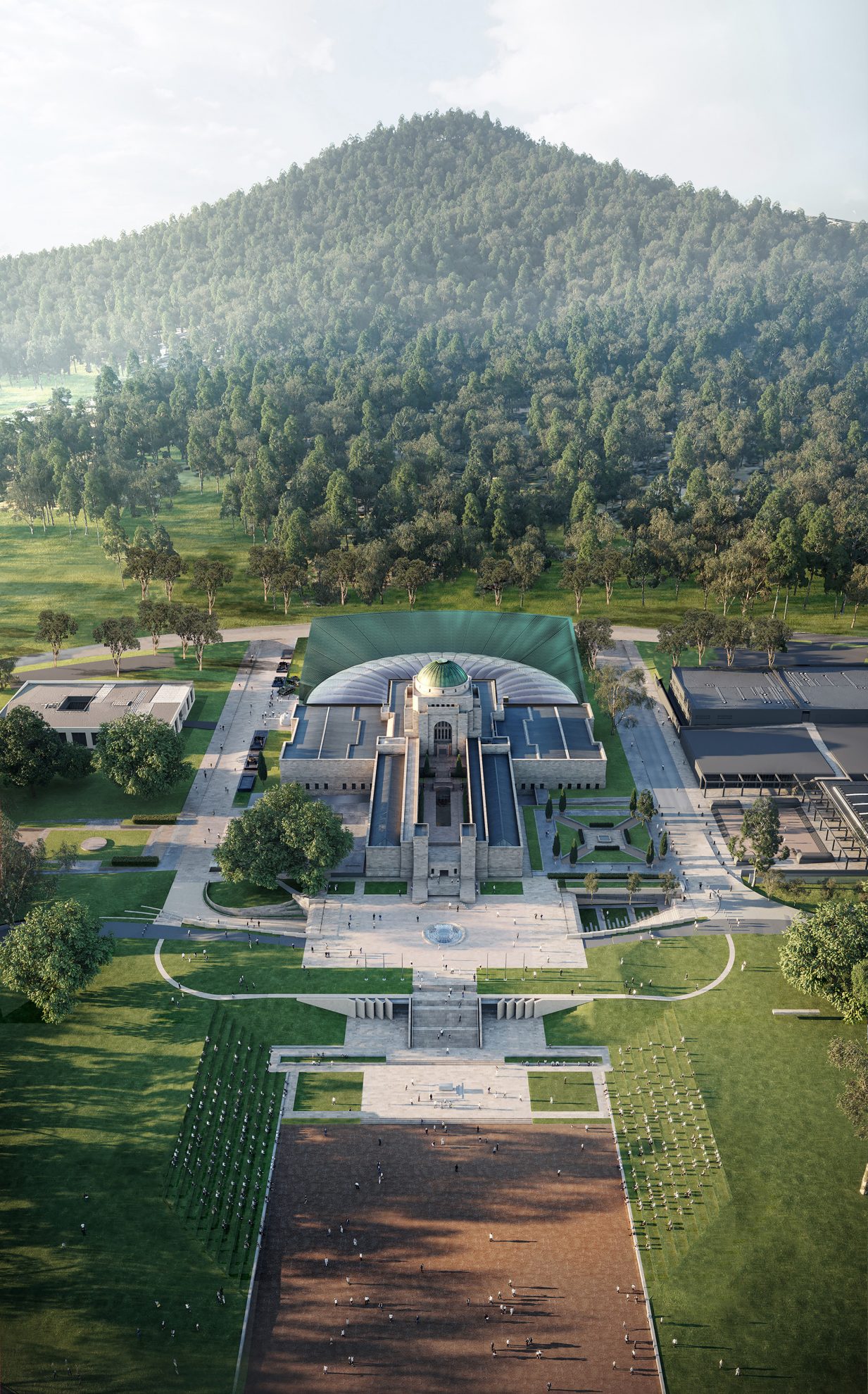
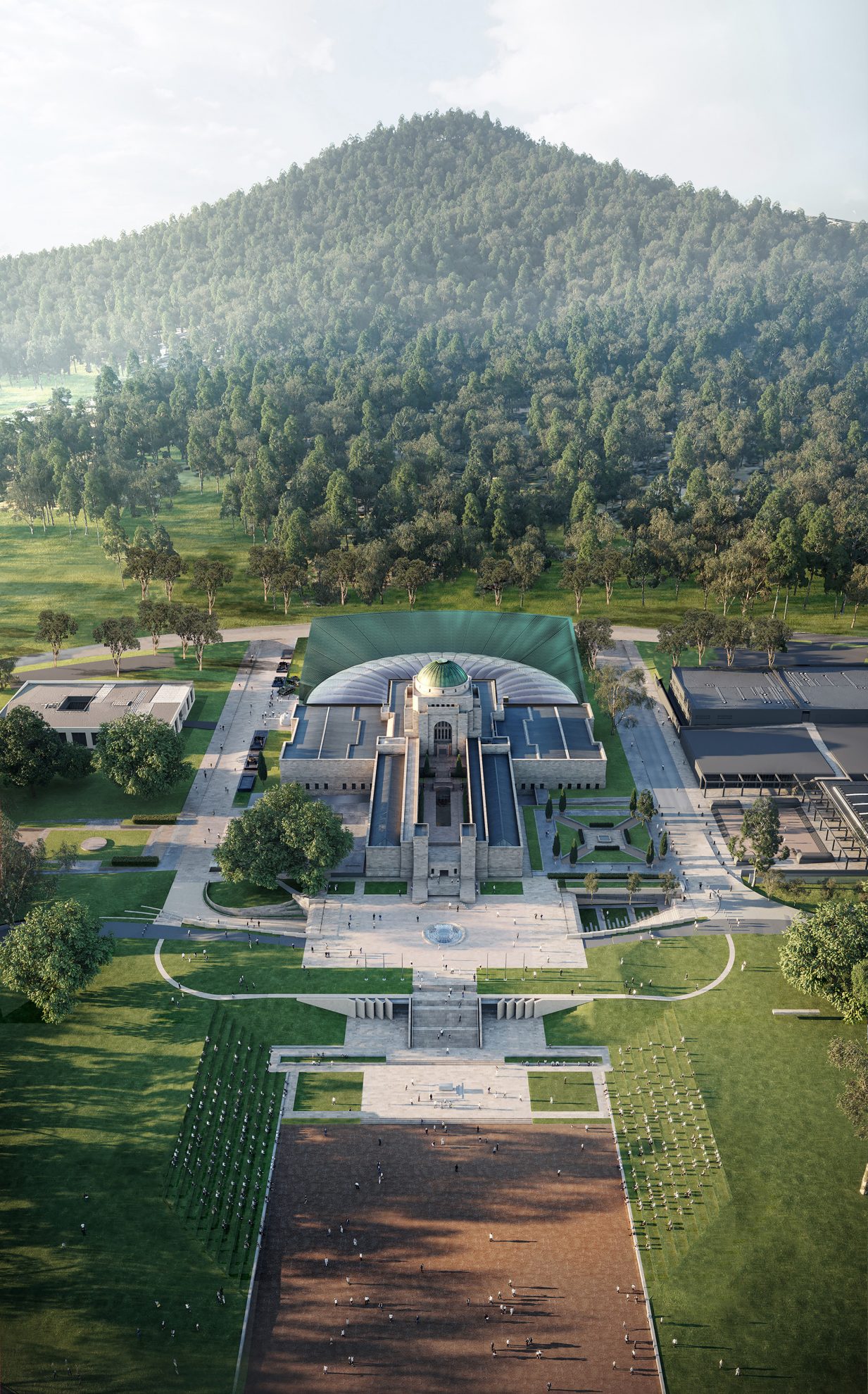
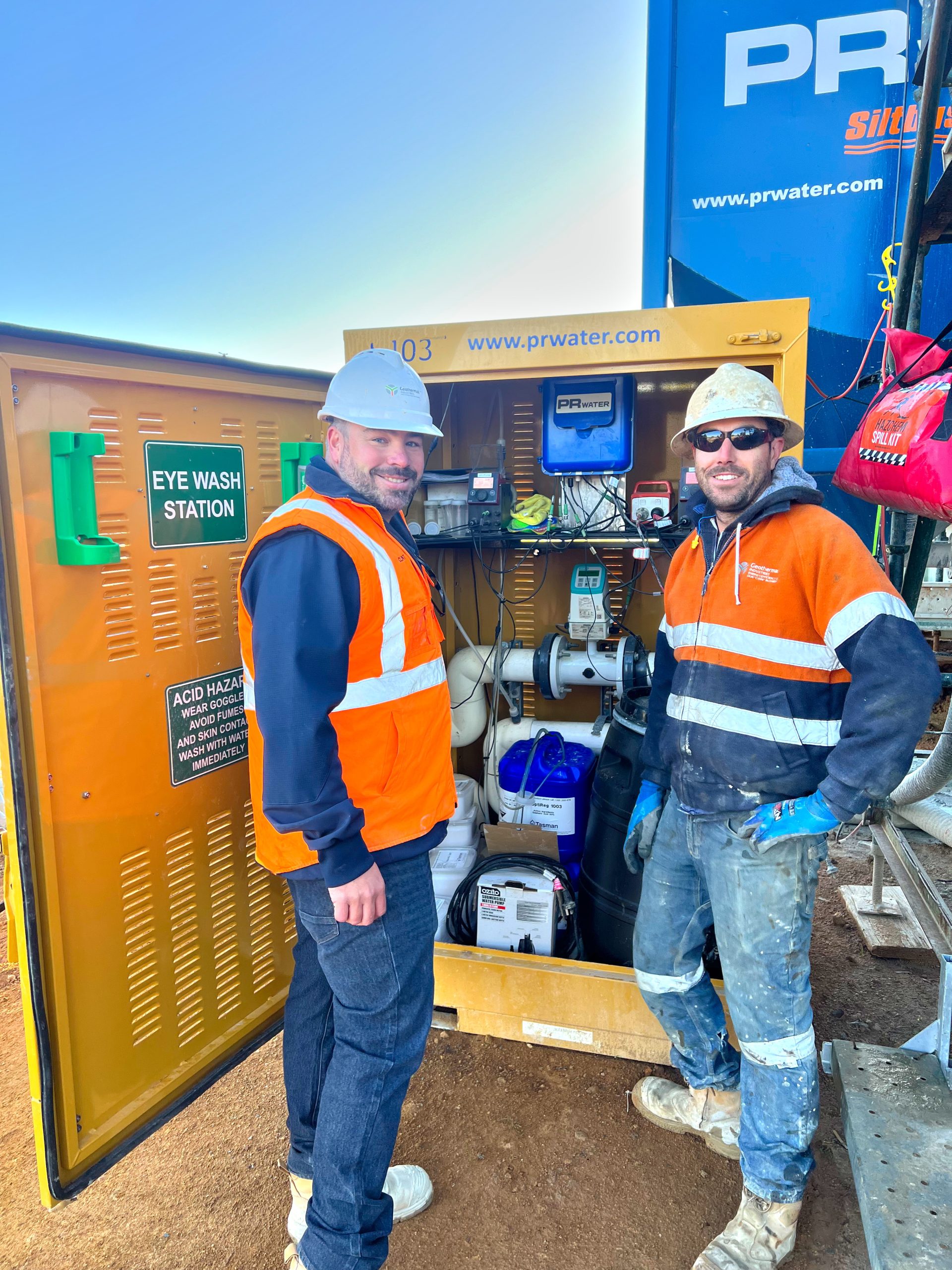
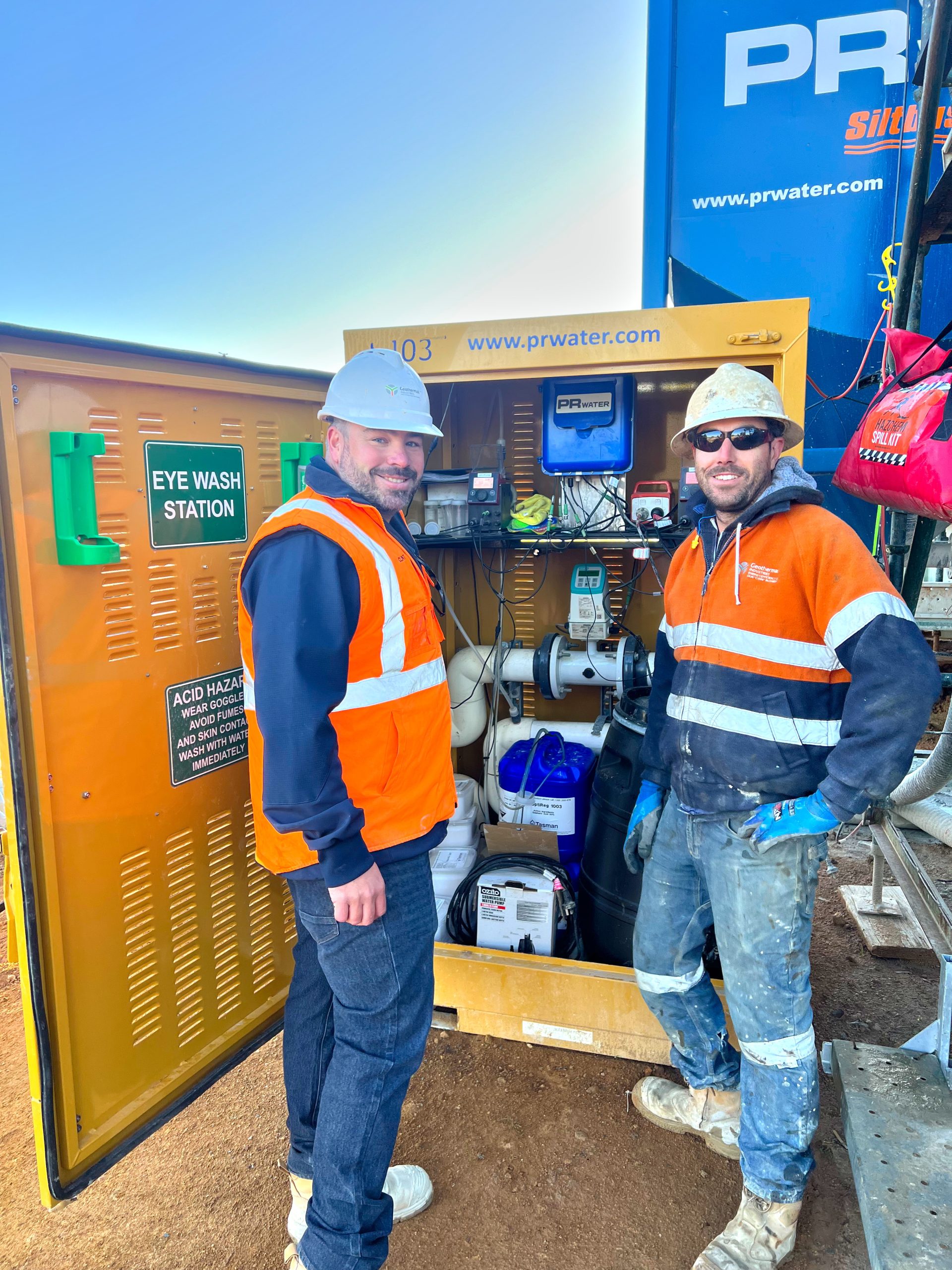
The mech contractor contribution
Benmax General Manager, Construction Steve Watt and Project Manager Matt Dickson outline the work of the mechanical contractor on the project.
The initial scope of work was the HVAC install of the central energy plant (CEP), the Bean Building expansion, the southern entrance expansion and the preliminary sitewide pipework. This comprised detailed calculations of all HVAC equipment, 3D modelling to LOD 400, and commissioning.
“With multiple builders over various sites, we also became responsible for ensuring space conditions would be available for the Australian War Memorial’s operating area’s during construction,” says Benmax General Manager, Construction Steve Watt.
The Canberra mech contractor was contracted to deliver to the CEP three 1,350kW water-cooled chillers with two 1,140kW water-cooled heat pumps and “two and two” 750kW reverse-cycle, water-cooled heat pumps with manual changeover for extreme weather events.
“Cooling water is provided primarily by new geothermal bore holes filled with 20 per cent glycol, in addition to three cooling towers with space for a fourth. These provide tempering/back-up heat- rejection to the geothermal system via heat exchangers,” explains Benmax Project Manager Matt Dickson.
An additional heat exchanger between the return chilled water and leaving cooling water from the heat pumps provides free cooling during winter. The central energy plant contains 32 pumps with high efficiency IE5 synchronous reluctance motors, comprising 17 primary pumps and 15 secondary pumps, with additional future spaces allocated.
For the Bean Building expansion project, Benmax’s role was to assist in the partial demolition and provide HVAC services to the expansion of the Bean Building. New office space for staff, collections store, new archival stores and viewing rooms are served by multiple AHU plant rooms. Conditions for the archival stores are served with dual redundant AHUs.
The archival store is required to be operational to store artefacts during construction works or for long-term preservation. AHUs serving the collections store, archival stores and viewing rooms are served via pre-treatment AHUs that have carbon filters for mitigation against smoke from bushfires.
“The southern entrance is a new expansion located at the front of memorial,” explains Dickson. “The new entrance and gallery are partially underground and are focused on the public-facing functions, featuring new auditoriums, visitor centres, gift shops and more. The entire space is provided with slab heating and air conditioning.”
Underground service tunnels connect these and any potential future buildings. Benmax was engaged early to install prefabricated heating and chilled water pipework throughout.
Project brief and considerations
The project brief called for a central energy plant bringing together mechanical, electrical, fire and hydraulic services for the precinct. A fully electrified central plant provides heating and cooling to the main building, clad in 80-year-old heritage stonework, and new buildings.
There was to be a new two-level Anzac Hall gallery of about 10,000m², with a subterranean southern entrance including theatre, event space and flexible gallery space.
A glazed link will connect the existing memorial building and the new two-level Anzac Hall gallery.
The project also involved refurbishment of the existing heritage building including galleries and education spaces, and refurbishment and extension of the CEW Bean Building archives and Research Centre.
Completing the brief, a sitewide services and public realm refresh was stipulated, and as part of the initiative there was to be a project sustainability strategy.
Senior Associate and Technical Manager Rafe McAuliffe led NDY’s mechanical design team.
“With an 80-year heritage, the building needs sensitive and considered design,” he says regarding those project-specific considerations that had to be kept in mind. “Visitors come to pay their respects, and any mechanical solution needs to be peaceful.
“The museum is AAA-graded and holds precious historical artefacts. It needs heating and cooling at a constant temperature of 20–23°C and humidity of 45–55 per cent.”
McAuliffe says some of the gallery areas are 12m high and surrounded by heritage stonework – a challenging space for temperature regulation.
“Our heating and cooling solution needed to work within the parameters of an electrical design that’s already been approved,” McAuliffe explains. “Since the heating and cooling system loads don’t change, this needs a solution that’s extremely efficient.”
And of course, Canberra has a net-zero electrical grid and is transitioning away from the use of fossil fuels. Any solution therefore had to be future-proof.
Closed-loop geothermal energy
“Geothermal energy harnesses the earth’s stable temperature to provide heating and cooling, and typically generates around 40 per cent in energy saving compared to a traditional system,” McAuliffe says. “AWM’s energy solution goes even further, with a 105 per cent improvement over a traditional system.
“We understand this to be the first system in the world to use multiple large water-source heat pumps and chillers with electromagnetic oil-free bearing compressors in a geothermal application. The system provides a reliable and 100 per cent renewable energy solution that uses ground-source heat pumps and is fully electrified.”
Yale Carden, M.AIRAH, heads up GeoExchange Australia.
“We provided preliminary advice on the technology in general and its suitability for the project,” Carden explains. “Much of this included debunking a series of myths about the technology and providing comfort to the client that it was a proven technology and thus a viable option.”
This work progressed into a concept design and preliminary feasibility study, including business case development, that then advanced to a test borehole.
“Despite the work itself being well received and demonstrating its viability, geothermal was not included at first in the design,” Carden says. “However, about three years later, geo was back in, and so we updated the feasibility with new data and progressed into a detailed design and tender specification. This included some additional test boreholes, as the location of the ground heat exchanger was now in a different location and we were looking to extend its depth from 120m to 150m, as less surface area was now available.
“Our scope covered the geoexchange design and its integration with the plant room,” Carden says. “We worked closely with NDY on the plant room integration, including collaboration on design of plant items such as circulating pumps and the ground-source heat pumps.”
Challenges faces and overcome
“The earliest challenge we faced was the sitewide pipework, as the roads that crossed above them needed to have minimal disruption to the operation of the AWM,” says Benmax Project Manager Matt Dickson. “Following close behind the builder and utilising prefabricated modules, installation time was kept at the minimum amount.
“Another issue we faced was parts of the Bean Building having very tight ceiling spaces in the corridors next to the meeting rooms. Because acoustics were important for these rooms, all services were squeezed.
“Finally, there was a period where the geothermal team encountered difficulties drilling some of the bores to accommodate the full number needed for the CEP. Flexibility was needed, as some borehole locations needed to be added and re-drilled to accommodate these issues, using spare space.”
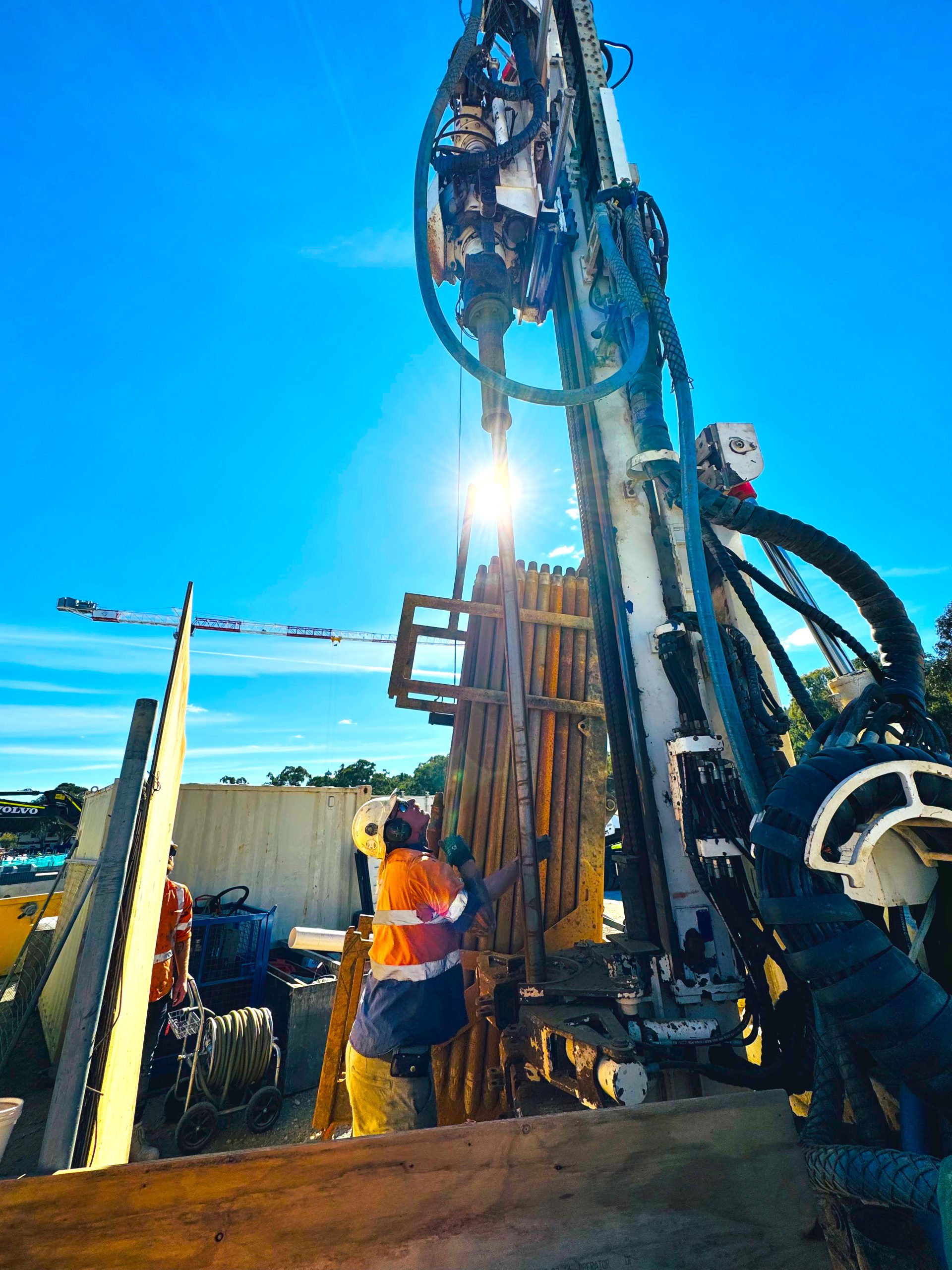
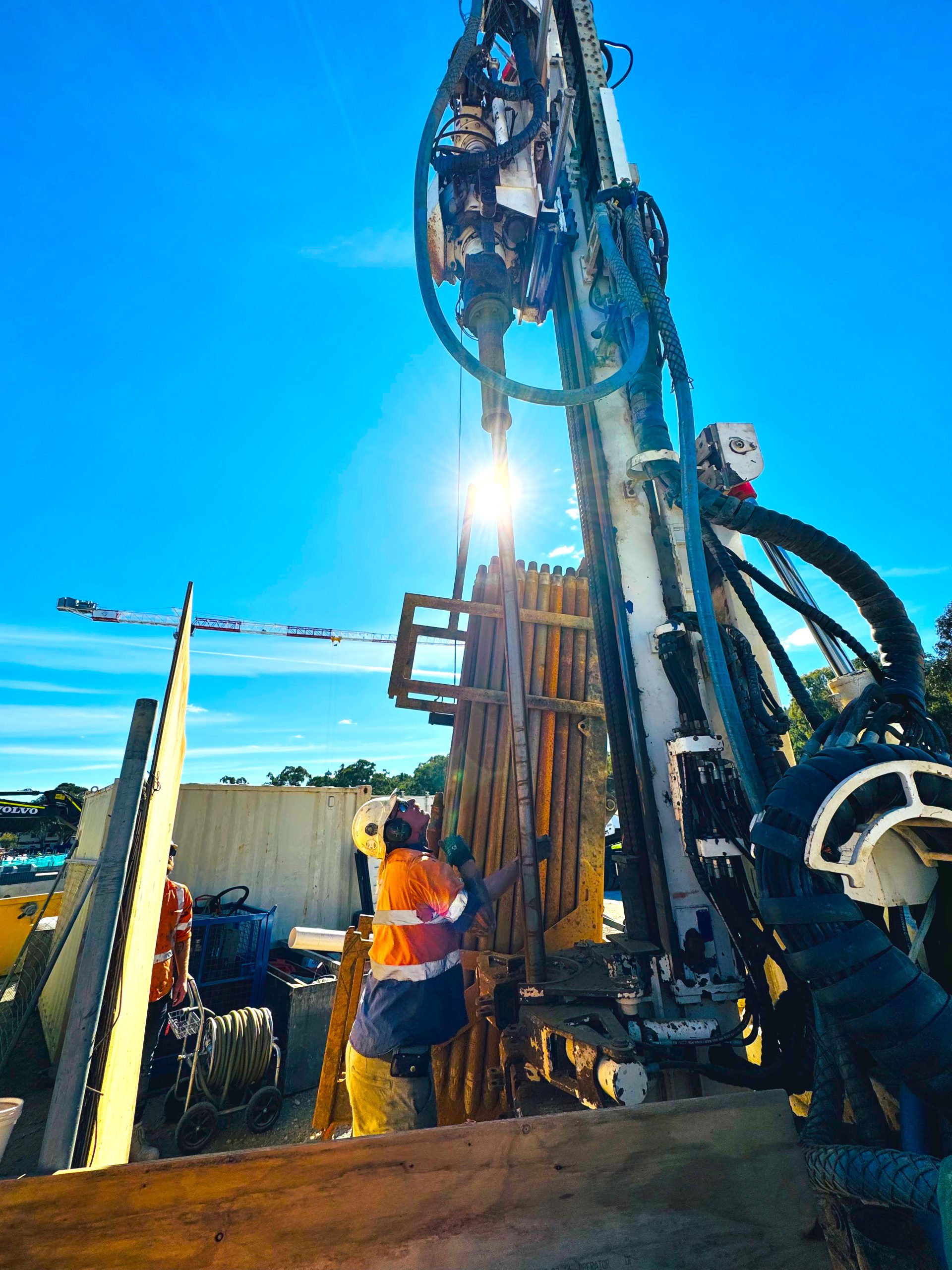
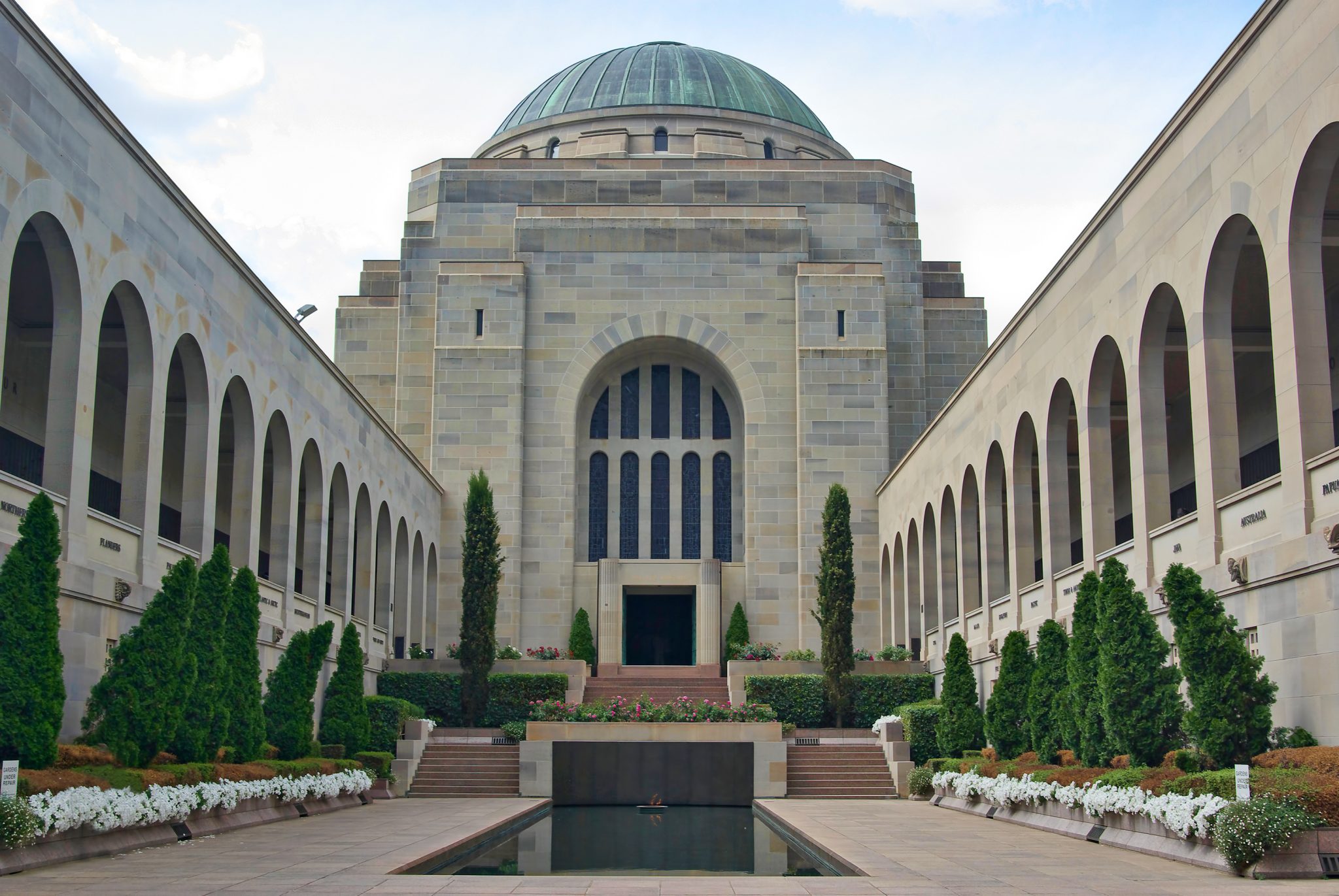
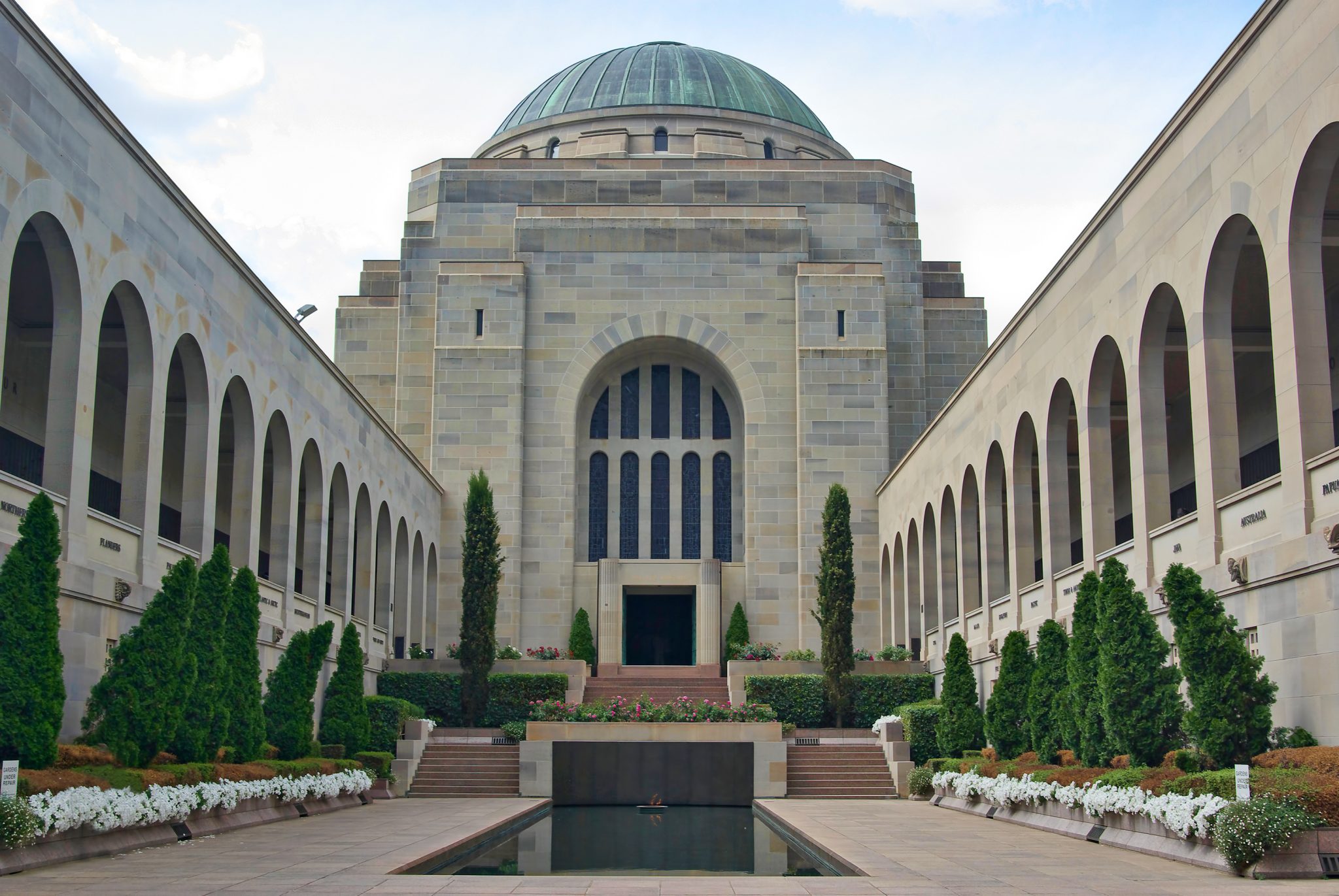
Alternative sustainability strategies
Wayne Hitches is Executive Program Director for the Australian War Memorial Development.
“The Australian War Memorial had requested NDY look at alternative sustainability strategies to improve the precinct services planning as part of the initial concept designs,” he explains.
“This was accelerated with the excavation of our new carpark extension in late 2019, and a preliminary geothermal heat exchange system was proposed. Although supported at project level, the payback and initial investment were considered ‘borderline’ within a project that was already tightly budgeted for a very ambitious masterplan. Eighteen months later, however, the announcement of a degassing initiative from [the] government increased public environmental focus and large gas price increases encouraged the project team to revisit the plan.
“Supported by NDY and GeoExchange Australia, the team put a compelling case to the Council of the Australian War Memorial. After considerable discussion, the AWM Council unanimously agreed that we would take this leap towards a sustainable precinct.”
The Australian War Memorial’s Director and Chairman fully supported the solution and committed to the initiative, proposed from a dedicated few that will see this development’s outcome as courageous common sense rather than a risky venture – or leading-edge endeavour – when viewed from the future.
Whole-of-life financial savings are also expected to be significant, with current modelling anticipating savings to pay off the initial extra-over investment in eight to 10 years.
Efficiency gains
McAuliffe says a geothermal heating and cooling system is more efficient than a traditional air-source heating and cooling system because it doesn’t use large fans to reject waste heat to the air. Rather, it uses water to transfer heat into the earth, using long loops of pipe that are sunk deep into the ground.
In cold weather, heat pumps are used to generate hot water that heats the buildings. However, for the geothermal system, the waste energy is absorbed underground, carried down through the loop of pipes where the earth absorbs the waste energy.
In warm weather, the system works the opposite way, cooling the building with chillers and rejecting the heat underground.
“AWM’s closed-loop system relies on 32km of vertical boreholes, drilled as deep as 150m, fitted with over 130km of pipework to form an underground heat exchanger,” McAuliffe says. “This geothermal ground heat exchanger is the system that unlocks the high efficiencies of geothermal cooling and heating.
“During periods of cold weather, the heat pumps are generating chilled water as a waste product. However, there are still cooling requirements for the communications and specialist cold rooms – these loads will be satisfied by this waste energy source. The design of the system allows the energy to be recovered and [therefore] avoid running chillers, resulting in simultaneous cooling and heating.”
The heart of the mechanical system
The heart of the mechanical system is a combination of large-capacity chillers and water-source heat pumps, a total of seven machines with a combined 7,850kW of refrigeration.
“Due to the significant capacities needed, conventional geothermal machines would have been unsuitable – the site would have needed 40 of the biggest machines available,” McAuliffe says.
“We took an innovative approach using the latest technology of electromagnetic bearing and oil-free compressors, combined with ultra-low-GWP refrigerant and customised machines. This allows the chillers and heat pumps to operate despite extreme temperature ranges from the geothermal ground loop water: from -1°C to 39°C. To deal with such a wide range of temperatures and avoid freezing, the geothermal pipework is filled with 20 per cent glycol.”
Another important feature that makes the system work so effectively is that all the geothermal machines are set up in a centralised plant arrangement – within a central energy precinct – avoiding the distribution of hundreds of small geothermal units throughout the site.
The centralised system also allows the five buildings connected on the site to share a common system and gain benefits from diversity in operation.
“It’s the combination of these elements that make up Australia’s biggest geothermal system,” McAuliffe says.
Understanding the challenges
Carden says the project’s heritage aspects, combined heating and cooling requirements and Canberra’s net zero electrical grid were not so much challenges as they were supportive of a geoexchange system.
“The heritage elements didn’t impact our scope as such, although they do tend to encourage the use of a geoexchange system to eliminate or minimise the external plant required by air source solutions,” he explains.
Carden says NDY developed the thermal loads for the building as part of its broader work, and these were integrated into the geoexchange design.
“Contrary to most people’s preconceptions, the building loads are equally, possibly more important, than the underlying geology in a geoexchange design,” he says.
“The ACT’s policies on a net zero grid and the removal of gas were a catalyst for the uptake of geo rather than a challenge. Once gas boilers are removed from consideration, heat pumps are a clear alternative, and then it comes down to whether you use the air or the ground as the source of thermal energy.
“The challenges for us on projects tend to be cultural or maybe philosophical as much as they are technical,” Carden says.
Debunking myths about geoexchange limitations and the power of gas as the status quo can be significant obstacles to negotiate, he says.
“Once these were navigated around, the fundamentals of the geo system were compelling,” Carden explains.
In the case of the AWM, we’re talking about substantial annual energy savings, reduced electrical loads, and of course the enormous capacity of the geoexchange as thermal storage.
“Technically, balancing the hybrid cooling system and coordinating borehole locations around numerous site constraints both beneath and outside the building footprint were the main challenges,” Carden explains. “The latter required splitting the geoexchange across three separate locations, including having some back-up options, before optimising system flow back to the central energy plant.”
Innovation on tap
“Another innovation that we integrated into the design was the ability to reverse the operation of two of the machines,” McAuliffe explains. “These specially customised units are designed to operate normally as either a chiller or a heat pump, but if there is a failure of any of the seven machines then these units can be swapped to reverse operation.”
“You don’t run all of your chillers in winter and you also don’t run all of your heat pumps in summer. So, if machines can be reversed, the AWM only needs to install the required equipment for normal operation, but still have a spare machine for redundancy in peak conditions. This avoids the significant cost of buying two dedicated stand-by machines that sit idle, while still having the surplus they need for their critical gallery space.”
Geothermal, but unique
The AWM’s geothermal energy system uses multiple electromagnetic bearing, oil-free compressors, which are usually only available in large-capacity chillers.
“Since these chillers are some of the most efficient on the market and used in building projects that are looking for extremely efficient energy, we wanted to use them for this new type of application,” McAuliffe says.
“We worked with manufacturers to adapt a standard chiller to work with the extreme range of temperatures needed in the geothermal loop. We were also able to reverse their standard function and manufacture a bespoke water-source heat pump to generate heating water – again operating with the extreme range of expected temperatures.
“Normally a large geothermal system with a central plant uses relatively low-tech machines,” McAuliffe explains. “Higher-tech solutions are usually deployed on a smaller scale and less centralised. However, through creativity in mechanical engineering, we managed to develop a bespoke and highly sophisticated system that works with the centralised energy precinct.
“We collaborated with GeoExchange Australia to design a ground heat exchanger that would work with the mechanical plant,” McAuliffe explains. “The modelling of the ground loop performance was carefully matched with the proposed plant, adapting the operating temperatures to work within the limits of the machines.
“A key innovation was to use double loops in each borehole, which allowed greater performance from each borehole and higher water flow rates. This reduced the number of boreholes needed and allowed cooling towers to be connected at the end of the ground loop, for trim cooling.”
Excellent payback
“The capital cost of geothermal can be high, but the payback is excellent,” McAuliffe says. “The plant itself only needs to be replaced after approximately 40 years as opposed to an air-cooled plant, which is replaced after 10–15 years. This saves millions of dollars. Also, as heating and cooling comes from the earth’s stable temperature, energy bills are much lower than they would be under an air-sourced system.
“As the temperature of the earth that we tap into stays at around 17°C, the heating and cooling systems have a stable heat rejection base to work with, rather than the extremes ambient air reaches in peak summer and winter.”
Carden says the project was extremely satisfying to be involved in.
“One of our objectives as a company is to work on significant and technically interesting projects that challenge general and industry preconceptions of how we heat and cool our buildings,” he says. “Importantly, in doing so, we shift mindsets through real-world examples and thus positively contribute to the energy transition. The AWM project ticks all these boxes.”
What was learned
Benmax Project Manager Matt Dickson shares some process improvement ideas picked up on the AWM project.
More investigative works and point cloud scanning
“The Australian War Memorial is a building that’s been around for over 80 years and has been expanded, refurbished and repaired countless times,” says Benmax Project Manager Matt Dickson. “Plans can age out, be lost or damaged, or just not updated. If there was more scanning done prior to demo there would have been less surprise beams, hydronic pipe, fire rating, etc., and thus you design and build around that.”
Use more prefabrication and earlier in the project
“The ideal scenario would be all equipment is pre-piped, pre-wired and tested, and all that’s left is to join the segments,” Dickson says. “Part of the process would be about informing other services what’s happening and asking if they want to be onboard.”
A clear sequence of operation
“Because the memorial remains open to the public during the refurbishment works, with the multiple worksites at various stages of completion, there are some timing issues for services where new pipework is required to replace existing live pipework already in the way,” Dickson says. “A new route would need to be found that also won’t cause future issues in later stages of works.”
Project at a glance
The professionals
Client: Australian War Memorial
Geothermal consultant: GeoExchange Australia
Geothermal driller: Geothermal Industries Australia
Geothermal pipe installer: A Plus Plumbing
Mechanical services designer: NDY
Mechanical services contractor: Benmax
Principal contractor: Hindmarsh Construction Australia
The equipment
Air handling units: GJ Walker
Chillers: Smardt WB125
Cooling towers: BAC PCT1010
CRAC units: Stulz
Fans: Fantech
Fan coil units: GJ Walker
Heat pumps: Smardt WB100
HEX: Kelvion NA10S and NA06S
Pumps: Grundfos NKG with ABB SynRM motors
R/C heat pumps: Smardt WB080
VAVs: Holyoake
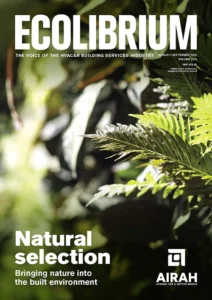
This article appears in Ecolibrium’s August-September 2024 edition
View the archive of previous editions
Latest edition
See everything from the latest edition of Ecolibrium, AIRAH’s official journal.